Investigation of Mixture Formation and Combustion in an Ethanol Direct Injection Plus Gasoline Port Injection (EDI+GPI) Engine
Total Page:16
File Type:pdf, Size:1020Kb
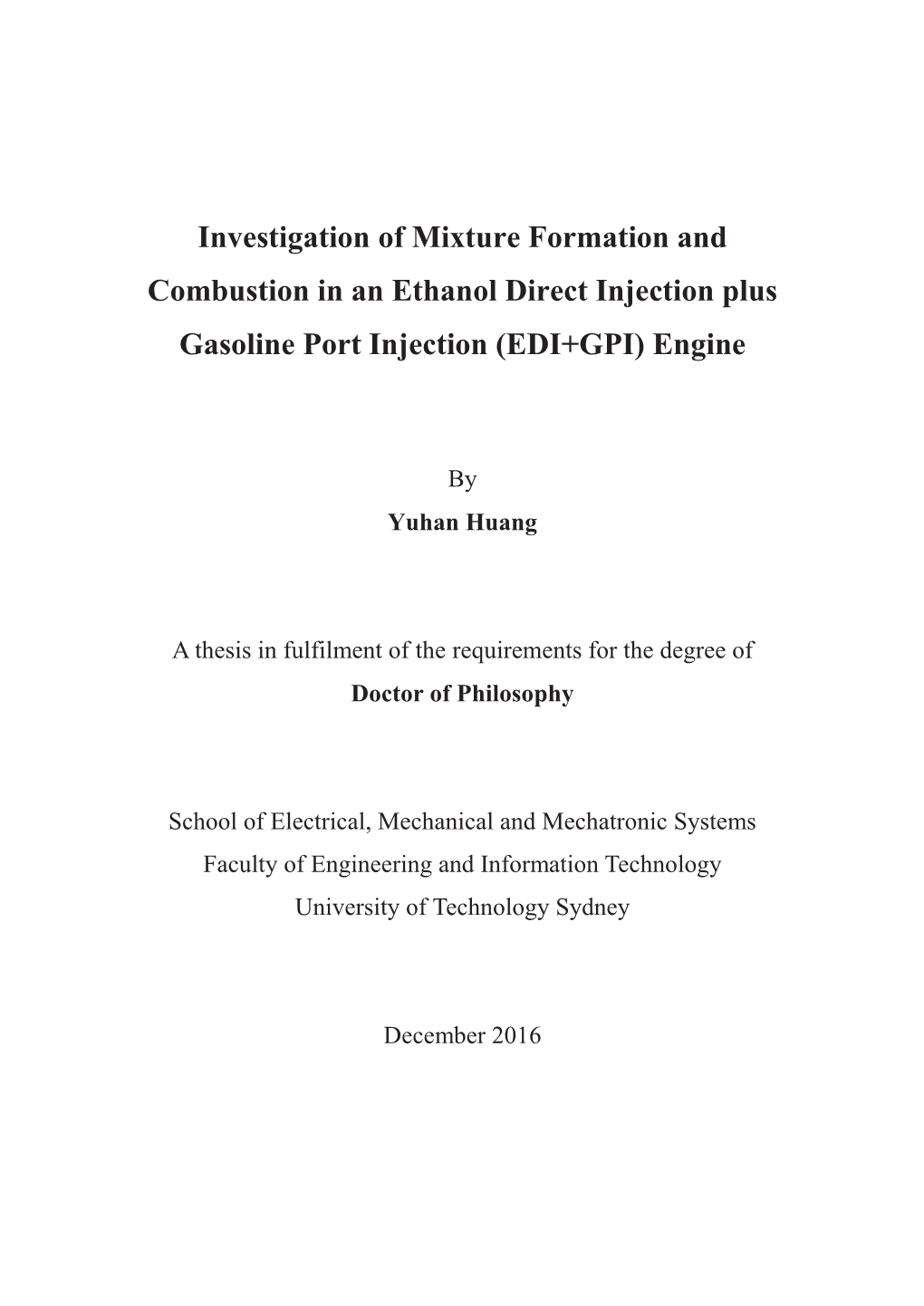
Load more
Recommended publications
-
Zenith Replacement Carburetors
not print a list price for their carburetors, each dealer can set Zenith Replacement their own prices. Check a few dealers to see who has the bet- Carburetors ter price. These referenced Zenith part numbers were supplied by by Phil Peters Mike Farmer, Application Engineer at Zenith in Bristol, VA, s a follow up to the recent reprinting of the Special where the factory is now located. The Zeniths are a newer Interest Auto article from 1977 (Fall & Winter, 2015) design universal carburetor which means they have multiple Aand the continuing requests for modern replacement fuel, choke, and throttle hook up locations. In addition, there carburetors, I have assembled the following chart of all our are air horn adaptors for modern air filters. They are com- Durant/Star/Flint/etc. engines with corresponding specifica- patible with modern ethanol fuels, have a robust inlet port, tions and replacement Zenith part numbers. As pointed out multiple venturi sizes and “back suction economizer” for part by Norm Toone and other knowledgeable members, there throttle fuel economy. were a number of errors concerning the model numbers and OEM brands in the SIA article. This chart represents The models that were picked for our engines were de- the collective input from a number of helpful members and termined by maximum air flow at 2,200 RPM for the 2 3/8” was done with engine model numbers. Car models were mounts (SAE size #1) and 2,600 RPM for the 2 11/16” not always related to calendar years. Differences in produc- mounts (SAE size #2). -
The Trilobe Engine Project Greensteam
The Trilobe Engine Project Greensteam Michael DeLessio 4/19/2020 – 8/31/2020 Table of Contents Introduction ................................................................................................................................................... 2 The Trilobe Engine ................................................................................................................................... 2 Computer Design Model ............................................................................................................................... 3 Research Topics and Design Challenges ...................................................................................................... 4 Two Stroke Engines .................................................................................................................................. 4 The Trilobe Cam ....................................................................................................................................... 5 The Flywheel ............................................................................................................................................ 6 Other “Tri” Cams ...................................................................................................................................... 7 The Tristar ............................................................................................................................................. 8 The Asymmetrical Trilobe ................................................................................................................... -
Estimation of Fuel Economy Improvement in Gasoline Vehicle Using Cylinder Deactivation
