(AD). Ali. 2322232 12 Patent Application Publication Aug
Total Page:16
File Type:pdf, Size:1020Kb
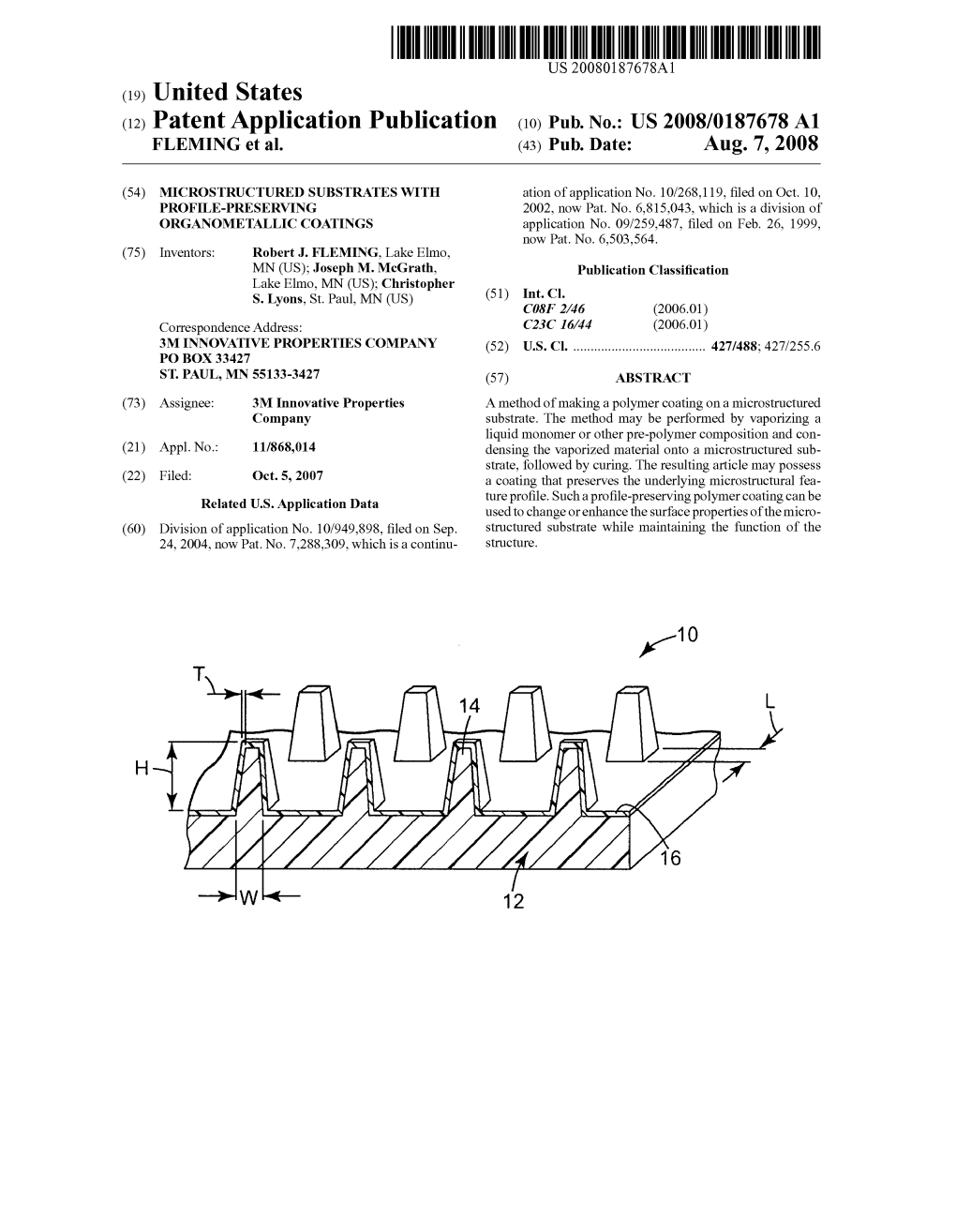
Load more
Recommended publications
-
Preparation and Characterization of Magnetic Hollow Glass Microspheres by Electroless Plating
id4520328 pdfMachine by Broadgun Software - a great PDF writer! - a great PDF creator! - http://www.pdfmachine.com http://www.broadgun.com March 2010 ISSN : 0974 - 7486 Volume 6 Issue 1 An Indian Journal Trade Science Inc. MMaatteerriiaallss SScciieennccee Full Paper MSAIJ, 6(1), 2010 [47-51] Preparation and characterization of magnetic hollow glass microspheres by electroless plating Wen-Bin Yang*, Xiao-Hong Tang, Xiao-Ping Hu, Chao Wang, Yuan-Lin Zhou School of Materials Science and Engineering, Southwest University of Science and Technology, Mianyang 621010, (P. R. CHINA) E-mail : [email protected] Received: 7th January, 2010 ; Accepted: 17th January, 2010 ABSTRACT KEYWORDS Magnetic hollow glass microspheres (HGM) were prepared by electroless Hollow glass microsphere; plating technique. Morphology, composition, structure, infrared radiation Electroless plating; and magnetic property of hollow glass microspheres before and after plat- Magnetic; ing were characterized by SEM, EDS, XPS, XRD, IR and VSM, respectively. Preparation; ìm The results showed that Ni-P plating, composed of particles of 1~2 Characterization. diameters, was uniformly coated on surfaces of HGM. Because of the exist- ence of Ni-P plating, peak intensity of the plated HGM in IR and XRD were lower than those before. Since the plated HGM own anti-infrared radiation and magnetic property, they are useful in some special areas. 2010 Trade Science Inc. - INDIA INTRODUCTION ing[8-12]. Due to spheric shape and low density of HGMs, it is very difficult to deposit a continuous and uniform Hollow glass microsphere (HGM) is a kind of ma- coating on the surface of HGMs. terial with many advantages, such as low density, huge Electroless plating owns many advantages, such as surface area, excellent thermal resistance, high wearing low cost, easy formation of continuous and uniform resistance and fine fluidity, so it has been widely used in coating on surface of substrate with complex shape, plastic, rubber, paint and coating systems[1-4]. -
Hollow Polymer Microcapsule Embedded Transparent and Heat-Insulating film† Cite This: RSC Adv.,2018,8, 9480 Chae Bin Kim, Nam-Ho You and Munju Goh *
RSC Advances View Article Online PAPER View Journal | View Issue Hollow polymer microcapsule embedded transparent and heat-insulating film† Cite this: RSC Adv.,2018,8, 9480 Chae Bin Kim, Nam-Ho You and Munju Goh * We herein report a facile and scalable approach to manufacturing optically transparent and heat-insulating films by incorporating hollow poly(methyl methacrylate) microcapsules into a transparent polymeric matrix. The microcapsule was prepared via emulsion polymerization. The size of the microcapsules could be easily controlled from 1to3mm by varying the polymerization time in a narrow size distribution. The microcapsules were then mixed with a UV-curable transparent liquid resin and cured by a subsequent light irradiation. The current approach could enhance the thermal barrier property of the films without a significant reduction in the optical transparency. The solid film possessing 30 wt% microcapsules, for Received 26th January 2018 example, exhibited a high visible light transmittance (80% as measured by UV-vis spectroscopy) and the Accepted 27th February 2018 thermal conductivity was reduced to 0.06 W mKÀ1, corresponding to 46% of the capsule free film. To DOI: 10.1039/c8ra00801a quantify and verify this result, theoretical models describing a heat transfer in a hollow microsphere Creative Commons Attribution 3.0 Unported Licence. rsc.li/rsc-advances composite were used, and the model showed a good agreement with our experimental observations. 1. Introduction process ow including adjustment of the gas mixture securely is somewhat complicated and uneconomical.5 Also, the glazed To safely accommodate global increases in population and per windows may form cracks due to a thermal stress during the capita energy consumption, a signicant need for immediate usage. -
