Draft Epa Dive Safety Plan for 04/04
Total Page:16
File Type:pdf, Size:1020Kb
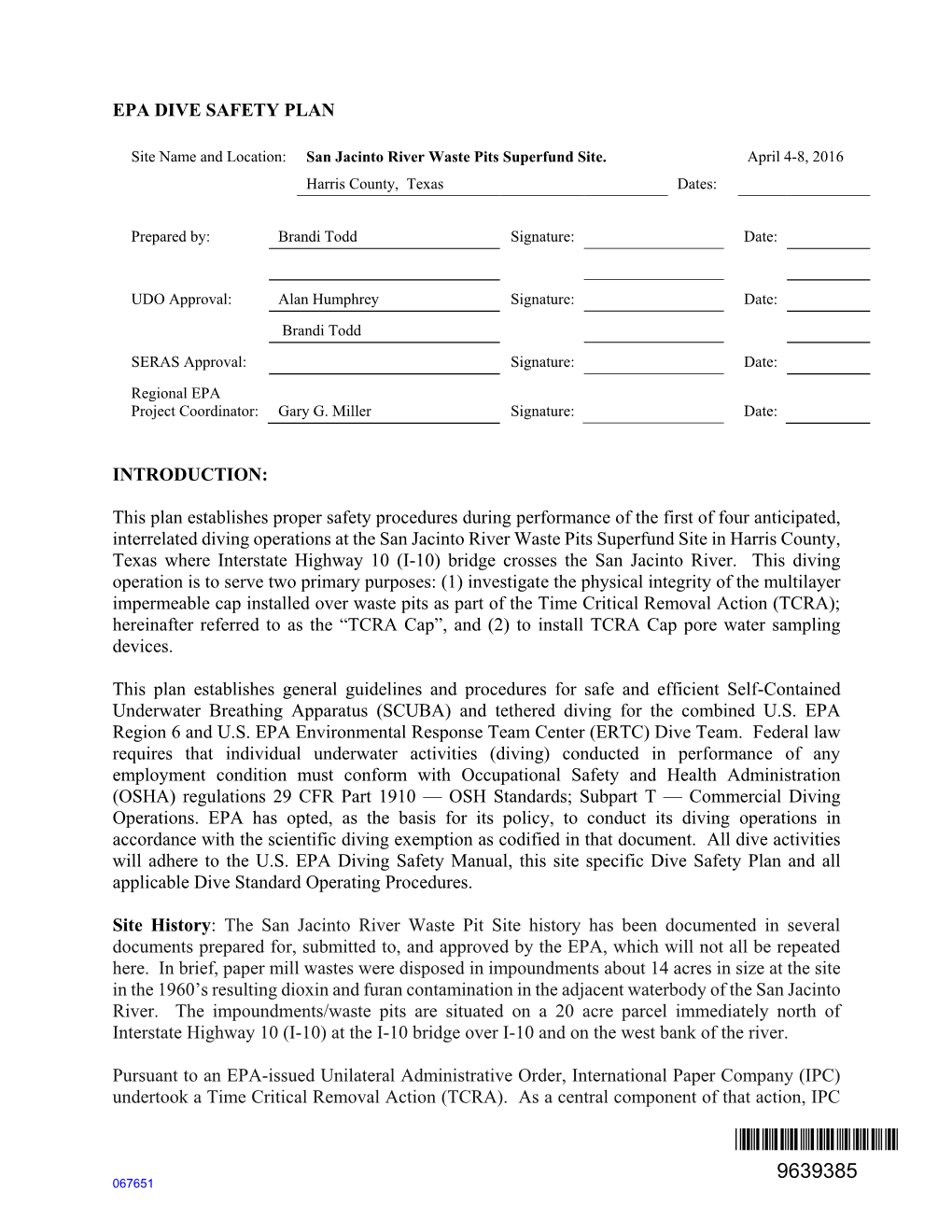
Load more
Recommended publications
-
Lake Huron Scuba Diving
SOUTHERN LAKE ASSESSMENT SOUTHERN RECREATION PROFILE LAKE Scuba Diving: OPPORTUNITIES FOR LAKE HURON ASSESSMENT FINGER LAKES SCUBA LAKES FINGER The southern Lake Huron coast is a fantastic setting for outdoor exploration. Promoting the region’s natural assets can help build vibrant communities and support local economies. This series of fact sheets profiles different outdoor recreation activities that could appeal to residents and visitors of Michigan’s Thumb. We hope this information will help guide regional planning, business develop- ment and marketing efforts throughout the region. Here we focus on scuba diving – providing details on what is involved in the sport, who participates, and what is unique about diving in Lake Huron. WHY DIVE IN LAKE HURON? With wildlife, shipwrecks, clear water and nearshore dives, the waters of southern Lake Huron create a unique environment for scuba divers. Underwater life abounds, including colorful sunfish and unusual species like the longnose gar. The area offers a large collection of shipwrecks, and is home to two of Michigan’s 12 underwater preserves. Many of the wrecks are in close proximity to each other and are easily accessed by charter or private boat. The fresh water of Lake Huron helps to preserve the wrecks better than saltwater, and the lake’s clear water offers excellent visibility – often up to 50 feet! With many shipwrecks at different depths, the area offers dives for recreational as well as technical divers. How Popular is Scuba Diving? Who Scuba Dives? n Scuba diving in New York’s Great Lakes region stimulated more than $108 In 2010, 2.7 million Americans went scuba A snapshot of U.S. -
Download the Full Article As Pdf ⬇︎
AndreaInterview with Donati — Pioneering Technical Diving on Ponza for 30 Years Andrea Donati (left) and his partner, Daniela Spaziani, run Ponza Diving, which is located in the main harbour (above) of Ponza Island in Italy. In my line of work as a dive industry professional, I attend a lot of dive shows and get to meet a lot of people, most of them nice and interesting in various ways. It was also at a dive show in Italy, many years ago, that I first met Andrea Donati and his partner, Daniela Spaziani, of Ponza Diving. I clearly remember my first impression of how sympathetic, unpretentious and genuine the two came across, which scores a lot of points in my book. They appeared competent and organised, and with their operation located in one of the most picturesque locations I have ever seen, it did not take any arm twisting to lure me down there for a visit. Text and photos by Peter Symes future. This profile will be about the virtues driven, and adapting more readily to the accommodate a wider range of requests anchoring it. In hindsight, I now consider of diving Italian-style, as Ponza Diving services we could offer in those times. and needs of customers. mooring essential for a successful dive. The world is dotted with beautiful loca- marks its 30th season. Of course, diving equipment was not We started off with just a 6m dinghy, Year by year, the number of divers tions, and there exist many excellent dive so sophisticated at that time. We dived a compressor and 20 tanks, but already increased, and I kept reinvesting in the operations across the globe that also PS: Please reflect on your three decades only with air, no nitrox, no trimix and no in the first year, I bought another dinghy, operation. -
