941165 Results of a Rocket-Based Combined-Cycle SSTO Design Using Parametric MDO Methods
Total Page:16
File Type:pdf, Size:1020Kb
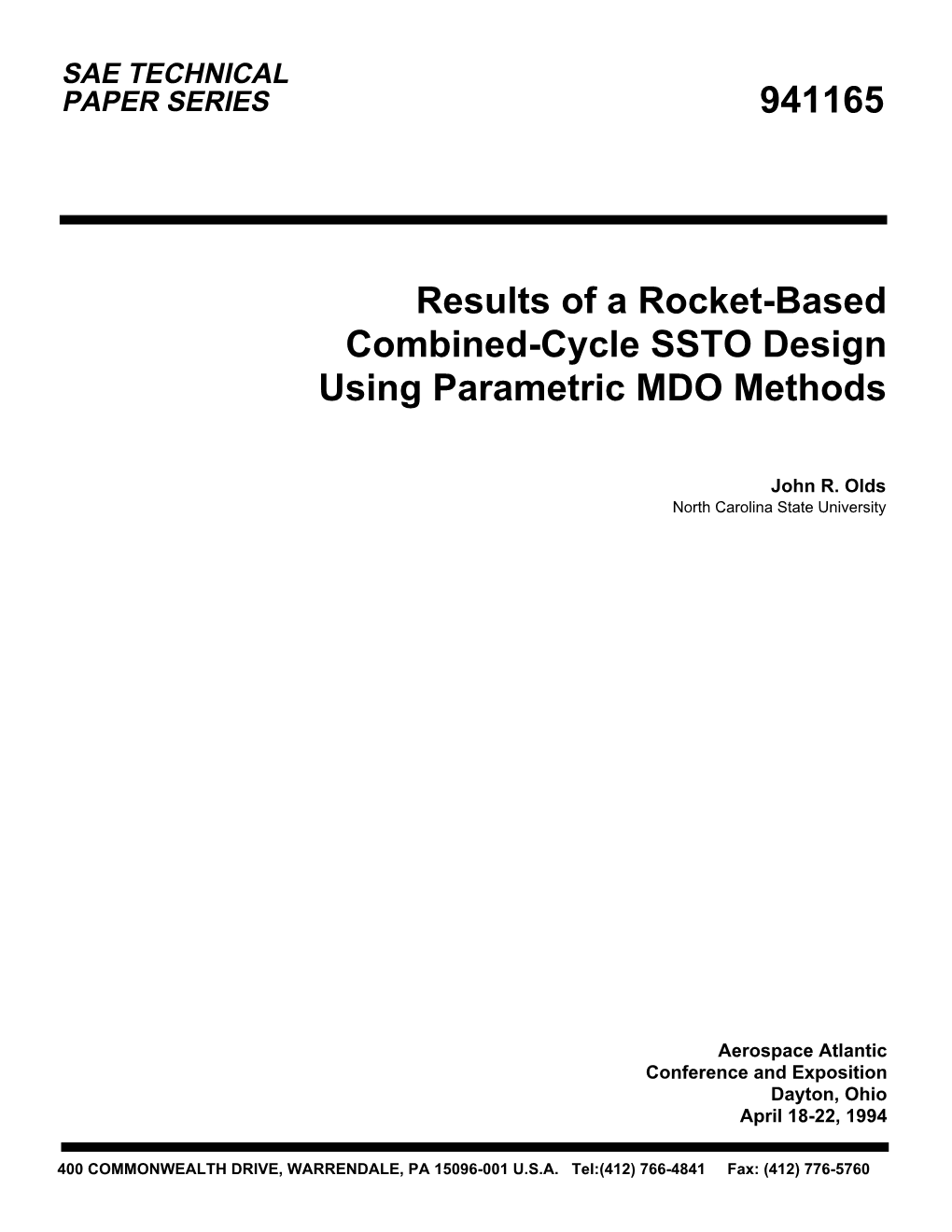
Load more
Recommended publications
-
THERMODYNAMIC MODELING of ADVANCED CYCLES for HIGH SPEED PROPULSION Von Karman Institute for Fluid Dynamics Universitat Politèc
THERMODYNAMIC MODELING OF ADVANCED CYCLES FOR HIGH SPEED PROPULSION Author Jose Tomás Sánchez Esparza Directors Bayindir H. Saracoglu Pedro Piqueras Cabrera Von Karman Institute for Fluid Dynamics Universitat Politècnica de València Escuela Técnica Superior de Ingeniería del Diseño Valencia, July 2018 Thermodynamic modeling of advanced cycles for high speed propulsion Jose Tomás Sánchez Esparza Von Karman Institute for Fluid Dynamics Universitat Politècnica de València Escuela Técnica Superior de Ingeniería del Diseño July 2018 Choose life. Choose a job. Choose a career. Choose a family. Choose a big television, choose washing machines, cars, compact disc players, and electrical tin openers. Choose good health, low cholesterol and dental insurance. Choose fixed-interest mortgage repayments. Choose a starter home. Choose your friends. Choose leisure wear and matching luggage. Choose a three piece suite on hire purchase in a range of fucking fabrics. Choose DIY and wondering who you are on a Sunday morning. Choose sitting on that couch watching mind-numbing spirit-crushing game shows, stuffing junk food into your mouth. Choose rotting away at the end of it all, pishing your last in a miserable home, nothing more than an embarrassment to the selfish brats you have spawned to replace yourselves. Choose your future. Choose life . But why would I want to do a thing like that? I chose not to choose life: I chose something else. And the reasons? There are no reasons. Who needs reasons when you’ve got heroin? Mark Renton - Trainspotting 4 Acknowledgments I would like to express my gratitude to my supervisor at the Von Karman Institute for Fluid Dynamics for helping me so far with my project during my internship, for teaching me and giving me pieces of advice in so many topics, even not related with science and technology. -
Modeling and Optimization of TBCC Engine
ABSTRACT Title of Thesis: Modeling and Optimization of Turbine-Based Combined-Cycle Engine Performance Joshua Clough, Master of Science, 2004 Thesis Directed By: Prof. Mark Lewis Aerospace Engineering The fundamental performance of several TBCC engines is investigated from Mach 0- 5. The primary objective of this research is the direct comparison of several TBCC engine concepts, ultimately determining the most suitable option for the first stage of a two-state-to-orbit launch vehicle. TBCC performance models are developed and optimized. A hybrid optimizer is developed, combining the global accuracy of probabilistic optimization with the local efficiency of gradient-based optimization. Trade studies are performed to determine the sensitivity of TBCC performance to various design variables and engine parameters. The optimization is quite effective, producing results with less than 1% error from optimizer repeatability. The turbine- bypass engine (TBE) provides superior specific impulse performance. The hydrocarbon-fueled gas-generator air turborocket and hydrogen-fueled expander- cycle air turborocket are also competitive because they may provide greater thrust-to- weight than the TBE, but require some engineering problems to be addressed before being fully developed. MODELING AND OPTIMIZATION OF TURBINE-BASED COMBINED-CYCLE ENGINE PERFORMANCE By Joshua Clough Thesis submitted to the Faculty of the Graduate School of the University of Maryland, College Park, in partial fulfillment of the requirements for the degree of Master of Science 2004 Advisory Committee: Professor Mark Lewis, Chair Professor Christopher Cadou Professor Ken Yu © Copyright by Joshua Clough 2004 PREFACE “The existing technological ability and scientific background accumulated in many years of work will be lost if a small but continuing effort in this field is not maintained” -Antonio Ferri, speaking on the future of airbreathing engines at the 4th AGARD Colloquium, in 1960. -
