Effect of Stress Concentrations on Fatigue of Composite and Metallic Structures
Total Page:16
File Type:pdf, Size:1020Kb
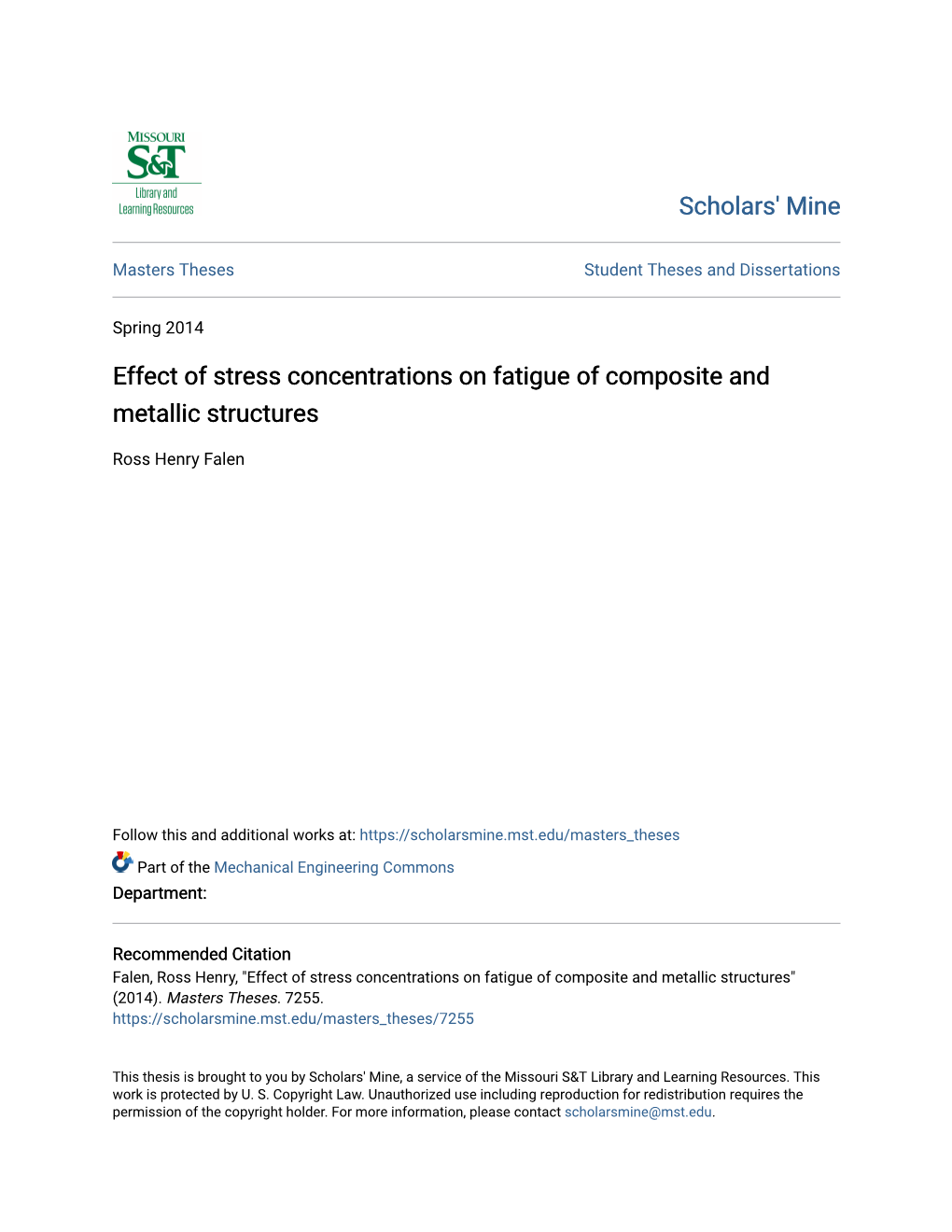
Load more
Recommended publications
-
Visual Examination and Light Microscopy
ASM Handbook, Volume 12: Fractography Copyright © 1987 ASM International® ASM Handbook Committee, p 91-165 All rights reserved. DOI: 10.1361/asmhba0001834 www.asminternational.org Visual Examination and Light Microscopy George F. Vander Voort, Carpenter Technology Corporation THE VISUAL EXAMINATION of fractures by light microscopy. Interesting features can be sections, to determine the origin of the failure, is deeply rooted in the history of metals pro- marked with a scribe, microhardness indents, and to separate the fractures according to the duction and usage, as discussed in the article or a felt-tip pen and then examined by SEM time sequence of failure, that is, which frac- "History of Fractography" in this Volume. and other procedures, such as energy- tures existed before the event versus which ones This important subject, referred to as macro- dispersive x-ray analysis, as required. occurred during the event. This article will fractography, or the examination of fracture The techniques and procedures for the visual assume that such work has already been accom- surfaces with the unaided human eye or at low and light microscopic examination of fracture plished and will concentrate on fracture exam- magnifications (--<50), is the cornerstone of surfaces will be described and illustrated in this ination and interpretation. Other related topics failure analysis. In addition, a number of qual- article. Results will also be compared and specific to failure analyses are discussed in ity control procedures rely on visual fracture contrasted with those produced by electron Volume 11 of the 9th Edition of Metals Hand- examinations. For failure analysis, visual in- metallographic methods, primarily SEM. -
Estimating the Fatigue Stress Concentration Factor of Machined Surfaces D
International Journal of Fatigue 24 (2002) 923–930 www.elsevier.com/locate/ijfatigue Estimating the fatigue stress concentration factor of machined surfaces D. Arola *, C.L. Williams 1 Department of Mechanical Engineering, University of Maryland Baltimore County, 1000 Hilltop Circle, Baltimore, MD 21250, USA Received 18 December 2000; received in revised form 12 September 2001; accepted 19 December 2001 Abstract In this study the effects of surface texture on the fatigue life of a high-strength low-alloy steel were evaluated in terms of the apparent fatigue stress concentration. An abrasive waterjet was used to machine uniaxial dogbone fatigue specimens with specific surface quality from a rolled sheet of AISI 4130 CR steel. The surface texture resulting from machining was characterized using contact profilometry and the surface roughness parameters were used in estimating effective stress concentration factors using the Neuber rule and Arola–Ramulu model. The steel specimens were subjected to tension–tension axial fatigue to failure and changes 3Յ Յ 6 in the fatigue strength resulting from the surface texture were assessed throughout the stress–life regime (10 Nf 10 cycles). It was found that the fatigue life of AISI 4130 is surface-texture-dependent and that the fatigue strength decreased with an increase in surface roughness. The fatigue stress concentration factor (Kf) of the machined surfaces determined from experiments was found to range from 1.01 to 1.08. Predictions for the effective fatigue stress concentration (K¯ f) using the Arola–Ramulu model were within 2% of the apparent fatigue stress concentration factors estimated from experimental results. 2002 Published by Elsevier Science Ltd. -
