High-Gain Observer-Based Sliding-Mode Dynamic Surface Control for Particleboard Glue Mixing and Dosing System
Total Page:16
File Type:pdf, Size:1020Kb
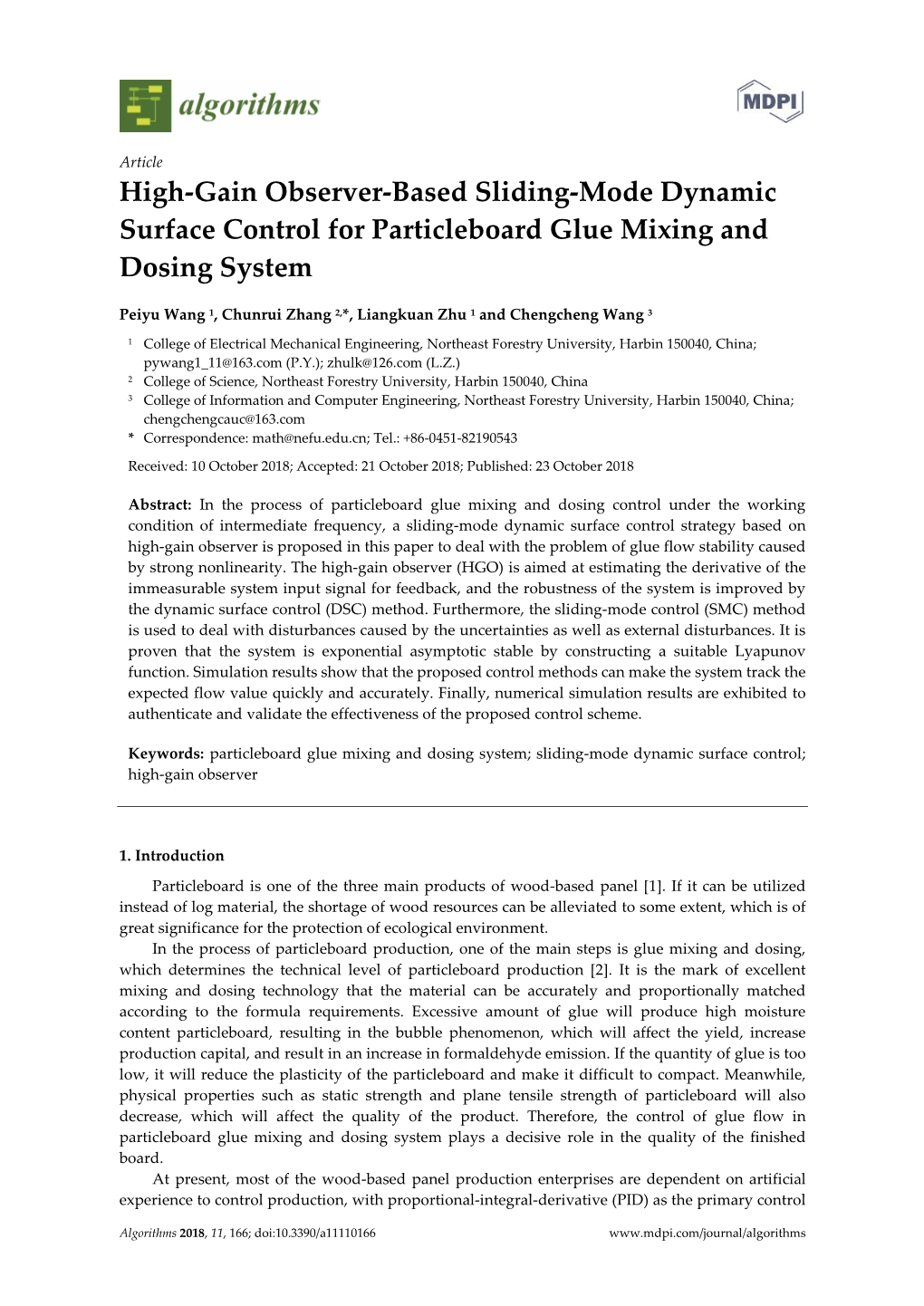
Load more
Recommended publications
-
Sliding Mode Control of Discrete-Time Weakly Coupled Systems
SLIDING MODE CONTROL OF DISCRETE-TIME WEAKLY COUPLED SYSTEMS by PRASHANTH KUMAR GOPALA A thesis submitted to the Graduate School-New Brunswick Rutgers, The State University of New Jersey In partial fulfillment of the requirements For the degree of Master of Science Graduate Program in Electrical and Computer Engineering Written under the direction of Professor Zoran Gaji´c And approved by New Brunswick, New Jersey January, 2011 ABSTRACT OF THE THESIS Sliding Mode Control of Discrete-time Weakly Coupled Systems by Prashanth Kumar Gopala Thesis Director: Professor Zoran Gaji´c Sliding mode control is a form of variable structure control which is a powerful tool to cope with external disturbances and uncertainty. There are many applications of sliding mode control of weakly coupled system to absorption columns, catalytic crackers, chemical plants, chemical reactors, helicopters, satellites, flexible beams, cold-rolling mills, power systems, electrical circuits, computer/communication networks, etc. In this thesis, the problem of sliding mode control for systems, which are composed of two weakly coupled subsystems, is addressed. This thesis presents several methods to apply sliding mode control to linear discrete- time weakly-coupled systems and different approaches to decouple the sub-systems. The application of Utkin and Young's sliding mode control method on discrete-time weakly-coupled systems is studied in detail which is then compared with other control algorithms while emphasising the importance of the decoupling technique in each case. It also presents the possibility of integrating two or more control strategies for a sin- gle system; one for each sub-system, depending upon the respective requirements and constraints. -
Sliding Mode Vector Control of Three Phase Induction Motor
SLIDING MODE VECTOR CONTROL OF THREE PHASE INDUCTION MOTOR A THESIS SUBMITTED IN PARTIAL FULFILLMENT OF THE REQUIREMENTS FOR THE DEGREE OF Master of Technology in ‘Power Control and Drives’ By SOBHA CHANDRA BARIK Department of Electrical Engineering National Institute of Technology Rourkela Orissa May-2007 SLIDING MODE VECTOR CONTROL OF THREE PHASE INDUCTION MOTOR A THESIS SUBMITTED IN PARTIAL FULFILLMENT OF THE REQUIREMENTS FOR THE DEGREE OF Master of Technology in ‘Power Control and Drives’ By SOBHA CHANDRA BARIK Under the guidance of Dr. K.B. MOHANTY Department of Electrical Engineering National Institute of Technology Rourkela Orissa May-2007 CERTIFICATE This is to certify that the work in this thesis entitled “Sliding Mode Vector Control of three phase induction motor” by Sobha Chandra Barik, has been carried out under my supervision in partial fulfillment of the requirements for the degree of Master of Technology in ‘Power Control and Drives’ during session 2006-2007 in the Department of Electrical Engineering, National Institute of Technology, Rourkela and this work has not been submitted elsewhere for a degree. To the best of my knowledge and belief, this work has not been submitted to any other university or institution for the award of any degree or diploma. Dr. K.B.Mohanty Place: Date: Asst. Professor Dept. of Electrical Engineering National Institute of Technology, Rourkela ACKNOWLEDGEMENTS On the submission of my Thesis report of “Sensorless Sliding mode Vector control of three phase induction motor”, I would like to extend my gratitude & my sincere thanks to my supervisor Dr. K. B. Mohanty, Asst. Professor, Department of Electrical Engineering for his constant motivation and support during the course of my work in the last one year. -
