A Simultaneous Conversion and Extraction of Furfural from Pentose in Dilute Acid Hydrolysate of Quercus Mongolica Using an Aqueous Biphasic System
Total Page:16
File Type:pdf, Size:1020Kb
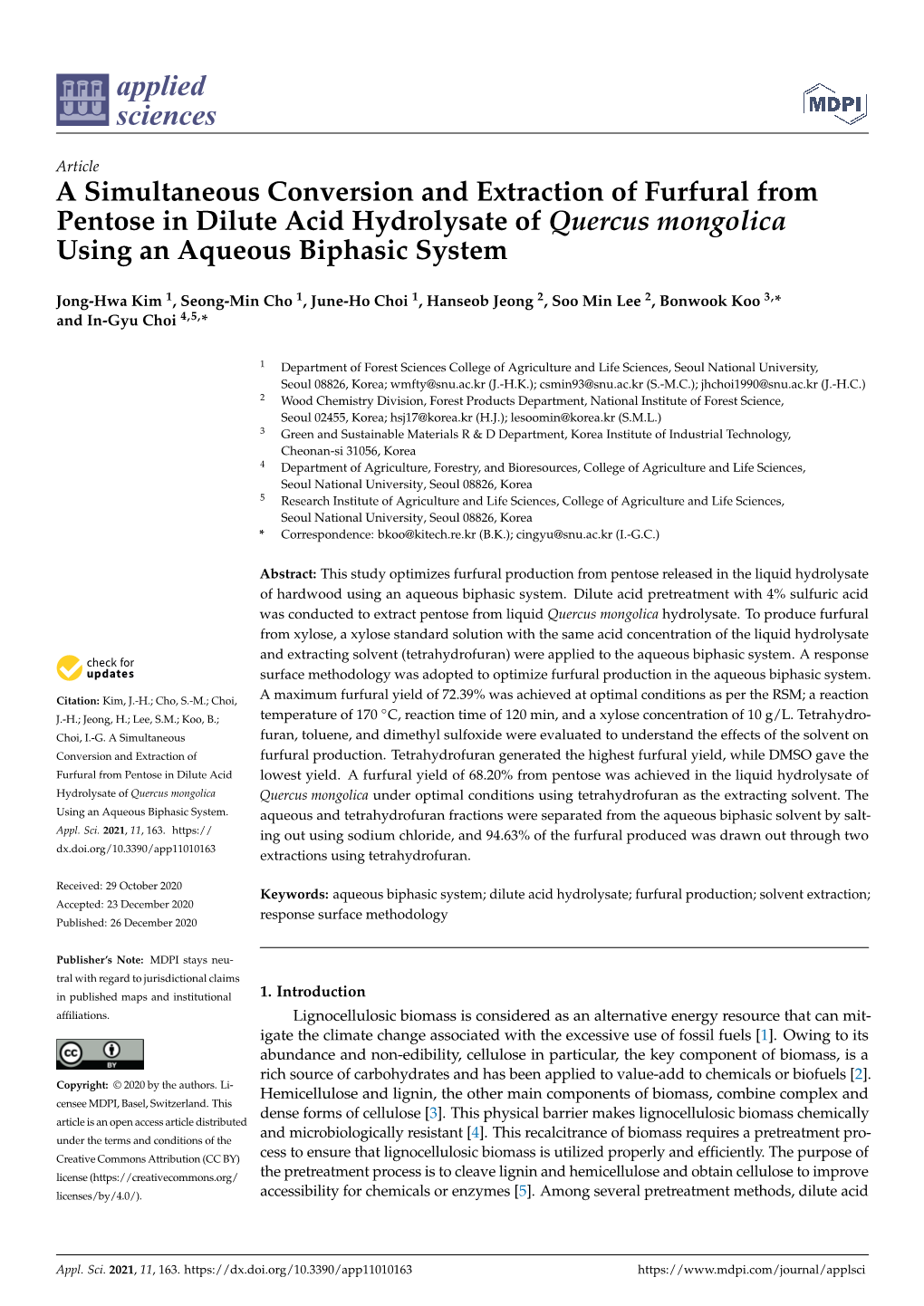
Load more
Recommended publications
-
2-FURALDEHYDE (Furfural)
EU RISK ASSESSMENT – FURFURAL FINAL SUMMARY, FEBRUARY 2008 2-FURALDEHYDE (Furfural) CAS No: 98-01-1 EINECS No: 202-627-7 SUMMARY RISK ASSESSMENT REPORT Final report, February 2008 The Netherlands FINAL APPROVED VERSION Rapporteur for the risk assessment of furfural is the Ministry of Housing, Spatial Planning and the Environment (VROM) and the Ministry of Social Affairs and Employment (SZW), in consultation with the Ministry of Public Health, Welfare and Sport (VWS). Responsible for the risk evaluation and subsequently for the contents of this report is the rapporteur. The scientific work on this report has been prepared by the Netherlands Organization for Applied Scientific Research (TNO) and the National Institute of Public Health and Environment (RIVM), by order of the rapporteur. Contact point: Chemical Substances Bureau P.O. Box 1 3720 BA Bilthoven The Netherlands EU RISK ASSESSMENT – FURFURAL Date of Last Literature Search: March, 2006 Review of report by MS Technical Experts finalised: June, 2006 Final report: February 2008 © European Communities, [ECB: year of publication] EU RISK ASSESSMENT – FURFURAL PREFACE This report provides a summary, with conclusions, of the risk assessment report of the substance 2-furaldehyde that has been prepared by The Netherlands in the context of Council Regulation (EEC) No. 793/93 on the evaluation and control of existing substances. For detailed information on the risk assessment principles and procedures followed, the underlying data and the literature references the reader is referred to the comprehensive Final Risk Assessment Report (Final RAR) that can be obtained from the European Chemicals Bureau1. The Final RAR should be used for citation purposes rather than this present Summary Report. -
Risto Laitinen/August 4, 2016 International Union of Pure and Applied Chemistry Division VIII Chemical Nomenclature and Structur
Approved Minutes, Busan 2015 Risto Laitinen/August 4, 2016 International Union of Pure and Applied Chemistry Division VIII Chemical Nomenclature and Structure Representation Approved Minutes of Division Committee Meeting in Busan, Korea, 8–9 August, 2015 1. Welcome, introductory remarks and housekeeping announcements Karl-Heinz Hellwich (KHH) welcomed everybody to the meeting, extending a special welcome to those who were attending the Division Committee meeting for the first time. He described house rules and arrangements during the meeting. KHH also regretfully reported that it has come to his attention that since the Bangor meeting in August 2014, Prof. Derek Horton (Member, Division VIII task groups on Carbohydrate and Flavonoids nomenclature; Associate Member, IUBMB-IUPAC Joint Commission on Biochemical Nomenclature) and Dr. Libuse Goebels, Member of the former Commission on Nomenclature of Organic Chemistry) have passed away. The meeting attendees paid a tribute to their memory by a moment of silence. 2. Attendance and apologies Present: Karl-Heinz Hellwich (president, KHH) , Risto Laitinen (acting secretary, RSL), Richard Hartshorn (past-president, RMH), Michael Beckett (MAB), Alan Hutton (ATH), Gerry P. Moss (GPM), Michelle Rogers (MMR), Jiří Vohlídal (JV), Andrey Yerin (AY) Observers: Leah McEwen (part time, chair of proposed project, LME), Elisabeth Mansfield (task group chair, EM), Johan Scheers (young observer, day 1; JS), Prof. Kazuyuki Tatsumi (past- president of the union, part of day 2) Apologies: Ture Damhus (secretary, TD), Vefa Ahsen, Kirill Degtyarenko, Gernot Eller, Mohammed Abul Hashem, Phil Hodge (PH), Todd Lowary, József Nagy, Ebbe Nordlander (EN), Amélia Pilar Rauter (APR), Hinnerk Rey (HR), John Todd, Lidija Varga-Defterdarović. -
