The Use of Glass to Optimize Bitumen Absorption of Hot Mix Asphalt Containing Recycled Construction Aggregates
Total Page:16
File Type:pdf, Size:1020Kb
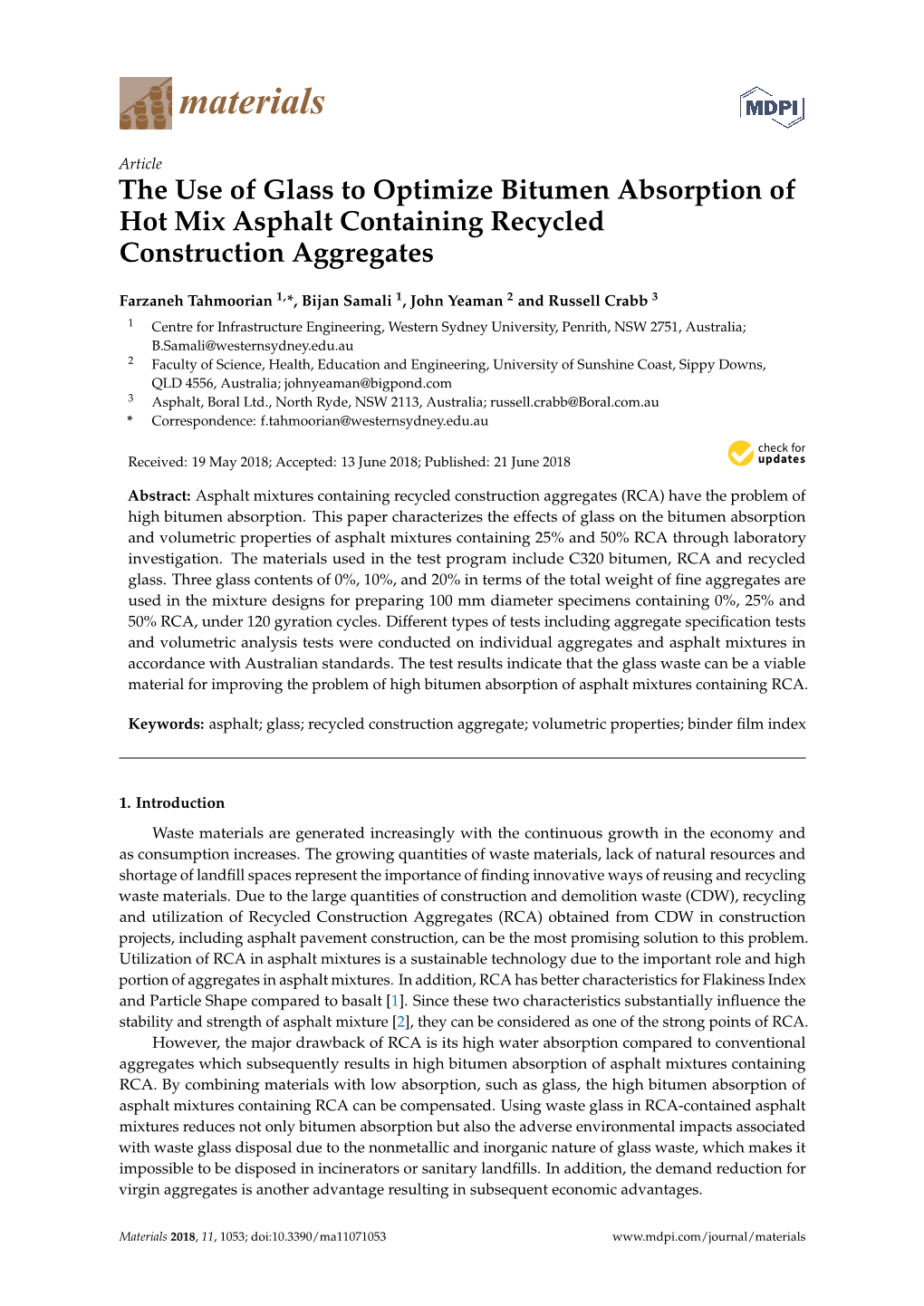
Load more
Recommended publications
-
Roads and Parking Lots Pavement Condition Index Surveys1
Designation: D 6433 – 07 Standard Practice for Roads and Parking Lots Pavement Condition Index Surveys1 This standard is issued under the fixed designation D 6433; the number immediately following the designation indicates the year of original adoption or, in the case of revision, the year of last revision. A number in parentheses indicates the year of last reapproval. A superscript epsilon (e) indicates an editorial change since the last revision or reapproval. 1. Scope 2.1.3 pavement branch—a branch is an identifiable part of 1.1 This practice covers the determination of roads and the pavement network that is a single entity and has a distinct parking lots pavement condition through visual surveys using function. For example, each roadway or parking area is a the Pavement Condition Index (PCI) method of quantifying separate branch. pavement condition. 2.1.4 pavement condition index (PCI)—a numerical rating 1.2 The PCI for roads and parking lots was developed by the of the pavement condition that ranges from 0 to 100 with 0 U.S. Army Corps of Engineers (1, 2).2 It is further verified and being the worst possible condition and 100 being the best adopted by DOD and APWA. possible condition. 1.3 The values stated in inch-pound units are to be regarded 2.1.5 pavement condition rating—a verbal description of as the standard. The SI units given in parentheses are for pavement condition as a function of the PCI value that varies information only. from “failed” to “excellent” as shown in Fig. 1. -
Traffic Paint Tests
60 Traffic Paint Tests W. G. VANNOY, Pigments Department, E. I. du Pont de Nemours and Company, Newport, Delaware SYNOPSIS TRAFFIC-paint-testing procedures are reviewed in an attempt to determine which tests might be considered as standard. Although there is no official set of standard tests for traffic paints, those in use by a large percentage of consumers and those established by ASTM are considered as standard. Certain laboratory control tests together with small scale road tests are given as the most effective means available at the present time for evaluating candidate traffic paints. Laboratory tests as used to predict traffic paint durability are considered unreliable without further testing details and clarification. Current ASTM efforts to establish accelerated laboratory traffic-paint tests for dur• ability and suspension are reviewed. The need for such accelerated tests is emphasized in order to permit performance rather than compositional specifications. • SUITABLE testsfor traffic paint com• Although there is no official set of stand• positions are problems of major impor• ard tests for traffic paint, the tests in tance. These problems are faced by use by a large percentage of consumers every state highway department in writing might be considered as standard. Fur• reliable traffic paint specifications. Fur• ther, certain standards and standard ther, the manufacturers, as well as the methods of test have been established by consumers, are faced with these same the American Society for Testing Mate• problems because various compositions rials and insofar as possible such gen• must be evaluated and the more promis• erally accepted and established testing ing candidates selected. -
Massachusetts Driver's Manual