Glass Microspheres for Hydrogen Storage
Glass Microspheres for Hydrogen Storage James Shelby and Matthew Hall Alfred University Wed, May 25 Project ID # This presentation does not contain any proprietary or confidential information STP47 HOLLOW GLASS MICROSPHERES The concept of using hollow glass microspheres (HGM) as a hydrogen storage medium has been known for some time. Hydrogen diffuses through the thin wall of the HGM at elevated temperatures and pressures. The gas is then trapped upon cooling to room temperature. The ability of HGM to safely store compressed hydrogen gas is a major HYDROGEN-FILLED HOLLOW advantage. However, a traditional GLASS MICROSPHERE limitation of HGM has been the poor thermal conductivity of a packed bed of HGM; poor conduction of heat translates to unsuitably low release rates of hydrogen gas. 2 HOLLOW GLASS MICROSPHERES Previous work by Rapp and Shelby demonstrated that the release rate of hydrogen from a monolithic glass plate could be greatly accelerated by the radiation emitted from an infrared lamp. In order to effect this “photo-enhanced” outgassing, the glass was doped with an optically active element; in this case, 0.5 wt% Fe3O4 was used 3 OVERVIEW Timeline Barriers • Estimated start date: • Barriers addressed: May 2005 – Cost: HGM are currently made in tonnage quantities from low- cost raw materials Budget – Weight and volume: HGM are an ideal storage medium from • Total project funding the standpoint of weight – Durability: Provided that the for FY 05 glass membrane is not broken, HGM may be indefinitely used – AU: $50k for hydrogen storage -
Crystallization Kinetics of Chalcogenide Glasses
2 Crystallization Kinetics of Chalcogenide Glasses Abhay Kumar Singh Department of Physics, Banaras Hindu University, Varanasi, India 1. Introduction 1.1 Background of chalcogenides Chalcogenide glasses are disordered non crystalline materials which have pronounced tendency their atoms to link together to form link chain. Chalcogenide glasses can be obtained by mixing the chalcogen elements, viz, S, Se and Te with elements of the periodic table such as Ga, In, Si, Ge, Sn, As, Sb and Bi, Ag, Cd, Zn etc. In these glasses, short-range inter-atomic forces are predominantly covalent: strong in magnitude and highly directional, whereas weak van der Waals' forces contribute significantly to the medium-range order. The atomic bonding structure is, in general more rigid than that of organic polymers and more flexible than that of oxide glasses. Accordingly, the glass-transition temperatures and elastic properties lay in between those of these materials. Some metallic element containing chalcogenide glasses behave as (super) ionic conductors. These glasses also behave as semiconductors or, more strictly, they are a kind of amorphous semi-conductors with band gap energies of 1±3eV (Fritzsche, 1971). Commonly, chalcogenide glasses have much lower mechanical strength and thermal stability as compared to existing oxide glasses, but they have higher thermal expansion, refractive index, larger range of infrared transparency and higher order of optical non-linearity. It is difficult to define with accuracy when mankind first fabricated its own glass but sources demonstrate that it discovered 10,000 years back in time. It is also difficult to point in time, when the field of chalcogenide glasses started. -