Supporting Information Highly Efficient Formic Acid-Mediated Oxidation Of
Electronic Supplementary Material (ESI) for Green Chemistry. This journal is © The Royal Society of Chemistry 2016 Supporting Information Highly Efficient Formic Acid-Mediated Oxidation of Renewable Furfural to Maleic Acid with H2O2 Xiukai Li, Ben Ho, Diane S. W. Lim and Yugen Zhang* Table of Contents General Information ...................................................................................................................1 Experimental Procedure .............................................................................................................2 Extended Optimization Tables...................................................................................................2 Identification of Reaction Intermediates....................................................................................4 Reaction Pathways for H2O2 Oxidation of Furfural to Maleic Acid..........................................7 General Information Materials: all starting materials are commercially available and were used as received, unless otherwise indicated. Furfural (> 98%), formic acid (> 98%), and acetic acid (glacial) were purchased from Merck. Amberlyst 15, hydrogen peroxide (31%), propionic acid, and butyric acid were purchased from Sigma-Aldrich. The other chemicals not stated here were either purchased from Sigma-Aldrich, Merck, or Fisher Scientific. Product analysis: analysis of the reactant and product in the oxidation of furfural to maleic acid was performed using HPLC (Agilent Technologies, 1200 series) with UV (254 nm and 280 -
TOXICOLOGY and EXPOSURE GUIDELINES ______(For Assistance, Please Contact EHS at (402) 472-4925, Or Visit Our Web Site At
(Revised 1/03) TOXICOLOGY AND EXPOSURE GUIDELINES ______________________________________________________________________ (For assistance, please contact EHS at (402) 472-4925, or visit our web site at http://ehs.unl.edu/) "All substances are poisons; there is none which is not a poison. The right dose differentiates a poison and a remedy." This early observation concerning the toxicity of chemicals was made by Paracelsus (1493- 1541). The classic connotation of toxicology was "the science of poisons." Since that time, the science has expanded to encompass several disciplines. Toxicology is the study of the interaction between chemical agents and biological systems. While the subject of toxicology is quite complex, it is necessary to understand the basic concepts in order to make logical decisions concerning the protection of personnel from toxic injuries. Toxicity can be defined as the relative ability of a substance to cause adverse effects in living organisms. This "relative ability is dependent upon several conditions. As Paracelsus suggests, the quantity or the dose of the substance determines whether the effects of the chemical are toxic, nontoxic or beneficial. In addition to dose, other factors may also influence the toxicity of the compound such as the route of entry, duration and frequency of exposure, variations between different species (interspecies) and variations among members of the same species (intraspecies). To apply these principles to hazardous materials response, the routes by which chemicals enter the human body will be considered first. Knowledge of these routes will support the selection of personal protective equipment and the development of safety plans. The second section deals with dose-response relationships. -