Airbreathing Hypersonic Technology Vision Vehicles and Development Dreams
AI A A 99 - 4 9 7 8 Airbreathing Hypersonic Technology Vision Vehicles and Development Dreams C. R. McClinton, J. L. Hunt, and R. H. Ricketts NA S A Langley Research Center, Hampton VA P. Reukauf NA S A Dryden Flight Research Center, Edwards, CA an d C. L. Peddie NA S A John Glenn Research Center, Cleveland, OH 9th International Space Planes and Hypersonic Systems and Technologies Conference an d 3rd Weakly Ionized Gases Wor k s h o p November 1-5, 1999/Norfolk, VA For permission to copy or republish, contact the American Institute of Aeronautics and Astronautics 370 L'Enfant Promenade, SW • Washington, DC 20024 AIAA 99-4978 Ai r b r eathing Hypersonic Tec h n o l o g y Vision Vehicles and Development Drea m s C. R. McClinton, J. L. Hunt, and R. H. Ricketts NASA Langley Research Center, Hampton VA P. Reukauf NASA Dryden Flight Research Center, Edwards, CA C. L. Peddie NASA John Glenn Research Center, Cleveland, OH ABSTRACT Significant advancements in hypersonic airbreathing vehicle technology have been made in the country’s research cen- ters and industry over the past 40 years. Some of that technology is being validated with the X-43 flight tests. This paper presents an overview of hypersonic airbreathing technology status within the US, and a hypersonic technology development plan. This plan builds on the nation’s large investment in hypersonics. This affordable, incremental plan focuses technology development on hypersonic systems, which could be operating by the 2020’s. IN T R O D U C T I O N over 40 years. -
Classifications of Aircraft Engines
Aeronautic Techniques Engineering Assist lecturer: Ali H. Mutib Aircraft Engines 3rd Class Classifications of Aircraft Engines An aircraft engine (or aero engine) is a propulsion system for an aircraft. Aircraft engines are the key module or the heart in aviation progress. Aero engines must be: 1. Reliable, as losing power in an airplane, is a substantially greater problem than in road vehicles. 2. Operate at extreme temperature, pressure and speed. 3. Light weight as a heavy engine increases the empty weight of the aircraft and reduces its payload. 4. Powerful, to overcome the weight and drag of the aircraft. 5. Small and easily streamlined to minimize the created drag. 6. Field repairable to keep the cost of replacement down. Minor repairs should be relatively inexpensive and possible outside of specialized shops. 7. Fuel efficient to give the aircraft the range and maneuverability the design requires. 8. Capable of operating at sufficient altitude for the aircraft. 9. Generate the least noise. 10. Generates the least emission. Aero engines may be classified based on input power into three main categories, namely, internal combustion engines, external combustion engines, and other power sources (Fig. 1-1). 1.1 External Combustion External combustion engines are steam, stirling, or nuclear engines. In these types, all heat transfer takes place through the engine wall. This is in contrast to an internal combustion engine where the heat input is by combustion of a fuel within the body of the working fluid. 1.1.1 Steam Engines Steam aircraft are aircraft that are propelled by steam engines. They were unusual devices because of the difficulty in producing a power plant with a high enough power to weight ratio to be practical. -