Simplex Sliding Mode Control of Multi-Input Systems with ⋆ Chattering Reduction and Mono-Directional Actuators
Simplex Sliding Mode Control of Multi-Input Systems with ⋆ Chattering Reduction and Mono-Directional Actuators Giorgio Bartolini a, Elisabetta Punta b, Tullio Zolezzi c aDepartment of Electrical and Electronic Engineering, University of Cagliari, Piazza d’Armi - 09123 Cagliari, Italy. bInstitute of Intelligent Systems for Automation, National Research Council of Italy, Via De Marini, 6 - 16149 Genoa, Italy. cDepartment of Mathematics, University of Genoa, Via Dodecaneso, 35 - 16146 Genoa, Italy. Abstract This paper analyzes features and problems related to the application of the simplex sliding mode control to systems with mono- directional actuators and integrators in the input channel. The plain use of the method formulated in previous contributions results in unacceptable behaviors, such as control laws (the output of the mono-directional actuators), which increase without bounds. It is proposed a non trivial modification of the original algorithm; the new simplex strategy allows the perfect fulfillment of the control objectives by means of bounded inputs from the actuators. Key words: Simplex sliding mode control; Multi-input systems; Chattering reduction; Uncertain dynamic systems. 1 Introduction The simplex sliding mode control methodology dates back to the pioneering work of Bajda and Izosimov, [1], and it was extensively analyzed in previous papers, [6], [7]. In the recent work [7] a class of uncertain nonlinear non affine control systems has been dealt with by this control strategy applied to the first time derivative of the actual control vector. In principle this “trick” (negligible dynamics of actuators and sensors) counteracts the chattering phenomenon, which is often considered the main drawback of the sliding mode control methodology, in practice it allows to reduce the phenomenon to an acceptable, high frequency, small amplitude perturbation of the ideal control law. -
A Comparative Study of the Extended Kalman Filter and Sliding Mode Observer for Orbital Determination for Formation Flying About the L(2) Lagrange Point
University of New Hampshire University of New Hampshire Scholars' Repository Master's Theses and Capstones Student Scholarship Spring 2007 A comparative study of the extended Kalman filter and sliding mode observer for orbital determination for formation flying about the L(2) Lagrange point Oliver Olson University of New Hampshire, Durham Follow this and additional works at: https://scholars.unh.edu/thesis Recommended Citation Olson, Oliver, "A comparative study of the extended Kalman filter and sliding mode observer for orbital determination for formation flying about the L(2) Lagrange point" (2007). Master's Theses and Capstones. 275. https://scholars.unh.edu/thesis/275 This Thesis is brought to you for free and open access by the Student Scholarship at University of New Hampshire Scholars' Repository. It has been accepted for inclusion in Master's Theses and Capstones by an authorized administrator of University of New Hampshire Scholars' Repository. For more information, please contact [email protected]. A COMPARATIVE STUDY OF THE EXTENDED KALMAN FILTER AND SLIDING MODE OBSERVER FOR ORBITAL DETERMINATION FOR FORMATION FLYING ABOUT THE L2 LAGRANGE POINT BY OLIVER OLSON B.S., University of New Hampshire, 2004 THESIS Submitted to the University of New Hampshire in partial fulfillment of the requirements for the degree of Master of Science in Mechanical Engineering May 2007 Reproduced with permission of the copyright owner. Further reproduction prohibited without permission. UMI Number: 1443625 INFORMATION TO USERS The quality of this reproduction is dependent upon the quality of the copy submitted. Broken or indistinct print, colored or poor quality illustrations and photographs, print bleed-through, substandard margins, and improper alignment can adversely affect reproduction. -