Synthesis of Furfuryl Alcohol from Furfural
Synthesis of Furfuryl Alcohol from Furfural: A Comparison between Batch and Continuous Flow Reactors Maïté Audemar, Yantao Wang, Deyang Zhao, Sébastien Royer, François Jerome, Christophe Len, Karine de Oliveira Vigier To cite this version: Maïté Audemar, Yantao Wang, Deyang Zhao, Sébastien Royer, François Jerome, et al.. Synthesis of Furfuryl Alcohol from Furfural: A Comparison between Batch and Continuous Flow Reactors. Energies, MDPI, 2020, 13 (4), pp.1002. 10.3390/en13041002. hal-03015037 HAL Id: hal-03015037 https://hal.archives-ouvertes.fr/hal-03015037 Submitted on 19 Nov 2020 HAL is a multi-disciplinary open access L’archive ouverte pluridisciplinaire HAL, est archive for the deposit and dissemination of sci- destinée au dépôt et à la diffusion de documents entific research documents, whether they are pub- scientifiques de niveau recherche, publiés ou non, lished or not. The documents may come from émanant des établissements d’enseignement et de teaching and research institutions in France or recherche français ou étrangers, des laboratoires abroad, or from public or private research centers. publics ou privés. 1 Communication 2 Synthesis of furfuryl alcohol from furfural: a 3 comparison between batch and continuous flow 4 reactors 5 Maïté Audemar 1, Yantao Wang 2,3, Deyang Zhao 2,4, Sébastien Royer,5 François Jérôme,1 6 Christophe Len 2,4 and Karine De Oliveira Vigier 1,* 7 1 Université de Poitiers, IC2MP, UMR CNRS 7285, 1 rue Marcel Doré, 86073 Poitiers Cedex 9; 8 [email protected] 9 2 Sorbonne universités, Université de Technologie de Compiègne, Centre de recherche Royallieu, CS 60 319, 10 F-60203 Compiègne cedex, France 11 3 School of Resources Environmental & Chemical Engineering, Nanchang university, Nanchang, 12 330031,China. -
Recovery of Furfural and Acetic Acid from Wood Hydrolysates in Biotechnological Downstream Processing
Nadia Galeottia, Fabian Jiraseka, Jakob Burgerb,*, Hans Hassea Recovery of furfural and acetic acid from wood hydrolysates in biotechnological downstream processing Abstract Wood hydrolysates contain sugars that can be used as feedstock in fermentation processes. For that purpose, the hydrolysate must be concentrated and inhibitors that harm fermentation must be removed. Herein, the integration of these tasks with the recovery of inhibitors is studied. The wood hydrolysate is represented as a mixture of water, xylose, acetic acid, and furfural. Acetic acid and furfural are two frequently occurring inhibitors and valuable chemicals, and thus, their recovery is studied. Furfural is recovered from the vapors by heteroazeotropic distillation. It is shown that this can be achieved without additional energy. The recovery of acetic acid by distillation is also possible, but not attractive. The new process is simulated by using a thermodynamic model based on experimental data. Keywords: acetic acid, furfural, heteroazeotropic distillation, wood hydrolysates aLaboratory of Engineering Thermodynamics (LTD), University of Kaiserslautern, Erwin- Schrödinger Straße 44, 67663 Kaiserslautern, Germany bChair for Chemical Process Engineering, Technical University of Munich, Campus Straubing for Biotechnology and Sustainability, 94315 Straubing, Germany *Corresponding author Email address: [email protected] (Jakob Burger) 1. Introduction The production of chemicals, polymers, and fuels from biomass is becoming increasingly important [1-3]. One of the most widely used biomass feedstock is lignocellulosic biomass. It is available e.g. in large amounts in the pulp and paper industry. Hydrolysates of lignocellulosic biomass contain sugars that can be used in fermentations which yield desired products such as ethanol [4-8]. However, the raw hydrolysates are not suited for the fermentation, firstly because the sugar concentration is too low, and secondly because they contain components that are toxic for the microorganisms, the so-called inhibitors. -