Nanopatterning with Photonic Nanojets: Review and Perspectives in Biomedical Research
micromachines Review Nanopatterning with Photonic Nanojets: Review and Perspectives in Biomedical Research Salvatore Surdo 1,* , Martí Duocastella 1,2,* and Alberto Diaspro 1,3,* 1 Nanoscopy, Istituto Italiano di Tecnologia, Via Enrico Melen 83, Building B, 16152 Genoa, Italy 2 Department of Applied Physics, University of Barcelona, C/Martí i Franquès 1, 08028 Barcelona, Spain 3 Department of Physics, University of Genoa, Via Dodecaneso 33, 16146 Genova, Italy * Correspondence: [email protected] (S.S.); [email protected] (M.D.); [email protected] (A.D.) Abstract: Nanostructured surfaces and devices offer astounding possibilities for biomedical re- search, including cellular and molecular biology, diagnostics, and therapeutics. However, the wide implementation of these systems is currently limited by the lack of cost-effective and easy-to-use nanopatterning tools. A promising solution is to use optical methods based on photonic nanojets, namely, needle-like beams featuring a nanometric width. In this review, we survey the physics, engi- neering strategies, and recent implementations of photonic nanojets for high-throughput generation of arbitrary nanopatterns, along with applications in optics, electronics, mechanics, and biosensing. An outlook of the potential impact of nanopatterning technologies based on photonic nanojets in several relevant biomedical areas is also provided. Keywords: nanotechnology; lithography; laser direct-write; near field; subwavelength Citation: Surdo, S.; Duocastella, M.; 1. Introduction Diaspro, A. Nanopatterning with The ability to pattern a surface with tailored nanostructures, such as trenches, pil- Photonic Nanojets: Review and lars, and spirals, has led to significant advances in the field of biomedical research [1–3]. Perspectives in Biomedical Research. Nanoscale features provide access to unique mechanical, optical, and electronic phenom- Micromachines 2021, 12, 256. -
Processing of Hollow Glass Microspheres
Sci Eng Compos Mater 2021; 28:116–127 Research Article Olusegun A. Afolabi, Krishnan Kanny, and T. P Mohan* Processing of Hollow Glass Microspheres (HGM) filled Epoxy Syntactic Foam Composites with improved Structural Characteristics https://doi.org/10.1515/secm-2021-0011 This HGM is embedded in a polymer material to form syntac- Received Aug 10, 2020; accepted Nov 30, 2020 tic foam composites. The hollow particles may sometimes be in the form of metal, carbon, ceramics, or polymer [1, 3]. Abstract: The objective of this work is to improve the struc- Furthermore, thermoset resins such as epoxy are generally tural characteristics of hollow glass microsphere (HGM) used as a binder for combining of microballoons, which pro- filled epoxy syntactic foam composites with little voids con- duces composite material with improved properties. Com- tent and improved HGM dispersion in the composite. posite material developed from this combination is widely A modified degassing technique has been introduced dur- used in structural applications due to its low cost, excellent ing resin casting process of the HGM filled syntactic foam specific strength, and ease of processing [4, 5]. composites. The effect of HGM content volume fractions There is a need to produce a lightweight material for the (5-25%) on the degassing techniques was examined. The structural application that is economically friendly and fire syntactic foam composites were characterized by analysing retardant. Syntactic foams have been studied to fit into this structural morphology using Scanning Electron Microscopy aspect because they are known to be of good advantages (SEM), Transmission Electron Microscopy(TEM), and den- for construction purposes due to their reduced weight thus sity measurements (theoretical and experimental). -
