Application of Vacuum Arc Melting Techniques
Total Page:16
File Type:pdf, Size:1020Kb
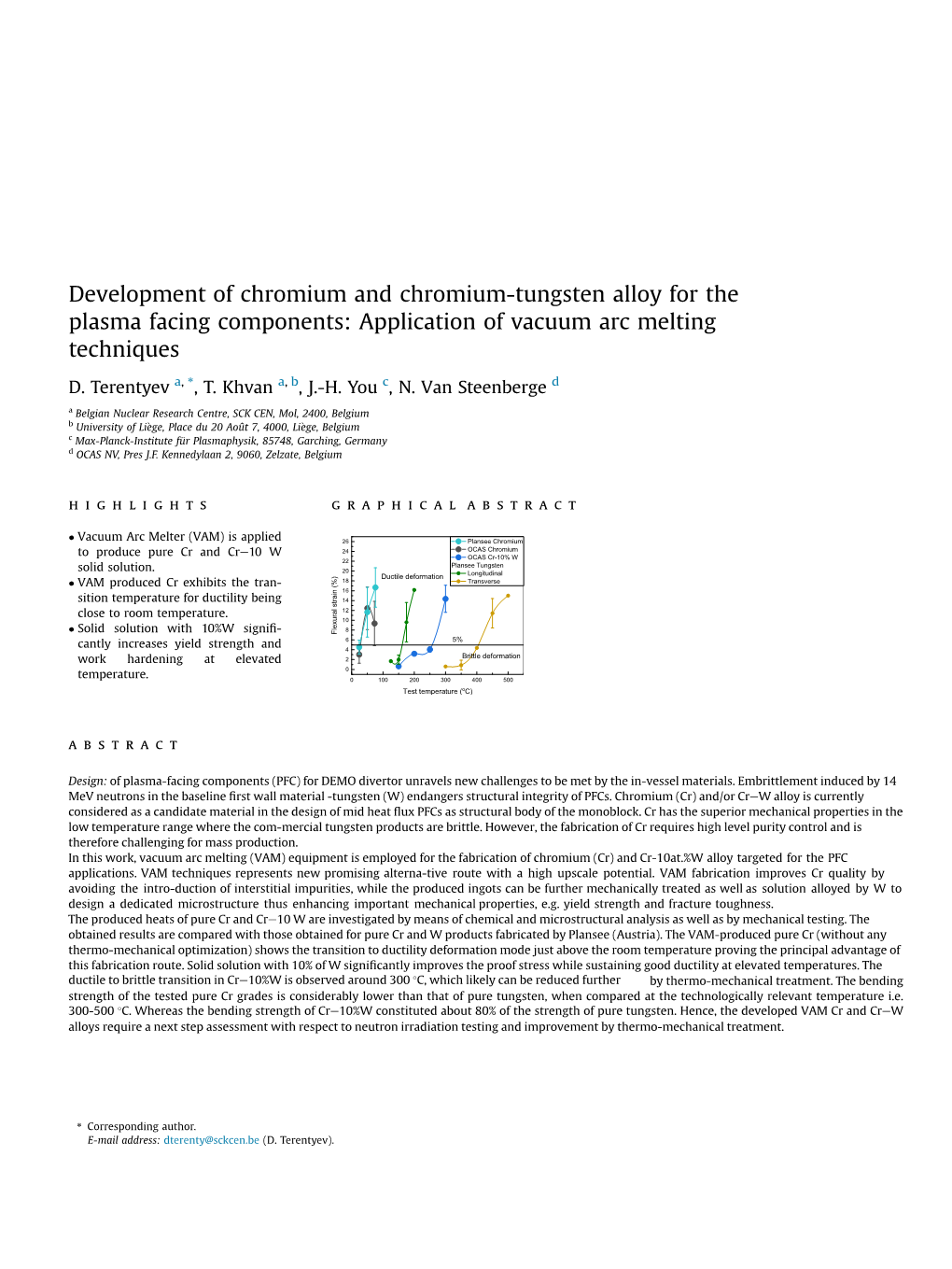
Load more
Recommended publications
-
Brinell Hardness Testing Methods and Their Applicability
2020 AFS Proceedings of the 124th Metalcasting Congress Paper 2020-012 (10 pages) Brinell Hardness Testing Methods and Their Applicability Devin R. Hess, Ph.D., General Motors Engine Materials Engineer, Pontiac, Michigan Herbert W. Doty, Ph.D. General Motors Materials Technology, Pontiac, Michigan Copyright 2020 American Foundry Society ABSTRACT test, better known as the Product A, was introduced in 1975.4 The Leeb test is a form of the scleroscope test. Hardness is one of the most commonly specified requirements on automotive propulsion system One definition of hardness is a materials resistance to engineering drawings. It is used as a process control indentation. This is typically determined by measuring the check and as a proxy for strength, wear resistance, and permanent depth or diameter of the indentation left by the machinability. It is commonly assumed harder means testing method. The resulting hardness value depends on stronger, and while this is generally true, what are we the Product And the test parameters being used. Hardness really controlling when we measure hardness? Depending therefore is not a fundamental physical property of a on the material and the manufacturing process, hardness material. Thus, it is critical that the Product A parameters can be used to verify that the material has been exposed to be clearly defined when specifying or reporting a the appropriate thermal conditions and that the proper hardness value. One concern that often arises is how to microstructure is present. compare hardness values obtained from different test methods. This paper explores some of the issues that can arise when trying to compare between different scales within a given HARDNESS TEST METHODS REVIEWED IN THIS Product And when trying to convert from one test method PAPER to another and offers some rationale for these limitations. -
Rockwell Hardness Lab Report
Rockwell Hardness Lab Report th By Group-II (6 S emester) Department of Metallurgy and Materials Engineering, Indian Institute of Engineering Science and Technology (IIEST), Shibpur 711103, West Bengal, India Group-II Lab Members 1. Animesh Das (511117017) 2. Bhaskarjyoti Das (511117018) 3. Priyanshu Gupta (511117020) 4. Angothu Mohan (511117022) 5. Faraz Ahmed (511117024) 6. Rohit Kumar Mahato (511117026) 7. Shuvannita Dey (511117030) 8. Souradeep Ghosh (511117032) 9. Nitish Kumar (511117034) 10. Shailendra Singh (511117035) 11. Adarsh Kumar Singh (511117038) 12. Md. Farhan (511117040) 13. Yogesh Verma (511117041) Introduction Hardness can be defined as the resistance of material to local plastic deformation on the application of some external load or stress (scratch, indentation or abrasion). Although hardness is not a fundamental property of material, hardness testing is widely used in industries because of its simplicity, faster results, near NDT testing properties, cheap procedure and many more advantages. Also, it can give a qualitative relationship to other materials properties like strength, ductility, rigidity etc. Indentation test is one of the prominently used hardness testing method where we apply a certain predefined load with the help of an indenter which penetrates into the sample surface; thus we get the hardness values by measuring the indentation depth or size of the projected indentation area. Rockwell hardness test is one of the static hardness testing methods using indentation depth as a measuring criterion. Basically, two types of indenter are used; one Diamond O spheroconical (Brale) indenter with an angle of 120 and a spherical tip of 0.2mm; second is steel ball indenter with diameters as 1/16, 1/8, 1/4, ½ inches. -
