Numerical Analysys of Tipical Aircraft Air-Conditioning Air Cycle Machines
Total Page:16
File Type:pdf, Size:1020Kb
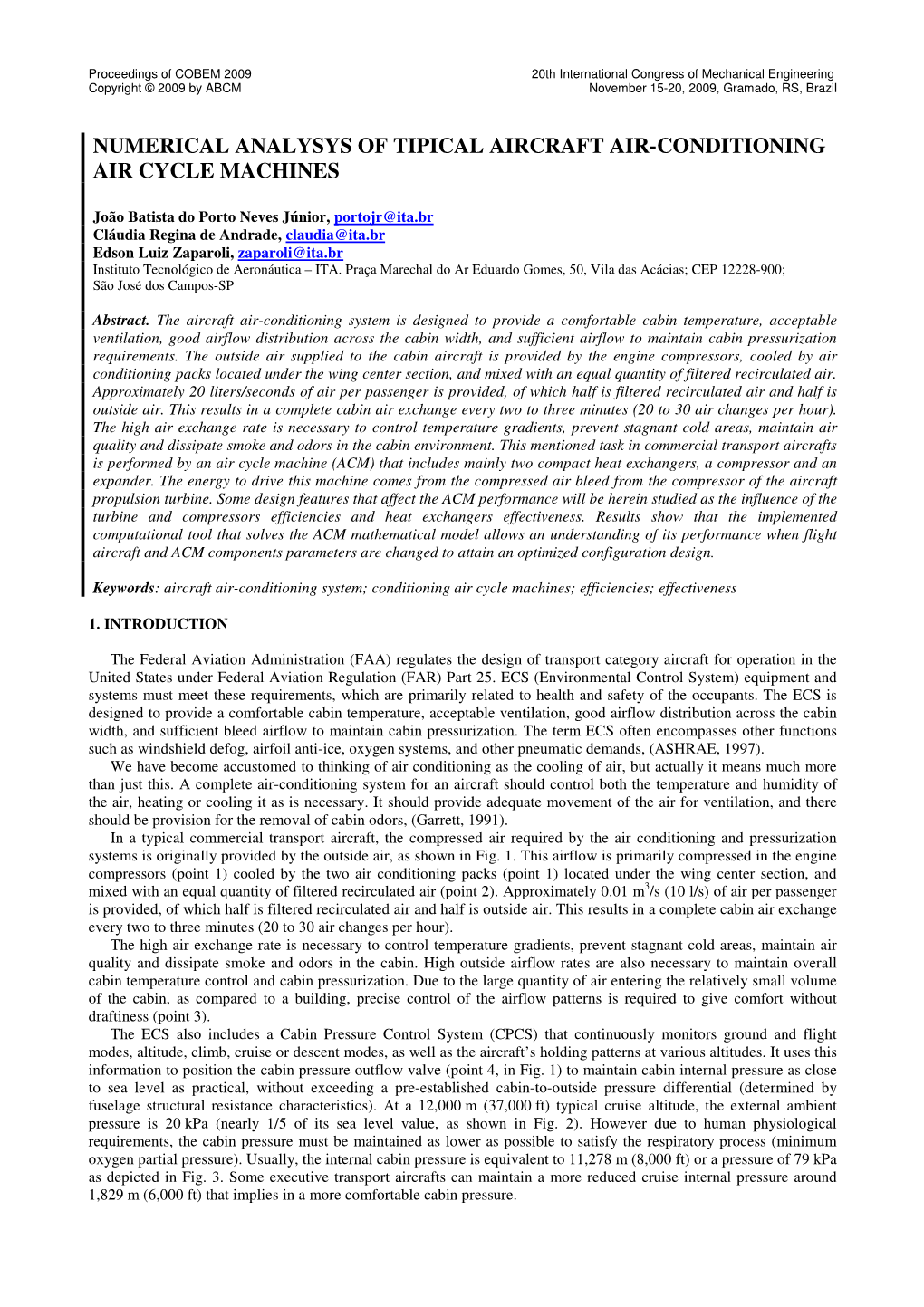
Load more
Recommended publications
-
Exergy-Based Analysis of Aircraft Environmental Control Systems and Its Integration Into Model-Based Design
Exergy-Based Analysis of Aircraft Environmental Control Systems and its Integration into Model-Based Design vorgelegt von Diplom-Ingenieur Daniel Bender geb. in Nürnberg von der Fakultät III - Prozesswissenschaften der Technischen Universität Berlin zur Erlangung des akademischen Grades Doktor der Ingenieurwissenschaften - Dr.-Ing. - genehmigte Dissertation Promotionsausschuss: Vorsitzender: Prof. Dr.-Ing. Felix Ziegler Gutachterin: Prof. Dr. Tetyana Morozyuk Gutachter: Dr. Dirk Zimmer Tag der wissenschaftlichen Aussprache: 25. September 2018 Berlin 2019 Once you have tasted flight, you will forever walk the earth with your eyes turned skyward, for there you have been, and there you will always long to return. – Leonardo da Vinci – Acknowledgements The idea for the topic of this thesis developed at the end of 2013 shortly after I started working at the DLR German Aerospace Center. Up until that time, exergy analysis had not been covered at the institute. My research on that topic then brought me to the TU Berlin. After a wonderful experience at the ELCAS2015 conference in Greece, Prof. Tsatsaronis and Prof. Morozyuk warmly welcomed us in Berlin and showed great interest in our proposal for bringing exergy and aircraft environmental control systems together. On this day, a wonderful collaboration began that hopefully will not end with this PhD thesis. First of all, I want to express my gratitude to Prof. Tetyana Morozyuk for her personal and inspiring supervision of my PhD thesis, for the great time and discussions during my visits in Berlin and the opportunity to join the TU Berlin group for many conferences. Every time I was warmly welcomed and felt like a part of the group. -
Influences of Different Architectures on the Thermodynamic Performance
entropy Article Influences of Different Architectures on the Thermodynamic Performance and Network Structure of Aircraft Environmental Control System Han Yang 1,2, Chunxin Yang 1,2,* , Xingjuan Zhang 1 and Xiugan Yuan 1 1 School of Aeronautic Science and Engineering, Beihang University, Beijing 100191, China; [email protected] (H.Y.); [email protected] (X.Z.); [email protected] (X.Y.) 2 Beijing Advanced Discipline Center for Unmanned Aircraft System, Beijing 100191, China * Correspondence: [email protected] Abstract: The environmental control system (ECS) is one of the most important systems in the aircraft used to regulate the pressure, temperature and humidity of the air in the cabin. This study investigates the influences of different architectures on the thermal performance and network structure of ECS. The refrigeration and pressurization performances of ECS with four different architectures are analyzed and compared by the endoreversible thermodynamic analysis method, and their external and internal responses have also been discussed. The results show that the connection modes of the heat exchanger have minor effects on the performance of ECSs, but the influence of the air cycle machine is obvious. This study attempts to abstract the ECS as a network structure based on the graph theory, and use entropy in information theory for quantitative evaluation. The results provide Citation: Yang, H.; Yang, C.; a theoretical basis for the design of ECS and facilitate engineers to make reliable decisions. Zhang, X.; Yuan, X. Influences of Different Architectures on the Keywords: environmental control system; endoreversible thermodynamic analysis method; refrigeration; Thermodynamic Performance and pressurization; information entropy; network structure Network Structure of Aircraft Environmental Control System. -
