Shines Bright at SCA Östrand 24
Total Page:16
File Type:pdf, Size:1020Kb
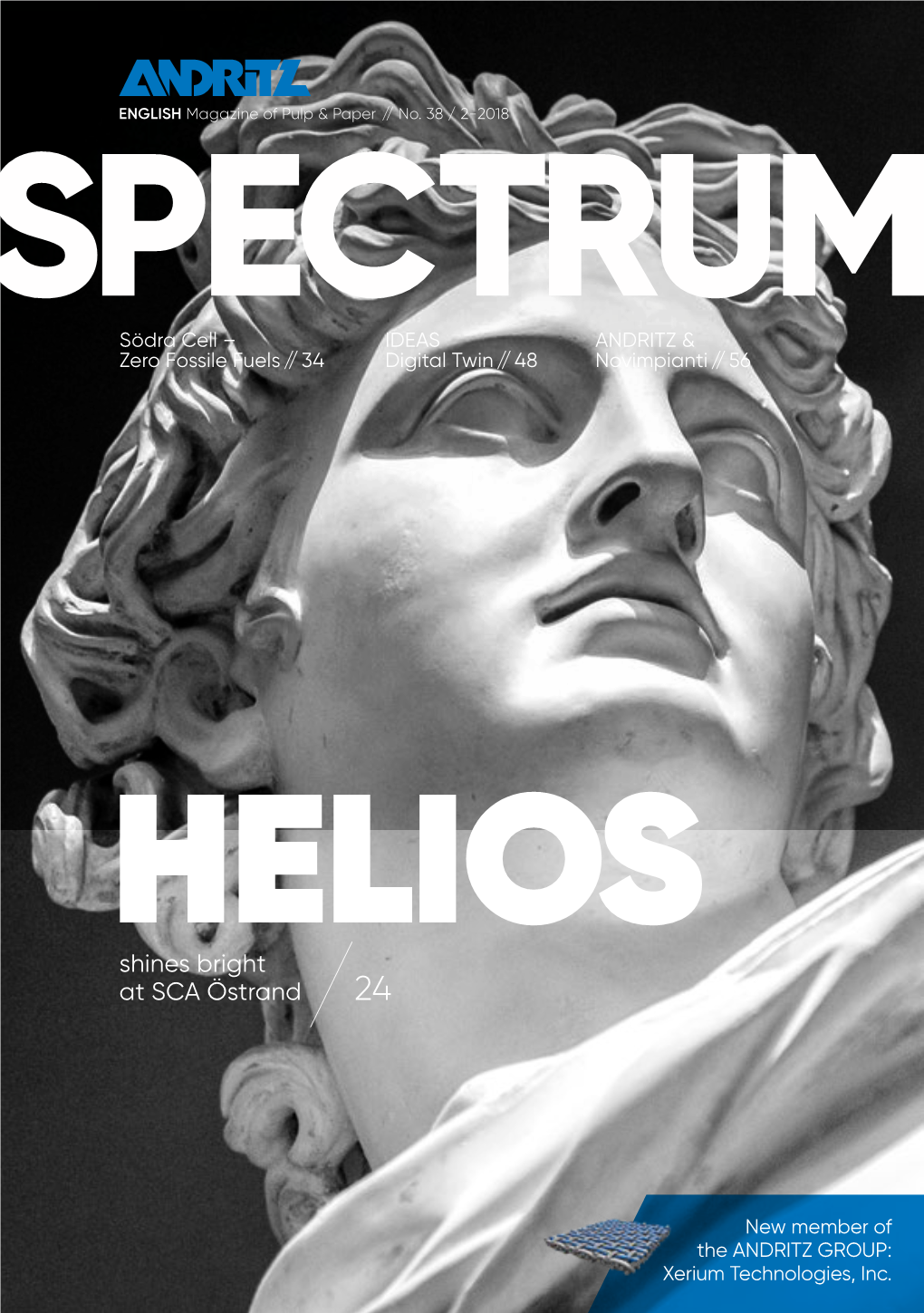
Load more
Recommended publications
-
Paper, Paperboard and Wood Pulp Markets, 2010-2011 Chapter 8
UNECE/FAO Forest Products Annual Market Review, 2010-2011 __________________________________________________________ 71 8 Paper, paperboard and woodpulp markets, 2010-2011 Lead Author, Peter Ince Contributing Authors, Eduard Akim, Bernard Lombard, Tomas Parik and Anastasia Tolmatsova Highlights • Paper and paperboard output rebounded along with overall industrial production in both Europe and the United States, but has not yet fully recovered to the peak levels of 2007-2008. • Generally more robust market conditions prevailed from 2010 to early 2011, with higher consumption and prices for most pulp, paper and paperboard commodities. • Prices reached a plateau by late 2010 and may have peaked in a cycle that began with rebound from the global financial crisis of 2008-2009; but prices still remained high in early 2011. • The Russian Federation is seeing an almost complete recovery of pulp and paper output to the levels that preceded the global financial crisis of 2008-2009. • European pulp, paper and paperboard output rebounded in 2010 after declining in 2008-2009, but the production levels before the crisis have not yet been reached. • Similarly, US production of pulp, paper and paperboard all rebounded from the sharp declines of 2008-2009, but production levels in 2010-2011 remained below previous cyclical peak levels. • A major project to expand use of larch was initiated in the Russian Federation, while wood pellet output and wood energy use also expanded in the Russian pulp and paper industry. • The market rebound coincides with expanding industry interest in the contributions of paper and paperboard products to green and sustainable development. • Green and sustainable product features such as use of renewable resources and product recyclability help support sustainability initiatives and an evolving symbiotic relationship between pulp and paper market development and the green economy. -
Holmen Paper Magazine Study
THE FUTURE OF MAGAZINES MARKET STUDY BY HOLMEN PAPER With the past decades’ rapid digital evolution, print media in almost all forms has taken a step back. As a company selling printing paper, Holmen Paper has observed and experienced this decline first hand. Newspapers was the first segment that suffered a rapid decrease in readers and is, as a result, no longer the largest end-use segment for graphical paper. Instead magazines now hold that position. Hence the future of the magazine market is crucial to the future of graphical paper. This is why we decided to conduct this study, where we look at how publishers meet the new challenges, how pricing is affected and how the readers demands are changing. TABLE OF CONTENTS MARKET SELLING PRICE 3 OVERVIEW 13 VS ADVERTISING How is the magazine market developing? What sets the price of a magazine? SHIFT IN MILLENNIALS’ BUSINESS READING 7 MODELS 16 HABITS Are the publishers’ changes radical enough? What does this group want in a printed magazine? Understanding where the magazine market is heading, helps you to gain insights and make sound future business decisions. This study therefore starts by looking at the current state of the magazine market, including historic developments as well as forecasted development. It then proceeds to look at the market from a publisher’s perspective, based on qualitative interviews with European publishers. The outcome is an extensive summary of the challenges that many publishers are experiencing, but also how they adapt their business models to to overcome them. The study also includes a thorough analysis of a large number of consumer magazines, where attributes such as price versus advertising density are investigated. -