Performing a Rockwell Test Consists In
PRACTICAL HARDNESS TESTING MADE SIMPLE Table of Contents Page 1. GENERAL 1 2. INTRODUCTION 3 3. BRINELL HARDNESS TESTING 9 4. VICKERS HARDNESS TESTING 14 5. ROCKWELL HARDNESS TESTING 17 6. INFORMATIONS 22 i PRACTICAL HARDNESS TESTING MADE SIMPLE 1. GENERAL Important facts and features to be known and remembered. This booklet intends to stress the significance of Hardness Testing and to dispel a few common misconceptions attributing to it inappropriate meanings and implications. It is dedicated to all people using Hardness Testing in their daily work, for them to be aware of the usefulness of the methods, when applied correctly, and of the dangers of faulty generalisations, if interpreted outside the frame of their relevance. It may also be useful for students learning to practice Hardness Testing, to orient them in the understanding of a broader meaning of the results collected. The information appearing in the following pages can be found in the best Handbooks dealing with the subject matter. As these may or may not be readily available to the interested persons, the material included is presented here following the personal experience and preference of the writer. Note: the information, given herewith in good faith for enlarging the understanding of quite common a testing, is believed to be correct at the time of this writing, fruit of longtime practice with actual operations in an industrial environment. 1 PRACTICAL HARDNESS TESTING MADE SIMPLE Nothing written here though should be construed as authority to use the results for reaching conclusions bearing direct influence on possible harming of people or loss of material gain. -
Microstructural and Micromechanical Tests of Titanium Biomaterials Intended for Prosthetic Reconstructions
Acta of Bioengineering and Biomechanics Original paper Vol. 18, No. 1, 2016 DOI: 10.5277/ABB-00193-2014-02 Microstructural and micromechanical tests of titanium biomaterials intended for prosthetic reconstructions ANNA M. RYNIEWICZ1*, ŁUKASZ BOJKO1, WOJCIECH I. RYNIEWICZ2 1 AGH University of Science and Technology, Faculty of Mechanical Engineering and Robotics, Kraków, Poland. 2 Jagiellonian University Medical College, Faculty of Medicine, Department of Prosthetic Dentistry, Kraków, Poland. Purpose: The aim of the present paper was a question of structural identification and evaluation of strength parameters of Titanium (Ticp – grade 2) and its alloy (Ti6Al4V) which are used to serve as a base for those permanent prosthetic supplements which are later manufactured employing CAD/CAM systems. Methods: Microstructural tests of Ticp and Ti6Al4V were conducted using an optical microscope as well as a scanning microscope. Hardness was measured with the Vickers method. Micromechanical properties of samples: microhardness and Young’s modulus value, were measured with the Oliver and Pharr method. Results: Based on studies using optical microscopy it was observed that the Ticp from the milling technology had a single phase, granular microstructure. The Ti64 alloy had a two-phase, fine-grained microstructure with an acicular-lamellar character. The results of scanning tests show that titanium Ticp had a single phase structure. On its grain there was visible acicular martensite. The structure of the two phase Ti64 alloy consists of a matrix as well as released phase deposits in the shape of extended needles. Micromechanical tests demonstrated that the alloy of Ti64 in both methods showed twice as high the microhardness as Ticp. -