Environmental Control System for Military & Civil Aircraft
Global Journal of researches in engineering: d AEROSPACE Engineering Volume 11 Issue 5 Version 1.0 August 2011 Type: Double Blind Peer Reviewed International Research Journal Publisher: Global Journals Inc. (USA) Online ISSN: 2249-4596 & Print ISSN: 0975-5861 Environmental Control System for Military & Civil Aircraft By Prof. D.V.Mahindru, Ms Priyanka Mahendru SRMGPC, Tewari Ganj, Lucknow, U.P. , India Abstract - With a view to provide cooling, heating, ventilation, humidity/contaminant control and pressurization within aircraft occupied compartments, cargo compartments and electronic equipment bays Environmental Control system is a part of all Military and civil aircrafts . It also caters to other pneumatic demands like windshield demisting, aerofoil anti-icing, door-sealing, fuel-tank pressurization and engine bay ventilation. The technology used for air conditioning of all types of Military/Civil aircrafts is predominantly Air Cycle air Conditioning. Based upon Joule or Reversed Brayton Cycle, the system utilizes the high temperature, high pressure bleed air extracted from compressor of main engine/APU. It not only enjoys the advantage of simplicity and inherent compactness of pneumatic equipment but also meets the integrated cooling and pressurization requirements of an aircraft. Both air-cycle based refrigeration system which lowers the enthalpy level of air by transforming heat energy into work and conventional vapor compression cooling system that extracts heat by evaporating a suitable liquid refrigerant have their own limitations. Keywords: Air Management System, ventilation, humidity/ contaminant control windshield demisting, aerofoil anti-icing, door-sealing, fuel-tank pressurization engine bay ventilation and pressurization within aircraft . GJRE- D Classification : FOR Code: 090799 Environmental Control System for Military Civil Aircraft Strictly as per the compliance and regulations of: © 2011. -
Integrated Air Management System Page 1
Bombardier Global Express - Integrated Air Management System INTRODUCTION BLEED AIR SYSTEM The Bleed Air System is controlled during all phases of operation by two Bleed Management Controllers (BMC). The BMCs provide indications and warnings to EICAS and maintenance information to CAIMS. In the Bleed Air System, normal flight operations, supplies air from the engines to the ECS and Wing and Cowl Anti-Ice systems. For more information on Ice and Rain Protection, refer to Chapter 3. On the ground air is normally supplied from the APU. A high-pressure ground air supply unit or bleed air from the engines can also be used. The Bleed Air System control panel is located on the overhead panel. ENVIRONMENTAL CONTROL SYSTEM (ECS) The Environmental Control System (ECS) performs the following functions: • Provides conditioned air • Provides ram air in the event of a total ECS failure • Provides air for pressurization control • Controls cockpit and passenger compartment temperature control • Provides sufficient airflow for emergency pressurization • Provides air recirculation • Exhausts the air from the cockpit and the cabin • Exhausts the air from the toilets and the galley(s) • Ventilates the avionics bay and cockpit displays • Provides indications and warnings to the EICAS and maintenance information to the Central Aircraft Information Maintenance System (CAIMS) The air conditioning system is controlled during all phases of operation by two Air Conditioning System Controllers (ACSC). The ACSCs provide indications and warnings to EICAS and maintenance information to CAIMS. The air conditioning system is comprised of the following subsystems: • Flow Control System • Air Conditioning Units (2) • Temperature Control System • Air Distribution and Exhaust System • Emergency Pressurization System The Air Conditioning System control panel is located on the overhead panel. -
