Numerical Investigation of Transient Mixed Convection of Nanofluid in A
Total Page:16
File Type:pdf, Size:1020Kb
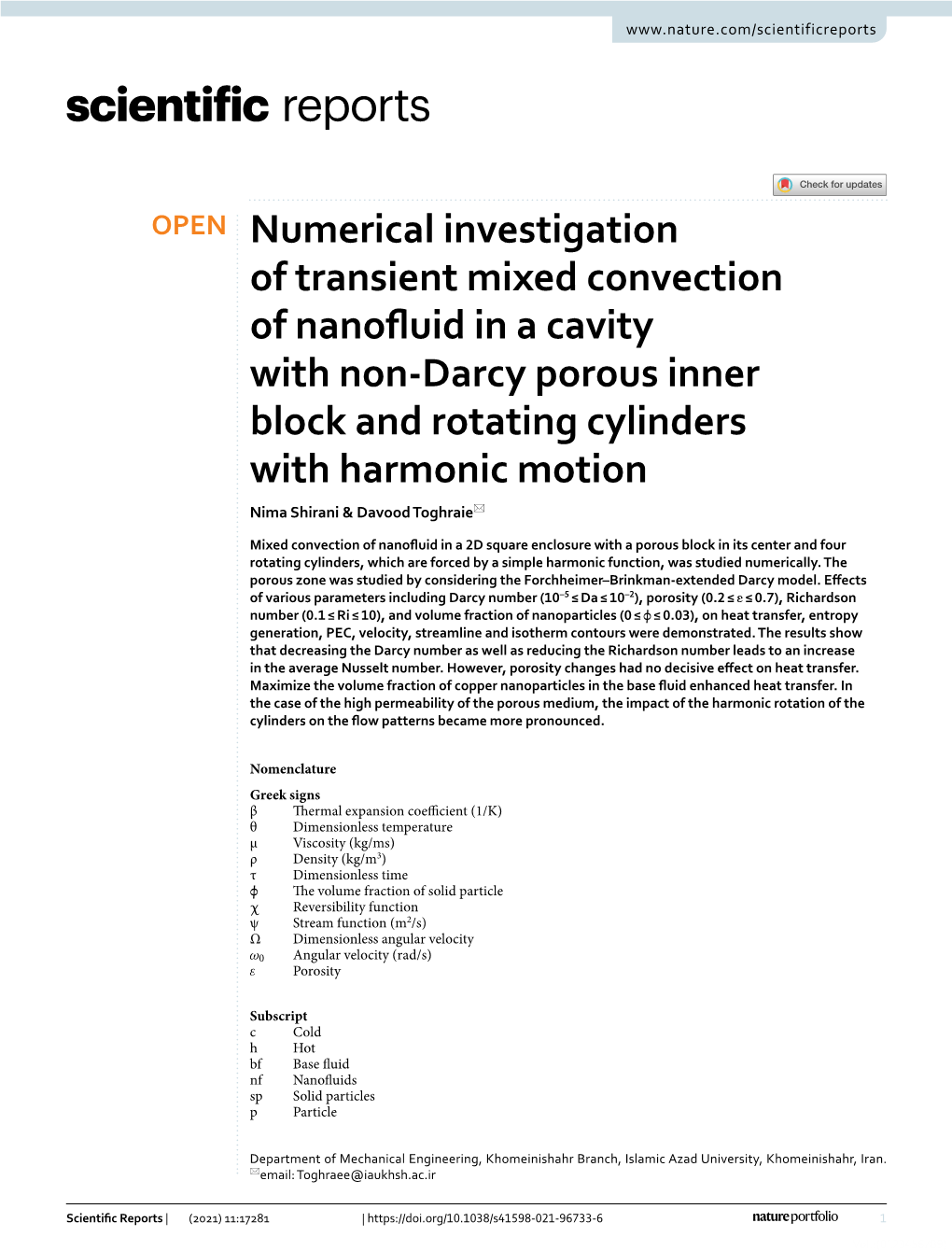
Load more
Recommended publications
-
Influence of Heat Source/Sink on Free Convection in Annular Porous Region
International Journal of Heat and Technology Vol. 39, No. 3, June, 2021, pp. 841-850 Journal homepage: http://iieta.org/journals/ijht Influence of Heat Source/Sink on Free Convection in Annular Porous Region Anurag1, Shyam Lal Yadav2*, Ashok Kumar Singh1 1 Department of Mathematics, Institute of Science, Banaras Hindu University, Varanasi 221005, Uttar Pradesh, India 2 Department of Mathematics, Lok Nayak Jai Prakash Institute of Technology, Chhapra 841302, Bihar, India Corresponding Author Email: [email protected] https://doi.org/10.18280/ijht.390318 ABSTRACT Received: 4 January 2020 The significant interpretation of this model is to explore the influence of temperature- Accepted: 26 December 2020 dependent heat source/sink on laminar free-convective flow in an annular porous region such as petroleum engineering, thermal technique and groundwater hydrology. For a Keywords: unified solution of the Brinkman-Darcy model, the regulatory equations solved analytically fully developed flow, natural convection, by applying the variation of parameter technique in terms of Bessel's functions for the heat source and sink, isothermal and constant heat source and sink. Moreover, we have investigated the Variations of Darcy number, Heat flux, modified Bessel function source/sink and viscosity ratio in the presence of isothermal and constant heat flux sequentially. As a result, we received the critical value of the velocity for the radii ratio (R = 2.05 and 2.92) in both the cases of source and sink (S = 1.0 and Si = 0.1) respectively which is exhibited through the graphs. Further, the numerical outcomes present of the skin friction including volume flow with annular gap by the graphs as well as tables. -
Stability of Thermosolutal Free Convection on Electrically Conducting Superposed Fluid and Porous Layer
International Journal of Applied Engineering Research ISSN 0973-4562 Volume 13, Number 17 (2018) pp. 13022-13030 © Research India Publications. http://www.ripublication.com Stability of Thermosolutal Free Convection on Electrically Conducting Superposed Fluid and Porous Layer K.Sumathi1*, T.Arunachalam2 and S.Aiswarya3 Department of Mathematics, 1,3PSGR Krishnammal College for Women, Coimbatore – 641 004, TamilNadu, India. 2Kumaraguru College of Technology, Coimbatore – 641 049, TamilNadu, India. (*Corresponding Author) Abstract investigated the onset of convection in a horizontal sparsely packed porous medium with imposed thermal and The effect of thermosolutal convection on linear stability of an concentration gradient at both the boundaries and found that incompressible fluid in a horizontal fluid/porous interface in Darcy number destabilizes the system in case of stationary the presence of a vertical magnetic field has been analyzed. and oscillatory convection. Asymptotic solution is obtained for rigid boundaries using normal mode analysis and the analysis is restricted to long Jena et al. [6] by employing Darcy-Brinkman-Forchheimer wave approximations. The influence of various non- model studied about the linear stability of onset of dimensional parameters such as Chandrasekhar number, thermosolutal convection in a rectangular annulus which is magnetic Prandtl number, Schmidt number, Prandtl number, highly heated and soluted from within and exposed to low porosity, wave number and depth ratio on stability thermal and solutal gradients from outside in a non-Darcian characteristics of flow field are represented numerically. region. Abdullah et al. [2] studied the effect of thermosolutal convection of a viscous incompressible fluid in the presence Keywords: Thermosolutal convection, magnetic field, fluid- of rotation on the stability of the system and observed that porous interface, stability analysis. -