Enghandbook.Pdf
785.392.3017 FAX 785.392.2845 Box 232, Exit 49 G.L. Huyett Expy Minneapolis, KS 67467 ENGINEERING HANDBOOK TECHNICAL INFORMATION STEELMAKING Basic descriptions of making carbon, alloy, stainless, and tool steel p. 4. METALS & ALLOYS Carbon grades, types, and numbering systems; glossary p. 13. Identification factors and composition standards p. 27. CHEMICAL CONTENT This document and the information contained herein is not Quenching, hardening, and other thermal modifications p. 30. HEAT TREATMENT a design standard, design guide or otherwise, but is here TESTING THE HARDNESS OF METALS Types and comparisons; glossary p. 34. solely for the convenience of our customers. For more Comparisons of ductility, stresses; glossary p.41. design assistance MECHANICAL PROPERTIES OF METAL contact our plant or consult the Machinery G.L. Huyett’s distinct capabilities; glossary p. 53. Handbook, published MANUFACTURING PROCESSES by Industrial Press Inc., New York. COATING, PLATING & THE COLORING OF METALS Finishes p. 81. CONVERSION CHARTS Imperial and metric p. 84. 1 TABLE OF CONTENTS Introduction 3 Steelmaking 4 Metals and Alloys 13 Designations for Chemical Content 27 Designations for Heat Treatment 30 Testing the Hardness of Metals 34 Mechanical Properties of Metal 41 Manufacturing Processes 53 Manufacturing Glossary 57 Conversion Coating, Plating, and the Coloring of Metals 81 Conversion Charts 84 Links and Related Sites 89 Index 90 Box 232 • Exit 49 G.L. Huyett Expressway • Minneapolis, Kansas 67467 785-392-3017 • Fax 785-392-2845 • [email protected] • www.huyett.com INTRODUCTION & ACKNOWLEDGMENTS This document was created based on research and experience of Huyett staff. Invaluable technical information, including statistical data contained in the tables, is from the 26th Edition Machinery Handbook, copyrighted and published in 2000 by Industrial Press, Inc. -
Mechanical Properties of Surface Nitrided Titanium for Abrasion Resistant Implant Materials
Materials Transactions, Vol. 43, No. 12 (2002) pp. 3043 to 3051 Special Issuse on Biomaterials and Bioengineering c 2002 The Japan Institute of Metals Mechanical Properties of Surface Nitrided Titanium for Abrasion Resistant Implant Materials Yutaka Tamura1, ∗, Atsuro Yokoyama1, Fumio Watari2, Motohiro Uo2 and Takao Kawasaki1 1Removable Prosthodontics and Stomatognathostatic Rehabilitation, Department of Oral Functional Science, Graduate School of Dental Medicine, Hokkaido University, Sapporo 060-8586, Japan 2Dental Materials and Engineering, Department of Oral Health Science, Graduate School of Dental Medicine, Hokkaido University, Sapporo 060-8586, Japan In order to verify its application for abrasion-resistant implant materials such as abutment in dental implants and artificial joints, mechan- ical properties of surface nitrided titanium were evaluated by three different tests, the Vickers hardness test, Martens scratch test and ultrasonic scaler abrasion test. The Vickers hardness of a nitrided layer of 2 µm in the thickness was 1300, about ten times higher than that of pure tita- nium. The Martens scratch test showed high bonding strength for the nitrided layer with matrix titanium. The abrasion test using an ultrasonic scaler showed very small scratch depth and width, demonstrating extremely high abrasion resistance. The