Improved Fatigue Test Specimens with Minimum Stress Concentration Effects1
IMPROVED FATIGUE TEST SPECIMENS WITH MINIMUM STRESS CONCENTRATION EFFECTS1 Daniel de Albuquerque Simões2 Jaime Tupiassú Pinho de Castro3 Marco Antonio Meggiolaro3 Abstract The American Standard for Testing and Materials (ASTM) has standardized numerous mechanical tests such as the constant amplitude axial fatigue test of metallic materials (E 466–96), the strain-controlled fatigue testing (E 606–92) and the strain-controlled axial-torsional fatigue testing with thin-walled tubular specimens (E 2207–02). The specimens for such tests must have notches to connect their uniform test section to the larger heads required to grip them. The usual practice is to specify notches with as large as possible constant radius roots, since they can be easily fabricated in traditional machine tools. However, notches with properly specified variable radius may have much lower stress concentration factors than those obtainable by fixed notch root radii. The objective of this study is to analyze the stress distribution in these specimens using the finite element method and to quantify the stress concentration improvements achievable by optimizing variable radius notches for typical push-pull, rotary bending and alternate bending fatigue test specimens by redesigning the specimen geometry without changing their overall dimensions. Key words: Stress concentration factor; Shape optimization; Finite element methods. CORPOS DE PROVA DE FADIGA COM CONCENTRAÇÃO DE TENSÃO REDUZIDA Resumo A ASTM (The American Standard for Testing and Materials) padronizou inúmeros testes mecânicos, como por exemplo, o teste de fadiga de amplitude constante para materiais metálicos (E466–96), o teste de fadiga com deformação controlada (E 606–92) e o teste de fadiga de torção axial de corpos de prova tubulares (E 2207–02). -
Characterization of Biomaterials
Chapter 3 Mechanical Characterization of Biomaterials Ryan K. Roeder Department of Aerospace and Mechanical Engineering, Bioengineering Graduate Program, University of Notre Dame, Notre Dame, IN, USA Chapter Outline 3.1. Introduction 50 3.4. Application and 3.2. Fundamental Concepts 51 Measurement of Load 3.2.1. Stress and Strain and Deformation 64 versus Force and 3.4.1. Equipment 64 Displacement 51 3.4.2. Modes of Loading 67 3.2.2. Mechanical 3.4.3. Strain Rate and Time- Properties on Dependent Behavior 71 a StresseStrain Curve 52 3.4.4. Frequency and Time- 3.2.3. Material Classes 55 Dependent Behavior 78 3.2.4. Types of StresseStrain 3.4.5. Nondestructive Tests 83 Curves and 3.5. Environment 91 Constitutive Models 56 3.5.1. Temperature and 3.2.5. Anisotropy 58 Pressure 91 3.2.6. Fracture Mechanics 58 3.5.2. Aqueous Media 92 3.3. Specimens 62 3.5.3. Irradiation 94 3.3.1. Specimen Size and 3.6. Data Acquisition and Geometry 62 Analysis 95 3.3.2. Specimen Acknowledgments 96 Preparation 63 References 97 Characterization of Biomaterials. http://dx.doi.org/10.1016/B978-0-12-415800-9.00003-6 Copyright Ó 2013 Elsevier Inc. All rights reserved. 49 50 Characterization of Biomaterials 3.1. INTRODUCTION Mechanical behavior is crucial to the performance of biomaterials used in most biomedical implants and devices. In many cases, the importance is obvious and the connection direct. The femoral stem of a total hip replacement must bear static and cyclic loads imposed by body weight and muscle forces without failure for the lifetime of the implant. -
Cranfield University