$5.00 COMMONWEALTH OF MASSACHUSETTS DRIVER’S MANUAL MASSACHUSETTS OF DRIVER’S COMMONWEALTH Commonwealth of Massachusetts DRIVER’S MANUAL PASSENGER VEHICLES Revised 2/2018 REVISED 2/2018 The policies in this Driver’s Manual include changes that take effect on March 26, 2018. All other information you need to study for a learner’s permit exam and road test (such as safety laws and rules of the road) is current both before and after March 26, 2018. A Message to Massachusetts Motorists from Erin C. Deveney, Registrar of Motor Vehicles Dear Motorist, The MassDOT Registry of Motor Vehicles recognizes that the work we perform impacts you and nearly every person in the Commonwealth of Massachusetts. We give our customers the joy of getting their first license. We register vehicles that take people all over the state for work, school, to access medical care and for exciting and important events in their lives. We also have the very serious responsibility of making sure all drivers, as well as the vehicles on our roadways, are safe and fit to operate. The RMV is committed to providing you with efficient, reliable and professional customer service. The Driver’s Manual prepares you for your driving career and also for doing business with the Registry. It includes requirements for transactions we provide, as well as service options and RMV Service Center location information. To serve you better, we offer 28 transactions and services via our website, www.mass.gov/rmv. Online services bring the RMV to you. We have expanded the number of AAA locations offering Registry renewal services through an innovative public-private partnership. -
Appendix B-Distress
144 APPENDIX B DISTRESSES 145 INTRODUCTION The purpose of this appendix is not to provide a detailed discussion of the various descriptions and causes of distresses that may occur in any given pavement structure. The purpose of this appendix is only to provide a brief presentation. Numerous other manuals and publications already exist that provide information that is much more detailed. The state DOT Agency’s Pavement Designer group should review these manuals and publications. This will assist them in understanding the causes of distresses in pavements. This knowledge can then be used to effectively select a preferred pre-overlay treatment strategy for use on a specific project. The information, figures, and pictures provided in this chapter, unless otherwise noted, were obtained from the FHWA’s Distress Identification Manual for the Long-Term Pavement Performance Program. These descriptions are provided as a guide only and should not be viewed as the only guidance available for distress type-severity description or identification. Since the publication of this Distress Identification Manual, additional distress-type-severity descriptions or identifications for frost heave, roughness, and alkali–silica reaction (ASR) have been added to this synthesis. Other distresses may exist, but will not be made a part of this synthesis. HOT-MIX ASPHALT (HMA) PAVEMENT DISTRESSES This section contains the general descriptions of the major types of distress that may be encountered in flexible pavements. A typical description of three severity levels associated with each distress is provided. Fatigue Cracking This distress occurs in areas subjected to repeated traffic loadings, usually in the wheel path. -
2012 Asphalt Pavement Survey Manual
NORTH CAROLINA DEPARTMENT OF TRANSPORTATION PAVEMENT CONDITION SURVEY MANUAL 2012 2012 NCDOT Pavement Condition Survey TABLE OF CONTENTS Introduction ................................................................................................................................................................. 1 A. Getting Started ....................................................................................................................................................... 1 B. Conducting the Survey – General Guidelines ...................................................................................................... 2 C. The Form ................................................................................................................................................................ 3 D. Notes on Mileposting ............................................................................................................................................. 7 E. Instructions for Multi-Lane Sections ................................................................................................................... 9 F. Instructions for Urban Areas .............................................................................................................................. 12 G. Pavement Section Adjustment ............................................................................................................................ 12 H. Updating Section Information ........................................................................................................................... -