Dynamic Modeling of Thermal Management System with Exergy Based Optimization
Dynamic Modeling of Thermal Management System with Exergy Based Optimization A thesis submitted in partial fulfillment of the requirements for the degree of Master of Science in Mechanical Engineering By: Marcus J. Bracey B.S.M.E., Wright State University, 2016 2017 Wright State University WRIGHT STATE UNIVERSITY GRADUATE SCHOOL May 23, 2017 I HEREBY RECOMMEND THAT THE THESIS PREPARED UNDER MY SUPERVISION BY Marcus J. Bracey ENTITLED Dynamic Modeling of Aircraft Thermal Management System with Exergy Based Optimization BE ACCEPTED IN PARTIAL FULFILLMENT OF THE REQUIREMENTS FOR THE DEGREE OF Master of Science in Mechanical Engineering. Committee on Final Examination Rory Roberts, Ph.D Rory Roberts, Ph.D Thesis Director Mitch Wolff, Ph.D James Menart, Ph.D Thesis Director Joseph Slater, Ph.D, P.E. Mitch Wolff, Ph.D Chair, Department of Mechanical and Materials Engineering Robert E.W. Fyffe, Ph.D Vice President for Research and Dean of the Graduate School ABSTRACT Bracey, Marcus J., M.S.M.E. Department of Mechanical and Materials Engineering, Wright State University, 2016. Dynamic Modeling of Aircraft Thermal Management System with Exergy Based Optimization. System optimization and design of aircraft is required to achieve many of the long term objectives for future aircraft platforms. To address the necessity for system optimization a vehicle-level aircraft model has been developed in a multidisciplinary modeling and simulation environment. Individual subsystem models developed exclusively in MATLAB-SimulinkTM, representing the vehicle dynamics, the propulsion, electrical power, and thermal systems, and their associated controllers, are combined to investigate the energy and thermal management issues of tactical air vehicle platforms. -
Heat Pump and Refrigeration Cycle
Project – OASIS MACHINE October 19, 2014 Subject – ENERGY & WATER PRODUCTION Page 1 of 17 OASIS MACHINE The following 1st concept sketch was produced as a means of defining this device as we prepare for funding applications. Also to communicate with our several development teams relative to their supplying the Electric PowerUnit: GEMs David Yurth of Nova Inst. Of Technology Bo Tomlyn All other components for this OASIS machine are easily available open market, EXCEPT FOR THE POWER SUPPLY. COMPONENTS ELECTRIC POWER UNIT New technology, over unity device, requires no external power or fuel. Power output from 25 to 50 KW, voltages as noted. Internally powers pumps, fans, UV unit, refrigeration unit, lights. C:\Users\Dozier\Downloads\OASISMACHINEcOSx.docx GEMs ATMOSPHERIC WATER GENERATION (AWG) UNIT Atmospheric water is condensed out of the air by a cold surface that is colder than the dew point temperature. Any commercially available refrigeration or air conditioning unit could work in this application. Filters, fans, cold coils, and condensate collection pan. WATER PROCESSING UNIT Agricultural water does not require processing. It flows directly from the condensate collection pan into ponds and reservoirs. Potable water is filtered and treated with UV light. Hot and cold water is produced for cooking, drinking, washing, etc. REFRIGERATION UNIT The refrigeration cycle produces both hot and cold air. Cooling coils are used for condensing water from the atmosphere. Heating coils are used for heating homes, greenhouses, barns, etc. BASIS FOR DESIGN This unit is intended to open up for farming vast tracts of arid land that is now not being used due to lack of water. -