Cranfield University Andrea Cini Scribe marks at fuselage joints: initiation and propagation of fatigue cracks from mechanical defects in aluminium alloys School of Applied Sciences PhD Cranfield University School of Applied Sciences Department of Materials - Damage Tolerance Group PhD thesis Academic Year 2011-2012 Andrea Cini Scribe marks at fuselage joints: initiation and propagation of fatigue cracks from mechanical defects in aluminium alloys Supervisor: Professor Philip E. Irving August 2012 This thesis is submitted in partial fulfilment of the requirements for the degree of Doctor of Philosophy © Cranfield University 2012. All rights reserved. No part of this publication may be reproduced without the written permission of the copyright owner. Abstract Mechanical damages, like scratches, are commonly detected on the surfaces of aircraft components and structures. They can be accidentally introduced during machining or maintenance operations or be the result of wear and impacts during aircraft service. Under the action of service loads, such mechanical damage can generate fatigue cracks reducing the component fatigue life and compromising the aircraft structural integrity. The evaluation of the effect of scratches and other small mechanical defects on the structure and component fatigue lives is therefore necessary to define an inspections programme and ensure the structural safety. Conventional fatigue life prediction methods generally consider scratches tents of microns deep too shallow to appreciably affect the fatigue performances of structural components. However the discovery of the scribe marks on fuselage joints disproved that prediction. In fact several commercial airlines discovered during inspections that aircraft which have been repainted showed multiple scratches on the fuselage skin along longitudinal and circumferential joints. -
Fatigue Life for Different Stress Concentration Factors for Stainless
materials Article Fatigue Life for Different Stress Concentration Factors for Stainless Steel 1.4301 Przemysław Strzelecki 1,* , Adam Mazurkiewicz 1, Janusz Musiał 1, Tomasz Tomaszewski 1 and Małgorzata Słomion 2 1 Mechanical Engineering Department, University of Science and Technology, Kaliskiego 7 Street, 85-789 Bydgoszcz, Poland; [email protected] (A.M.); [email protected] (J.M.); [email protected] (T.T.) 2 Faculty of Management, University of Science and Technology, Kaliskiego 7 Street, 85-789 Bydgoszcz, Poland; [email protected] * Correspondence: [email protected]; Tel.: +48-52-340-86-72 Received: 26 September 2019; Accepted: 5 November 2019; Published: 8 November 2019 Abstract: This paper presents the results of the static tensile and fatigue life tests under rotating bending of round 1.4301 (AISI 304) steel samples. The fatigue tests were carried out on smooth and notched samples with three different rounding angles with a shape factor of 1.4, 2 and 2.6. A fatigue life was determined for samples with different shape factors subject to identical loads. The results showed that the scatter of fatigue test results decreases with an increase in shape factor. To evaluate the cracking properties (cracking mode and mechanism), microstructure and fractographic tests of the fractured samples were carried out. Keywords: fatigue design; S–N curve; high-cycle fatigue; stainless steel 1. Introduction The use of stainless steel in engineering has grown significantly in recent years. In 2018, the use of stainless steel in the industry has grown over 60% compared to 2010 [1], estimated at 50.7 Mt [2]. -
Effect of Stress Concentration in Low Cycle Fatigue Life Prediction at High Temperature