Base-Free Synthesis of Furfurylamines from Biomass
catalysts Communication CommunicationBase-Free Synthesis of Furfurylamines from Biomass Furans Base-Free Synthesis of Furfurylamines from Biomass Furans Using Ru Pincer Complexes Using Ru Pincer Complexes Danielle Lobo Justo Pinheiro and Martin Nielsen * Danielle Lobo Justo Pinheiro and Martin Nielsen * Department of Chemistry, Technical University of Denmark, DK-2800 Kgs. Lyngby, Denmark; [email protected] of Chemistry, Technical University of Denmark, DK-2800 Kgs. Lyngby, Denmark; [email protected] ** Correspondence:Correspondence:[email protected]; [email protected];Tel.: Tel.:+45-24651045 +45-24651045 Abstract: WeWe reportreport thethe firstfirst exampleexample ofof employingemploying homogeneoushomogeneous organometal-catalyzedorganometal-catalyzed transfertransfer hydrogenation for the selectiveselective reductivereductive aminationamination ofof furfuralsfurfurals toto furfurylamines.furfurylamines. An efficient,efficient, chemoselective, andand base-freebase-free methodmethod isis describeddescribed usingusing Ru-MACHO-BHRu-MACHO-BH asas catalystcatalyst andand iiPrOHPrOH asas H donor. The method toleratestolerates aa rangerange ofof substituentssubstituents affordingaffording moderatemoderate toto excellentexcellent yields.yields. Keywords: transfer hydrogenation; furfurals;furfurals; furfurylamine;furfurylamine; reductivereductive amination;amination; Ru-MACHORu-MACHO 1. Introduction The development of sustainable techniques to transform biomass into useful com- pounds is one of of the the biggest biggest challenges -
Some Furfural Condensation Products John Henry Jensen Jr
Iowa State University Capstones, Theses and Retrospective Theses and Dissertations Dissertations 1948 Some furfural condensation products John Henry Jensen Jr. Iowa State College Follow this and additional works at: https://lib.dr.iastate.edu/rtd Part of the Chemical Engineering Commons Recommended Citation Jensen, John Henry Jr., "Some furfural condensation products " (1948). Retrospective Theses and Dissertations. 13870. https://lib.dr.iastate.edu/rtd/13870 This Dissertation is brought to you for free and open access by the Iowa State University Capstones, Theses and Dissertations at Iowa State University Digital Repository. It has been accepted for inclusion in Retrospective Theses and Dissertations by an authorized administrator of Iowa State University Digital Repository. For more information, please contact [email protected]. INFORMATION TO USERS This manuscript has been reproduced from the microfilm master. UMI films the text directly from the original or copy submitted. Thus, some thesis and dissertation copies are in typewriter face, while others may be from any type of computer printer. The quality of this reproduction is dependent upon the quality of the copy submitted. Broken or indistinct print, colored or poor quality illustrations and photographs, print bleedthrough, substandard margins, and improper alignment can adversely affect reproduction. In the unlikely event that the author did not send UMI a complete manuscript and there are missing pages, these v\/ill be noted. Also, if unauthorized copyright material had to be removed, a note will indicate the deletion. Oversize materials (e.g., maps, drawings, charts) are reproduced by sectioning the original, beginning at the upper left-hand comer and continuing from left to right in equal sections with small overiaps. -