energies Article Estimation of Fuel Economy Improvement in Gasoline Vehicle Using Cylinder Deactivation Nankyu Lee 1 , Jinil Park 1,*, Jonghwa Lee 1 , Kyoungseok Park 2, Myoungsik Choi 3 and Wongyu Kim 3 1 Department of Mechanical Engineering, Ajou University, Suwon 16499, Gyeonggi, Korea; [email protected] (N.L.); [email protected] (J.L.) 2 Department of Mechanical System Engineering, Kumho National Institute of Technology, Gumi 39177, Gyeongbuk, Korea; [email protected] 3 Hyundai Motor Company, 150, Hyundaiyeonguso-ro, Jangdeok-ri, Namyang-eup, Hwaseong-si 18280, Gyeonggi-do, Korea; [email protected] (M.C.); [email protected] (W.K.) * Correspondence: [email protected]; Tel.: +82-31-219-2337 Received: 8 October 2018; Accepted: 6 November 2018; Published: 8 November 2018 Abstract: Cylinder deactivation is a fuel economy improvement technology that has attracted particular attention recently. The currently produced cylinder deactivation engines utilize fixed-type cylinder deactivation in which only a fixed number of cylinders are deactivated. As fixed-type cylinder deactivation has some shortcomings, variable-type cylinder deactivation with no limit on the number of deactivated cylinders is under research. For variable-type cylinder deactivation, control is more complicated and production cost is higher than fixed-type cylinder deactivation. Therefore, it is necessary to select the cylinder deactivation control method considering both advantages and disadvantages of the two control methods. In this study, a fuel economy prediction simulation model was created using the measurement data of various vehicles with engine displacements of 1.0–5.0 L. The fuel economy improvement of fixed-type cylinder deactivation was compared with that of variable-type cylinder deactivation using the created simulation. -
Flow Testing and Evaluation
About MAX BMW Motorcycles Machine Shop Articles: 2017 brings MAX BMW's Machine Shop to full operational status and a series of articles on our individual machines and operational practices. In this series, we highlight some of the specific equipment, tools and jigs we have developed to come to the exacting standards of ultimate quality, attention to detail, accurate measurements and swift turnaround of customer jobs. ARTICLE 3 April 21, 2017 Flow Testing and Evaluation In this article, we are going to start looking at a few performance services that are available at MAX BMW. Specifically, we’ll look at an overview of cylinder head performance through flow testing and evaluation. With any machine shop work, the proper tools are essential when exacting results and a high standard of quality are required. One of those tools is our Super Flow SF600 cylinder head flow bench. 2 When building an engine where more power is desired, everything in the engine must be considered to be working together as a package. The starting point for any project is always understanding its intended use. Are you building a stock engine, a high horse power street bike or perhaps a track-only bike that sees sustained high rpms and loads? Once this is determined, the details to achieve these goals fall into place. Specifically, engine displacement, cam selection, cylinder head improvements such as valve size and material, valve seat machining and port design are all areas that can be modified and tuned for performance improvements. Even though there have been volumes written on air flow theory and port design, this will be a brief overview to help understand how it can all be measured, modified and tested to prove effective results. -
Air Filter Sizing
SSeeccoonndd SSttrriikkee The Newsletter for the Superformance Owners Group January 17, 2008 / September 5, 2011 Volume 8, Number 1 SECOND STRIKE CARBURETOR CALCULATOR The Carburetor Controlling the airflow introduces the throttle plate assembly. Metering the fuel requires measuring the airflow and measuring the airflow introduces the venturi. Metering the fuel flow introduces boosters. The high flow velocity requirement constrains the size of the air passages. These obstructions cause a pressure drop, a necessary consequence of proper carburetor function. Carburetors are sized by airflow, airflow at 5% pressure drop for four-barrels, 10% for two-barrels. This means that the price for a properly sized four-barrel is a 5% pressure loss and a corresponding 5% horsepower loss. The important thing to remember is that carburetors are sized to provide balanced performance across the entire driving range, not just peak horsepower. When designing low and mid range metering, the carburetor engineers assume airflow conditions for a properly As with everything in the engine, airflow is power. sized carburetor - one sized for 5% loss at the power peak. Carburetors are a key to airflow. As with any component, the key to best all around performance is to pick parts that match Selecting a larger carburetor than recommended will reduce your performance goal and each other – carburetor, intake, pressure losses at high rpm and may help top end horsepower, heads, exhaust, cam, displacement, rpm range, and bottom but will have lower flow velocity at low rpm and poor end. metering and mixing with a loss in low and mid range power and drivability. -
