Vol.3, No.2 2014
Total Page:16
File Type:pdf, Size:1020Kb
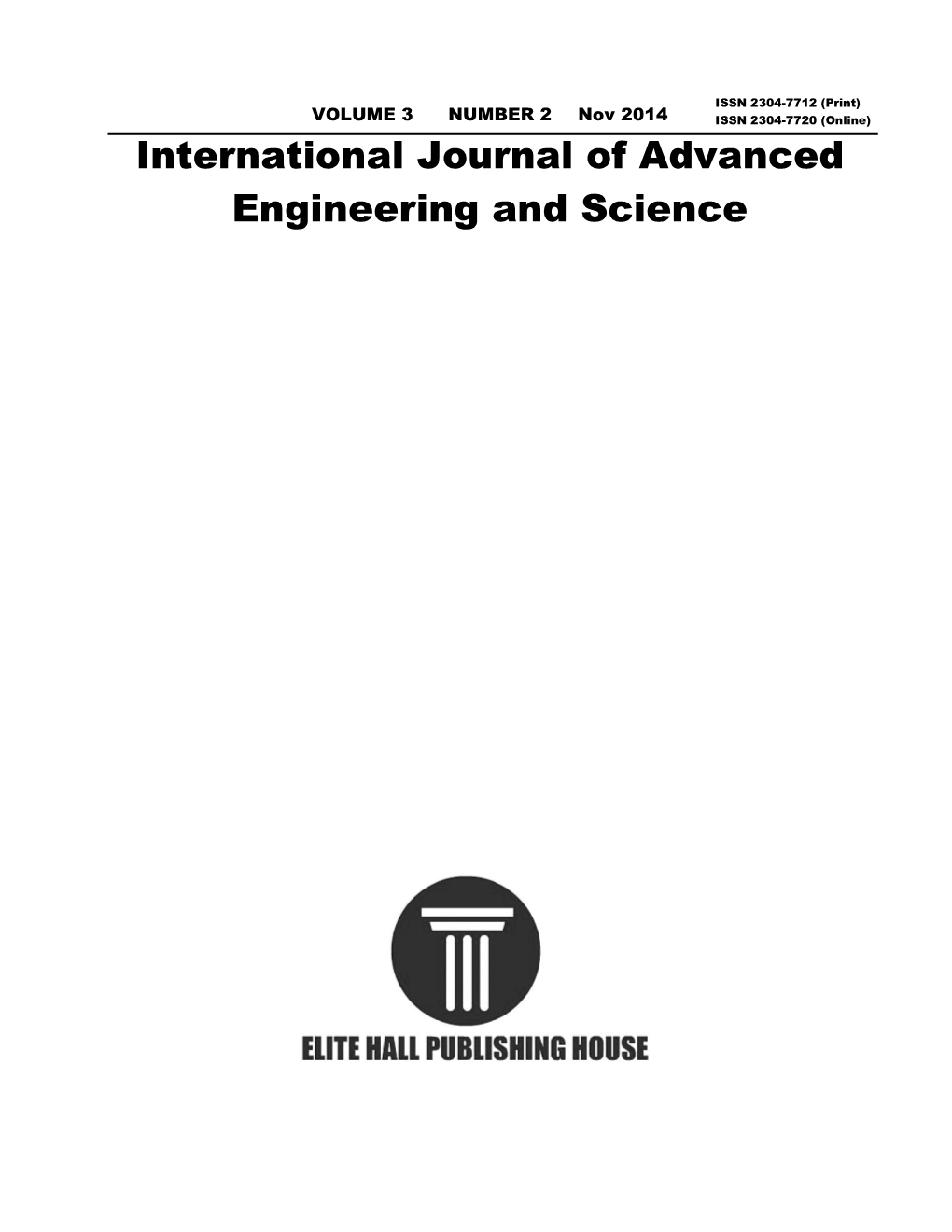
Load more
Recommended publications
-
Draft 1 the Evolution of Specialty Geotechnical
draft THE EVOLUTION OF SPECIALTY GEOTECHNICAL CONSTRUCTION TECHNIQUES: THE “GREAT LEAP” THEORY “The mind is not a vessel to be filled, but a fire to be ignited.” (Plutarch c 120 AD) 1. DEVELOPMENT OF THE BASIC THESIS Between 1858 and 1865, the great Scottish historian Thomas Carlyle wrote a 6-volume opus on the life and times of King Frederick the Great of Prussia. This work had followed his 1841 masterpiece “On Heroes, Hero-Worship and the Heroic in History.” In these publications, Carlyle developed what we now call the “Great Man” theory of history. This states that “the history of the world is but a biography of great men.” He evaluated the hero as divinity (in the form of pagan myths), as prophet (Mohammed), as poet (Dante, Shakespeare), as pastor (Martin Luther, John Knox), as man of letters (Samuel Johnson, Robbie Burns), and as king (Oliver Cromwell, Napoleon Bonaparte, paradoxically, kings in all but name). With time, at a different time, Carlyle could have doubtless explored the hero as a warrior (Admiral Lord Nelson, General Stonewall Jackson, General George Patton) or the hero as a musician (as David Bowie wanted to be in his 1977 masterpiece) or as patriot, like that other Bowie of Scottish origins, Jim, who died fighting for the freedom of Texas at the Alamo in 1836. All of us here today are engaged in some aspect of the broad field of geotechnical engineering – a discipline barely embryonic in Carlyle’s day, and bound primarily to the demands of military engineering. We can be convinced that the “Great Man” theory is equally valid when considering the more fundamental and theoretical branches of our discipline, such as rock and soil mechanics. -
Application for 7Th Lizzi Scholarship 13Th International Society for Micropiles Vancouver, Bc, Canada March 29-April 1, 2017
APPLICATION FOR 7TH LIZZI SCHOLARSHIP 13TH INTERNATIONAL SOCIETY FOR MICROPILES VANCOUVER, BC, CANADA MARCH 29-APRIL 1, 2017 The International Society for Micropiles (ISM) invites applications for the 7th Lizzi Scholarship from graduate students studying in the field of micropiles. Applicants must reside in British Columbia or Washington State, be enrolled in graduate studies, and be either proposing to conduct or currently conducting research on micropiles. The scholarship award will consist of financial reimbursement of