Numerical Simulation of Williamson Combined Natural and Forced
entropy Article Numerical Simulation of Williamson Combined Natural and Forced Convective Fluid Flow between Parallel Vertical Walls with Slip Effects and Radiative Heat Transfer in a Porous Medium Mohammad Yaghoub Abdollahzadeh Jamalabadi 1,*, Payam Hooshmand 2, Navid Bagheri 3, HamidReza KhakRah 4 and Majid Dousti 5 1 Department of Mechanical, Robotics and Energy Engineering, Dongguk Universit, Seoul 04620, Korea 2 Young Researchers and Elite Club, Mahabad Branch, Islamic Azad University, Mahabad 433-59135, Iran; [email protected] 3 Department of Energy Engineering, Graduate School of the Environment and Energy, Science and Research Branch, Islamic Azad University, Tehran 1477893855, Iran; [email protected] 4 Department of Mechanical Engineering, College of Engineering, Shiraz Branch, Islamic Azad University, Shiraz 71987-74731, Iran; [email protected] 5 Faculty of Engineering, Zanjan University, Zanjan 38791-45371, Iran; [email protected] * Correspondence: [email protected] or [email protected]; Tel.: +82-22-260-3073 Academic Editor: Milivoje M. Kostic Received: 29 February 2016; Accepted: 8 April 2016; Published: 18 April 2016 Abstract: Numerical study of the slip effects and radiative heat transfer on a steady state fully developed Williamson flow of an incompressible Newtonian fluid; between parallel vertical walls of a microchannel with isothermal walls in a porous medium is performed. The slip effects are considered at both boundary conditions. Radiative highly absorbing medium is modeled by the Rosseland approximation. The non-dimensional governing Navier–Stokes and energy coupled partial differential equations formed a boundary problem are solved numerically using the fourth order Runge–Kutta algorithm by means of a shooting method. Numerical outcomes for the skin friction coefficient, the rate of heat transfer represented by the local Nusselt number were presented even as the velocity and temperature profiles illustrated graphically and analyzed. -
Finite Element Solutions for Non-Newtonian Pulsatile Flow in a Non-Darcian Porous Medium Conduit ∗
Nonlinear Analysis: Modelling and Control, 2007, Vol. 12, No.3, 317–327 Finite Element Solutions for Non-Newtonian Pulsatile Flow in a Non-Darcian Porous Medium Conduit ∗ R. Bhargava1, H. S. Takhar2, S. Rawat1, Tasveer A. Bég3, O. Anwar Bég4 1Mathematics Department, Indian Institute of Technology Roorkee-247667, India [email protected] 2Engineering Department, Manchester Metropolitan University Oxford Rd., Manchester, M5 1GD, UK [email protected] 3Engineering Mechanics and Earthquake Dynamics Research 18 Milton Grove, Manchester, M16 OBP [email protected] 4Fire Engineering Sciences, Leeds College of Building / Leeds Metropolitan University North Street, Leeds, LS2 7QT, UK [email protected] Received: 17.05.2006 Revised: 08.11.2006 Published online: 31.08.2007 Abstract. The present analysis is motivated by the need to elucidate with more accuracy and sophistication the hydrodynamics of non-Newtonian flow via a channel containing a porous material under pulsating pressure gradient. A one-dimensional transient rheological model for pulsating flow through a Darcy-Forcheimmer porous channel is used. A modified Casson non-Newtonian constitutive model is employed for the transport fluid with a drag force formulation for the porous body force effects. The model is transformed and solved using a finite element numerical technique. Rheological effects are examined using a β parameter which vanishes in the limit (Newtonian flow). Velocity profiles are plotted for studying the influence of Reynolds number, Darcy number, Forchheimer number and the β (non-Newtonian) parameter. The channel considered is rigid with a pulsatile pressure applied via an appropriate pressure gradient term. The model finds applications in industrial filtration systems, pumping of polymeric fluids etc. -