Calculating Compression Ratio/Engine Displacement Practice Small Power and Equipment Secti
Calculating Compression Ratio/Engine Displacement Practice Small Power and Equipment Section 1 – Compression Ratio Calculate the compression ratio for a small engine given the following information (SHOW ALL WORK!!!): Bore of the cylinder (B) = 105 mm Stroke of the engine (S) = 90 mm Compressed Gasket Thickness (Gt) = 3.5 mm Bore of the gasket (Gb) = 93.5 mm Volume of the combustion chamber in the cylinder head (Vcc) = 50 ml Gross Piston Head Volume (Vphg) = 80 ml Piston Depression (Pd) = 25 mm Item Symbol Formula Formula Result Applied Depression Vdp B x B x Pd x F Volume Net Piston Vph Vphg - Vdp Head Volume Gasket Volume Vg Gb x Gb x Gt x F TDC Volume Vtdc Vcc + Vg + Vph Swept Volum Vsw B x B x S x F e BDC Volume Vbdc Vtdc + Vsw Compression CR Vbdc / Vtdc Ratio Calculating Compression Ratio/Engine Displacement Practice Small Power and Equipment Bore of the cylinder (B) = 110 mm Stroke of the engine (S) = 75 mm Compressed Gasket Thickness (Gt) = 1.5 mm Bore of the gasket (Gb) = 80.5 mm Volume of the combustion chamber in the cylinder head (Vcc) = 50 ml Gross Piston Head Volume (Vphg) = 88 ml Piston Depression (Pd) = 15 mm Item Symbol Formula Formula Result Applied Depression Vdp B x B x Pd x F Volume Net Piston Vph Vphg - Vdp Head Volume Gasket Volume Vg Gb x Gb x Gt x F TDC Volume Vtdc Vcc + Vg + Vph Swept Volum Vsw B x B x S x F e BDC Volume Vbdc Vtdc + Vsw Compression CR Vbdc / Vtdc Ratio Section 2 – Engine Displacement (5 points each = 10 points) Calculate the engine displacement given the following information (SHOW ALL WORK!!!). -
Lecture 8 3Rd Semester M Tech
Lecture 8 3rd Semester M Tech. Mechanical Systems Design Mechanical Engineering Department Subject: Advanced Engine Design I/C Prof M Marouf Wani Topic: Design Of Diesel Passenger Car Engine A Compression Ignition Engine Design Objective: Estimate Engine Displacement Volume Required – 05-10-2020 Numerical Example: Q1 Design a Diesel Passenger Car Engine. The engine is to have a rated power of 100 KW at 4200 rpm. Solution: The engine has to be designed for a passenger car run by diesel fuel This is a C.I engine based Passenger Car Given Data: Rated Power = 100 KW Rated Speed = 4200 rpm The above Rated Speed suits a diesel passenger car engine for the following reasons: Consider the equation for Newton’s Second Law of Motion for a reciprocating piston . F = m*a Reason 1 Lean Operation of CI engines. A/F = 18 - 70 1. For pollution control the CI engines are operated lean. 2. So CI engines have larger displacement volume as compared to SI engines for same power. 3. Larger displacement volume will make the geometrical size and therefore the mass of the piston for CI engine larger. 4. Assuming that the force F acting on the piston is same for both the SI and CI engines. 5. Since the term mass m of the piston on the right hand side of the Newton’s second law of motion has a higher value for CI engines, so the second term acceleration, a should be brought down. 6. So the crankshaft rotational speed N is decreased. 1 Note : Inertia is associated with mass only. -
DEPARTMENT of TRANSPORTATION National
