Instability of Taylor-Couette Flow Between Concentric Rotating Cylinders, Inter
Total Page:16
File Type:pdf, Size:1020Kb
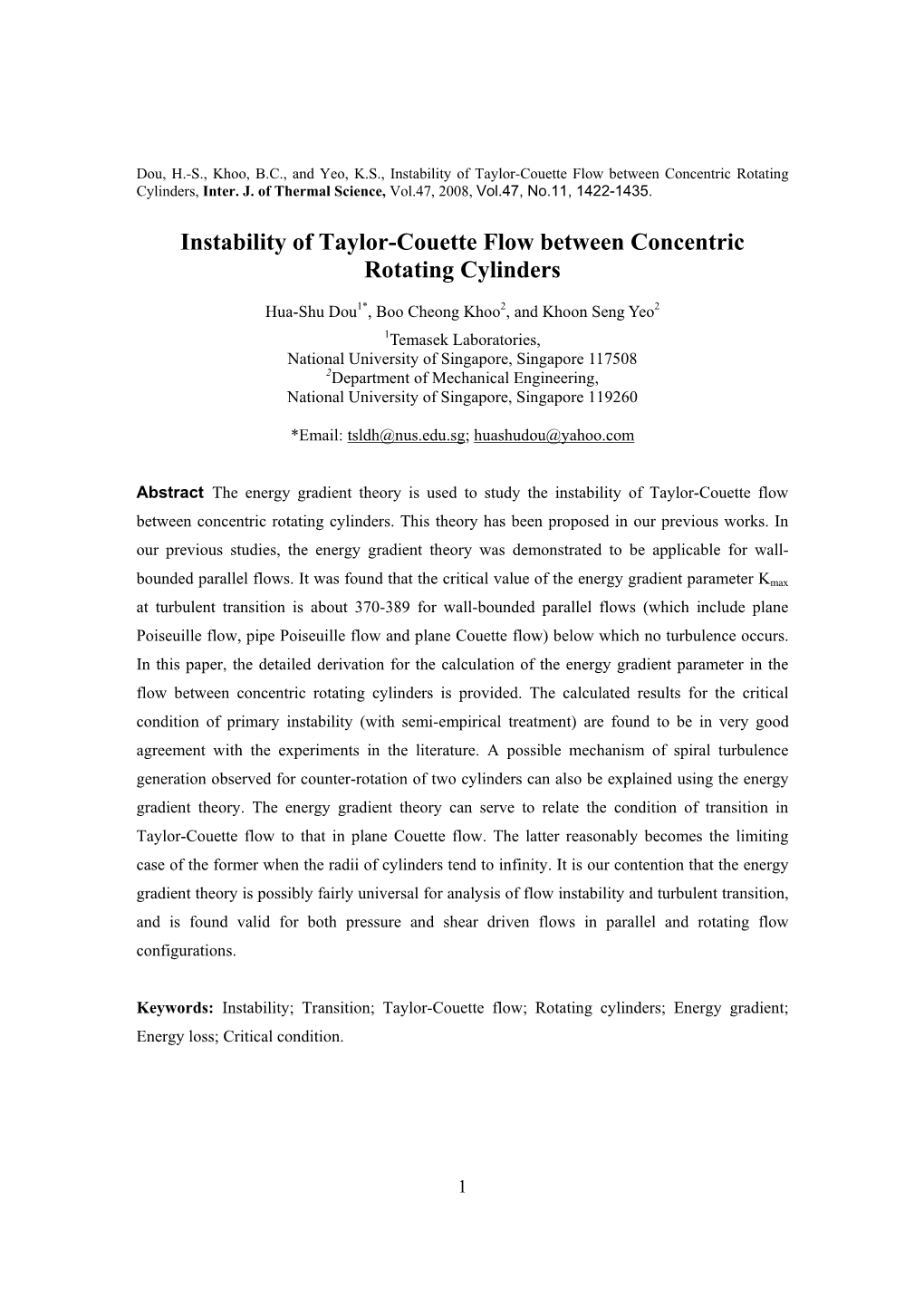
Load more
Recommended publications
-
Experimental and Numerical Characterization of the Thermal and Hydraulic Performance of a Canned Motor Pump Operating with Two-P
EXPERIMENTAL AND NUMERICAL CHARACTERIZATION OF THE THERMAL AND HYDRAULIC PERFORMANCE OF A CANNED MOTOR PUMP OPERATING WITH TWO-PHASE FLOW A Dissertation by YINTAO WANG Submitted to the Office of Graduate and Professional Studies of Texas A&M University in partial fulfillment of the requirements for the degree of DOCTOR OF PHILOSOPHY Chair of Committee, Adolfo Delgado Committee Members, Karen Vierow Kirkland Michael Pate Je-Chin Han Head of Department, Andreas A. Polycarpou May 2019 Major Subject: Mechanical Engineering Copyright 2019 Yintao Wang ABSTRACT Canned motor pump (CMP), as one kind of sealless pump, has been utilized in industry for many years to handle hazards or toxic product and to minimize leakage to the environment. In a canned motor pump, the impeller is directly mounted on the motor shaft and the pump bearing is usually cooled and lubricated by the pump process liquid. To be employed in oil field, CMP must have the ability to work under multiphase flow conditions, which is a common situation for artificial lift. In this study, we studied the performance and reliability of a vertical CMP from Curtiss-Wright Corporation in oil and air two-phase flow condition. Part of the process liquid in this CMP is recirculated to cool the motor and lubricate the thrust bearing. The pump went through varying flow rates and different gas volume fractions (GVFs). In the test, three important parameters, including the hydraulic performance, the pump inside temperature and the thrust bearing load were monitored, recorded and analyzed. The CMP has a second recirculation loop inside the pump to lubricate the thrust bearing as well as to cool down the motor windings. -
Friction Losses and Heat Transfer in High-Speed Electrical Machines
XK'Sj Friction losses and heat transfer in high-speed electrical machines Juha Saari DJSTR10UTK)N OF THI6 DOCUMENT IS UNLIMITED Teknillinen korkeakoulu Helsinki University of Technology Sahkotekniikan osasto Faculty of Electrical Engineering Sahkomekaniikan laboratorio Laboratory of Electromechanics Otaniemi 1996 1 50 2 Saari J. 1996. Friction losses and heat transfer in high-speed electrical machines. Helsinki University of Technology, Laboratory of Electromechanics, Report 50, Espoo, Finland, p. 34. Keywords: Friction loss, heat transfer, high-speed electrical machine Abstract High-speed electrical machines usually rotate between 20 000 and 100 000 rpm and the peripheral speed of the rotor exceeds 150 m/s. In addition to high power density, these figures mean high friction losses, especially in the air gap. In order to design good electrical machines, one should be able to predict accurately enough the friction losses and heat-transfer rates in the air gap. This report reviews earlier investigations concerning frictional drag and heat transfer between two concentric cylinders with inner cylinder. rotating. The aim was to find out whether these studies cover the operation range of high-speed electrical machines. Friction coefficients have been measured at very high Reynolds numbers. If the air-gap surfaces are smooth, the equations developed can be applied into high-speed machines. The effect of stator slots and axial cooling flows, however, should be studied in more detail. Heat-transfer rates from rotor and stator are controlled mainly by the Taylor vortices in the air-gap flow. Their appearance is affected by the flow rate of the cooling gas. The papers published do not cover flows with both high rotation speed and flow rate. -
