Additives in Wood Products—Today and Future Development
Total Page:16
File Type:pdf, Size:1020Kb
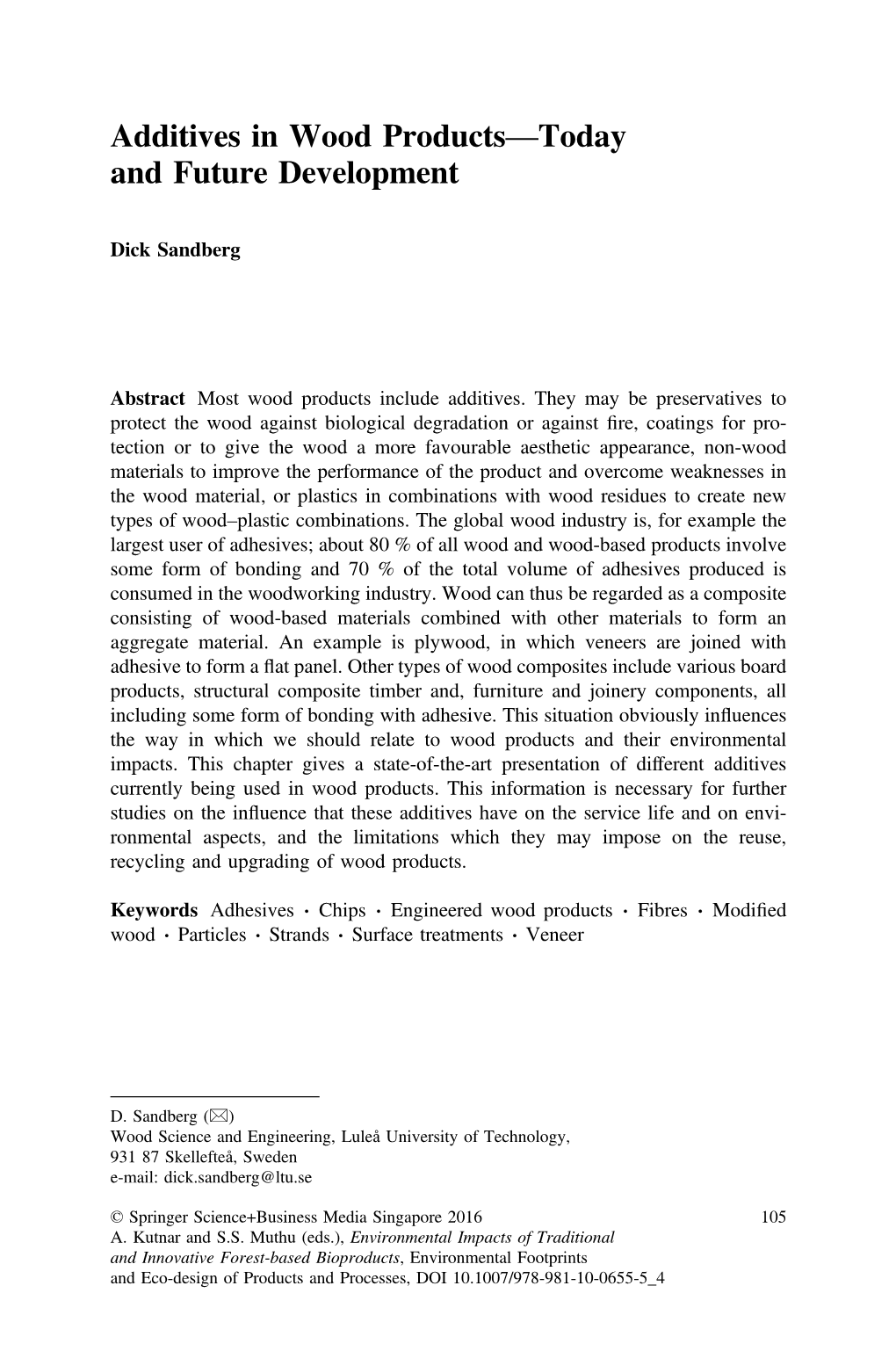
Load more
Recommended publications
-
Everything for Perfect Wood Finishing
Akzo Nobel Hilden GmbH Düsseldorfer Straße 96-100 40721 Hilden Germany Everything for perfect wood finishing Interior portfolio - Quantum Range Wood Coatings Passion for wood www.akzonobel.com AkzoNobel creates everyday essentials to make people’s lives more liveable and inspiring. As a leading global paints and coatings company and a major producer of specialty chemicals, we supply essential ingredients, essential protection and essential color to industries and consumers worldwide. Backed by a pioneering heritage, our innovative products and sustainable technologies are designed to meet the growing demands of our fast-changing planet, while making life eas- ier. Headquartered in Amsterdam, the Nether-lands, we have approximately 45,000 people in around 80 countries, while our portfolio includes well-known brands such as Dulux, Sikkens, Inter-national, Interpon and Eka. Consistently ranked as a leader in sustainability, we are dedicated to energizing cities and communities while creating a protected, colorful world where life is improved by what we do. © 2016 Akzo Nobel Hilden GmbH All rights reserved. AN_XXXXXXXXXXX · Subject to alterations and errors. Contents PU Acrylic, clear Additional products Sealer Hardener Quantum Q-IS160 8 Hardener HPU6300 14 Quantum Q-S170 8 Thinner Top coat Thinner TPU9300 - F 15 Quantum Q-T260-__ 9 Thinner TPU9301 -S 15 Quantum Q-T261-05 9 Quantum Q-T263-90 10 Quantum Q-T280-__ 10 PU Acrylic, pigmented Primer QuantumColor QC-IP350 11 Top coat QuantumColor QC-T460-__- 12 ____ QuantumColor QC-T470-90-____ 12 2 3 Contents PU Acrylic, clear Additional products Sealer Hardener Quantum Q-IS160 8 Hardener HPU6300 14 Quantum Q-S170 8 Thinner Top coat Thinner TPU9300 - F 15 Quantum Q-T260-__ 9 Thinner TPU9301 -S 15 Quantum Q-T261-05 9 Quantum Q-T263-90 10 Quantum Q-T280-__ 10 PU Acrylic, pigmented Primer QuantumColor QC-IP350 11 Top coat QuantumColor QC-T460-__- 12 ____ QuantumColor QC-T470-90-____ 12 2 3 Code-System Learn more about the AkzoNobel Wood Coatings code system. -
Wood Finishing Demonstration Project Final Report
Wood Finishing Demonstration Project Final Report Paul Pagel Minnesota Technical Assistance Program & Barb Loida Minnesota Pollution Control Agency Small Business Compliance Assistance Program January 1997 Table of Contents INTRODUCTION......................................................................................................................................... 1 FINDING AND SELECTING A CANDIDATE FOR THE PROJECT................................................... 1 THE WOOD FINISHING PROCESS......................................................................................................... 2 PROCESS CONSIDERATIONS AND COMPANY COMPARISONS............................................................................. 2 EMISSIONS AND WASTES ....................................................................................................................... 4 AT PINE-TIQUE ................................................................................................................................................ 4 AT VIKING ....................................................................................................................................................... 5 USE OF WATERBORNE FINISHES......................................................................................................... 6 FINISH CRITERIA AND PROCESS CONSIDERATIONS FOR SELECTING ALTERNATIVE COATINGS ......................... 6 TESTING, MODIFICATIONS AND RESULTS...................................................................................... -
Wood-Based Composite Materials Panel Products, Glued-Laminated Timber, Structural Composite Lumber, and Wood–Nonwood Composite Materials Nicole M