Journal of Basic and Applied Engineering Research Print ISSN: 2350-0077; Online ISSN: 2350-0255; Volume 1, Number 2; October, 2014 pp. 69-72 © Krishi Sanskriti Publications http://www.krishisanskriti.org/jbaer.html Effect of Stress Concentration in Low Cycle Fatigue Life Prediction at High Temperature Richa Agrawal 1, Rashmi Uddanwadiker 2, Pramod Padole 3, Veerababu J.4 Department of Mechanical Engineering, Pillai Institute of Information and Technology, Maharashtra Abstract: Low Cycle Fatigue (LCF) is one of the dominant failure specimen. The state of stress can be varied by changing the modes in high temperature structural components. LCF behavior notch root radius. of notched specimens and un-notched specimens made of 316(L)N was investigated. Test were conducted on un-notched 316L(N) is a low carbon, nitrogen-enhanced version of type specimens and notched specimens with circular notch with varying diameter at high temperature in order to study the effect 316 molybdenum-bearing austenitic stainless steel. The type of notch at high temperature on estimation of fatigue life of 316 alloys are more resistant to general corrosion and pitting 316(L) N. The results were also compared with the simulated corrosion than the conventional chromium-nickel austenitic results. The fatigue life at high temperature decreased with the stainless steels such as type 304. They also offer higher creep, increase in notch severities. stress-rupture and tensile strength at elevated temperature. The nitrogen in type 316L(N) adds additional resistance to 1. INTRODUCTION sensitization in some circumstances and also provides some solid solution hardening, raising its minimum specified yield Fatigue is a localized damage process of a component strength compared to type 316L stainless steel. -
Fatigue Testing
Atlas of Fatigue Curves Copyright © 1986 ASM International® H.E. Boyer, Author All rights reserved www.asminternational.org 1 Fatigue Testing ence of reversed stresses that exceed the flow Introduction stress, followed by development of cracks at per Fatigue is the progressive, localized, perma sistent slip bands or at grain boundaries. nent structural change that occurs in materials subjected to fluctuating stresses and strains that Prediction of Fatigue life may result in cracks or fracture after a sufficient The fatigue life of any specimen or structure is number of fluctuations. Fatigue fractures are the number of stress (strain) cycles required to caused by the simultaneous action of cyclic cause failure. This number is a function of many stress, tensile stress and plastic strain. If any one variables, including stress level, stress state, cy of these three is not present, fatigue cracking will clic wave form, fatigue environment, and the not initiate and propagate. The cyclic stress metallurgical condition of the material. Small starts the crack; the tensile stress produces crack changes in the specimen or test conditions can growth (propagation). Although compressive significantly affect fatigue behavior, making ana stress will not cause fatigue, compression load lytical prediction of fatigue life difficult. There may do so. fore, the designer may rely on experience with The process of fatigue consists of three stages: similar components in service rather than on • Initial fatigue damage leading to crack nu laboratory evaluation of mechanical test speci cleation and crack initiation mens. Laboratory tests, however, are essential in • Progressive cyclic growth of a crack (crack understanding fatigue behavior, and current propagation) until the remaining uncracked studies with fracture mechanics test specimens cross section of a part becomes too weak to are beginning to provide satisfactory design sustain the loads imposed criteria. -
Interacting Stress Concentration Factors and Their Effect on Fatigue of Metallic Aerostructures