Mechanical and Chemical Chip Pre-Treatment in Mechanical Pulp Production
Institutionen för fysik, kemi och biologi Mechanical and chemical chip pre-treatment in mechanical pulp production Malin Sjölin Braviken, Holmen Paper AB 2008-08-27 Supervisor Erik Persson Holmen Paper AB Examiner David Lawrence Master´s thesis LITH-IFM-EX--08/1950--SE 2 Institutionen för fysik, kemi och biologi Mekanisk och kemisk flisförbehandling i mekanisk massaproduktion Malin Sjölin Braviken, Holmen Paper AB 2008-08-27 Handledare Erik Persson Holmen Paper AB Examinator David Lawrence Examensarbete LITH-IFM-EX--08/1950--SE 3 4 Avdelning, institution Datum Division, Department 2008-08-27 Chemistry Department of Physics, Chemistry and Biology Linköping University Språk Rapporttyp ISBN Language Report category x Svenska/Swedish Licentiatavhandling ISRN: LITH-IFM-EX--08/1950--SE x Engelska/English Examensarbete _________________________________________________________________ C-uppsats D-uppsats Serietitel och serienummer ISSN ________________ Övrig rapport Title of series, numbering ______________________________ _____________ URL för elektronisk version Titel Mechanical and chemical chip pre-treatment in Mechanical pulping Författare Malin Sjölin Sammanfattning Abstract The mechanical pulping industry has been developing throughout the years, due to competitive prices in the electricity market and good accessibility of wood. This has made it possible for such and “expensive” process to further develop. Today, with increasing electricity prizes, it is of great interest to reduce electrical consumption in mechanical pulping industry, since the process consumes large amounts of electricity. Braviken paper mill is starting up a new thermomechanical pulping line, scheduled for start-up in August 2008, which aims to reduce electrical consumption. The new line will include chip pre-treatment equipment such as an impregnator, an Andrtiz Impressafiner (Screw press), a high intensity primary stage refines double disc (DD), and a new low consistency refiner (LC), significantly bigger than those earlier available on the market. -
Holmen Annual Report 2019 Contents 2019
2019Annual Report The Board of Directors and the CEO of The basis for the sustainability information Holmen Aktiebolag (publ.), corporate identity presented is the sustainability issues identified number 556001-3301, submit their annual as key in view of the materiality analysis report for the parent company and the Group conducted in 2018. The sustainability work for the 2019 financial year. The annual report is reported in accordance with the Global comprises the administration report (pages Reporting Initiative’s GRI guidelines at Core 2, 4–5, 10–11, 30–31, 33, 34–45, 77, 82–83) level. The Sustainability Report comprises and the financial statements, together with the pages 2, 5–9, 12–13, 16–38, 40–41, 44–45, notes and supplementary information (pages 47, 57, 60–62, 72, 75, 81–84, 88–89 and the 46–76). The statutory sustainability report GRI index on the website holmen.com. The in accordance with the Annual Accounts information is audited by a third party, see Act is included in the annual report (pages separate assurance report at holmen.com. 10–11, 30–31, 33, 36–38, 41). The Group’s consolidated income statement and balance This is a translation of the Swedish annual sheet and the parent company’s income report of Holmen Aktiebolag (publ.). In the statement and balance sheet will be adopted event of inconsistency between the English at the Annual General Meeting. and the Swedish versions, the Swedish version shall prevail. Holmen in brief The trees that grow, the water and paper at our mills. And even the bark our way of managing the forest brings that rushes down the mighty and sawdust is put to use, as bioenergy. -