results show that a surface-nitrided titanium has sufficient abrasion resistance if it is used under clinical conditions. (Received August 5, 2002; Accepted October 28, 2002) Keywords: biomaterial, implant, titanium, surface reforming, titanium nitride, abrasion resistance, hardness 1. Introduction 2. Materials and Experimental Methods Titanium is the most commonly used as an implant mate- 2.1 Sample preparation rial at present. Its surface has a passive film formed in stable JIS type 1 pure titanium plates (10 × 10 × 0.5 mm: KOBE oxides working for biocompatibility under the severe environ- STEEL LTD, Kobe, Japan) were used as specimens. -
Hardness Measurement of Copper Bonding Wire
Available online at www.sciencedirect.com ScienceDirect Procedia Engineering 75 ( 2014 ) 134 – 139 MRS Singapore - ICMAT Symposia Proceedings Synthesis, Processing and Characterization III Hardness Measurement of Copper Bonding Wire Johnny Yeunga, Loke Chee Keonga aHeraeus Materials Singapore Pte Ltd, Block 5002, Ang Mo Kio Ave 5, #04-07, Singapore 569871 Abstract In semiconductor packaging industry, thin metal bonding wires, such as gold and copper, in the diameter range of 18 to 25 microns, are commonly used to connect between IC chip and connector pins through thermosonic and ultrasonic welding (bonding) in various types of packages. Copper bonding wire posts great challenges to industry users when they need to bond it onto IC bond pad of sensitive construction underneath. Any hard impact due to the material property, i.e. hardness, or excess ultrasonic parameter setting in the bonding process can easily cause the pad to crack. It is therefore of interest to the users on how hard the copper wire is and most importantly, the subsequent solidified molten ball as a result of melting the tip of the wire in the process. A Vickers micro-indentation hardness tester with minimum load of 0.5 gmf (5mN) capability is used to measure the hardness of copper wire along its length and in the free air ball (FAB). To determine the suitable load to be used to measure hardness of such fine diameter and minimize variation in the measured results due to different sample preparation effects, a range of load from 1 gmf to less than 50 gmf was studied. © 2013 TheThe Authors. -
Indentation Hardness Measurements at Macro-, Micro-, and Nanoscale: a Critical Overview
Tribol Lett (2017) 65:23 DOI 10.1007/s11249-016-0805-5 REVIEW Indentation Hardness Measurements at Macro-, Micro-, and Nanoscale: A Critical Overview Esteban Broitman1 Received: 25 September 2016 / Accepted: 15 December 2016 / Published online: 28 December 2016 Ó The Author(s) 2016. This article is published with open access at Springerlink.com Abstract The Brinell, Vickers, Meyer, Rockwell, Shore, 1 Introduction IHRD, Knoop, Buchholz, and nanoindentation methods used to measure the indentation hardness of materials at The hardness of a solid material can be defined as a mea- different scales are compared, and main issues and mis- sure of its resistance to a permanent shape change when a conceptions in the understanding of these methods are constant compressive force is applied. The deformation can comprehensively reviewed and discussed. Basic equations be produced by different mechanisms, like indentation, and parameters employed to calculate hardness are clearly scratching, cutting, mechanical wear, or bending. In metals, explained, and the different international standards for each ceramics, and most of polymers, the hardness is related to method are summarized. The limits for each scale are the plastic deformation of the surface. Hardness has also a explored, and the different forms to calculate hardness in close relation to other mechanical properties like strength, each method are compared and established. The influence ductility, and fatigue resistance, and therefore, hardness of elasticity and plasticity of the material in each mea- testing can be used in the industry as a simple, fast, and surement method is reviewed, and the impact of the surface relatively cheap material quality control method. -