Rayleigh-Bernard Convection Without Rotation and Magnetic Field
Nonlinear Convection of Electrically Conducting Fluid in a Rotating Magnetic System H.P. Rani Department of Mathematics, National Institute of Technology, Warangal. India. Y. Rameshwar Department of Mathematics, Osmania University, Hyderabad. India. J. Brestensky and Enrico Filippi Faculty of Mathematics, Physics, Informatics, Comenius University, Slovakia. Session: GD3.1 Core Dynamics Earth's core structure, dynamics and evolution: observations, models, experiments. Online EGU General Assembly May 2-8 2020 1 Abstract • Nonlinear analysis in a rotating Rayleigh-Bernard system of electrical conducting fluid is studied numerically in the presence of externally applied horizontal magnetic field with rigid-rigid boundary conditions. • This research model is also studied for stress free boundary conditions in the absence of Lorentz and Coriolis forces. • This DNS approach is carried near the onset of convection to study the flow behaviour in the limiting case of Prandtl number. • The fluid flow is visualized in terms of streamlines, limiting streamlines and isotherms. The dependence of Nusselt number on the Rayleigh number, Ekman number, Elasser number is examined. 2 Outline • Introduction • Physical model • Governing equations • Methodology • Validation – RBC – 2D – RBC – 3D • Results – RBC – RBC with magnetic field (MC) – Plane layer dynamo (RMC) 3 Introduction • Nonlinear interaction between convection and magnetic fields (Magnetoconvection) may explain certain prominent features on the solar surface. • Yet we are far from a real understanding of the dynamical coupling between convection and magnetic fields in stars and magnetically confined high-temperature plasmas etc. Therefore it is of great importance to understand how energy transport and convection are affected by an imposed magnetic field: i.e., how the Lorentz force affects convection patterns in sunspots and magnetically confined, high-temperature plasmas. -
A Numerical and Experimental Investigation of Taylor Flow Instabilities in Narrow Gaps and Their Relationship to Turbulent Flow
A NUMERICAL AND EXPERIMENTAL INVESTIGATION OF TAYLOR FLOW INSTABILITIES IN NARROW GAPS AND THEIR RELATIONSHIP TO TURBULENT FLOW IN BEARINGS A Dissertation Presented to The Graduate Faculty of The University of Akron In Partial Fulfillment of the Requirements for the Degree Doctor of Philosophy Dingfeng Deng August, 2007 A NUMERICAL AND EXPERIMENTAL INVESTIGATION OF TAYLOR FLOW INSTABILITIES IN NARROW GAPS AND THEIR RELATIONSHIP TO TURBULENT FLOW IN BEARINGS Dingfeng Deng Dissertation Approved: Accepted: _______________________________ _______________________________ Advisor Department Chair Dr. M. J. Braun Dr. C. Batur _______________________________ _______________________________ Committee Member Dean of the College Dr. J. Drummond Dr. G. K. Haritos _______________________________ _______________________________ Committee Member Dean of the Graduate School Dr. S. I. Hariharan Dr. G. R. Newkome _______________________________ _______________________________ Committee Member Date R. C. Hendricks _______________________________ Committee Member Dr. A. Povitsky _______________________________ Committee Member Dr. G. Young ii ABSTRACT The relationship between the onset of Taylor instability and appearance of what is commonly known as “turbulence” in narrow gaps between two cylinders is investigated. A question open to debate is whether the flow formations observed during Taylor instability regimes are, or are related to the actual “turbulence” as it is presently modeled in micro-scale clearance flows. This question is approached by considering the viscous fluid flow in narrow gaps between two cylinders with various eccentricity ratios. The computational engine is provided by CFD-ACE+, a commercial multi-physics software. The flow patterns, velocity profiles and torques on the outer cylinder are determined when the speed of the inner cylinder, clearance and eccentricity ratio are changed on a parametric basis. -