Annual Report 2012 Including Sustainability Report (Publ) • P.O
Annual report 2012 including sustainability report 2012 report Annual 2 012 Annual report including sustainability report Holmen AB (publ) • P.O. Box 5407, SE-114 84 STOCKHOLM, SWEDEN Tel +46 8 666 21 00 • Fax +46 8 666 21 30 • E-mail [email protected] • www.holmen.com • ID No. 556001-3301 • Registered office Stockholm BRAVIKEN PAPER MILL Raw materials: Spruce pulpwood and Contents recovered paper. Process: TMP and DIP. Products: MF Magazine, newsprint and telephone directory paper. The Board of Directors and the CEO of Holmen Aktiebolag (publ.), corporate identity number 556001-3301, submit their Production capacity: 750 000 tonnes/year. annual report for the parent company and the Group for the 2012 financial year. The annual report comprises pages Average no. of employees: 551. 4–88. The results of the year’s operations and the financial position of the parent company and the Group are presented in the administration report, pages 4–53, and the accompanying income statements and balance sheets, together with BRAVIKEN SAWMILL the notes and supplementary information. The Group’s income statement and balance sheet and the parent company’s Raw materials: Spruce saw logs. income statement and balance sheet will be submitted to the Annual General Meeting for adoption. Process: Sawmilling. Products: Spruce sawn timber. Production capacity: 550 000 m3/year. Average no. of employees: 94. CEO’s message 2 ANNUAL REPORT List of notes HALLSTA PAPER MILL Business operation 1. Accounting policies 64 Raw materials: Spruce pulpwood. The year in brief 4 2. Operating segment reporting 68 Process: TMP and groundwood pulp. 3. -
Magazine Recycling May Boom As New Technology Increases
Magazine Recycling May Boom as New Technology Increases Magazine publishers have long been locked in editorial and financial competition with their media brethren - newspapers. But in at least one respect, the competi- tion hasn’t even been close. While environmentalists and state legislatures have been successfulty exerting pres- sure on newspapers to print ever-more copies on recyc- led paper, the magazine in- dustry has largely escaped unscathed. That seem to be about to change. While newspaper publish- ers have been under regula- tory and consumer pressure for several years to concen- trate their attention on re- cycling efforts, their maga- stock into paper. zine counterparts are only newsprint become available. There is a great deal of beginning to feel the heat, Flotation technology, still interest,” said Rod Edwards, since until only recently has being developed in the U.S., is vice president of the Ameri- it been feasible to recycle now in use in only a handful can Paper Institute’s paper- most glossy magazine of mills around the country. board group. “Magazine stock back into reuse. That number is headed for a publishers, distributors and FUTURE DEMAND. The mar- steep incline, and soon. wholesalers are all being ket for recycled magazine The flotation system is a asked leading questions on stock has existed for years, deinking system that has where they stand on recycl- but it has been limited to been used for a long time ing ethics. And this, in my uses in the paperboard in- in Europe and Japan. It is a opinion, comes up faster dustry, which has employed substitute for the long-stand- and faster to the surface recycled magazine paper in ing washing procedure used since Earth Day.” producing boxes and home- by U.S. -