Smooth Fractional Order Sliding Mode Controller for Spherical Robots with Input Saturation
applied sciences Article Smooth Fractional Order Sliding Mode Controller for Spherical Robots with Input Saturation Ting Zhou, Yu-gong Xu and Bin Wu * School of Mechanical, Electronic and Control Engineering, Beijing Jiaotong University, Beijing 100044, China; [email protected] (T.Z.); [email protected] (Y.-g.X.) * Correspondence: [email protected]; Tel.: +86-138-1171-6598 Received: 15 February 2020; Accepted: 12 March 2020; Published: 20 March 2020 Abstract: This study considers the control of spherical robot linear motion under input saturation. A fractional sliding mode controller that combines fractional order calculus and the hierarchical sliding mode control method is proposed for the spherical robot. Employing this controller, an auxiliary system in which a filter was used to gain smooth control performance was designed to overcome the input saturation. Based on the Lyapunov stability theorem, the closed-loop system was globally stable and the desired state was achieved using the fractional sliding mode controller. The advantages of the proposed controller are illustrated by comparing the simulation results from the fractional order sliding mode controllers and the integer order controller. Keywords: fractional sliding mode control; spherical robot; linear motion; input saturation 1. Introduction Spherical robots are a new type of robot with a ball-shaped exterior shell. Their advantages, such as the lower energy consumption and enhanced locomotion compared to traditional wheeled or legged mobile robots have motivated many researchers to develop them with different structures in recent decades [1–6]. The inner parts are hermetically sealed inside the spherical shell, resulting in increased reliability in hostile environments, making them suitable for security and exploratory tasks [7,8]. -
Design of Terminal Sliding Mode Controllers for Disturbed Non-Linear Systems Described by Matrix Differential Equations of the Second and First Orders
applied sciences Article Design of Terminal Sliding Mode Controllers for Disturbed Non-Linear Systems Described by Matrix Differential Equations of the Second and First Orders Paweł Skruch * and Marek Długosz Department of Automatic Control and Robotics, AGH University of Science and Technology, al. A. Mickiewicza 30, 30-059 Krakow, Poland; [email protected] * Correspondence: [email protected] Received: 2 February 2019; Accepted: 1 June 2019; Published: 6 June 2019 Abstract: This paper describes a design scheme for terminal sliding mode controllers of certain types of non-linear dynamical systems. Two classes of such systems are considered: the dynamic behavior of the first class of systems is described by non-linear second-order matrix differential equations, and the other class is described by non-linear first-order matrix differential equations. These two classes of non-linear systems are not completely disjointed, and are, therefore, investigated together; however, they are certainly not equivalent. In both cases, the systems experience unknown disturbances which are considered bounded. Sliding surfaces are defined by equations combining the state of the system and the expected trajectory. The control laws are drawn to force the system trajectory from an initial condition to the defined sliding surface in finite time. After reaching the sliding surface, the system trajectory remains on it. The effectiveness of the approaches proposed is verified by a few computer simulation examples. Keywords: non-linear dynamical system; disturbance; sliding mode control; sliding surface 1. Introduction 1.1. Motivation Stabilization of non-linear systems finds applications in many areas of engineering, particularly in the fields of mechanics, robotics, electronics, and so on [1,2]. -