Me 212 Laboratory Experiment #3 Hardness Testing And
ME 212 LABORATORY EXPERIMENT #3 HARDNESS TESTING AND AGE HARDENING 1. OBJECTIVE Our primary aim is to measure the Rockwell Hardness values of materials and estimate ultimate tensile strengths by the aid of conversion tables. We will also focus on age hardening, the info on which can be found in the last part of this experiment sheet. 2. HARDNESS TESTING THEORY Hardness is usually defined as the resistance of a material to plastic penetration of its surface. There are three main types of tests used to determine hardness: • Scratch tests are the simplest form of hardness tests. In this test, various materials are rated on their ability to scratch one another. Mohs hardness test is of this type. This test is used mainly in mineralogy. • In Dynamic Hardness tests, an object of standard mass and dimensions is bounced back from a surface after falling by its own weight. The height of the rebound is indicated. Shore hardness is measured by this method. • Static Indentation tests are based on the relation of indentation of the specimen by a penetrator under a given load. The relationship of total test force to the area or depth of indentation provides a measure of hardness. The Rockwell, Brinell, Knoop, Vickers, and ultrasonic hardness tests are of this type. For engineering purposes, mostly the static indentation tests are used. BRINELL HARDNESS TEST: This test consists of applying a constant load, usually between 500 and 3000 kgf for a specified time (10 to 30 s) using a 5 or 10-mm diameter hardened steel or tungsten carbide ball on the flat surface of a workpiece. -
Rockwell Hardness Testing Symbols and Definitions
No.E17004 Hardness Testing ISO 6508-1 Rockwell Hardness Test -- Test Method ISO 6507-1 Vickers Hardness Test -- Test Method ISO 6506-1 Brinell Hardness Test --Test Method Rockwell Hardness Test ISO6508-1 JIS Z 2245 Hardness Test Methods and Applications Brinell Hardness Test ISO6506-1 JIS Z 2243 Calculation Formulae Rockwell Hardness Scales Rockwell Superficial Hardness Scales Special heat treatment, thin coating, surface- Calculation Formulae Minimum Allowable Indentation Spacing Rockwell scales = − h Hardness Test Method F 2F HR 100 modification layer, elastic material, etc. HBW = k = 0.102 A/C/D 0.002 Preliminary test force 98.07N Preliminary test force 29.42N 2 2 (example: titanium system coating, DLC treatment, S πD(D − D − d ) Rockwell scales h ■ Often-used range HR = 130 − Scale Indenter Test force (N) Application Scale Indenter Test force (N) Application semiconductor-field material) k = Constant. F = Test force (N). S = Surface area of indentation. B/E/F/G/H/K 0.002 D = Diameter of the ball (mm). Rockwell Superficial scales h A 588.4 HRA: Tungsten carbide and thin 15N 147.1 Instrumented Indentation Test (IIT) d = Arithmetic mean (mm) of the indentation diameters 3d or more 2.5d or more HR = 100 − (Commonly known as "Nanoindentation" - measured at 90°(d1, d2). N/T 0.001 ** age-hardening steel or thinner ** D 2 2 D Diamond 980.7 30N Diamond 294.2 IIT specimen thickness: approx. 10µm or less) h = Depth of indentation. h = (1− 1− d / D ) h = Permanent indentation depth (mm). surface layer than is HRC testable. 2 h1 = Indentation depth produced by the preliminary test force. -