travel and accommodations expenses for attendance at the 13th International Workshop on Micropiles in Vancouver, BC, Canada from March 29-April 1, 2017, waiver of registration fees for the workshop, and a selection of micropile publications. Application and Award Requirements Please submit your application using the attached form to Nick Salisbury, Crux Subsurface, Inc., Host Sponsor and Organizing Committee Chair at [email protected]. The scholarship recipient will be selected by the ISM organizing committee. The scholarship recipient will be required to make a brief presentation outlining his/her proposed or current micropile research at the 2017 workshop. About Dr. Fernando Lizzi Fernando Lizzi was born in 1914 in Castelnuovo di Porto, Italy near Rome. At age 18, he entered the artillery military academy in Torino and became an officer in the Italian Army. At the end of his academy training in 1936, he was posted to Tripoli, Libya, where he fought and was injured in 1942 in the battle of Djrababub. He was then captured by the British army and eventually sent to a prisoner-of-war camp in an area now near the border between Pakistan and Afghanistan. -
(Root Pile, Micro Pile) Technology for Preservation of Historical Islamic Monuments in Cairo Egypt
SAYED HEMEDA Pali radice (Root pile, Micro pile) Technology for Preservation of Historical Islamic Monuments in Cairo Egypt. 2 Paliradice (Root pile, Micro pile) Technology for Preservation of Historical Islamic Monuments in Cairo Egypt. Sayed Hemeda Published by Mistral Service sas Via U. Bonino, 3, 98100 Messina (Italy) This book is distributed as an Open Access work. All users can download copy and use the present volume as long as the author and the publisher are properly cited. The content of this manuscript has been revised by our international Editorial Board members. Important Notice The publisher does not assume any responsibility for any damage or injury to property or persons arising out of the use of any materials, instructions, methods or ideas contained in this book. Opinions and statements expressed in this book are these of the authors and not those of the publisher. Furthermore, the published does not take any responsibility for the accuracy of information contained in the present volume. First published: January 2015 Pali radice (Root pile, Micro pile) Technology for Preservation of Historical Islamic Monuments in Cairo Egypt. S. Hemeda ISBN: 978-88-98161-32-4 3 Table of content Abstract 4 1- Introduction 5 2- Types of ancient foundations 7 3- Failure Modes for Shallow Foundations 9 4- Aspects of structural strengthening of architectural 15 heritage in Egypt 5- Application of micropiles in preservation of historical 16 buildings. 