Fracture Analysis of Glass Microsphere Filled Epoxy Resin Syntactic Foam
SCHOOL OF AEROSPACE, CIVIL AND MECHANICAL ENGINEERING UNIVERSITY COLLEGE UNIVERSITY OF NEW SOUTH WALES AUSTRALIAN DEFENCE FORCE ACADEMY FRACTURE ANALYSIS OF GLASS MICROSPHERE FILLED EPOXY RESIN SYNTACTIC FOAM MAJOR PETER YOUNG A thesis submitted for the degree of Masters of Engineering AMEC – 2691 AUGUST 2007 Thesis Supervisor: Dr Krishna Shankar Co - Supervisor: Dr Andrew Neely i ABSTRACT Hollow glass microspheres have been used extensively in the automotive and marine industries as an additive for reducing weight and saving material costs. They are also added to paints and other materials for their reflective properties. They have shown promise for weight critical applications, but have thus far resulted in materials with low fracture toughness and impact resistance when combined with thermosetting resins in syntactic foam. The advent of commercially available microspheres with a wide range of crushing strengths, densities and adhesive properties has given new impetus to research into syntactic foam with better fracture behaviour. Current research suggests that the beneficial effects on fracture and impact resistance gained by the addition of solid reinforcements such as rubber and ceramic particles are not seen with the addition of hollow glass microspheres. The research presented in this paper has examined the mechanisms for fracture resistance in glass microsphere filled epoxy (GMFE) syntactic foams, as well as determined the effect microsphere crushing strength and adhesion strength has on the material’s fracture toughness. The flexural properties of various GMFE have also been determined. GMFE were manufactured with varying microsphere volume fraction up to 50%, and with variances in microsphere crushing strength and adhesion. The specimens were tested for Mode I fracture toughness in a three point single edge notched bending setup as described in ASTM D5045 as well as a three point flexural setup as described in ASTM D790-3. -
The 12Th Pacific Rim Conference On
Hilton Waikoloa Village | Waikoloa, Hawaii, USA rld of Scie o nc Scan for meeting app. W e A CONFERENCE PROGRAM PACRIM a nd gy Technolo The 12th Pacific Rim Conference on Ceramic and Glass Technology including – Glass & Optical Materials Division Annual Meeting (GOMD 2017) May 21 – 26, 2017 PACRIM Partner Societies: The American Ceramic Society The Australian Ceramic Society The Ceramic Society of Japan The Chinese Ceramic Society ceramics.org/pacrim12 The Korean Ceramic Society Join Wiley and The American Ceramic Society at the 12th Pacific Rim Conference Including the Glass & Optical Materials Division Meeting JACerS Throughout 2017, we are celebrating the 100th anniversary of Celebrating the Journal of the American Ceramic Society. The most 100 Years of highly-respected global source for scholarly articles on ceramic Excellence materials research is enjoying its Centennial year and you can in 2017! JACerS: 1918–2017... learn all about it at wileyonlinelibrary.com/jacers100. and beyond This year at PACRIM/GOMD, take advantage of all these great offerings, plus more: • “So You Want to Get Published: A workshop for graduate students and young professionals” - led by Bill Fahrenholtz, Editor-in-Chief, Journal of the American Ceramic Society. - Monday, May 22, 2017, noon to 1:15 pm • Special Centennial Issue of JACerS available with unique articles and features picked by the editors • FREE sample copies of all 3 journals of the American Ceramic Society • Enjoy a 35% discount on all purchases at the Wiley booth • Meet with Wiley and ACerS -
Glass Microspheres Cam Mikro Kürecikleri