Simulation of Taylor-Couette Flow. Part 2. Numerical Results for Wavy-Vortex Flow with One Travelling Wave
J. E’l~idM(&. (1984),FOI. 146, pp. 65-113 65 Printed in Chat Britain Simulation of Taylor-Couette flow. Part 2. Numerical results for wavy-vortex flow with one travelling wave By PHILIP S. MARCUS Division of Applied Sciences and Department of Astronomy, Harvard University (Received 26 July 1983 and in revised form 23 March 1984) We use a numerical method that was described in Part 1 (Marcus 1984a) to solve the time-dependent Navier-Stokes equation and boundary conditions that govern Taylor-Couette flow. We compute several stable axisymmetric Taylor-vortex equi- libria and several stable non-axisymmetric wavy-vortex flows that correspond to one travelling wave. For each flow we compute the energy, angular momentum, torque, wave speed, energy dissipation rate, enstrophy, and energy and enstrophy spectra. We also plot several 2-dimensional projections of the velocity field. Using the results of the numerical calculations, we conjecture that the travelling waves are a secondary instability caused by the strong radial motion in the outflow boundaries of the Taylor vortices and are not shear instabilities associated with inflection points of the azimuthal flow. We demonstrate numerically that, at the critical Reynolds number where Taylor-vortex flow becomes unstable to wavy-vortex flow, the speed of the travelling wave is equal to the azimuthal angular velocity of the fluid at the centre of the Taylor vortices. For Reynolds numbers larger than the critical value, the travelling waves have their maximum amplitude at the comoving surface, where the comoving surface is defined to be the surface of fluid that has the same azimuthal velocity as the velocity of the travelling wave. -
Numerical Modeling of Fluid Flow and Heat Transfer in a Narrow Taylor-Couette-Poiseuille System
Numerical modeling of fluid flow and heat transfer ina narrow Taylor-Couette-Poiseuille system Sébastien Poncet, Sofia Haddadi, Stéphane Viazzo To cite this version: Sébastien Poncet, Sofia Haddadi, Stéphane Viazzo. Numerical modeling of fluid flow and heat transfer in a narrow Taylor-Couette-Poiseuille system. International Journal of Heat and Fluid Flow, Elsevier, 2010, 32, pp.128-144. 10.1016/j.ijheatfluidflow.2010.08.003. hal-00678877 HAL Id: hal-00678877 https://hal.archives-ouvertes.fr/hal-00678877 Submitted on 14 Mar 2012 HAL is a multi-disciplinary open access L’archive ouverte pluridisciplinaire HAL, est archive for the deposit and dissemination of sci- destinée au dépôt et à la diffusion de documents entific research documents, whether they are pub- scientifiques de niveau recherche, publiés ou non, lished or not. The documents may come from émanant des établissements d’enseignement et de teaching and research institutions in France or recherche français ou étrangers, des laboratoires abroad, or from public or private research centers. publics ou privés. Numerical modeling of fluid flow and heat transfer in a narrow Taylor-Couette-Poiseuille system S¶ebastienPoncet,¤ So¯a Haddadi,y and St¶ephaneViazzoz Laboratoire M2P2, UMR 6181 CNRS - Universit¶ed'Aix-Marseille - Ecole Centrale Marseille, IMT la Jet¶ee,38 rue Joliot-Curie, 13451 Marseille (France) (Dated: February 17, 2010) We consider turbulent flows in a di®erentially heated Taylor-Couette system with an axial Poiseuille flow. The numerical approach is based on the Reynolds Stress Modeling (RSM) of Elena and Schiestel [1, 2] widely validated in various rotor-stator cavities with throughflow [3{5] and heat transfer [6]. -