Effect of Darcy, Reynolds, and Prandtl Numbers on the Performance of Two-Phase Flow Heat Exchanger Filled with Porous Media
Heat Transfer—Asian Research, 43 (8), 2014 Effect of Darcy, Reynolds, and Prandtl Numbers on the Performance of Two-Phase Flow Heat Exchanger Filled with Porous Media M. Tarawneh,1 A.S. Alshiqirate,2 and A.M. Jawarneh1 1Mechanical Engineering, The Hashemite University, Zarqa, Jordan 2Mechanical Engineering, Alshoubak University College, Al-Balqa’ Applied University, Alsalt, Jordan Experimental investigation of two-phase laminar forced convection in a single porous tube heat exchanger is presented. The effect of Darcy, Reynolds, and Prandtl numbers on the performance of this heat exchanger during the condensation process of carbon dioxide at different test conditions were investigated. Gravel sand with different porosities is used as a porous medium. The flow in the porous medium is modeled using the Brinkman–Forchheimer-extended Darcy model. Parametric studies are also conducted to evaluate the effects of porosity and Reynolds and Prandtl numbers on the heat transfer coefficient and the friction factor. A dimensionless performance parameter is developed in order to be used in evaluating the porous tube heat exchanger based on both the heat transfer enhancement and the associated pressure. drop. The study covers a wide range of inlet pressure (Pin), mass flow rate ε ≤ ≤ (m), porosity of gravel. sand ( ), and Darcy number (Da) which ranged: 34.5 Pin 43 bars, 8*10–5 ≤ m ≤ 16*10–5 kg/s, 34.9% ≤ ε ≤ 44.5%, 1.6*10–6 ≤ Da ≤ 5*10–6, respectively. The study predicted the combined effect of the Reynolds number, Darcy number, porosity, and Prandtl number on the heat transfer and pressure drop of carbon dioxide during the condensation process in a porous medium. -
Analysis of Transport Models and Computation Algorithms for Flow Through Porous Media
ANALYSIS OF TRANSPORT MODELS AND COMPUTATION ALGORITHMS FOR FLOW THROUGH POROUS MEDIA DISSERTATION Presented in Partial Fulfillment of the Requirements for the Degree Doctor of Philosophy in the Graduate School of The Ohio State Univeristy By Bader Shabeeb Al-Azmi, M.S. ***** The Ohio State University 2003 Dissertation Committee: Approved by Professor Kambiz Vafai, Adviser Professor Robert Henry Essenhigh ___________________________ Professor Sudhir Sastry Adviser Department of Mechanical Engineering ABSTRACT Computational investigation of variant models and boundary conditions in the area of fluid flow and heat transfer in porous media is presented in this dissertation. This study is divided into four major parts. In the first part, a summary of variant models of fluid flow and heat transfer through porous media found in the literature is presented. These variances can be categorized into four primary sections, constant porosity, variable porosity, thermal dispersion and local thermal non-equilibrium. Models for constant porosity and variable porosity are presented in terms of Darcy, Brinkman and Forchheimer terms. The second part focuses on the interfacial conditions between a porous layer and a fluid layer. It is found that these interface conditions can be classified as a slip or a no slip. The no slip conditions assume a continuity of the property, velocity and/or temperature, while a discontinuity at the interface is assumed for the slip interface conditions. It is shown that in general, the variances have a more pronounced effect on the velocity field and a substantially smaller effect on the temperature field and even a smaller effect on the Nusselt number distributions. When constant heat flux boundary conditions are present, it is found that researchers use inconsistent wall temperature and heat flux boundary conditions at the solid walls of the porous medium. -