Speed Controller of Three Phase Induction Motor Using Sliding Mode Controller
52 DOI: https://doi.org/10.33103/uot.ijccce.19.1.7 Speed Controller of Three Phase Induction Motor Using Sliding Mode Controller Dr.Farazdaq R.Yaseen1,Walaa H. Nasser2 1,2Control and System Eng. Dep.at Unversity of Technology [email protected],[email protected] Abstract— A Sliding Mode Control (SMC) with integral surface is employed to control the speed of Three-Phase Induction Motor in this paper. The strategy used is a modified field oriented control to control the IM drive system. The SMC is used to calculate the frequency required for generating three phase voltage of Space vVector Pulse Width Modulation (SVPWM) invertor. When the SMC is used with current controller, the quadratic component of stator current is estimated by the controller. Instead of using current controller, this paper proposed estimating the frequency of stator voltage whereas the slip speed is representing a function of the quadratic current. The simulation results of using the SMC showed that a good dynamic response can be obtained under load disturbances as compared with the classical PI controller; the complete mathematical model of the system is described and simulated in MATLAB/SIMULINK. Index Terms— Induction Motor, Space Vector Pulse Width Modulation, Sliding Mode Control and Field Oriented Control. I. INTRODUCTION The three phase Induction Motors (IM) have earned a great interest in the recent years and used widely in industrial applications such as robotics, paper and textile mills and hybrid vehicles due to their low cost, high torque to size ratio, reliability, versatility, ruggedness, high durability, and the ability to work in various environments. -
Mathematical Basis of Sliding Mode Control of an Uninterruptible Power Supply
Acta Polytechnica Hungarica Vol. 11, No. 3, 2014 Mathematical Basis of Sliding Mode Control of an Uninterruptible Power Supply Károly Széll and Péter Korondi Budapest University of Technology and Economics, Hungary Bertalan Lajos u. 4-6, H-1111 Budapest, Hungary [email protected]; [email protected] The sliding mode control of Variable Structure Systems has a unique role in control theories. First, the exact mathematical treatment represents numerous interesting challenges for the mathematicians. Secondly, in many cases it can be relatively easy to apply without a deeper understanding of its strong mathematical background and is therefore widely used in the field of power electronics. This paper is intended to constitute a bridge between the exact mathematical description and the engineering applications. The paper presents a practical application of the theory of differential equation with discontinuous right hand side proposed by Filippov for an uninterruptible power supply. Theoretical solutions, system equations, and experimental results are presented. Keywords: sliding mode control; variable structure system; uninterruptable power supply 1 Introduction Recently most of the controlled systems are driven by electricity as it is one of the cleanest and easiest (with smallest time constant) to change (controllable) energy source. The conversion of electrical energy is solved by power electronics [1]. One of the most characteristic common features of the power electronic devices is the switching mode. We can switch on and off the semiconductor elements of the power electronic devices in order to reduce losses because if the voltage or current of the switching element is nearly zero, then the loss is also near to zero. -