Diving Safety Manual Revision 3.2
Diving Safety Manual Revision 3.2 Original Document: June 22, 1983 Revision 1: January 1, 1991 Revision 2: May 15, 2002 Revision 3: September 1, 2010 Revision 3.1: September 15, 2014 Revision 3.2: February 8, 2018 WOODS HOLE OCEANOGRAPHIC INSTITUTION i WHOI Diving Safety Manual DIVING SAFETY MANUAL, REVISION 3.2 Revision 3.2 of the Woods Hole Oceanographic Institution Diving Safety Manual has been reviewed and is approved for implementation. It replaces and supersedes all previous versions and diving-related Institution Memoranda. Dr. George P. Lohmann Edward F. O’Brien Chair, Diving Control Board Diving Safety Officer MS#23 MS#28 [email protected] [email protected] Ronald Reif David Fisichella Institution Safety Officer Diving Control Board MS#48 MS#17 [email protected] [email protected] Dr. Laurence P. Madin John D. Sisson Diving Control Board Diving Control Board MS#39 MS#18 [email protected] [email protected] Christopher Land Dr. Steve Elgar Diving Control Board Diving Control Board MS# 33 MS #11 [email protected] [email protected] Martin McCafferty EMT-P, DMT, EMD-A Diving Control Board DAN Medical Information Specialist [email protected] ii WHOI Diving Safety Manual WOODS HOLE OCEANOGRAPHIC INSTITUTION DIVING SAFETY MANUAL REVISION 3.2, September 5, 2017 INTRODUCTION Scuba diving was first used at the Institution in the summer of 1952. At first, formal instruction and proper information was unavailable, but in early 1953 training was obtained at the Naval Submarine Escape Training Tank in New London, Connecticut and also with the Navy Underwater Demolition Team in St. -
Surface-Supplied Diver Training Manual
Surface-supplied Diver Training Manual Tennessee Aquarium Chattanooga, TN Published by the Diving Control Board Tennessee Aquarium Chattanooga, TN 1st Edition 2007 Purpose Surface-supplied diving is defined in the Tennessee Aquarium Diving Safety Manual (TADSM) as a diving mode in which the diver in the water is supplied from the dive location with compressed gas for breathing and is in voice communication with the tender on the surface. This definition is based upon the requirements outlined in the Occupational Safety and Health Administration’s Code of Federal Regulations. (29 CFR 1910 Subpart T) This federal law outlines the criteria for all commercial diving. The surface-supplied diving mode requires gear and techniques that are not introduced in recreational diver training. This text was designed by the Tennessee Aquarium Diving Control Board to introduce Aquarium divers to the fundamental principles associated with surface-supplied diving. This text should be accompanied by proper practical training, as outlined in Appendix A, to promote safe surface-supplied diving under the auspice of the Tennessee Aquarium. Figure 1 – Secret Reef Dive Show- A primary use of surface-supplied diving at the Tennessee Aquarium. i Introduction There are numerous advantages to surface-supplied diving that make it an excellent choice for many diving operations. First, the diver has the benefit of an unlimited air supply. With a surface-supplied diving system, a diver can theoretically stay underwater forever. Of course, in reality, there are comfort, thermal, and decompression limits. For deep technical diving, a surface-supplied rig relieves the diver of the need to carry numerous stage bottles. -