Appendix 2: HARDNESS QUESTIONNAIRE
NPL REPORT CMAM 69 Results of a survey of the priorities for an increased range of UK traceable hardness scales Francis Davis August 2001 CMAM 69 August 2001 Results of a survey of the priorities for an increased range of UK traceable hardness scales Francis Davis Centre for Mechanical and Acoustical Metrology National Physical Laboratory Queens Road Teddington Middlesex TW11 0LW Abstract As part of the 1996-1999 NMS mass metrology programme, a project was launched to re- establish hardness standards for the highest priority scales. A consultative document published, in support of this re-establishment, stated that the scales supported were considered a minimum requirement, and that the future mass metrology programmes should reflect the need for an increased range of national traceable hardness scales. This report has been written as part of deliverable 2.3.3 of the NMS mass metrology programme 1999 – 2002, “to establish the priorities for an increased range of hardness scales”. These priorities were derived from the analysis of a survey of both manufacturers and users of hardness equipment. The survey was carried out during June - August 2001 and circulated to the UK hardness community by use of the distribution lists of the BSI hardness committee (ISE/NFE/4/5), BMTA members, UKAS-accredited hardness laboratories, the NPL MATC Materials Measurement flyer, and the NPL Force and Hardness Group. The survey covers traditional indentation hardness methods, rubber hardness, and the instrumented indentation method for hardness and material properties. Provided as appendices to this report are background notes on hardness scales, the questionnaire that was circulated, and a list of the organisations that responded. -
Hardness Testing Machines
HARDNESS TESTING MACHINES HM/HV/HR/HH SERIES TEST EQUIPMENT AND SEISMOMETERS PRE1442 HARDNESS TESTING MACHINES CONTENTS Page Page Rockwell Hardness testing machines Introduction 4 29 HR-500 Series 5 Hardness testing machines lineup 30 Touch panel display and function Types of hardness and selection criteria for hardness Specifications/Standard accessories/Optional accessories 6 testing machines 31 Micro Vickers hardness testing machines: Optional accessories 8 HM-200 Series 32 Vickers hardness testing machines Data processing software 9 HV-100 Series 34 for hardness testing machines Micro Vickers hardness testing machines system Portable hardness tester 10 configuration 36 Hardmatic HH Series Vickers hardness testing machines system Rebound type portable hardness tester 11 configuration 38 Hardmatic HH-411 AVPAK-20 software functions for 12 controlling B/C/D-Type systems 39 Specifications/Standard accessories/Optional accessories Durometers for sponges, rubber and plastics Touch-panel display and function for System A 15 40 Hardmatic HH-300 Series 16 Outline drawings 42 Specifications 17 Specifications 43 Optional accessories Examples of hardness measurement Micro-Vickers and Vickers Sets 20 44 performance in various standards 22 Optional accessories 45 Related information and materials 24 Rockwell hardness testing machine series 49 Related hardness standards Rockwell hardness testing machines Reference materials 26 HR Series 52 Rockwell Hardness testing machines Indenters 27 HR-100 to HR-400 Series 58 28 Specifications/Standard accessories/Optional