Design and Assessment of a Novel Electrically Driven Environmental Control System for More Electric Aircraft
Design and assessment of a Novel Electri- cally Driven Environmental Control System for More Electric Aircraft M. A. Popescu 4278372 Delft University of Technology Design and assessment of a Novel Electrically Driven Environmental Control System for More Electric Aircraft by M. A. Popescu 4278372 in partial fulfillment of the requirements for the degree of Master of Science in Aerospace Engineering at the Delft University of Technology, to be defended publicly on 05.06.2020 Student number: 4278372 Project duration: January 15, 2019 – April 15, 2020 Supervisor: Dr. ir. R. Vos, TU Delft Thesis committee: Prof. dr. ir. P.Colonna, TU Delft Prof. dr. ir. S. A. Klein, TU Delft Cover image made by the author. An electronic version of this thesis is available at http://repository.tudelft.nl/. PREFACE The current research represents the final step towards graduation from Technical University of Delft. During a time span of just more than one year I had the chance to focus my attention to the field of environmental control systems for aircraft applications. The complete process of gathering literature data, setting up simu- lation models for electrically driven air cycle machine systems as well as for vapour cycle refrigeration units, verifying the models using uncertainty analysis, validating models using experimental data and analysing results has been a strong foundation for my upcoming career in the aerospace industry. I hope the work per- formed can be valuable for future students wishing to pursue a thesis in the field of environmental control systems. I would like to thank my supervisor dr. ir. Roelof Vos for his support and guidance provided throughout the various steps of the master thesis. -
A Comparative Analysis of 3 and 4-Wheel Air Cycle Machines for Aeronautical Appications
ISSN 2176-5480 22nd International Congress of Mechanical Engineering (COBEM 2013) November 3-7, 2013, Ribeirão Preto, SP, Brazil Copyright © 2013 by ABCM A COMPARATIVE ANALYSIS OF 3 AND 4-WHEEL AIR CYCLE MACHINES FOR AERONAUTICAL APPICATIONS Cláudia Regina de Andrade Edson Luiz Zaparoli [email protected] [email protected] Instituto Tecnológico de Aeronáutica Pça Marechal Eduardo Gomes, 50 - 12228-900 - São José dos Campos, SP, Brasil Abstract. Air cycle refrigeration is an attractive alternative that has been employed to provide aircraft cabin cooling. The primary function of the cabin air conditioning and pressurization system is to maintain an aircraft environment that will ensure safety and comfort of the passengers and crew during all fly operational conditions and provide adequate avionics cooling. The energy to drive these machines comes from the compressed air bleed from the compressor of the aircraft propulsion turbine. Usually, ACM (Air Cycle Machine ) architecture includes mainly two compact air-to-air heat exchangers, a compressor and a expander with one or two expansion stages (called 3-whell or 4-whell configuration, respectively). At this context, this work focuses on a comparative thermodynamic study of 3 and 4 wheels air-conditioning aircraft air cycle machines. This comparison will be performed taking account some design features that affect the ACM performance as: aircraft flight Mach number, cabin altitude, heat exchanger effectiveness and compressed bleed air conditions. Results showed that the second level of expansion from 4-wheel air cycle machine increases its thermodynamic efficiency. As the amount of rejected heat in the secondary heat exchanger (SHX) is greater for the 4-wheel architecture, it is possible to have the same cooling effect than the 3-wheel machine but with a more compact SHX. -
Cycle Environmental Control System for Automotive Applications