User Manual for Amron International, Inc. Model 2820A and 2825A Two
User Manual For Amron International, Inc. Model 2820A and 2825A Two Diver Communicator S/N ____________________ 1380 Aspen Way, Vista California 92081-8349 United States of America Phone: (760) 208-6500 Fax (760) 599-3857 Email: [email protected] Web: www.amronintl.com This manual and the information contained herein are provided for use as an operation and maintenance guide. No license or rights to manufacture, reproduce, or sell either the manual or articles described herein are given. Amron International, Inc. reserves the right to change specifications without notice. Copyright© 2017 Amron International, Inc. 2820A AND 2825A TWO DIVER COMMUNICATOR USER MANUAL TABLE OF CONTENTS 1 INTRODUCTION AND SPECIFICATIONS .......................................................................................... 1 1.1 INTRODUCTION ........................................................................................................................... 1 1.2 ELECTRICAL SPECIFICATIONS ................................................................................................ 1 1.3 MECHANICAL SPECIFICATIONS ............................................................................................... 2 1.4 AMCOM II MODEL 2820A DIVER COMMUNICATOR ................................................................ 3 1.5 AMCOM II MODEL 2825A DIVER COMMUNICATOR ................................................................ 4 2 LIMITED WARRANTY AND SERVICE POLICY ................................................................................. -
Enabling Tracking & Diver Communications
Enabling Tracking & Diver Communications Ioseba Tena UDT 2019 Introduction to Sonardyne Leading independent provider of underwater acoustic, inertial, optical and sonar technology 70+ >275 >45 The number of Sonardyne The age of our 10,000 countries where employees worldwide company Transducer we operate manufactured each year 10mm 156,000 Positioning accuracy of 6G Total square footage acoustic of our facilities technology 500Mb/s 12,000m The speed we How deep our can transfer data equipment can operate subsea 100% 24/7 Deep water fields where 80% Support any Sonardyne technology is Percentage of time you need it used products we export Enabling Tracking and Diver Communication Over 45 years of experience Enabling Tracking and Diver Communication Dead-reckoning/DGPS (U.S. Navy photo by Mass Communication Specialist 2nd Class Tyler Thompson/Released) Enabling Tracking and Diver Communication Can we leverage commercial work? Enabling Tracking and Diver Communication Can we leverage commercial work? Enabling Tracking and Diver Communication How does USBL work? Ultra-Short BaseLine positioning systems We can track calculate the position of multiple targets subsea target by in sequence measuring the range and bearing of a transponder from the vessel Enabling Tracking and Diver Communication Can we leverage commercial work? Sonardyne Wideband® 2 Track Exchange Data USBL Enabling Tracking and Diver Communication Smaller foot print for divers Enabling Tracking and Diver Communication Smaller foot print for divers Battery: 95% Status: Green Mission: -
Stepping Into Rebreather Rebreather Diving