Scholars' Mine Doctoral Dissertations Student Theses and Dissertations Fall 2013 Interacting stress concentration factors and their effect on fatigue of metallic aerostructures David Warren Whitley Follow this and additional works at: https://scholarsmine.mst.edu/doctoral_dissertations Part of the Aerospace Engineering Commons Department: Mechanical and Aerospace Engineering Recommended Citation Whitley, David Warren, "Interacting stress concentration factors and their effect on fatigue of metallic aerostructures" (2013). Doctoral Dissertations. 1830. https://scholarsmine.mst.edu/doctoral_dissertations/1830 This thesis is brought to you by Scholars' Mine, a service of the Missouri S&T Library and Learning Resources. This work is protected by U. S. Copyright Law. Unauthorized use including reproduction for redistribution requires the permission of the copyright holder. For more information, please contact [email protected]. INTERACTING STRESS CONCENTRATION FACTORS AND THEIR EFFECT ON FATIGUE OF METALLIC AEROSTRUCTURES by DAVID WARREN WHITLEY A DISSERTATION Presented to the Faculty of the Graduate School of the MISSOURI UNIVERSITY OF SCIENCE AND TECHNOLOGY In Partial Fulfillment of the Requirements for the Degree DOCTOR OF PHILOSOPHY in AEROSPACE ENGINEERING 2013 Approved by Dr. Lokeswarappa R. Dharani, Advisor Dr. Victor Birman, Co-Advisor Dr. K. Chandrashekhara Dr. Daniel Stutts Dr. Jefferey Thomas iii ABSTRACT During fabrication of certain aerostructure components, a situation can arise where a hole is mislocated so that it interferes with a radius, chem-mill step, machined step, or some other similar detail. The interaction of stress concentration effects between a hole and step are not well understood and the resulting impact on fatigue performance is difficult to predict. There exists a need for fatigue data that can be used to determine the analysis methods for evaluation of the interaction of machined steps and fastener holes. -
The Role of Grain Boundaries on Fatigue Crack Initiation В
International Journal of Plasticity xxx (2010) xxx–xxx Contents lists available at ScienceDirect International Journal of Plasticity journal homepage: www.elsevier.com/locate/ijplas The role of grain boundaries on fatigue crack initiation – An energy approach ⇑ Michael D. Sangid a, Hans J. Maier b, Huseyin Sehitoglu a, a Department of Mechanical Science and Engineering, University of Illinois at Urbana-Champaign, 1206 W. Green St., Urbana, IL 61801, USA b Lehrstuhl für Werkstoffkunde (Materials Science), University of Paderborn, 33095 Paderborn, Germany article info abstract Article history: In this paper, we construct a model for prediction of fatigue crack initiation based on the Received 6 August 2010 material’s microstructure. In order to do so, the energy of a persistent slip band (PSB) is Received in final revised form 14 September monitored and an energy balance approach is taken, in which cracks initiate and the mate- 2010 rial fails due to stress concentration from a PSB (with respect to dislocation motion). These Available online xxxx PSBs are able to traverse low-angle grain boundaries (GB), thus belonging to clusters of grains. As a consequence of the ongoing cyclic slip process, the PSBs evolve and interact Keywords: with high-angle GBs, the result of which leads to dislocation pile-ups, static extrusions Fatigue in the form of ledges/steps at the GB, stress concentration, and ultimately crack initiation. Grain boundaries Polycrystalline material Hence, this fatigue model is driven by the microstructure, i.e. grain orientations, widely Energy methods distributed grain sizes, precipitates, PSB–GB interactions, as well as the affect of neighbor- Persistent slip bands ing grains.