A Novel Turbo-Aided Rocket-Augmented Ramj Et Combined Cycle Engine Concept LING Wenhui WEI Baoxi LUO Chunqin LI Tinghe GANG Qiang
A Novel Turbo-aided Rocket-augmented Ramj et Combined Cycle Engine Concept LING Wenhui WEI Baoxi LUO Chunqin LI Tinghe GANG Qiang Beijing Power Machinery Research Institute, Science and Technology on Scramjet Laboratory, Beijing 100074, China Abstact: A novel multi-mode propulsion system is proposed for potential application to hypersonic planes. A unique feature of this concept is the use of mature turbo engine combined with RBCC. Its configuration is similar to TBCC, but the Ramjet tunnel is replaced by RBCC. turbo engine act as the primary thruster for Mach numbers in the range of about 0-2, and RBCC for Mach numbers of 2-6+. The obvious advantage is the high special impulse performance and high thrust-to-weight ability. But not like TBCC, it eliminates the need of advanced turbo engine which can work at Mach numbers of 0-4. It uses RBCC to resolve the relay problem from turbo mode to Ramjet mode. And with a suitable use of air augmented rocket, this new combined engine can provide high thrust-to-weight performance and extremely raise the stable combustion ability of ramjet mode at low pressure conditions. This allows the hypersonic plane to obtain the subsonic and hypersonic long-range cruise ability, the high maneuvering ability at hypersonic flight condition and high ceiling altitude hypersonic cruise ability. Preliminary performance estimates suggest that thrust and specific impulse are comparable or superior to existing TBCC designs. keywrods: aerospace aircraft combined engine 1 Introduction As an ideal propulsion device for the wide range flight of future near space aircraft and aerospace vehicle, the combined engine is integrated with two or more types of engines through the structure or thermodynamic cycle. -
An Overview of Propulsion Systems for Flying Vehicles
FOI-R--1563--SE June 2005 ISSN 1650-1942 Technical report Anders Hasselrot, Björn Montgomerie An Overview of Propulsion Systems for Flying Vehicles Source: Kanda and Kudo (2002) Systems Technology SE-172 90 STOCKHOLM SWEDISH DEFENCE RESEARCH AGENCY FOI-R--1563--SE Systems Technology June 2005 SE-172 90 Stockholm ISSN 1650-1942 Technical report Anders Hasselrot, Björn Montgomerie An Overview of Propulsion Systems for Flying Vehicles Issuing organization Report number, ISRN Report type FOI – Swedish Defence Research Agency FOI-R--1563--SE Technical report Systems Technology Research area code SE-172 90 Stockholm 7. Vehicles Month year Project no. June 2005 E83 0058 Customers code 5. Contracted Research Sub area code 73 Aeronautical Research Author/s (editor/s) Project manager Anders Hasselrot Fredrik Haglind Björn Montgomerie Approved by Monica Dahlén Sponsoring agency FMV Scientifically and technically responsible Anders Hasselrot, Björn Montgomerie Report title An Overview of Propulsion Systems for Flying Vehicles Abstract This report presents an overview of propulsion systems for flying vehicles, based on literature studies on current and future technologies. This effort is motivated by the need of this kind of information for the studies of vehicle concepts, being pursued in order to evaluate their performance merits. General information on inlets and outlets are also presented, as these influence the geometry and performance of the vehicles. The overview of inlet types is given with respect to the requirements at various Mach number regimes that govern the design. The stealth aspects are also viewed. In the report the available propulsion principles are presented category-wise, where most are based on combustion according to the Brayton cycle (heat addition under constant-pressure) and the other are based on combustion according to the Humphrey cycle (heat addition under constant-volume). -