www.dergipark.gov.tr ISSN:2148-3736 El-Cezerî Fen ve Mühendislik Dergisi Cilt: 6, No: 3, 2019 (613-641) El-Cezerî Journal of Science and Engineering ECJSE Vol: 6, No: 3, 2019 (613-641) DOI :10.31202/ecjse.562013 Research / Paper Makale Glass Microspheres Bekir KARASU, İrem DEMİREL, Anıl ÖZTUVAN, Burak ÖZDEMİR Eskişehir Technical University, Faculty of Engineering, Department of Materials Science and Engineering, Eskişehir/ Türkiye [email protected] Received/Geliş: 08.05.2019 Accepted/Kabul: 25.06.2019 Abstract: Glass microspheres are microscopic spheres of glass manufactured for a wide variety of uses in thermal insulation coating, putty, plastic casting polyester, radome, synthetic foam, adhesives, printed circuit board substrate, bowling, fan blades, and caulking materials, emulsion explosives, golf, sealant, pipeline insulation materials, artificial marble, PVC, low density oil drilling, light cement etc. Glass microspheres are usually between 1 and 1000 micrometres in diameter, although the sizes can range from 100 nanometres to 5 millimetres in diameter. Microspheres are spherical particles that can be distinguished into two categories; solid or hollow. This paper presented a general overview of glass microspheres. Keywords: Glass microspheres, history, property, application, development. Cam Mikro Kürecikleri Öz: Cam mikro küreler, ısı izolasyon kaplaması, yapıştırıcı, polyester, radar, sentetik köpük, bağlayıcılar, elektronik devre altlıkları, üfleç bıçakları, sıvı patlayıcılar, bowling, golf, sızdırmazlık elemanı, boru hattı izolasyon malzemeleri, sunni mermer, PVC, düşük yoğunluklu deliciler, hafif çimento vb. alanlarda çok çeşitli kullanımlar için üretilmiş mikroskobik cam kürelerdir. Bunların çapı genellikle 1 ila 1000 mikrometre arasındadır. Ancak, boyutları 100 nanometre ile 5 milimetre arasında değişebilir. Mikro küreler, katı veya içi boş olmak üzere iki kategoriye ayrılabilirler. -
An Analysis of the Structure and Thermal Conductivity of Hollow Microsphere Filled Syntactic Foams
Civil and Environmental Engineering Vol. 15, Issue 1, 36-41, DOI: 10.2478/cee-2019-0006 AN ANALYSIS OF THE STRUCTURE AND THERMAL CONDUCTIVITY OF HOLLOW MICROSPHERE FILLED SYNTACTIC FOAMS Rositsa PETKOVA-SLIPETS 1,* , Penka ZLATEVA 2 1 Department of Civil Engineering, Faculty of Architecture, Varna Free University “Chernorizets Hrabar”, Resort Chaika, 9007 Varna, Bulgaria. 2 Department of Thermal Engineering, Shipbuilding Faculty, Technical University of Varna, Studentska Str.1, 9010 Varna, Bulgaria. * corresponding author: [email protected]. Abstract Keywords: Syntactic foams; The influence of types and parameters of hollow microspheres in the composition of syntactic foams on their structure and coefficient of Ceramic microspheres; thermal conductivity has been studied. By using structural and Glass microspheres; thermal analysis it has been found that the volume concentration and Infrared thermography; Thermal conductivity. the size of the ceramic and glass hollow microspheres have a strong impact on the density and thermophysical properties of the thin syntactic foams coatings. It has been shown that the best heat insulating properties belong to syntactic foam with composition of 60 µ vol. % ceramic microspheres with particle size of 1 - 40 m ( k = 0.029 · 2· W/m K, R = 0.008 (m K)/W) and with composition of 80 vol. % glass hollow microspheres with particle size of 9 - 25 µm ( k = 0.087 W/m ·K, R = 0.008 (m 2·K)/W). The results demonstrate that application of syntactic foams as thin insulating coatings is appropriate and they are an energy efficient material with number of benefits compare with the common thermal insulators. 1 Introduction Syntactic foams are a new and promising generation of materials, which could be used as thin- layer heat insulating coatings as well. -