Evaluation of the Cavitation Effect on Liquid Fuel Atomization by Numerical Simulation
Korean J. Chem. Eng., 35(11), 2164-2171 (2018) pISSN: 0256-1115 DOI: 10.1007/s11814-018-0141-6 eISSN: 1975-7220 INVITED REVIEW PAPER INVITED REVIEW PAPER Evaluation of the cavitation effect on liquid fuel atomization by numerical simulation Sang In Choi*, Jia Ping Feng*, Ho Suk Seo**, Young Min Jo*,†, and Hyun Chang Lee*** *Department of Applied Environmental Science, Kyung Hee University, Yongin 17104, Korea **EG Power Tech Co., Ltd., Suwon 16229, Korea ***Dept. of Mechanical Design, Kangwon National University, Samcheok 25913, Korea (Received 16 February 2018 • accepted 16 August 2018) AbstractHeavy duty diesel vehicles deteriorate urban air quality by discharging a large volume of air pollutants such as soot and nitrogen oxides. In this study, a newly introduced auxiliary device a fuel activation device (FAD) to improve the combustion efficiency of internal engines by utilizing the cavitation effect was closely investigated by the fluid flow mechanism via a numerical analysis method. As a result, the FAD contributed to fuel atomization from the injection nozzle at lower inlet pressure by reducing the pressure energy. The improved cavitation effect facilitated fuel atomization, and ultimately reduced pollutant emission due to the decrease in fuel consumption. The axial velocity along the flow channel was increased 8.7 times with the aid of FAD, which improved the primary break-up of bubbles. The FAD cavitation effect produced 1.09-times larger turbulent bubbles under the same pressure and fuel injection amount than without FAD. Keywords: Diesel Engine, Fuel Activation Device, Cavitation, Cavitation Number, CFD INTRODUCTION was determined by an atomization effect. The smaller the droplets, the total number of droplets increases. -
University of Nevada, Reno a Dissertation Submitted in Partial Fulfillment of the Requirements for the Degree of Doctor of Philo
University of Nevada, Reno Computational Investigation of Cavitation Performance and Heat Transfer in Cryogenic Centrifugal Pumps with Helical Inducers A dissertation submitted in partial fulfillment of the requirements for the degree of Doctor of Philosophy in Mechanical Engineering by Enver Sinan Karakas Dr. Cahit A. Evrensel/Dissertation Advisor May, 2019 THE GRADUATE SCHOOL We recommend that the dissertation prepared under our supervision by Entitled be accepted in partial fulfillment of the requirements for the degree of , Advisor , Committee Member , Comm ittee Member , Committee Member , Graduate School Representative David W. Zeh, Ph.D., Dean, Graduate School i i. ABSTRACT In this dissertation, heat transfer and cooling mechanism of a cryogenic submerged pump motor, and cavitation behavior of a cryogenic pump are investigated. Cryogenic pumps for Liquefied Natural Gas (LNG) applications are unique in design with respect other industrial pump applications. The two distinct features of the cryogenic pumps are: (1) pump motor is submerged to process liquid for improved cooling, and (2) a helical style inducer is utilized at the suction side of the pump to enhance the cavitation performance. The first part of this dissertation investigates the cooling of the submerged induction motor considering normal operating conditions of a typical cryogenic pump to understand the effect of the motor rotor geometry. In this effort, the flow structure across the motor annulus, which is commonly known as “motor air gap”, is investigated in the presence of realistic rotor geometries commonly found in practical applications. The purpose of this study is to observe and understand the fluid dynamics of Taylor-Couette-Poiseuille (TCP) flow and its significance to the cooling performance of the submerged motor, considering various configurations of the rotor surface. -