SSteptepping into rebreather diving By Paul Beenaround Alex had always been interested in learning to dive with the new breed of closed circuit rebreather’s that had appeared in recent years, so when he was suddenly faced with the choice of a dance weekend in chilly Munich or a week learning to dive with them in the Red Sea it wasn’t a hard decision to make. He was soon on his way with Easyjet flying over the Swiss Alps en-route for Sharm el sheik. Everything went very smoothly and he had soon settled down in the Camel hotel, a slightly upmarket one in the centre of Sharm which was not far from the Red Sea College where he would be doing his rebreather course. The next day he met Sherif, an impish Egyptian who was going to be his mentor for the combined basic and advanced four day course. After some classroom work he was shown the intricate workings of the Poseidon MK6 rebreather, the only one recognised by PADI for recreational sports divers on their recently introduced rebreather course. It was a very complex piece of kit, largely controlled by computer software, which took away the risk of diver error. This is unlike many other versions on the market that had caused accidents and deaths, usually through the diver making a mistake. As nice as it was to know that it was keeping him alive, the Poseidon rebreather’s had had many software problems that largely prevented you either starting a dive or necessitated aborting a dive halfway through for often non-existent faults. -
OCEANIC ·.ENGINEERING Sociel=Y
. : . ': R1..�t et',i.,.\ t< •. �IEEE OCEANIC ·.ENGINEERING SOCIEl=Y ""' 1'11*"* * ...* IEEE OCEANIC ENGINEERING SOCIETY President Vice President, East Coast Vice President, West Coast Treasurer Secretary STANLEY G. CHAMBERLAIN ANTHONY I. ELLER LLOYD Z. MAUDLIN EDWARD W. EARLY JOSEPH CZIKA Raytheon Co. Code 130 Lloyd Z. Maudlin Assoc. 4919 N.E. 93rd St. The Analytical Sciences Submarine Signal Division NORDA Liaison Office 5461 Toyon Rd. Seattle, WA 98115 Corp. Box 360 800 North Quincy St. San Diego, CA 92115 (206) 543-9825 1700 North Moore St. Portsmouth, RI 02871 Arlington, VA 22217 (619) 265-9292 (H) Suite 1220 (401) 847-8000Ext. 442' (202) 696-4951 (619) 474-2214 (0) Arlington, VA 22209 (703} 558-7400 Jr. Past President Membership Development Chapters Awards and Fellows Nominations DONALD M. BOLLE DA YID E. WEISSMAN ARTHUR S. WESTNEAT,JR. DONALD M. BOLLE DONALD M. BOLLE College of Eng. Phys. Sci. Dept.of Eng. & Computer Sci. Wadleigh Falls Rd. RD#! College of Eng. Phys. Sci. Packard Labs #19 123 Adams Hall Newmarket, NH 03857 Packard Labs #19 Lehigh Univ. Hofstra Univ. (603} 659-2195 Lehigh Univ. Bethlehem, PA 18105 Hempstead, NY 11550 Bethlehem, PA 18105 (215) 861-4025 (516) 560-5546 (215} 861-4025 Constitution and Bylaws Sr. Past President Meetings Committee LLOYD Z. MAUDLIN ANTHONY I. ELLER (East) JOSEPH CZIKA Lloyd Z. Maudlin Assoc. LLOYD Z. MAUDLIN (West} 5461 Toyon Rd. San Diego, CA 92115 (714) 265-9292 IEEE Oceanic Engineering Society News/el/er is published quarterly by the Oceanic Engineering Society of the Institute of Electrical and Electronics Engineers, Inc. -
SM2 DX300 Saturation Diving System