DEVELOPMENT OF AN AIR‐CYCLE ENVIRONMENTAL CONTROL SYSTEM FOR AUTOMOTIVE APPLICATIONS A thesis Presented to the faculty of California Polytechnic State University San Luis Obispo In Partial Fulfillment of the Requirements for the Degree of Master of Science in Mechanical Engineering by Christopher J. Forster December 2009 i © 2009 Christopher J. Forster ALL RIGHTS RESERVED ii APPROVAL PAGE TITLE: DEVELOPMENT OF AN AIR‐CYCLE ENVIRONMENTAL CONTROL SYSTEM FOR AUTOMOTIVE APPLICATIONS AUTHOR: Christopher James Forster DATE SUBMITTED: Committee Chair: Dr. Patrick Lemieux Committee Member: Dr. Chris Pascual Committee Member: Dr. Kim Shollenberger iii Abstract Development of an Air‐Cycle Environmental Control System for Automotive Applications Christopher James Forster Mechanical Engineering Department California Polytechnic State University, San Luis Obispo An air‐cycle air conditioning system, using a typical automotive turbocharger as the core of the system, was designed and tested. Effects on engine performance were kept to a minimum while providing the maximum amount of cooling possible and minimizing weight and space requirements. A test stand utilizing shop compressed air was developed to measure component performance. An unmodified automotive turbocharger was tested initially as a baseline in a Reversed‐Brayton Cycle air cooling system. Once the baseline was established, another air‐ cycle machine, assembled from commercial turbocharger components chosen individually to optimize their performance for cooling purposes, was tested to improve the overall cycle efficiency. Finally, once the air‐cycle air conditioning system was optimized, it was tested on an engine to simulate more realistic operating conditions and performance. The shop‐air test stand experiments showed a peak dry‐air‐rated (DAR) coefficient of performance (COP) of 0.38 and a DAR cooling capacity of 0.45 tons for the baseline turbocharger, and a peak DAR COP of 0.73 and DAR cooling capacity of 1.5 tons for the optimized system with a modified turbocharger. -
Hybrid Environmental Control System Integrated Modeling Trade Study
Hybrid Environmental Control System Integrated Modeling Trade Study Analysis for Commercial Aviation A dissertation submitted to the Division of Research and Advanced Studies Of the University of Cincinnati in partial fulfillment of the requirements for the degree of DOCTORATE OF PHILOSOPHY (Ph.D.) In the Department of Aerospace Engineering and Engineering Mechanics Of the College of Engineering and Applied Science April 2014 By Javier Parrilla M.S. Aerospace Engineering, University Of Michigan, 2004 B.S. Mechanical Engineering, University of Puerto Rico, 2001 Committee Chair: Dr. Awatef Hamed ABSTRACT Current industry trends demonstrate aircraft electrification will be part of future platforms in order to achieve higher levels of efficiency in various vehicle level sub- systems. However electrification requires a substantial change in aircraft design that is not suitable for re-winged or re-engined applications as some aircraft manufacturers are opting for today. Thermal limits arise as engine cores progressively get smaller and hotter to improve overall engine efficiency[8], while legacy systems still demand a substantial amount of pneumatic, hydraulic and electric power extraction. The environmental control system (ECS) provides pressurization, ventilation and air conditioning in commercial aircraft[7], making it the main heat sink for all aircraft loads with exception of the engine. To mitigate the architecture thermal limits in an efficient manner, the form in which the ECS interacts with the engine will have to be enhanced as to reduce the overall energy consumed and achieve an energy optimized solution. This study examines a tradeoff analysis of an electric ECS by use of a fully integrated Numerical Propulsion Simulation System (NPSS) model that is capable of studying the interaction between the ECS and the engine cycle deck. -