Tech Topic Flexible Pavement Distresses
Tech Topic Flexible Pavement Distresses Flexible pavements can suffer from several categories and subcategories of distresses that will lead to progressive deterioration of ride condition, structural strength, and motorist/pedestrian safety. The more common distresses found in the Delaware area are introduced herein. Bleeding Description: A film of asphalt binder on the pavement surface, such that the surface will appear shiny and/or have black spots or blotchy areas. Causes: Bleeding occurs when asphalt binder fills the aggregate voids during hot weather, then expands onto the pavement surface. Since bleeding is not reversible during cold weather, asphalt binder will accumulate on the pavement surface over time. This can be caused by an excess amount of asphalt binder in the flexible pavement mixture and/or low air void content. Bleeding typically originates from poor hot mix production or transportation (i.e., segregation of aggregate and binder). Leads to: Bleeding reduces the friction characteristics of the road surface. As the skid resistance of the roadway decrease, the likelihood of crashes increases. Typical Repair Methods: When bleeding is minor, coarse sand can be applied to the pavement in order to absorb the excess asphalt binder. When much of the pavement surface is affected by bleeding, the surface may need to be removed (i.e., milled) and the surface wearing course replaced. Patching Description: Patches are localized areas of surface asphalt replacement related to utility work or repair of distressed areas. Causes: Patches commonly are a reaction to localized pavement deterioration (potholes, alligator cracking, etc.) and are intended to be a short to medium term repair. -
Pavement Distress Detection Methods: a Review
infrastructures Review Pavement Distress Detection Methods: A Review Antonella Ragnoli 1,* , Maria Rosaria De Blasiis 2 and Alessandro Di Benedetto 2 1 Department of Civil, Constructional and Environmental Engineering, Sapienza University of Rome, 00184 Rome, Italy 2 Department of Engineering, Roma Tre University, 00154 Rome, Italy; [email protected] (M.R.D.B.); [email protected] (A.D.B.) * Correspondence: [email protected]; Tel.: +39-0644-585-115 Received: 28 September 2018; Accepted: 17 December 2018; Published: 19 December 2018 Abstract: The road pavement conditions affect safety and comfort, traffic and travel times, vehicles operating cost, and emission levels. In order to optimize the road pavement management and guarantee satisfactory mobility conditions for all road users, the Pavement Management System (PMS) is an effective tool for the road manager. An effective PMS requires the availability of pavement distress data, the possibility of data maintenance and updating, in order to evaluate the best maintenance program. In the last decade, many researches have been focused on pavement distress detection, using a huge variety of technological solutions for both data collection and information extraction and qualification. This paper presents a literature review of data collection systems and processing approach aimed at the pavement condition evaluation. Both commercial solutions and research approaches have been included. The main goal is to draw a framework of the actual existing solutions, considering them from a different point of view in order to identify the most suitable for further research and technical improvement, while also considering the automated and semi-automated emerging technologies. An important attempt is to evaluate the aptness of the data collection and extraction to the type of distress, considering the distress detection, classification, and quantification phases of the procedure. -
PTD 2019 001 | RMS.19.1436 – Treatments for Bleeding Seals