CHAPTER 11 Wood-Based Composite Materials Panel Products, Glued-Laminated Timber, Structural Composite Lumber, and Wood–Nonwood Composite Materials Nicole M. Stark, Research Chemical Engineer Zhiyong Cai, Supervisory Research Materials Engineer Charles Carll, Research Forest Products Technologist The term composite is being used in this chapter to describe Contents any wood material adhesively bonded together. Wood-based Scope 11–2 composites encompass a range of products, from fiberboard Conventional Wood-Based Composite Panels 11–2 to laminated beams. Wood-based composites are used for a number of nonstructural and structural applications in prod- Elements 11–2 uct lines ranging from panels for interior covering purposes Adhesives 11–3 to panels for exterior uses and in furniture and support struc- Additives 11–5 tures in buildings (Fig. 11–1). Maloney (1986) proposed Plywood 11–5 a classification system to logically categorize the array of wood-based composites. The classification in Table 11-1 Oriented Strandboard 11–7 reflects the latest product developments. Particleboard 11–10 The basic element for wood-based composites is the fiber, Fiberboard 11–12 with larger particles composed of many fibers. Elements Speciality Composite Materials 11–15 used in the production of wood-based composites can be Performance and Standards 11–15 made in a variety of sizes and shapes. Typical elements in- Glulam Timber 11–17 clude fibers, particles, flakes, veneers, laminates, or lumber. Figure 11–2 shows the variation and relative size of wood Advantages 11–17 elements. Element size and geometry largely dictate the Types of Glulam Combinations 11–17 product manufactured and product performance. -
Removing the Old Finish Wood Finishing Dr
Fact Sheet #3 Removing the Old Finish Wood Finishing Dr. Leona K. Hawks & Refinishing Home Furnishings and Housing Specialist 1995 HI 23 Introduction A successful refinishing job depends upon the care and the thoroughness with which the old finish is removed. Commercial paint removers are the most effective materials available to use in removing old finishes. Read the label to see what kind of finish the paint remover will soften. The heavy-duty or premium grades that soften epoxy will soften the old finish faster and save you time. Safety Practices When dealing with potentially harmful paint removing chemicals, there are some safety practices that should be followed: 1. Work in a well-ventilated room. 2. Store all wood refinishing chemicals away from children and animals. 3. Avoid all contact of products with skin and eyes by wearing rubber gloves, old clothes with long sleeves, and glasses. 4. Always open the lid of the paint remover slowly to allow pressure to escape. When stored for long periods of time, excessive pressure builds up in the container and opening rapidly may cause the remover to spray the user. 5. Never apply finishing chemicals in a room where there is an open flame or a pilot light. 6. If at all possible, select a nonflammable paint remover. 7. Clean brushes and discard rags soaked with paint remover. Prior Preparation Prior to stripping wood furniture, there are some things you should do to get ready: 1. Spread work area with layers of newspaper for protection. 2. Remove hardware such as handles, drawer pulls, knobs, and hinges. -
Aqualitrange R Portfolio- Contents
Akzo Nobel Hilden GmbH Düsseldorfer Straße 96-100 40721 Hilden Germany Everything for perfect wood finishing Interior portfolio - Aqualit Range Wood Coatings Passion for wood www.akzonobel.com AkzoNobel creates everyday essentials to make people’s lives more liveable and inspiring. As a leading global paints and coatings company and a major producer of specialty chemicals, we supply essential ingredients, essential protection and essential color to industries and consumers worldwide. Backed by a pioneering heritage, our innovative products and sustainable technologies are designed to meet the growing demands of our fast-changing planet, while making life eas- ier. Headquartered in Amsterdam, the Nether-lands, we have approximately 45,000 people in around 80 countries, while our portfolio includes well-known brands such as Dulux, Sikkens, Inter-national, Interpon and Eka. Consistently ranked as a