Numerical Simulation of Vortex Shedding at Triangular Obstacle for Various Reynolds Numbers and Times with Open FOAM
International Journal of Engineering and Applied Sciences (IJEAS) ISSN: 2394-3661, Volume-4, Issue-7, July 2017 Numerical Simulation of Vortex Shedding at Triangular Obstacle for Various Reynolds Numbers and Times with Open FOAM Ahmad Jafari, Seyyedeh Zahra Malekhoseini Abstract— The present study aimed to simulate the rotational movements and create a regular pattern of vortices two-dimensional flow around a triangular obstacle in a channel. in the wake region (Figure 1). Rajani et al. simulated an Numerical study was performed by the open-source numerical unsteady laminar flow downstream of an obstacle using the model, OpenFOAM. IcoFoam solver was used to solve the open-source model OpenFOAM [3]. As a result, length of the equations governing the flow in the modeling. The wake region was reduced and the flow separation point was Navier-Stokes and continuity equations are the dominant changed in the small gap between the side wall and the equations in this solver. In the first step, flow lines and velocity vectors were simulated for Reynolds numbers of 20, 30 and 35. obstacle. Wei et al. simulated and analyzed vortex-induced The simulations showed that the separation of flow lines and the vibrations for a circular obstacle using the numerical model formation of vortex bubbles depend on the Reynolds number, OpenFOAM [4]. The results of this numerical model were even when this parameter slightly increases. In the second step, similar to those obtained from experimental data. Roohi et al. the flow lines at six different times with the time interval t/6 at examined the backflow downstream of an obstacle using the Reynolds numbers of 150 and 200 were identified. -
Effect of Magnetic Field on the Mixed Convection Ferrofluid Flow in A
Pramana – J. Phys. (2020) 94:156 © Indian Academy of Sciences https://doi.org/10.1007/s12043-020-02015-7 Effect of magnetic field on the mixed convection Fe3O4/water ferrofluid flow in a horizontal porous channel AMIRA JARRAY, ZOUHAIER MEHREZ∗ and AFIF EL CAFSI Laboratoire d’Energétique et des Transferts Thermique et Massique (LETTM), Département de Physique, Faculté des Sciences de Tunis, Université d’el Manar, Tunis, Tunisia ∗Corresponding author. E-mail: [email protected]; [email protected] MS received 7 May 2020; revised 11 July 2020; accepted 29 July 2020 Abstract. The effect of an external magnetic field on the mixed convection Fe3O4/water ferrofluid flow in a horizontal porous channel was studied numerically. The governing equations using the Darcy–Brinkman– Forchheimer formulation were solved by employing the finite volume method. The computations were carried out for a range of volume fractions of nanoparticles 0 ≤ ϕ ≤ 0.05, magnetic numbers 0 ≤ Mn ≤ 100, Reynolds numbers 100 ≤ Re ≤ 500, Darcy numbers 10−3 ≤ Da ≤ 10−1 and porosity parameters 0.7 ≤ ε ≤ 0.9 while fixing the Grashof number at 104. Results show the formation of recirculation zone in the vicinity of the magnetic source under the influence of Kelvin force. It grows as the magnetic number increases. The friction factor increases by increasing the magnetic number and diminishes with the increase in Darcy number. The flow accelerates as the magnetic field intensifies. The heat transfer rate increases by increasing the volume fraction of the nanoparticles and the magnetic number. The effect of magnetic field on the hydrodynamic and thermal behaviours of the ferrofluid flow considerably intensifies by increasing Reynolds number and Darcy number. -