DEPARTMENT OF TRANSPORTATION National Highway Traffic Safety Administration 49 CFR Parts 531 and 533 [Docket No. NHTSA-2008-0069] Passenger Car Average Fuel Economy Standards--Model Years 2008-2020 and Light Truck Average Fuel Economy Standards--Model Years 2008-2020; Request for Product Plan Information AGENCY: National Highway Traffic Safety Administration (NHTSA), Department of Transportation (DOT). ACTION: Request for Comments SUMMARY: The purpose of this request for comments is to acquire new and updated information regarding vehicle manufacturers’ future product plans to assist the agency in analyzing the proposed passenger car and light truck corporate average fuel economy (CAFE) standards as required by the Energy Policy and Conservation Act, as amended by the Energy Independence and Security Act (EISA) of 2007, P.L. 110-140. This proposal is discussed in a companion notice published today. DATES: Comments must be received on or before [insert date 60 days after publication in the Federal Register]. ADDRESSES: You may submit comments [identified by Docket No. NHTSA-2008- 0069] by any of the following methods: • Federal eRulemaking Portal: Go to http://www.regulations.gov. Follow the online instructions for submitting comments. 1 • Mail: Docket Management Facility: U.S. Department of Transportation, 1200 New Jersey Avenue, SE, West Building Ground Floor, Room W12- 140, Washington, DC 20590. • Hand Delivery or Courier: West Building Ground Floor, Room W12-140, 1200 New Jersey Avenue, SE, between 9 am and 5 pm ET, Monday through Friday, except Federal holidays. Telephone: 1-800-647-5527. • Fax: 202-493-2251 Instructions: All submissions must include the agency name and docket number for this proposed collection of information. -
Jennings: Two-Stroke Tuner's Handbook
Two-Stroke TUNER’S HANDBOOK By Gordon Jennings Illustrations by the author Copyright © 1973 by Gordon Jennings Compiled for reprint © 2007 by Ken i PREFACE Many years have passed since Gordon Jennings first published this manual. Its 2007 and although there have been huge technological changes the basics are still the basics. There is a huge interest in vintage snowmobiles and their “simple” two stroke power plants of yesteryear. There is a wealth of knowledge contained in this manual. Let’s journey back to 1973 and read the book that was the two stroke bible of that era. Decades have passed since I hung around with John and Jim. John and I worked for the same corporation and I found a 500 triple Kawasaki for him at a reasonable price. He converted it into a drag bike, modified the engine completely and added mikuni carbs and tuned pipes. John borrowed Jim’s copy of the ‘Two Stoke Tuner’s Handbook” and used it and tips from “Fast by Gast” to create one fast bike. John kept his 500 until he retired and moved to the coast in 2005. The whereabouts of Wild Jim, his 750 Kawasaki drag bike and the only copy of ‘Two Stoke Tuner’s Handbook” that I have ever seen is a complete mystery. I recently acquired a 1980 Polaris TXL and am digging into the inner workings of the engine. I wanted a copy of this manual but wasn’t willing to wait for a copy to show up on EBay. Happily, a search of the internet finally hit on a Word version of the manual. -
Introduction to Internal Combustion Engines
k Chapter 1 Introduction to Internal Combustion Engines 1.1 INTRODUCTION The goals of this textbook are to describe how internal combustion engines work and provide insight into how engine performance can be modeled and analyzed. The main focus of the text is the application of the thermal sciences, including thermodynamics, combus- tion, fluid mechanics, and heat transfer, to internal combustion engines. An aspect upon which we will put considerable emphasis is the development of idealized models to repre- sent the actual features of an operating engine. Engineers use the methods and analyses introduced in the textbook to calculate the performance of proposed engine designs and to parameterize and correlate engines experiments. With the advent of high-speed computers and advanced measurement tech- niques, today’s internal combustion engine design process has evolved from being purely k k empirical to a rigorous semi-empirical process in which computer based engineering software is used to evaluate the performance of a proposed engine design even before the engine is built and tested. In addition to detailed analysis, the textbook contains numerous computer routines for calculating the various thermal and mechanical parameters that describe internal combustion engine operation. In this chapter we discuss the engineering parameters, such as thermal efficiency, mean effective pressure, and specific fuel consumption, that are used to characterize the over- all performance of internal combustion engines. Major engine cycles, configurations, and geometries are also covered. The following chapters will apply the thermal science princi- ples to determine an internal combustion engine’s temperature and pressure profiles, work, volumetric efficiency, and exhaust emissions. -