leader in sustainability, we are dedicated to energizing cities and communities while creating a protected, colorful world where life is improved by what we do. © 2016 Akzo Nobel Hilden GmbH All rights reserved. AN_XXXXXXXXXXX · Subject to alterations and errors. Contents PUWaterborne, Acrylic, clear clear Additional products Sealer Hardener Aqualit A-IS180 8 Hardener HWA6000 14 Aqualit A-S150 8 Thinner Sandoseal 199 Thinner TWA9000 - F 15 Top coat Aqualit A-T250-__ 9 Supercryl Aqualit A-T260-__ 9 Aqualit A-T280-90 10 Aqualit A-T280-__ 10 Waterborne, pigmented Primer AqualitColor AC-IP360 11 AqualitColor AC-P340 11 Aqua Surf 136 Top coat AqualitColor -
10 Step Guide to Wood Finishing
Westfarthing Woodworks 10 Step Guide To Wood Finishing Copyright Westfarthing Woodworks LLC 2014 This work may be printed, handed out, linked to, and freely distributed as long as it re- mains in original form without any deletions, additions, or omissions. Please reference the source when linking and distributing, and best of luck in all your woodworking ad- ventures. This booklet and others can be found at westfarthingwoodworks.com 1 If you like this guide... My Books Are On Amazon Acoustic Guitar Making: How to Make Tools Templates and Jigs is a reference guide for many aspects of acoustic guitar making. The book covers making blanks, making tools instead of buying them, how small changes affect tone, and a thorough finishing section. This is a 508 page monster of a book, and it can be used as a reference for the guitar maker. This is not an ABC book, but a companion that teaches many of the things that the other step by step books leave out, or do not cover as thoroughly. For the be- ginning and the intermediate guitar maker, this book can be quite a resource. Click on the book cover and you can see more information and reviews on Amazon. Wooden Rings: How to Make Wooden Rings by Hand is my second book, and it has step by step instructions and photo examples of over 50 rings that even those with lim- ited woodworking experience can make. The instructions are written for basic tools which anyone can afford, though power tools can also be used if available. -
Wood Staining Staining & & Finishing Finishing
FINISH TOUCH BRO 1109_V6.qxd:FINISH TOUCH BRO_1109 11/24/09 6 A Complete Guide Guide to Wood Staining Staining & & Finishing Finishing Includes: Door Finishing Finishing & & Wood Wood Graining Instructions FINISH TOUCH BRO 1109_V6.qxd:FINISH TOUCH BRO_1109 11/24/09 6 GettingGetting Started Started Keep These Suggestions in Mind: 1. Always read the label! Follow all label directions exactly to ensure a successful wood finishing project. Pay particular attention to all “DANGER and CAUTION” instructions. 2. Protect your work area by laying lined drop cloths, cardboard or plastic over the floor area. 3. Be sure the area is warm and dry and it has adequate ventilation and good lighting. Pre-Plan for a Successful Project For best results have everything you need before you start. The condition of the wood you are finishing will help you decide what materials you need to do the job, such as scrapers, brushes, sandpaper, stir sticks, etc. New Bare Wood You may prefer to stain the wood and apply a polyurethane, or you can simply apply the polyurethane over the natural wood. Old Clear Finishes in Good Condition A finish in good condition can be covered with a fresh coat of polyurethane once the surface has been cleaned and properly sanded. UGL® Professional Strength D-Gloss Water-Based Liquid Sander & Cleaner Prepares surfaces for recoating. Removes surface contaminants and provides a slight “etching” of the surface allowing subsequent coatings to bond. Dulls paint, enamel, varnish and polyurethane. Some polyurethane finishes do not adhere to shellac or lacquer surfaces. It is advisable to remove these finishes before recoating. -
Wood Finishing Basics