Hollow Glass Microsphere Composites: Preparation and Properties
Hollow glass microsphere composites: preparation and properties Citation for published version (APA): Verweij, H., With, de, G., & Veeneman, D. (1985). Hollow glass microsphere composites: preparation and properties. Journal of Materials Science, 20(3), 1069-1078. https://doi.org/10.1007/BF00585751 DOI: 10.1007/BF00585751 Document status and date: Published: 01/01/1985 Document Version: Publisher’s PDF, also known as Version of Record (includes final page, issue and volume numbers) Please check the document version of this publication: • A submitted manuscript is the version of the article upon submission and before peer-review. There can be important differences between the submitted version and the official published version of record. People interested in the research are advised to contact the author for the final version of the publication, or visit the DOI to the publisher's website. • The final author version and the galley proof are versions of the publication after peer review. • The final published version features the final layout of the paper including the volume, issue and page numbers. Link to publication General rights Copyright and moral rights for the publications made accessible in the public portal are retained by the authors and/or other copyright owners and it is a condition of accessing publications that users recognise and abide by the legal requirements associated with these rights. • Users may download and print one copy of any publication from the public portal for the purpose of private study or research. • You may not further distribute the material or use it for any profit-making activity or commercial gain • You may freely distribute the URL identifying the publication in the public portal. -
Hollow Glass Microspheres for Plastics, Elastomers, and Adhesives Compounds Copyright © 2015 Elsevier Inc
11 Mixing and Dispersion of Hollow Glass Microsphere Products Stephanie Shira and Cary Buller Hollow glass microspheres have helped to revolutionize the area of polymer fillers with an extensive variety of glass microsphere offerings. A diversity of diameters and isostatic collapse strength varieties are available for a range of mixing, processing, and end-use solutions. The advantages offered by hollow glass microspheres are many, yet due to their unique aspect ratio, density, and chemical properties, they must be handled differently than typical mineral fillers, particularly in storage, formulating, metering, mixing, pumping, and weighing. Due to their ultra-low-density, hollow glass microspheres occupy up to 20 times the space for a given weight of a traditional filler. Also, due to their thin-shelled hollow nature, they may be broken by compression at constrain points, shear under areas of tight clearance, and impact at turns in transfer equipment. As a result of the above, one must beware to minimize the compression, impact, and shear forces upon the hollow glass microspheres to ensure they are not damaged during processing and transport. Hollow Glass Microsphere Transport to Mixer The first step involved in processing with hollow glass microspheres is getting them to the resin or polymer matrix. Dispensing hollow glass microspheres can be challenging, as using traditional dispensing machines can result in a significant glass microsphere breakage rate. Factors which impact the breakage rate when transporting hollow glass microspheres include material agitation methods, material viscosity, choice of pump, and temperature while incorporating hollow glass microspheres. One must be cautious of the electrostatic forces encountered when transporting hollow glass microspheres; piping should be grounded to ensure static control.