CAS Ffll Copy
https://ntrs.nasa.gov/search.jsp?R=19780003231 2020-03-22T07:10:28+00:00Z NASA TECHNICAL NASA TM X-3554 MEMORANDUM •o to CO CAS Ffll COPy AN EVALUATION OF COMPOSITE PROPULSION FOR SINGLE-STAGE-TO-ORBIT VEHICLES DESIGNED FOR HORIZONTAL TAKE-OFF James A. Martin Langley Research Center Hampton, Va. 23665 NATIONAL AERONAUTICS AND SPACE ADMINISTRATION • WASHINGTON, D. C. • NOVEMBER 1977 1. Report No. 2. Government Accession No. 3. Recipient's Catalog No. NASA TM X-3551* 4. Title and Subtitle 5. Report Date AN EVALUATION OF COMPOSITE PROPULSION FOR SINGLE-STAGE- November 1977 TO-ORBIT VEHICLES DESIGNED FOR HORIZONTAL TAKE-OFF 6. Performing Organization Code 7. Author(s) 8. Performing Organization Report No. L-115U8 James A. Martin 10. Work Unit No. 9. Performing Organization Name and Address 506-26-10-08 NASA Langley Research Center 11. Contract or Grant No. Hampton, VA 23665 13. Type of Report and Period Covered 12. Sponsoring Agency Name and Address Technical Memorandum National Aeronautics and Space Administration 14. Sponsoring Agency Code Washington, DC 205^6 15. Supplementary Notes 16. Abstract Composite propulsion has been analyzed for single-stage-to-orbit vehicles designed for horizontal take-off. Six engines previously studied have been evaluated. Trajectory, geometric, and mass analyses were performed to establish the orbital payload capability. This study augmented other studies of advanced Earth-to-orbit vehicles using rocket propulsion. The results indicate that none of the engines has performed adequately to deliver payloads to orbit as analyzed. The single-stage turbine and oxidizer- rich gas generator result in a low engine specific impulse, and the performance increment of the ejector subsystem is less than that of a separate rocket system with a high combustion pressure. -
ATINER's Conference Paper Series MEC2020-2713
ATINER CONFERENCE PAPER SERIES No: LNG2014-1176 Athens Institute for Education and Research ATINER ATINER's Conference Paper Series MEC2020-2713 Hybrid Air-Breathing Rockets & their Potential Tyler Borda Powerplant Engineer United Airlines USA Mark Guerrieri Aerospace Engineer San Jose State University USA Periklis Papadopoulos Professor San Jose State University USA 1 ATINER CONFERENCE PAPER SERIES No: MEC2020-2713 An Introduction to ATINER's Conference Paper Series Conference papers are research/policy papers written and presented by academics at one of ATINER’s academic events. ATINER’s association started to publish this conference paper series in 2012. All published conference papers go through an initial peer review aiming at disseminating and improving the ideas expressed in each work. Authors welcome comments. Dr. Gregory T. Papanikos President Athens Institute for Education and Research This paper should be cited as follows: Borda, T., Guerrieri, M. and Papadopoulos, P. (2020). "Hybrid Air- Breathing Rockets & their Potential", Athens: ATINER'S Conference Paper Series, No: MEC2020-2713. Athens Institute for Education and Research 8 Valaoritou Street, Kolonaki, 10671 Athens, Greece Tel: + 30 210 3634210 Fax: + 30 210 3634209 Email: [email protected] URL: www.atiner.gr URL Conference Papers Series: www.atiner.gr/papers.htm ISSN: 2241-2891 23/09/2020 2 ATINER CONFERENCE PAPER SERIES No: MEC2020-2713 Hybrid Air-Breathing Rockets & their Potential Tyler Borda Mark Guerrieri Periklis Papadopoulos Abstract Research and analysis of proposed hybrid air-breathing rocket engines will take place to make determinations about their suitability for future use as a reusable space-grade engine for human transport. This paper will go in-depth and discuss its theory of operation and mechanism of action specific to the Synergetic Air-Breathing Rocket Engine or SABRE as it is more commonly referred to. -