ANNUAL REPORT 2016 3 a Forest Forest Active and Sustainable Forestry Is Conducted on Over a Million Hectares of Owner with Productive Forest Land Owned by Holmen
Annual Report Forest Paperboard Paper Wood products Renewable energy 2016 Contents This is Holmen 4 The year in brief 5 Strategy and targets 6 CEO’s message 8 Operations in 2016 10 A sustainable business 12 Forest 14 The Board of Directors and the CEO of Holmen Renewable energy 16 Aktiebolag (publ.), corporate identity number 556001-3301, submit their annual report for the Paperboard 18 parent company and the Group for the 2016 financial year. The annual report comprises the Paper 20 administration report (pages 4–5, 10–11, 27–29, Wood products 22 32–41, 70, 74–75) and the financial statements, together with the notes and supplementary Environment 24 information (pages 42–69). The Group’s income statement and balance sheet and the parent Employees 28 company’s income statement and balance sheet A sustainable future 30 will be submitted to the Annual General Meeting for adoption. Corporate governance report 32 The basis for the sustainability information Risk management 36 presented is the sustainability issues identified as key in view of the business that Holmen conducts. Shareholder information 40 The sustainability work is reported in accordance with the Global Reporting Initiative’s GRI G4 guidelines at Core level. The Sustainability Report Financial statements 42 comprises pages 7,12–13, 24–31, 37, 80–81, the GRI index on the website holmen.com and Notes 48 the pages on holmen.com as set out in the GRI index. The information is audited by a third party, Proposed appropriation of profits 70 see separate assurance report at holmen.com. Auditor’s report 71 Review of Sustainability Report 73 Board of Directors 74 Group management 76 Key figures 77 Ten-year review, finance 78 Five-year review, sustainability 80 Definitions and glossary 82 Calendar 83 This is a translation of the Swedish annual report of Holmen Aktiebolag (publ.). -
Evaluation & Improvement of Surface Properties of Newsprint
G C C EVALUATION & IMPROVEMENT OF SURFACE PROPERTIES OF NEWSPRINT ,,- MANUFACTURED FROM RECYCLED c FIBERS (CESS PROJECT) L (. C <, ( L \. f \ , ( CENTRAL PULP & PAPER RESEARCH INSTITUTE SAHARANPUR - 247001 (U.P.) EVALUATION & IMPROVEMENT OF SURFACE PROPERTIES OF NEWSPRINT MANUFACTURED FROM RECYCLED FIBERS (CESS PROJECT) Based on the work of Dr. Y. V. Sood, P.C. Pande Sanjay Tyagi, R. Neethikumar, Arti Pandey, Nisha, Indranil Payra, Renu Tyagi, T. Johri, & Shobit Marwah CENTRAL PULP & PAPER RESEARCH INSTITUTE SAHARANPUR - 247001 (U.P.) ACKNOWLEDGEMENT The authors are thankful to Dr. T. K. Roy, Officiating Director, Central Pulp & Paper Research Institute for useful technical discussions during the preparation of the final report. The management of Central Pulp & Paper Research Institute is thankful to the management of MIs Rolex Paper Mills Ltd., MIs Ajanta Paper Mills Ltd., MIs Sri Ramdas Paper Boards Pvt Ltd., MIs Sreen Sri Papers Ltd., MIs Nelsun Paper Mills Ltd., MIs Cosboard Industries Ltd., MIs Shakumbhari Straw Products Ltd., MIs Pragati Papers Ltd. & MIs Delta Paper Mills Ltd. for their cooperation during the course of the investigation of this project. EXECUTIVE SUMMARY Due to lack of suitable fibrous raw material, India for the last few decades -has been importing about 50% (±10 %) of its requirement of newsprint. The scenario is slowly changing as the recycling of waste paper is gaining momentum and this substantially improve the production of indigenous newsprint and reduce the imports in near future~At present, a large number of small and medium paper mills based on waste paper are manufacturing newsprint. Only few of these mills are able to meet the minimum quality standard. -