SM2 DX300 Saturation Diving System DESCRIPTION Year Built : 2010 Manufacturer : Divex Asia Pacific Classification Society : Lloyds Register Compliance Standards : IMCA D018 & D024 Rev.1 Design Standard : Lloyds Rules & Regulations for the Construction & Classification of Submersibles & Underwater systems, December 1989 Capacity : 12 man Depth Rating : 300msw Design Pressure : 30 bar Design Temperature : -18 to +66 deg C DIVE CONTROL SURFACE COMPRESSION CHAMBERS Housed within a purpose Built 7m x 3m x 3m insulated with air conditioned container • DDC 1 - 6 man Living Chamber (ML Volume : 20.7 m3) comprising of; • DDC 2 - 3 man Living Chamber (Volume : 20.9 m3) • Dive gas Supply Panel. • DDC 3 - 3 man Twin Lock Living Chamber (EL Volume : 8.3 m3, ML Volume : 12.7 m3) • Diver gas reclaim control panel. • Medical Locks and Bell clamp with mechanical interlock system. • Analox G22 O2 and G30 CO2 monitoring systems. • Chamber internal outfitted with BIBS, HCU, scrubbers and lighting. • Bell Control Systems. • Supplied with PPO2 meters and lung scrubbers. • Bell hot water monitoring system. • Bell and Diver Video & unscrambler communications systems. HYPERBARIC RESCUE CHAMBER • OTS Through Water Emergency communications systems. • Gantry launch and recovery system. • Bell and Diver audio/ video recording suite. • HRC internal volume : 16 m3 • Fixed and Portable Breathing Appratus. • Gas Distribution Control panel. • Equipped with Emergency Lights, Smoke/ Heat Detector & Portable Fire Extinguishers. • Onboard Emergency Gas Cylinders. • Safe-Ox oxygen monitoring system with audio visual alarm. • HRC Emergency Power Battery. • 3 KVA UPS Power Supply Units. • Chamber internal outfitted with BIBS, HCU, scrubbers and lighting. • Supplied with PPO2 meters, EPIRB, strobe lights, survival suits, lung scrubbers and food LIFE SUPPORT CONTROL ration. -
EPA National Dive Safety Program 2015 Annual Report
Environmental Protection Agency National Dive Safety Program 2015 Annual Report Jed Campbell, former Director, EPA National Diver Training Program May 30, 2016 Executive Summary The U.S. Environmental Protection Agency (EPA) conducts a wide range of diving activities for regional and national programs. Diving is conducted in rivers, lakes, harbors, and the open ocean to support monitoring, research, and emergency response efforts. The EPA administers diving activities under guidelines established through the EPA Diving Safety Management Program, and in compliance with the Occupational Safety and Health Administration (OSHA) regulations. This report has been developed in response to the requirements of EPA’s Diving Safety Policy. The EPA’s National Diving Safety Program conducted 959 scientific, training and proficiency dives in FY2015, involving nine EPA dive units and 64 divers. This report describes how the program is administered nationally, and what activities each EPA dive unit undertakes. Questions regarding this report or about the EPA Diving Safety Program should be directed to: Alan Humphrey, Chairman EPA Diving Safety Program Phone: (609) 865-4546 E-mail: [email protected] 2 Introduction This report is provided to the Environmental Protection Agency’s (EPA) Safety and Sustainability Division (formerly SHMED) in accordance with EPA’s Dive Safety Policy. This policy and EPA’s Diving Safety Manual (April, 2016 Version 1.3) can be viewed online at: https://www.epa.gov/sites/production/files/2016-04/documents/epa-diving-safety-manual- 2016.pdf This report is a summary of the EPA’s National Diving Safety Program (NDSP) activities from October 1, 2014, through September 30, 2015. -
Excursionsand Diving Adventures