Download Download
IMPROVEMENT OF A FURFURAL DISTILLATION PLANT By P. STEINGASZNER, A. Ri.LINT and M. KOJNOK Department of Chemical Technology, Technical University Budapest (Received July 1, 1976) Presented by Assoc. Prof. I. SZEBENYI 1. Introduction Furfural is an important chemical, due to its unsaturated bonds and aldehyde group. It is extensively used in plastics and paint manufacture and in precision casting. Furfural is produced from pentosane-containing agricultural wastes (corncobs, coconut seed hulls etc.) and from hard woods (mainly birch) by acid hydrolysis and subsequent dehydration according to the following equations: H.O C5H 80 4 --=-----+ C5H lO0 5 Pentosane Pentose -H,O'" '-, '" It is also formed as a by-product in wood pulp manufacture where it can be recovered from the effluent by steam stripping. Steam hydrolysis of pentosane-containing materials yields a reaction product containing 4-6% by weight of furfural, 2-5% of acetic acid, some tenth of a per cent of methyl alcohol and various, mostly unidentified com pounds in trace amounts. 2. Recovery of furfural by distillation 2.1. Conventional flow scheme The hydrolysis product is processed by multistep distillation. A con ventional sequence of distillation steps is shown in Fig. 1. The hydrolyzate is fed to a continuous distillation tower 1 provided with side-draw facilities in the rectifying section above the feed inlet plate. The bottom product consists of water and acetic acid; the liquid side-draw 60 P. STE1.YGASZ.YER et al. product contains 25 to 35 % by weight of furfural with small amounts of methyl alcohol and acids, the rest being water; the top product is mainly methyl alcohol. -
Formic Acid Catalysed Xylose Dehydration Into Furfural
C543etukansi.kesken.fm Page 1 Thursday, September 3, 2015 12:37 PM C 543 OULU 2015 C 543 UNIVERSITY OF OULU P.O. Box 8000 FI-90014 UNIVERSITY OF OULU FINLAND ACTA UNIVERSITATISUNIVERSITATIS OULUENSISOULUENSIS ACTA UNIVERSITATIS OULUENSIS ACTAACTA TECHNICATECHNICACC Kaisa Lamminpää Kaisa Lamminpää Professor Esa Hohtola FORMIC ACID CATALYSED University Lecturer Santeri Palviainen XYLOSE DEHYDRATION Postdoctoral research fellow Sanna Taskila INTO FURFURAL Professor Olli Vuolteenaho University Lecturer Veli-Matti Ulvinen Director Sinikka Eskelinen Professor Jari Juga University Lecturer Anu Soikkeli Professor Olli Vuolteenaho UNIVERSITY OF OULU GRADUATE SCHOOL; UNIVERSITY OF OULU FACULTY OF TECHNOLOGY Publications Editor Kirsti Nurkkala ISBN 978-952-62-0913-5 (Paperback) ISBN 978-952-62-0914-2 (PDF) ISSN 0355-3213 (Print) ISSN 1796-2226 (Online) ACTA UNIVERSITATIS OULUENSIS C Technica 543 KAISA LAMMINPÄÄ FORMIC ACID CATALYSED XYLOSE DEHYDRATION INTO FURFURAL Academic dissertation to be presented with the assent of the Doctoral Training Committee of Technology and Natural Sciences of the University of Oulu for public defence in Kuusamonsali (YB210), Linnanmaa, on 16 October 2015, at 12 noon UNIVERSITY OF OULU, OULU 2015 Copyright © 2015 Acta Univ. Oul. C 543, 2015 Supervised by Professor Juha Tanskanen Doctor Juha Ahola Reviewed by Professor Tapio Salmi Associate Professor Wiebren de Jong Opponent Docent Arto Laari ISBN 978-952-62-0913-5 (Paperback) ISBN 978-952-62-0914-2 (PDF) ISSN 0355-3213 (Printed) ISSN 1796-2226 (Online) Cover Design Raimo Ahonen JUVENES PRINT TAMPERE 2015 Lamminpää, Kaisa, Formic acid catalysed xylose dehydration into furfural University of Oulu Graduate School; University of Oulu, Faculty of Technology Acta Univ. Oul. -