Technical Direction Pavements PTD 2019/001 | RMS 19.1436 – 01 November 2019 Treatments for bleeding seals Summary: Audience: The purpose of this Technical Direction is to provide guidelines on • District Works Managers how to treat bleeding sprayed seals that are not attributed by • Asset Managers pavement structural defects. • Maintenance Planners • Councils Introduction Sprayed seal is the predominant and most cost effective pavement surfacing type in New South Wales covering over 70% of the road network. Sprayed sealing offers a number of benefits including waterproofing pavement layers, increasing skid resistance, retarding cracking and minimising rate of pavement deterioration. However, inadequate selection and design of sprayed seals, inadequate site preparation and poor construction practices can cause a number of surface defects including bleeding. Bleeding can reduce skid resistance and can cause long term distress to the seal particularly on a hot day. This Technical Direction provides guidance on the selection of appropriate treatments for bleeding sprayed seal surfaces. Definition of bleeding seal ‘Bleeding’ is a surface defect in which excess binder completely covers the aggregate (see Figure 1). It occurs when excess binder fills the voids in the aggregate mat and moves to the pavement surface due to a combination of repeated wheel loading, with heat expansion in a non-reversible cumulative process. Approvals: Sam Henwood Owner: Review Date: November 2022 Director Pavements & Geotechnical Chris Harrison Authorised by: Effective Date: November 2019 Director of Engineering PTD 2019/001 | RMS 19.1436 – 01 November 2019 1 Version 1.0 UNCONTROLLED WHEN PRINTED Treatments for bleeding seals Figure 1: View of a bleeding sprayed seal Factors that contribute to bleeding seals Factors that contribute to bleeding seals include issues pertaining to: • Aggregates (e.g. -
Correction of Bleeding (Flus'hing) Surfaces Research Report 214-28 June 1981
E 61 EERI 6 ECO 0 Y A 0 E ER6Y CO SIDERAIIOS CORRECTION OF BLEEDING (FLUS'HING) SURFACES RESEARCH REPORT 214-28 JUNE 1981 ...•. _-- . COOPERATIVE RESEARCH PROJECT 2-9-74-214 "ENGINEERING, ECONOMY AND ENERGY CONSIDERATIONS IN DESIGN, CONSTRUCTION AND MATERIALS II TEXAS STATE DEPARTMENT OF HIGHWAYS AND PUBLIC TRANSPORTATION AND TEXAS TRANSPORTATION INSTITUTE TEXAS A&M UNIVERSITY STATE DEPARTMENT OF HIGHWAYS AND PUBLIC TRANSPORTATION TASK FORCE ON ENGINEERING, ECONOMY AND ENERGY CONSIDERATIONS Larry G. Walker, Task Force Chairman and Materials and Tests Engineer Charles H. Hughes, Sr., Study Contact Representative and Assistant Materials and Tests Engineer A.H. Pearson, Jr., Assistant State Engineer-Director Wayne Henneberger, Bridge Engineer Robert L. Lewis, Chief Engineer, Highway Design Byron C. Blaschke, Chief Engineer, Maintenance Operations J.R. Stone, District Engineer William V. Warg, Urban Project Engineer-Manager Phillip L. Wilson, State Planning Engineer Franklin C. Young, District Engineer Theodore E. Ziller, Construction Engineer CORRECTION OF BLEEDING (FLUSHING) SURFACES by F. N. FINN AND J. A. EPPS Research Report 214-28 June 1981 TEXAS TRANSPORTATION INSTITUTE The Texas A&M University System College Station, Texas I ~ TABLE OF CONTENTS Page Introduction . 1 Occurrence and Consequences of Bleeding 2 Asphalt Concrete ... 2 Seal Coats and Surface Treatments 3 Consequences of Bleeding . 4 Corrective Procedures for Bleeding Surfaces 6 Burning 6 Sanding 7 Heater-Planer without Aggregate 7 Sprinkle with Aggregate 8 Seal Coat . 8 Thin Hot Mix Asphalt Concrete Overlay. 9 Heater Scarification Without New Material 10 Open Graded As pha It Concrete . 11 Cold Milling With or Without New Material 11 Summary . -
Gravel Road Maintenance