Aircraft Cabin Air and Engine Oil an Engineering View
Hochschule für Angewandte Wissenschaften Hamburg Hamburg University of Applied Sciences AIRCRAFT DESIGN AND SYSTEMS GROUP (AERO) Aircraft Cabin Air and Engine Oil An Engineering View Dieter Scholz Hamburg University of Applied Sciences International Aircraft Cabin Air Conference 2017 Imperial College London, 19 - 20 September 2017 Hochschule für Angewandte Wissenschaften Hamburg Hamburg University of Applied Sciences Aircraft Cabin Air and Engine Oil An Engineering View Abstract Air conditioning in aviation means temperature control, pressure control and ventilation. The cabin is vented with a certain percentage (e.g. 50%) of fresh outside air. The remaining part of the air for cabin ventilation is provided as air from the cabin, filtered and recirculated back into the cabin. At cruise altitude, ambient pressure is below cabin pressure. Hence, the outside air needs to be compressed before it is delivered into the cabin. The air is compressed in the engine compressor and tapped off as "bleed air" at temperatures reaching 400 °C or more. Hence, bleed air cooling is necessary. The engine shaft is supported by lubricated bearings. They are sealed against the air in the compressor usually with labyrinth seals. It is explained why jet engine seals leak oil by design in small quantities. The amount of oil leakage can be estimated with a new equation. The estimate shows the same order of magnitude as measured in flight (Cranfield study, EASA study). The oil leaking into the compressor contains problematic additives which get pyrolized (burned) at the elevated temperatures in the compressor, leaving more than 100 substances behind, some of them hazardous and some known as Volatile Organic Compounds (VOC). -
Commercial Airliner Environmental Control System Engineering Aspects of Cabin Air Quality
Commercial Airliner Environmental Control System Engineering Aspects of Cabin Air Quality Elwood H. Hunt, Dr. Don H. Reid, David R. Space, and Dr. Fred E. Tilton This paper discusses engineering aspects of a modern commercial jet airliner environmental control system (ECS), focusing on cabin air quality. Recent national news media coverage suggests that aircraft cabin air quality is a serious concern. However, an Cabin pressure control valve objective review of pertinent data and Passenger compartment air distribution recent comprehensive testing do not Ozone catalytic converter (2 locations) support this perception. Air-conditioning packs (2 locations) Even more important than “air Mix manifold quality” is “survivability.” Because Recirculation system (2 locations) modern jet airplanes operate in a physical environment that is not Engine (2 locations) survivable by unprotected humans, these airplanes contain a complex ECS. Such systems enable survival, safety, and comfort. Aerospace Figure 1. Typical components and system layout for the 767 ECS medical experts are highly cognizant of this fact. ECS engineers study requirements for maintain- Flight Scenario ing human physiological integrity, provided by the aero- This discussion is based on a flight scenario from space medical community. These requirements are converted London’s Heathrow (HTH) airport to Los Angeles Interna- into components for environmental control and life support tional (LAX) airport. The airplane is a United Airlines 767- systems. Data from studies of human comfort factors are 300ER with Pratt & Whitney (P&W) 4000 engines. also applied to the design of these systems. The following discussion reviews the major components of the ECS that Engine sustains human life and comfort during flight.