Automotive Engine
AccessScience from McGraw-Hill Education Page 1 of 5 www.accessscience.com Automotive engine Contributed by: Donald L. Anglin Publication year: 2014 The component of the motor vehicle that converts the chemical energy in fuel into mechanical energy for power. The automotive engine also drives the generator and various accessories, such as the air-conditioning compressor and power-steering pump. See also: AUTOMOTIVE CLIMATE CONTROL ; AUTOMOTIVE ELECTRICAL SYSTEM ; AUTOMOTIVE STEERING . Early motor vehicles were powered by a variety of engines, including steam and gasoline, as well as by electric motors. The flexibility of the gasoline engine operating on the four-stroke Otto cycle soon made this engine predominant, and it remains the dominant automotive power plant. The basic modern automotive engine (see illustration ) is a gasoline- burning, liquid-cooled, spark-ignition, four-stroke-cycle, multicylinder engine. It has the intake and exhaust valves in the cylinder head, and electronically controlled ignition and fuel injection. See also: ENGINE . Otto-cycle engine An Otto-cycle engine is an internal combustion piston engine that may be designed to operate on either two strokes or four strokes of a piston that moves up and down in a cylinder. Generally, the automotive engine uses four strokes to convert chemical energy to mechanical energy through combustion of gasoline or similar hydrocarbon fuel. The heat produced is converted into mechanical work by pushing the piston down in the cylinder. A connecting rod attached to the piston transfers this energy to a rotating crankshaft. See also: GASOLINE ; INTERNAL COMBUSTION ENGINE ; OTTO CYCLE . Cylinder arrangement. Engines having from 1 to 16 cylinders in in-line, flat, horizontally opposed, or V-type cylinder arrangements have appeared in production vehicles, progressing from simple single-cylinder engines at the beginning of the twentieth century to complex V-12 and V-16 engines by the early 1930s. -
Fuel and Air Purge System for Diaphragm Carburetors
Europäisches Patentamt *EP001116873A2* (19) European Patent Office Office européen des brevets (11) EP 1 116 873 A2 (12) EUROPEAN PATENT APPLICATION (43) Date of publication: (51) Int Cl.7: F02M 17/04 18.07.2001 Bulletin 2001/29 (21) Application number: 01100447.0 (22) Date of filing: 08.01.2001 (84) Designated Contracting States: (72) Inventor: Pattullo, George M. AT BE CH CY DE DK ES FI FR GB GR IE IT LI LU Caro, MI 48723 (US) MC NL PT SE TR Designated Extension States: (74) Representative: Wehnert, Werner, Dipl.-Ing. AL LT LV MK RO SI Patentanwälte Hauck, Graalfs, Wehnert, Döring, Siemons et al (30) Priority: 13.01.2000 US 482690 Mozartstrasse 23 80336 München (DE) (71) Applicant: WALBRO CORPORATION Cass City, MI 48726 (US) (54) Fuel and air purge system for diaphragm carburetors (57) A method of reducing gaseous phase presence in the liquid fuel metering chamber of a diaphragm by providing a "High-Point Pick Up" hole positioned in the optimal metering chamber location (highest) to assure maximum purge evacuation of air and/or other gases prior to engine start-up and during running. This optimal location is dependent upon first determining, in advance of carburetor fuel feed circuitry and/or air purge system design, the orientation of the carburetor as mounted on the engine in its primary operator usage position, or so- called "standard operating position" (SOP). This SOP in turn is determined in the first instance by the engine manufacturer and/or the manufacturer of the portable engine-driven handheld appliance on which the engine is mounted.