36 PURDUE ENGINEERING EXTENSION SERVICE useless. In spite of the fact that we were almost unanimous that the things should be done, difficulties arose when the type of pavement was to be determined. To date, we have plans for concrete, Kentucky rock asphalt on concrete, Kentucky rock asphalt on macadam, sheet asphalt on concrete, and sheet asphalt on macadam. We have received assistance from the Engineering Exten sion Service of Purdue University and the State Highway Com mission and present indications are that our plans will be car ried out successfully in the near future. TABLE I.— HUNTINGTON COUNTY ROAD DATA DEC. 31, 1922. Total Town Road County State ship Township Tax *(1) *(2) *(3) *(4) Road Road Road Bonds Debt Valuation Levy Mileage Mileage Mileage Jackson .832 (.03-.132-.12-.55) 26.71 7 35.88 $174,109.80 $103,728.64 $4,174,920.00 Clear Creek .302 (.03-.132-.17-.07) 44.54 26 76,471.70 8,025.36 3,621,870.00 Warren .482 (.03-.132-.05-.27) 40.24 14 111,556.00 27,550.00 2,958,290.00 Dallas .642 (.03-.132-.10-.38) 23.68 5 15 123,220.00 54,026.96 2,822,290.00 Huntington .262 (.03-.132-.10 ) 40.03 7.75 21 121,576.00 5,754.00 24,475,610.00 Union .382 (.03-.132-.13-.09) 40.84 2.5 24 68,125.00 15,505.50 4,463,400.00 Rock Creek .802 (.03-.1S2-.15-.49) 44.44 26.5 133,737.00 64,188.50 3,733,430.00 Lancaster .622 1(.03-.132-.16-.30) 45.02 4.75 16.5 75,910.00 53,663.90 3,119,110.00 Polk .672 (.03-.132-.16-.35) 27.16 1.75 17 56,903.40 21,980.90 1,621,410.00 Wayne .532 (.03-. -
Chip Seal Best Practices Manual
NORTH CAROLINA DEPARTMENT OF TRANSPORTATION Chip Seal Best Practices Manual June 2015 Prepared By: SEPI Engineering & Construction, Inc. NCDOT CHIP SEAL BEST PRACTICES MANUAL TABLE OF CONTENTS Chapter 1. The “Art of Road Oil” ................................................................................................. 1 2. The Existing Roadway ............................................................................................... 3 3. Tools of the Trade ..................................................................................................... 6 Emulsion Distributor ..................................................................................................... 6 Stone Spreader ............................................................................................................ 7 Dump Truck ................................................................................................................ 8 Pneumatic Roller .......................................................................................................... 9 Static Steel Wheel Roller ............................................................................................... 9 Combination Roller ...................................................................................................... 10 Mechanical Broom ....................................................................................................... 11 Vacuum Truck ............................................................................................................ -
R27-174: Methodology for Evaluation of Seal-Coated, Gravel, and Dirt Roads
CIVIL ENGINEERING STUDIES Illinois Center for Transportation Series No. 19-009 UILU-ENG-2019-2009 ISSN: 0197-9191 METHODOLOGY FOR EVALUATION OF SEAL-COATED, GRAVEL, AND DIRT ROADS Prepared By Mohammad Imran Hossain Bradley University Erol Tutumluer University of Illinois at Urbana-Champaign Research Report No. FHWA-ICT-19-008 A report of the findings of ICT PROJECT R27-174 Methodology for Evaluation of Seal-Coated, Gravel, and Dirt Roads https://doi.org/10.36501/0197-9191/19-009 Illinois Center for Transportation June 2019 TECHNICAL REPORT DOCUMENTATION PAGE 1. Report No. 2. Government Accession No. 3. Recipient’s Catalog No. FHWA-ICT-19-008 N/A N/A 4. Title and Subtitle 5. Report Date Methodology for Evaluation of Seal-Coated, Gravel, and Dirt Roads June 2019 6. Performing Organization Code N/A 7. Authors 8. Performing Organization Report No. Mohammad I. Hossain and Erol Tutumluer ICT-19-009 UILU-ENG-2019-2009 9. Performing Organization Name and Address 10. Work Unit No. Illinois Center for Transportation N/A Department of Civil and Environmental Engineering 11. Contract or Grant No. University of Illinois at Urbana–Champaign R27-174 205 North Mathews Avenue, MC-250 Urbana, IL 61801 12. Sponsoring Agency Name and Address 13. Type of Report and Period Covered Illinois Department of Transportation (SPR) Final Report Bureau of Research 1/1/2016 – 6/30/2019 126 East Ash Street 14. Sponsoring Agency Code Springfield, IL 62704 15. Supplementary Notes Conducted in cooperation with the U.S. Department of Transportation, Federal Highway Administration. https://doi.org/10.36501/0197-9191/19-009 16.