Conventional and Second Order Sliding Mode Control of Permanent Magnet Synchronous Motor † Fed by Direct Matrix Converter: Comparative Study
energies Article Conventional and Second Order Sliding Mode Control of Permanent Magnet Synchronous Motor y Fed by Direct Matrix Converter: Comparative Study Abdelhakim Dendouga LI3CUB-Research Lab., Department of Electrical Engineering, University of Biskra, 07000 Biskra, Algeria; [email protected]; Tel.: +213-6-7400-6720 This Paper Is an Extended Version of Our Paper Published in 20th IEEE International Conference on y Environment and Electrical Engineering (EEEIC 2020), Web Conference, Madrid, Spain, 9–12 June 2020, pp. 1867–1871. Received: 25 August 2020; Accepted: 25 September 2020; Published: 30 September 2020 Abstract: The main objective of this work revolves around the design of second order sliding mode controllers (SOSMC) based on the super twisting algorithm (STA) for asynchronous permanent magnet motor (PMSM) fed by a direct matrix converter (DMC), in order to improve the effectiveness of the considered drive system. The SOSMC was selected to minimize the chattering phenomenon caused by the conventional sliding mode controller (SMC), as well to decrease the level of total harmonic distortion (THD) produced by the drive system. In addition, the literature has taken a great interest in the STA due to its robustness to modeling errors and to external disturbances. Furthermore, due to its low conduction losses, the space vector approach was designated as a switching law to control the DMC. In addition, the topology and design method of the damped passive filter, which allows improvement of the waveform and attenuation of the harmonics of the input current, have been detailed. Finally, to discover the strengths and weaknesses of the proposed control approach based on SOSMC, a comparative study between the latter and that using the conventional SMC was executed. -
Proportional-Integral Sliding Mode Control with an Application in the Balance Control of a Two-Wheel Vehicle System
applied sciences Article Proportional-Integral Sliding Mode Control with an Application in the Balance Control of a Two-Wheel Vehicle System Chien-Hong Lin 1 and Fu-Yuen Hsiao 2,* 1 Aeronautical Systems Research Division, National Chung-Shan Institute of Science and Technology, Taichung 40722, Taiwan; [email protected] 2 Department of Aerospace Engineering, Tamkang University, New Taipei 25137, Taiwan * Correspondence: [email protected]; Tel.: +886-2-26215656 (ext. 3319) Received: 29 May 2020; Accepted: 22 July 2020; Published: 24 July 2020 Abstract: A balance control method, the proportional-integral sliding mode control (PISMC), is proposed to control the tilt attitude of an experimental two-wheel vehicle system (TWVS). Based on our previous work of implementing a generalized PISMC to control a linearized dynamical system, this paper extends the algorithm to a wider range: First, the control design of a weighted-control system is proposed. Secondly, our algorithm was realized and verified in a TWVS using its original nonlinear model. Thirdly, a systematical way to tune parameters are presented. The robustness of the proposed algorithm is also discussed in this paper. The simulation results of this work validate that the PISMC has better robustness to counteract the external disturbances than the conventional sliding mode control (SMC) does. Additionally, the experimental results show that the PISMC is capable of autonomously balancing the TWVS more effectively than the conventional SMC. The successful implementation of our algorithm potentially extends the implementation of the PISMC to various nonlinear and emerging systems. Keywords: proportional-integral sliding mode control; sliding mode control; two-wheel vehicle system; nonlinear system 1. -