Fishing, Water Sports, Excursions and Diving Adventures Come and join us and experience the incredible range of aquatic activities you can enjoy at Niyama Private Islands. We have high-speed exhilarating adventures to excite you. Wind- powered high intensity sports to propel you across the water! Adventurous fishing trips to catch a magnificent fish for your table! Amazing world-class dive sites awaiting your exploration! Sky-scraping excitement parasailing with a breathtaking bird’s eye view of the stunning islands below you! We offer exciting trips and excursions to discover the fantastic marine life and top side beauty of this amazing archipelago. Snorkel near and far reefs with the resident marine biologist, experience the beauty and freedom of scuba diving for the first time or visit uninhabited islands and isolated Maldivian communities on a voyage of discovery. Then later, when you are looking for more sedate water-based activities, why not rent a kayak and paddle gently around our shallow, protected lagoon or relax in the sun as your captain takes you on a private silent journey by catamaran. Whether you are looking for speed, excitement, relaxation, marine beauty or an opportunity to create that private vision of paradise you have in your mind, then if it is water related, FLOAT can provide it for you. Please contact FLOAT on: Ext. 1270 or Ext. 1395 SCUBA diving Diving At FLOAT, we are simply fanatical about scuba diving. Our aim is to ensure you have a fantastic diving experience during your stay here at Niyama Private Islands. We are blessed with all the necessary elements to create this for you – stunning marine life, fantastic dive sites, warm water and wonderful weather. -
Diver Detection Sonar System
Diver Detection Sonar System Product Code: 5510-01 Key Features Track & classify Single or multi-head networked systems Low false alarm rate Integration 3rd party security systems Fixed, temporary or expeditionary deployment Easy to use Overview The Diver Detection Sonar System is a single or multi-head active sonar Features system designed to automatically detect and track underwater and surface threats, principally divers, scuba or closed circuit, with or Identifies & classifies targets without propulsion aids, surface swimmers and unmanned underwater vehicles. Single or multi-head systems It will identify targets at ranges of up to 1,200 metres, depending on environmental conditions and product variant. 900 metres range for divers. Low power consumption 70 watts per sonar head It is small and lightweight so is quick to deploy from a boat, install in a port or fix along a coastline - providing you with an instant underwater security shield. Low false alarm rate Easy to use, security personnel do not need to be sonar experts to use it Maximum depth rating 50 metres once it is set up, it can be left to run autonomously. Can be Integrated with other It can be configured to meet the needs of commercial and infrastructure security systems facility protection projects as a standalone security sensor or integrated with third party C2 (Command and Control) security systems. It can be networked sonar, allowing entire waterfronts can be protected using a single operator station [email protected] | www.wg-plc.com | +44 1295 756300 1 Westminster Group Plc, Westminster House, Blacklocks Hill, Banbury, Oxfordshire, OX17 2BS, United Kingdom Diver Detection Sonar System Applications The practicality of the Diver Detection Sonar makes the system a realistic option for protecting a wide range of maritime assets: - Expeditionary - Warfare units in overseas ports are widely recognised as the most visible and vulnerable of targets.