Experiments on Rayleigh–Bénard Convection, Magnetoconvection
J. Fluid Mech. (2001), vol. 430, pp. 283–307. Printed in the United Kingdom 283 c 2001 Cambridge University Press Experiments on Rayleigh–Benard´ convection, magnetoconvection and rotating magnetoconvection in liquid gallium By J. M. AURNOU AND P. L. OLSON Department of Earth and Planetary Sciences,† Johns Hopkins University, Baltimore, MD 21218, USA (Received 4 March 1999 and in revised form 12 September 2000) Thermal convection experiments in a liquid gallium layer subject to a uniform rotation and a uniform vertical magnetic field are carried out as a function of rotation rate and magnetic field strength. Our purpose is to measure heat transfer in a low-Prandtl-number (Pr =0.023), electrically conducting fluid as a function of the applied temperature difference, rotation rate, applied magnetic field strength and fluid-layer aspect ratio. For Rayleigh–Benard´ (non-rotating, non-magnetic) convection 0.272 0.006 we obtain a Nusselt number–Rayleigh number law Nu =0.129Ra ± over the range 3.0 103 <Ra<1.6 104. For non-rotating magnetoconvection, we find that the critical× Rayleigh number× RaC increases linearly with magnetic energy density, and a heat transfer law of the form Nu Ra1/2. Coherent thermal oscillations are detected in magnetoconvection at 1.4Ra∼C . For rotating magnetoconvection, we find that the convective heat transfer is∼ inhibited by rotation, in general agreement with theoretical predictions. At low rotation rates, the critical Rayleigh number increases linearly with magnetic field intensity. At moderate rotation rates, coherent thermal oscillations are detected near the onset of convection. The oscillation frequencies are close to the frequency of rotation, indicating inertially driven, oscillatory convection. -
Rotating Cylinders, Annuli, and Spheres
Chapter 6 Rotating Cylinders, Annuli, and Spheres Flow over rotating cylinders is important in a wide number of applications from shafts and axles to spinning projectiles. Also considered here is the flow in an annulus formed between two concentric cylinders where one or both of the cylindrical surfaces is or are rotating. As with the rotating flow associated with discs, the proximity of a surface can significantly alter the flow structure. 6.1. INTRODUCTION An indication of the typical flow configurations associated with rotating cylin ders and for an annulus with surface rotation is given in Figure 6.1. For the examples given in 6.1a, 6.1c, 6.1e, 6.1g, and 6.1i, a superposed axial flow is possible, resulting typically in a skewed, helical flow structure. This chapter describes the principal flow phenomena, and develops and presents methods to determine parameters such as the drag associated with a rotating cylinder and local flow velocities. Flow for a rotating cylinder is considered in Section 6.2. Laminar flow between two rotating concentric cylinders, known as rotating Couette flow, is considered in Section 6.3. Rota tion of annular surfaces can lead to instabilities in the flow and the formation of complex toroidal vortices, known, for certain flow conditions, as Taylor vor tices. Taylor vortex flow represents a significant modeling challenge and has been subject to a vast number of scientific studies. The relevance of these to practical applications stems from the requirement to avoid Taylor vortex flow, the requirement to determine or alter fluid residence time in chemical proces sing applications, and the desire to understand fluid flow physics and develop and validate fluid flow models. -