Analytical Investigation Into Effects of Capillary Force on Condensate Film Flowing Over Horizontal Semicircular Tube in Porous Medium
Hindawi Mathematical Problems in Engineering Volume 2021, Article ID 6693512, 10 pages https://doi.org/10.1155/2021/6693512 Research Article Analytical Investigation into Effects of Capillary Force on Condensate Film Flowing over Horizontal Semicircular Tube in Porous Medium Tong-Bou Chang , Bai-Heng Shiue, Yi-Bin Ciou, and Wai-Io Lo Department of Mechanical and Energy Engineering, National Chiayi University, Chiayi, Taiwan Correspondence should be addressed to Tong-Bou Chang; [email protected] Received 17 November 2020; Revised 21 February 2021; Accepted 6 March 2021; Published 18 March 2021 Academic Editor: Luca Chiapponi Copyright © 2021 Tong-Bou Chang et al. *is is an open access article distributed under the Creative Commons Attribution License, which permits unrestricted use, distribution, and reproduction in any medium, provided the original work is properly cited. A theoretical investigation is performed into the problem of laminar filmwise condensation flow over a horizontal semicircular tube embedded in a porous medium and subject to capillary forces. *e effects of the capillary force and gravity force on the condensation heat transfer performance are analyzed using an energy balance approach method. For analytical convenience, several dimensionless parameters are introduced, including the Jakob number Ja, Rayleigh number Ra, and capillary force parameter Boc. *e resulting dimensionless governing equation is solved using the numerical shooting method to determine the effect of capillary forces on the condensate thickness. A capillary suction velocity can be obtained mathematically in the cal- culation process and indicates whether the gravity force is greater than the capillary force. It is shown that if the capillary force is greater than the condensate gravity force, the liquid condensate will be sucked into the two-phase zone. -
Analysis of Variants Within the Porous Media Transport Models
Analysis of Variants Within the Porous Media Transport Models An investigation of variants within the porous media transport models is presented in this B. Alazmi work. Four major categories in modeling the transport processes through porous media, namely constant porosity, variable porosity, thermal dispersion, and local thermal non- K. Vafai equilibrium, are analyzed in detail. The main objective of the current study is to compare e-mail: [email protected] these variances in models for each of the four categories and establish conditions leading to convergence or divergence among different models. To analyze the effects of variants Department of Mechanical Engineering, within these transport models, a systematic reduction and sensitivity investigation for The Ohio State University, each of these four aspects is presented. The effects of the Darcy number, inertia param- Columbus, OH 43210 eter, Reynolds number, porosity, particle diameter, and the fluid-to-solid conductivity ratio on the variances within each of the four areas are analyzed. It is shown that for some cases the variances within different models have a negligible effect on the results while for some cases the variations can become significant. In general, the variances have a more pronounced effect on the velocity field and a substantially smaller effect on the temperature field and Nusselt number distribution. ͓S0022-1481͑00͒02602-5͔ Keywords: Convection, Heat Transfer, Modeling, Porous Media 1 Introduction ciable flow maldistribution, which appears as a sharp peak near the solid boundary and decreases to nearly a constant value at the Modeling of the non-Darcian transport through porous media center of the bed. -