Single Step Process for Conversion of Furfural to Tetrahydrofuran
(19) TZZ ___T (11) EP 2 951 165 B1 (12) EUROPEAN PATENT SPECIFICATION (45) Date of publication and mention (51) Int Cl.: of the grant of the patent: C07D 307/08 (2006.01) 04.10.2017 Bulletin 2017/40 (86) International application number: (21) Application number: 14724507.0 PCT/IN2014/000072 (22) Date of filing: 30.01.2014 (87) International publication number: WO 2014/118806 (07.08.2014 Gazette 2014/32) (54) SINGLE STEP PROCESS FOR CONVERSION OF FURFURAL TO TETRAHYDROFURAN EINSTUFIGES VERFAHREN ZUR UMWANDLUNG VON FURFURAL IN TETRAHYDROFURAN PROCÉDÉ EN UNE ÉTAPE POUR LA CONVERSION DE FURFURAL EN TÉTRAHYDROFURANE (84) Designated Contracting States: (74) Representative: Towler, Philip Dean AL AT BE BG CH CY CZ DE DK EE ES FI FR GB Dehns GR HR HU IE IS IT LI LT LU LV MC MK MT NL NO St Bride’s House PL PT RO RS SE SI SK SM TR 10 Salisbury Square London EC4Y 8JD (GB) (30) Priority: 30.01.2013 IN 249DE2013 (56) References cited: (43) Date of publication of application: US-A1- 2010 099 895 09.12.2015 Bulletin 2015/50 • SURAPAS SITTHISA ET AL: (73) Proprietor: Council of Scientific and Industrial "Hydrodeoxygenation of Furfural Over Research Supported Metal Catalysts: A Comparative Study New Delhi- 110001 (IN) of Cu, Pd and Ni", CATALYSIS LETTERS, KLUWER ACADEMIC PUBLISHERS-PLENUM (72) Inventors: PUBLISHERS, NE, vol. 141, no. 6, 29 March 2011 • RODE, Chandrasekhar, Vasant (2011-03-29), pages784-791, XP019905804, ISSN: Pune 411008 1572-879X, DOI: 10.1007/S10562-011-0581-7 Maharashtra (IN) • EDUARDO J. GARCÍA-SUÁREZ ET AL: "Versatile • BIRADAR, Narayan Shamrao dual hydrogenation-oxidation nanocatalysts for Pune 411008 the aqueous transformation of biomass-derived Maharashtra (IN) platform molecules", GREEN CHEMISTRY, vol. -
SECOND-GENERATION ETHANOL PRODUCTION by Wickerhamomyces Anomalus Hydrolysates (Da Cunha-Pereira Et Al
An Acad Bras Cienc (2020) 92(Suppl. 2): e20181030 DOI 10.1590/0001-3765202020181030 Anais da Academia Brasileira de Ciências | Annals of the Brazilian Academy of Sciences Printed ISSN 0001-3765 I Online ISSN 1678-2690 www.scielo.br/aabc | www.fb.com/aabcjournal BIOLOGICAL SCIENCES Second-generation ethanol production Running title: SECOND- by Wickerhamomyces anomalus strain GENERATION ETHANOL adapted to furfural, 5-hydroxymethylfurfural PRODUCTION BY Wickerhamomyces anomalus (HMF), and high osmotic pressure Academy Section: BIOLOGICAL NICOLE T. SEHNEM, ÂNGELA S. MACHADO, CARLA R. MATTE, SCIENCES MARCOS ANTONIO DE MORAIS JR & MARCO ANTÔNIO Z. AYUB Abstract: The aims of this work were to improve cell tolerance towards high e20181030 concentrations of furfural and 5-hydroxymethylfurfural (HMF) of an osmotolerant strain of Wickerhamomyces anomalus by means of evolutionary engineering, and to determine its ethanol production under stress conditions. Cells were grown in the presence of 92 furfural, HMF, either isolated or in combination, and under high osmotic pressure (Suppl. 2) conditions. The most toxic condition for the parental strain was the combination of 92(Suppl. 2) both furans, under which it was unable to grow and to produce ethanol. However, the tolerant adapted strain achieved a yield of ethanol of 0.43 g g-1glucose in the presence of furfural and HMF, showing an alcohol dehydrogenase activity of 0.68 mU mg protein-1. For this strain, osmotic pressure, did not affect its growth rate. These results suggest that W. anomalus WA-HF5.5strain shows potential to be used in second-generation ethanol production systems. Key words: Second-generation ethanol, Wickerhamomyces anomalus, furaldehydes tol- erance, osmotic pressure, lignocellulosic hydrolysates.