This Is Norske Skog in Words and Numbers
This is Norske Skog in words and numbers. Norske Skog is a leading Norwegian industrial company which focu- ses on these core areas: printing paper for newspapers and maga- zines, bleached sulphate pulp, and wood-based building materials. The Group has about 5,800 employees, and its operating income in 1996 was NOK 13,265 million. 78% of its income came from export markets, primarily in Europe, but also in the US and the Far East. The Group operates 23 companies in Norway, one mill in Austria and one in France. Its activities are organized in fourAreas: Paper, Fibre, Building Materials and Resources. In printing paper, Norske Skog is one of the world's leading suppliers, with capacity of 2.3 million tonnes in a market that totals about 50 million tonnes. Norske Skog is the third largest manufactu- rer of printing paper in Europe, and the world's fifth largest news- print producer. The pulp sold by the Group is used in the production of printing paper, fine paper and tissue. Norske Skog Bygg AS is Norway's largest producer of building materials: sawn timber for building purposes, board for the building and furniture industries, and flooring products. Since its foundation in 1962, Norske Skog has grown rapidly through mergers with other companies, and major investments in new mills, both in Norway and abroad. Since 1990 the Group has in- creased its printing paper capacity by one million tonnes, or just over 70%. Norske Skog has a sound financial basis, with total assets of NOK 16,623 million, and an equity capital ratio of 45,9%. -
Introduction to Stock Prep Refining Introduction to Stock Prep Refining 2016 Edition
Introduction to Stock Prep Refining Introduction to Stock Prep Refining 2016 Edition Table of Contents Page 1. Introduction . 3 2. Trees, Wood and Fiber . 4 3. Pulping for Paper & Paperboard Manufacturing . 8 4. Structure of Paper & Role of Refining . 11 5. Pulp Quality Measurements . 14 6. Paper Quality Measurements . 17 7. Theory of Refining: i) Qualitative Analysis . 20 ii) Quantitative Analysis . 23 8. Refiner Plate Selection: i) Correct Amount of Refining (Specific Energy Input) . 25 ii) Correct Intensity of Refining (Specific Edge Load) . 27 9. Flow Considerations in a Stock Preparation Refiner . 30 10. Conclusion . 31 Appendix A – No load power in a stock prep refiner . 32 Appendix B – Flow considerations in a stock prep refiner . 34 Appendix C – Case study and sample calculations . 40 2 1. Introduction The purpose of this manual is to present an easy to understand description of the stock preparation refin- ing process. Useful methods for analyzing the process will be presented, together with guidelines for the proper selection of refiner fillings and operation of refiners. It is difficult to learn about pulp refining without first knowing something about the overall process of papermaking. This introductory manual will provide a very brief discussion of the process of converting trees into finished paper products. To include such a broad scope of information requires a certain degree of simplification. Nevertheless, the big picture is very helpful when considering pulp refining applications, identifying process problems and recognizing the real economic opportunities of an optimized system. The refining technologist must learn how to select refiner fillings and operate refiners so as to optimize the performance of the paper being produced using available raw materials. -