MHD Flow Heat and Mass Transfer of Micropolar Fluid
Journal of Applied Fluid Mechanics, Vol. 9, No. 1, pp. 321-331, 2016. Available online at www.jafmonline.net, ISSN 1735-3572, EISSN 1735-3645. MHD Flow Heat and Mass Transfer of Micropolar Fluid over a Nonlinear Stretching Sheet with Variable Micro Inertia Density, Heat Flux and Chemical Reaction in a Non-darcy Porous Medium S. Rawat1, S. Kapoor2† and R. Bhargava3 1Department of General Studies, Jubail University College, Jubail, Saudi Arabia. 2 Department of Mathematics, Regional Institute of Education, Bhubneswar (NCERT), India 3Department of Mathematics, Indian Institute of Technology, Roorkee - 247667, India. †Corresponding Author Email: [email protected] (Received July 27, 2014; accepted February 5, 2015) ABSTRACT This paper investigates the two dimensional flow, heat and mass transfer of chemically reacting Micropolar fluid over a non-linear stretching sheet with variable heat flux in a non-darcy porous medium. The rate of chemical reaction is assumed to be constant throughout the fluid i.e. homogenous. Using a similarity transformation, the governing partial differential equations are transformed into a system of ordinary differential equation, which is then solved using Finite element method. Numerical results regarding local Nussult No. are shown graphically with Magnetic number () for variation in heat transfer exponent (n). This study also analyzes the effect of velocity exponent m, heat transfer exponent n, material parameter K, Magnetic Number()Darcy NumberDax, Forchheimer Number Nfx, Prandtl number Pr, Schmidt Number Sc and Chemical reaction rate parameter x on velocity, microrotation, temperature and concentration profiles. Velocity exponent m has a positive effect on the velocity, temperature and concentration profiles while microrotation decreases as m increases. -
Information to Users
INFORMATION TO USERS This manuscript has been reproduced from the microfilm master. UMI films the text directly from the original or copy submitted. Thus, some thesis and dissertation copies are in typewriter face, while others may be from any type of computer printer. The quality of this reproduction is dependent upon the quality of the copy submitted. Broken or indistinct print, colored or poor quality illustrations and photographs, print bleedthrough, substandard margins, and improper alignment can adversely affect reproduction. In the unlikely event that the author did not send UMI a complete manuscript and there are missing pages, these will be noted. Also, if unauthorized copyright material had to be removed, a note will indicate the deletion. Oversize materials (e.g., maps, drawings, charts) are reproduced by sectioning the original, beginning at the upper left-hand corner and continuing from left to right in equal sections with small overlaps. Each original is also photographed in one exposure and is included in reduced form at the back of the book. Photographs included in the original manuscript have been reproduced xerographically in this copy. Higher quality 6" x 9" black and white photographic prints are available for any photographs or illustrations appearing in this copy for an additional charge. Contact UMI directly to order. University Microfilms International A Bell & Howell Information C om pany 300 North Z eeb Road. Ann Arbor. Ml 48106-1346 USA 313/761-4700 800/521-0600 Order Number 9325512 Investigation and modeling of complex interfacial effects for porous/non-porous configurations Huang, Po-Chuan, Ph.D. The Ohio State University, 1993 UMI 300 N.