Recalculation of Air Turborocket Performance
第一工業大学研究報告 41 第25号(2013)pp.41-47 Recalculation of air turborocket performance Recalculation of air turborocket performance Recalculation of air turborocket performance Koichi SUZUKI* Koichi Suzuki* Koichi Suzuki* The turborocket engine has been proposed for use in very-high-speed vehicles, such as Earth-to-orbit The turborocket launchers. engine has The been pure proposed ramjet forengine use incan’t very-high-speed work at low vehicles,Mach numbers, such as whileEarth-to-orbit the turbojet launchers. engine hasThe poorpure performance ramjet engine at highcan’t Machwork numbersat low Mach because numbers, of the limitationwhile the turbojetof turbine engine inlet temperature.has poor performance The turborocket at high engineMach numbers improves because weak pointsof the oflimitation both engines, of turbine it has inlet one temperature. or two stage The fans turborocket which work engine at low improves Mach numbers weak points and turbinesof both engines, which use it hasindependent one or two gas stage from fansfree streamwhich workair. The at turborocketlow Mach numbers engine andhas beenturbines introduced which use in theindependent standard gastextbook from freeof Dr. stream Jack L.air. Kerrebrock’s The turborocket “Aircraft engine Engines has andbeen Gasintroduced Turbines” in the , standardbut unfortunately textbook of thereDr. Jack are L. someKerrebrock’s misunderstandings “Aircraft Engines and miscalculationand Gas Turbines” of the ,engine but unfortunatelyperformance. Thethere engine are someperformance misunderstandings of his book is andtoo high.miscalculation The text bookof the is enginenot revised performance. though it Theused engine worldwide, performance so this paperof his is book one ofis thetoo proposalhigh. The of text correction book is ofnot chapter revised 10.8 though of the it book. -
A Performance Analysis of a Rocket Based Combined Cycle (RBCC) Propulsion System for Single-Stage-To-Orbit Vehicle Applications
University of Tennessee, Knoxville TRACE: Tennessee Research and Creative Exchange Masters Theses Graduate School 12-2010 A Performance Analysis of a Rocket Based Combined Cycle (RBCC) Propulsion System for Single-Stage-To-Orbit Vehicle Applications Nehemiah Joel Williams UTSI, [email protected] Follow this and additional works at: https://trace.tennessee.edu/utk_gradthes Part of the Propulsion and Power Commons Recommended Citation Williams, Nehemiah Joel, "A Performance Analysis of a Rocket Based Combined Cycle (RBCC) Propulsion System for Single-Stage-To-Orbit Vehicle Applications. " Master's Thesis, University of Tennessee, 2010. https://trace.tennessee.edu/utk_gradthes/842 This Thesis is brought to you for free and open access by the Graduate School at TRACE: Tennessee Research and Creative Exchange. It has been accepted for inclusion in Masters Theses by an authorized administrator of TRACE: Tennessee Research and Creative Exchange. For more information, please contact [email protected]. To the Graduate Council: I am submitting herewith a thesis written by Nehemiah Joel Williams entitled "A Performance Analysis of a Rocket Based Combined Cycle (RBCC) Propulsion System for Single-Stage-To- Orbit Vehicle Applications." I have examined the final electronic copy of this thesis for form and content and recommend that it be accepted in partial fulfillment of the equirr ements for the degree of Master of Science, with a major in Aerospace Engineering. Gary A. Flandro, Major Professor We have read this thesis and recommend its acceptance: Trevor -