Wood Finishing Basics APPLICATION TECHNIQUES & PRODUCT SELECTION GETTING STARTED Your home is a unique expression of your individual Before starting any wood finishing project it is important decorating taste. And what better way to display your to have a proper workspace and supplies. When creating style than through the warmth and beauty of natural the ideal area please keep the following in mind: wood? From traditional to contemporary and everywhere • The work station must have adequate light. in-between, the possibilities are endless! Wood’s natural • Always work in a well ventilated area. warmth and beauty add richness and character. And with • The workspace should be dry and warm. If the area is ® a little know-how and Minwax stains and finishes, it’s cool or damp it may alter the dry times indicated on the easier than you think to create a statement of style. labels. In this guide, author and craftsman, Bruce Johnson, There are a number of items frequently used in wood pairs application tips and techniques with product finishing projects. This list does not include all the supplies needed, but what is most commonly used. recommendations that best enhance the beauty of wood Always consult the label of the Minwax® products you are in your home. This booklet will take you through the wood using to see if special application tools are required. finishing process including preparation, staining and topcoating, as well as maintenance of your wood pieces. Rags Stir Sticks Whether you are a beginner or a seasoned do-it-yourselfer, Brushes Safety Glasses these ideas will help you achieve beautiful results with ease. -
WOOD FINISHING SYSTEMS ® Remarkable Support
® WOOD FINISHING SYSTEMS ® Remarkable Support. Fully understan ding your shop needs is the first step in recommending WOOD FINISHING SYSTEMS the right system. Ask your distributor la cquer specialist to suggest the best finishing system that is ideal for your shop applications. Toge ther, M.L. Campbell and our factory-trained distributors are dedicated to providing you with sup erior products and services. m.l.campbell® WOOD FINISHING SYSTEMS ® m.l.campbell training programs WOOD FINISHING SYSTEMS At our state-of-the-art training facility, M.L. Campbell offers a rigorous training program that prepares distributor color match experts lacquer specialists to analyze and recommend the right system Custom color stain and pigmented finishes are available from our for your shop needs. We also offer comprehensive hands-on M.L. Campbell® Color Studio™ with quick match turnaround time. training seminars and technical support at distributor locations. Utilizing M.L. Campbell’s unique color tint system and color match computers allows for precise color matching that can be easily shop consultations duplicated with accuracy. Through the help of our trained professionals, we work in-house with shops to help you achieve your specific finishing needs. sales tools Our factory-trained distributor lacquer specialists will come to Not only do our distributors make it easy your shop to personally demonstrate and spray M.L. Campbell® for you to get your hands on the best wood finishes. The demonstration will include recommendations quality products, they on proper wood finishing systems, spray equipment and any make it just as other finishing supplies that you may need. -
Wood Finishing Process
Wood finishing process Wood finishing process At OFS we believe that the employees are a company’s biggest asset and the way they experience their office space is through the furniture. When you invest in furniture, you are investing in your employees. A well designed space means that workspace supports the design intent, reflect your firms culture and ultimately delivers the desired experience. We understand and appreciate the magnitude of this decision. With OFS, you are working with a family owned company who values long term relationships over short term financial results. Along with a deep commitment to staying customer focused, you also have the backing and resources of the largest family owned wood casegoods company in the office furniture industry. OFS has been a leader in crafting superior wood furniture for over 80 years. Products that we proudly offer have stood up to heavy use for decades. We have several references that can speak first hand to our capability to outperform the