Press Release
Press release 19 November 2014 New product reduces newsprint capacity Holmen Paper is launching a new product in the SC segment in spring 2015, which will reduce the company’s production of newsprint. “This new initiative will quickly bring about a significant change in newsprint volumes,” comments sales and marketing director Karolina Svensson. Intensive preparations are under way on PM 53 at Braviken Paper Mill outside Norrköping, Sweden, for the conversion work that is scheduled to begin at the end of January next year. PM 53 is Braviken’s largest machine, with an annual capacity of 310 000 tonnes for the current product mix. The machine produces Holmen NEWS (newsprint) and Holmen XLNT – the uncoated magazine paper that makes up Holmen Paper’s single biggest product family. It is the production of newsprint for export outside the Nordic region that is going to be reduced when the new product is introduced next year. “We are predicting a rapid rise in volumes for the new product,” says Karolina Svensson. “The aim is to achieve an annualised running rate for production and sales of more than 100 000 tonnes by the end of 2015. “We’ll be reducing the production of newsprint at a corresponding rate, and in the longer term we’ll only keep the volumes to supply our local markets in Scandinavia.” Holmen Paper judges that its own measures, combined with previously announced capacity closures elsewhere in the market, will considerably improve capacity utilisation for newsprint in 2015. For more information, please contact: Jonas Lindell, Communications Manager, tel. +46 (0)70-323 20 13 E-mail [email protected] This is information that Holmen AB is obliged to disclose under the Swedish Securities Market Act and the Swedish Financial Instruments Trading Act. -
Forest Paperboard Paper Wood Products Renewable Energy the Year in Brief 3 Holmen in Brief CEO’S Message 4
Forest Paperboard Paper Wood Products Renewable Energy The year in brief 3 Holmen in brief CEO’s message 4 Strategy and targets 6 Forest 10 Paperboard 12 Paper 14 Forest Wood Products 16 Active and sustainable forestry is Renewable Energy 18 conducted on over a million hectares A sustainable business 20 of productive forest land owned by Holmen. The annual harvest amounts Environment 22 to 3 million cubic metres. Employees 24 UN Sustainable Development Goals 26 Corporate governance report 28 Paperboard Risk management 32 Paperboard in the premium consumer Shareholder information 36 packaging segment. Production, which takes place at one Swedish Financial statements 38 and one UK mill, amounts to 0.5 million tonnes a year. Notes 44 Proposed appropriation of profits 66 Auditor’s report 67 Review of Sustainability Report 69 Paper Board of Directors 70 Paper for magazines, books and Group management 72 advertising. The two Swedish mills produce a combined total Key figures 73 of 1 million tonnes per year. Ten-year review, finance 74 Five-year review, sustainability 76 Definitions, glossary and references 78 Wood Products Calendar 79 Wood products for the joinery and construction industries. The annual production at three The Board of Directors and the CEO of Holmen Aktiebolag (publ.), corporate sawmills amounts to just under identity number 556001-3301, submit their annual report for the parent 1 million cubic metres. The company and the Group for the 2018 financial year. The annual report com- prises the administration report (pages 2–3, 8–9, 23–24, 28–37, 66, 70–71) by-products are used in the and the financial statements, together with the notes and supplementary Group’s paperboard and information (pages 38–65).