NSIAD-92-5 Aerospace Plane Technology Executive Summary
-~-“-- .-... --- I ~nit.tvi-~_I_ Stat vs (;cbrtctral Accwrrnting-- Off’iw..-w--e. Report to the Chairm&, Cwnnzittee on GAO Science, Space, and ?‘echnolog,y , House of IZepresentati ves Oc.t.ctt,wI!)!) 1 AERbSPACE PLANE TECHNOLOGY Research and Development Efforts in Japan and Australia (;AO,‘NSIAD-92-5 , &gllllll ~iit&~~;gflce i , ” National Security and International Affairs Division B-236387 October 4,199l The Honorable George E. Brown, Jr. Chairman, Committee on Science, Space, and Technology House of Representatives Dear Mr. Chairman: As requested by the former Chairman, we reviewed investment in foreign aerospace vehicle research and technological development efforts. Supporters of the National Aero-Space Plane Program in the Congress are concerned about foreign competition to the program and its impact on U.S. technological leadership. We briefed representatives of the former Subcommittee on Transportation, Aviation, and Materials (now part of the Subcommittee on Technology and Competitiveness), House Committee on Science, Space, and Technology, previously on the results of our review. This report discusses investment in Japanese and Australian aerospace vehicle research and technological development efforts. This report is the third in a planned series of reports on aerospace investment in foreign countries. We issued our first report, Aerospace Technology: Technical Data and Information on Foreign Test Facilities (GAO/NSIAD-90-7lFS), on June 22, 1990. We issued our second report, Aerospace Plane Technology: Research and Development -
Liquid Hydrogen As a Propulsion Fuel, 1945-1959
https://ntrs.nasa.gov/search.jsp?R=19790008823 2020-03-20T18:21:35+00:00Z NASA SP-4404 LIQUID HYDROGEN AS A PROPULSION FUEL, 1945-1959 NATIONAL AERONAUTICS AND SPACE ADMINISTRATION LIQUID HYDROGEN AS A PROPULSION FUEL, 1945-1959 JOHN L. SLOOP The NASA History Series Scrri~tr/rcund 7 rchtrrr~/Itt/r~fm.rtmn Ofit? 19's NA'I'IONAI. AERONAUTICS AND SPA( E ADhIINIS1 RATIO1 lt'..~,btji q/ot~P ( Library of Congress Cataloging in Publication Data Sloop. John L Liquid hydrogen as a propulsion fuel. 1945-1959. (The NASA history series) (NASA SP ; 4404) Bibliography: p. Includes index. I. Rockets (Aeronautics)-Fuel. 2. Hydrogen as fuel. 1. Title. 11. Series: United States. National Aeronautics and Space Administration. The NASA history series. 111. Series: United States. National Aeronautics and Space Administration. NASA SP ; 4404. TL785.SS8 629.47'522 77-26960 For sale by the Superintendent of Documents Stock Number 033400-00707-8 U.S. Government Printing Office Washington, D.C. 20402 Contents FOREWORD .................................................... ...xi PREFACE ....................................................... x~ii 1 . INTRODUCTION ................................................ I PART I: 1945-1950 2 . AIR FORCE RESEARCH ON HYDROGEN ........................ I I The Cryogenics Laboratory at Ohio State University ................... 13 Hydrogen for Aircraft and Rockets .................................. 18 Hydrogen-Air ..................................................... 18 Hydrogen-Oxygen Rocket .........................................