industry in beauty and durability. There are several aspects to the process and formulation of OFS’s patented Euroluxe finish that gives our clients lasting satisfaction. The uniquely formulated urethane top coat that we call Euroluxe delivers a smooth, silky, warm touch, a true wood feel, while also providing the surface with a durable, chemical resistant and temperature resistant finish. Specifically, the Euroluxe finish will guard against water stains from spills or glass ring, heat marks from hot pizza boxes, scratches from shuffling files even a nail polish remover spill. Additionally, the Euroluxe finish offers the beauty and clarity in the wood finish that is unmatched in the industry. -
Understanding Wood Finishing –
UNDERSTANDING WOOD FINISHING How To Select And Apply The Right Finish By Bob Flexner WHY FINISH WOOD, ANYWAY? Sanitation Stabilization Decoration PREPARING THE WOOD SURFACE Preparing the Lumber Sanding and Smoothing Sponging Sharpening a Hand Scraper Sharpening a Cabinet Scraper Solvents for Removing Cured Glues Glue Splotches Dents, Gouges, and Holes Wood Putties TOOLS FOR APPLYING FINISHES Rags Brushes Rubbing Pads Spray Guns and Equipment Common Spraying Problems OIL FINISHES Our Ancestors and Linseed Oil Applying "Oil" Finishes Oil Finishes and Penetration How Oil and Oil/Varnish Finishes Protect Types of "Oil Safety and Oil Finishes Using Wax as a Finish Bleeding Oil Finishes Which One Is Which? How to Tell Which "Oil" You Have How to Maintain and Repair "Oil" Finishes Guide to "Oil" Finishes STAINING WOOD What Makes a Stain Understanding Stains A Guide to Stains Using Aniline Dyes Bleaching Wood Chemical Stains Ebonizing Wood Matching Color A Sampler of Wood Stains Solvents and Thinners for Dyes and Stains Compatibility of Stains and Finishes How Woods React to Stains Applying Stain Applying Glaze Pickling Common Staining Problems, Their Causes, and Solutions FILLING THE PORES Filling the Pores with the Finish Filling the Pores: Finish versus Paste-Wood Filler Filling the Pores with Paste-Wood Filler Using Oil/Varnish Paste-Wood Filler Using Water-Based Paste-Wood Filler INTRODUCTION TO FILM FINISHES........... What's in a Name? Sealers and Sanding Sealers The Way Finishes Cure Finishing Materials: How They Cure Stain and Finish -
Finishing Wood
CHAPTER 16 Finishing Wood Christopher G. Hunt, Research Chemist Wood finishes (paint, varnish, and stain, for example) give Contents a desired appearance, protect wood surfaces, and provide Wood Properties Affecting Finish Performance 16–1 a cleanable surface. Many people consider appearance Wood Products 16–6 most important when choosing finishes for wood products. Effect of Weathering on Finish Performance 16–9 However, from a technical aspect, protection—from water, sunlight, and weathering—is most important for Decay and Insects 16–11 wood used outdoors. For wood indoors, appearance Controlling Water and Water Vapor 16–12 and a cleanable surface are generally most important. General Properties of Wood Finishes 16–14 When selecting a finish, one should consider appearance, Exterior Finishes 16–15 protection, cleanability, how properties of wood affect finish application, and how long it will likely last. Application of Finishes, Special Uses 16–21 Failures 16–23 Wood properties vary within and across wood species. Wood composites, such as plywood, fiberboard, and Finishing Interior Wood 16–29 oriented strandboard (OSB), have different properties. Of Wood Cleaners and Brighteners 16–31 the 18,000 to 25,000 known wood species, approximately Paint Stripping 16–31 50 are commercial species used in the United States and Lead-Based Paint 16–33 Canada. (Chapters 2–4 describe their properties.) Of these commercial species, researchers report finishing Acknowledgment 16–34 characteristics for only a few of the most commonly used Literature Cited 16–34 species. However, if one understands how wood properties, Recommended Books 16–34 finish, and environmental conditions interact, it should FPL FinishLines and TechLines 16–34 be possible to predict and avoid issues with finishing performance for most wood products.