6- Capacity of piles from soil parameters 23 7- The mosque of Al-ZaherBaybars in cairo, Egypt. (Case 25 study). 8- Micropiles limitations 39 9- Concluding remarks 39 10- References 41 4 Abstract The 1992 Dahshour earthquake offered a unique opportunity to verify the knowledge on retrofitting strategies of historic masonry structures which have been developed during the last twenty years. -
International Society for Soil Mechanics and Geotechnical Engineering
INTERNATIONAL SOCIETY FOR SOIL MECHANICS AND GEOTECHNICAL ENGINEERING This paper was downloaded from the Online Library of the International Society for Soil Mechanics and Geotechnical Engineering (ISSMGE). The library is available here: https://www.issmge.org/publications/online-library This is an open-access database that archives thousands of papers published under the Auspices of the ISSMGE and maintained by the Innovation and Development Committee of ISSMGE. Organization of the conference Organisation du congrès Conférence Advisory Committee/ Comité consultatif du congrès Prof. Drh.c. M.B.Jamiolkowski, Chairman/ Président Prof. Dr Ir W. F. Van Impe Prof. S.Gulhati Prof. Dr-Ing. W.Wittke Prof. Dr-Ing. E.h. M. NuBbaumer DrR.H.G.Parry Conference Advisory Board/ Organising Committee Bureau consultatif du congrès/ Comité d'organisation Prof. Dr-Ing. W.Wittke, Chairman/ Président Dr-Ing. H.PDücker Prof. Dr-Ing. R. Floss Dipl.-Ing. K.D.Eschenburg Prof. Dr-Ing. Dr h.c. G.Gudehus Prof. Dr-Ing. Dr rer.pol. E. Heitkamp Prof. Dr Ir W. E Van Impe Prof. Drh.c. M.B.Jamiolkowski Dr-Ing. W. Leichnitz Dipl.-Ing. K.Lohrberg Prof. Dr R. Morgenstern Prof. Dr-Ing. E.h. M. Nußbaumer DrR. H.G.Parry Prof. H.G.Poulos Dipl.-Ing. D.Rappert Dr-Ing. J. Rappert Prof. Dr-Ing. W. Rodatz Dr-Ing. O. Franz Prof. Dipl.-Ing. D. Schröder Prof. Dr-Ing. Dr-Ing.E.h. U.Smoltczyk Dipl.-Ing. R.Thiel XVII Conference program Programme du congrès Time Table of the Scientific Conference Programme Time Monday Tuesday Time Monday, September 8, 1997 8.9.97 9.9.97 09.30 - 11.30 h Opening Ceremony 8.00 8.00 Hall 2 8.30 8.30 ■ Musical opening of the ceremony performed by the 9.00 9.00 "Finkwarder Speeldeel", a renowned north German 9.30 Plenary Session 3 9.30 folkloristic group, acting at the same time as em Hall 2 10.00 10.00 bassadors for the city of Hamburg.