Adaptive Fast Smooth Second-Order Sliding Mode Control for Attitude Tracking of a 3-DOF Helicopter
Adaptive Fast Smooth Second-Order Sliding Mode Control for Attitude Tracking of a 3-DOF Helicopter Xidong Wang, Zhan Li, Zhen He, Huijun Gao Abstract—This paper presents a novel adaptive fast smooth second-order sliding mode control for the atti- tude tracking of the three degree-of-freedom (3-DOF) heli- copter system with lumped disturbances. Combining with a non-singular integral sliding mode surface, we propose a novel adaptive fast smooth second-order sliding mode control method to enable elevation and pitch angles to track given desired trajectories respectively with the features of non-singularity, adaptation to disturbances, chattering suppression and fast finite-time convergence. In addition, a novel adaptive-gain smooth second-order sliding mode observer is proposed to compensate time-varying lumped disturbances with the smoother output compared with the adaptive-gain second-order sliding mode observer. The fast finite-time convergence of the closed-loop system with constant disturbances and the fast finite-time uniformly ultimately boundedness of the closed-loop system with the time-varying lumped disturbances are proved with the finite-time Lyapunov stability theory. Finally, the effective- Fig. 1. Structure of 3-DOF helicopter system with ADS ness and superiority of the proposed control methods are verified by comparative simulation experiments. Index Terms—Adaptive fast smooth second-order sliding mode control (AFSSOSMC), adaptive-gain smooth second- [4], [5], nonlinear control [2], [6]–[9] and intelligent control order sliding mode observer (ASSOSMO), 3-DOF helicopter. [10]–[12]. Among all the above-mentioned control methods, sliding mode control has attracted much attention because of its I. -
Extended Kalman Filter Based Sliding Mode Control of Parallel-Connected Two Five-Phase PMSM Drive System
Article Extended Kalman Filter Based Sliding Mode Control of Parallel-Connected Two Five-Phase PMSM Drive System Tounsi Kamel 1, Djahbar Abdelkader 1, Barkat Said 2, Sanjeevikumar Padmanaban 3 and Atif Iqbal 4,* 1 Department of Electrical Engineering, LGEER laboratory, U.H.B.B-Chlef University, Chlef 02000, Algeria; [email protected] (T.K.); [email protected] (D.A.) 2 Laboratoire de Génie Électrique, Faculté de Technologie, Université de M’Sila, M’Sila 28000, Algeria; [email protected] 3 Department of Energy Technology, Aalborg University, 6700 Esberg, Denmark; [email protected] 4 Department of Electrical Engineering Qatar University, Doha, Qatar; [email protected] * Correspondence: [email protected]; Tel.: +97-433-276-330 Received: 19 December 2017; Accepted: 19 January 2018; Published: 26 January 2018 Abstract: This paper presents sliding mode control of sensor-less parallel-connected two five-phase permanent magnet synchronous machines (PMSMs) fed by a single five-leg inverter. For both machines, the rotor speeds and rotor positions as well as load torques are estimated by using Extended Kalman Filter (EKF) scheme. Fully decoupled control of both machines is possible via an appropriate phase transposition while connecting the stator windings parallel and employing proposed speed sensor-less method. In the resulting parallel-connected two-machine drive, the independent control of each machine in the group is achieved by controlling the stator currents and speed of each machine under vector control consideration. The effectiveness of the proposed Extended Kalman Filter in conjunction with the sliding mode control is confirmed through application of different load torques for wide speed range operation.