Effects of Brinkman Number on Thermal-Driven Convective Spherical Dynamos
March 2013 JASEM ISSN 1119-8362 Full-text Available Online at J. Appl. Sci. Environ. Manage. All rights reserved www.ajol.info and Vol. 17 (1) 139-151 www.bioline.org.br/ja Effects of Brinkman number on thermal-driven convective spherical Dynamos . *1M. I. NGWUEKE; T. M. ABBEY Theoretical Physics Group; Department of Physics, University of Port Harcourt, Port Harcourt, Nigeria. *Corresponding author (e-mail: [email protected]; Phone: 234-703-5891392, 234-803-3409479 ) KEYWORDS: Magnetic field generation, Thermal-driven convection, Brinkman number, Dynamo action, Fluid outer core ABSTRACT: Brinkman number effects on the thermal-driven convective spherical dynamos are studied analytically. The high temperature of the Earth’s inner core boundary is usually conducted by the viscous, electrically conducting fluid of the outer core to the core mantle boundary as the Earth cools. The problem considers conducting fluid motion in a rapidly rotating spherical shell. The consequence of this exponential dependence of viscosity on temperature is considered to be a thermal- driven convective phenomenon. A set of constitutive non-linear equations were then formulated in which the solutions for the flow variables were obtained by perturbation technique. The results illustrate enhancement of dynamo actions, demonstrating that magnetic field generation with time is possible. Moreover, the increased magnetic Prandtl number Pm with high Brinkman number shows dynamo actions for fixed Rayleigh and Taylor number values. The overall analyses succour our -
Instability Theory of Swirling Flows with Suction (Pdf)
Instability theory of swirling flows with suction Basile GALLET, supervised by C.Doering and E.Spiegel August 24, 2007 1 Introduction Accretion disks radiate a tremendous amount of energy. In these systems the only source of energy is gravitational energy. Turbulence in the disk converts this gravitational energy into heat and finally radiation. During this process the angular momentum of the fluid is carried out by turbulent transport, which allows accretion of the fluid onto the central object. Without turbulence the angular momentum would not be carried out efficientely enough and the accretion rate would be extremely low. The velocity profile of an accretion disk is considered to be mostly Keplerian, and the accretion rate is quite low, which means that the motion of the fluid inside the disk is almost circular. However, circular Keplerian flows are known to be linearly stable and one may wonder how turbulence is generated in such a system. If the magnetic field inside the disk is high enough, it has been shown that the magnetorotational instability (MRI) can destabilize the flow and produce turbulence [3]. This provides at least one mechanism to drive turbulence in accretion disks. However, it has been shown that the MRI may be suppressed if the magnetic Prandtl number (ratio of the viscosity over the magnetic viscosity) is not high enough. In cold proptoplanetary nebulas for instance, the ionization is too low and one has to find another way to destabilize the flow than the MRI. This is one of our main motivations to study the combined effects of both rotation and accretion on a very simple flow : the Taylor-Couette flow with inward suction.