US5241112.Pdf
Total Page:16
File Type:pdf, Size:1020Kb
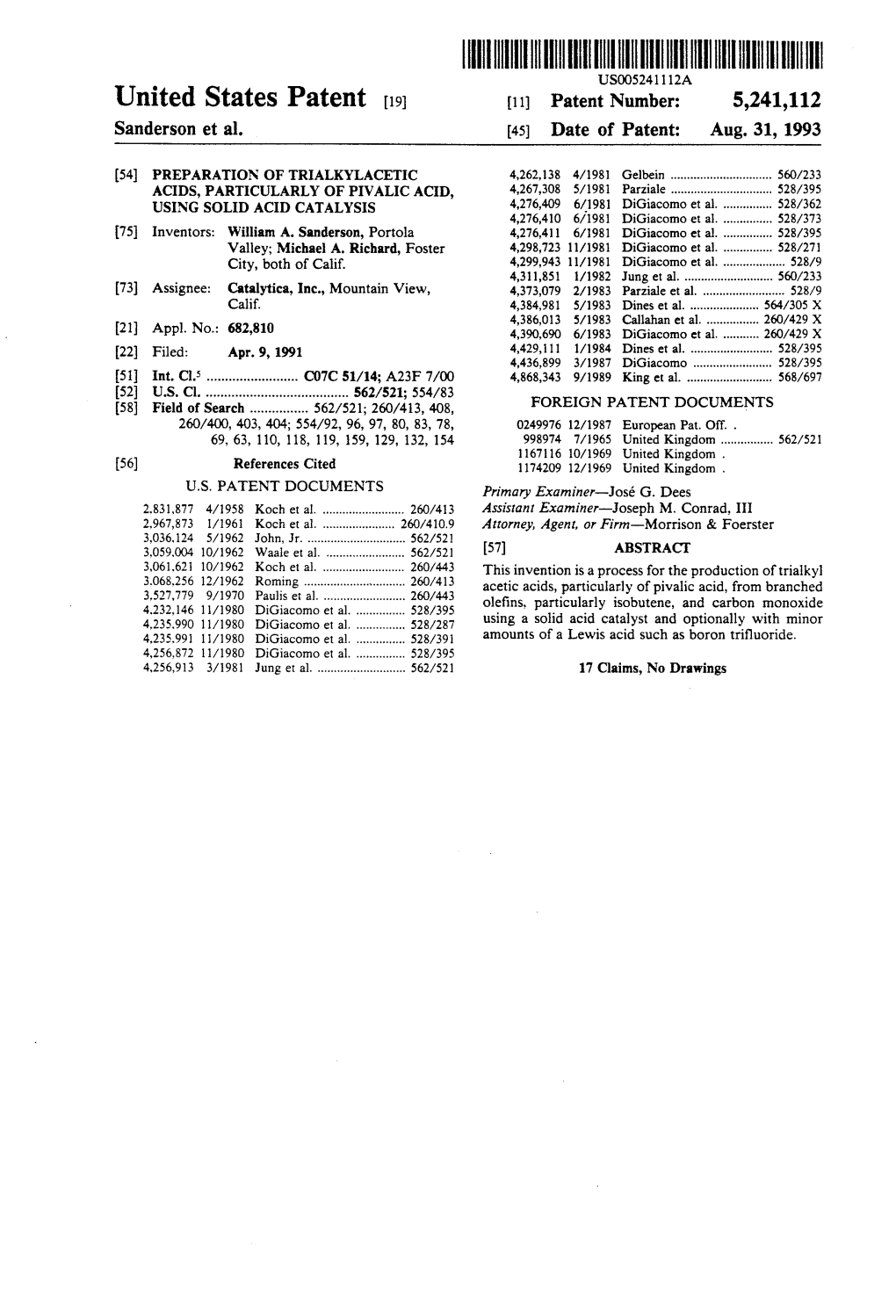
Load more
Recommended publications
-
United States Patent Office
3,455,998 United States Patent Office Patented July 15, 1969 2 tinuously or intermittently into the reaction mixture, e.g., 3,455,998 in the form of an acetylene stream loaded with Water WNYL ESTERS FROMACETYLENE AND vapor. CARBOXYLIC ACDS As the zinc salt component of the combination catalyst, Hans J. Arpe, Kohlkaul, Germany, assignor to Shell Oil use is preferably made of a zinc salt of the same carbox Company, New York, N.Y., a corporation of Delaware ylic acid as that to be vinylated. However, use may be No Drawing. Filed Mar. 20, 1967, Ser. No. 624,215 made of salts of other acids than of the acid to be Int, C. C07c 67/04, 67/00 vinylated. However, in the latter case, the anion of the U.S. C. 260-498 0 Claims acid is generally slowly exchanged for the anion of the IO acid being vinylated. These salts can readily be prepared ABSTRACT OF THE DISCLOSURE by reacting, e.g., zinc oxide, zinc hydroxide or zinc carbonate with the acid in a manner known per se. The Vinyl carboxylates are produced by liquid-phase re salt can either be prepared beforehand or allowed to form action of a carboxylic acid with acetylene in the presence in the reaction mixture itself. as catalyst of a zinc salt in combination with a metal-con 15 The liquid phase in which the vinylation is to be carried taining Lewis acid. out can be formed by the melt of the zinc carboxylate itself. It is, however, advantageous to use a high-boiling solvent, i.e. -
New Inhibitors of Methane Production by Rumen Micro-Organisms
Downloaded from 429 https://www.cambridge.org/core New inhibitors of methane production by rumen micro-organisms. Development and testing of inhibitors in vitro BY J. W. CZERKAWSKI AND GRACE BRECKENRIDGE . IP address: The Hannah Research Institute, Ayr KA6 5HL, Scotland 170.106.33.22 (Received 2 Yanuary 1975 - Accepted 9 May 1975) I. A procedure is described for assaying in vitro the activity of various inhibitors of methane production by rumen micro-organisms. , on 2. Methods of preparation of various inhibitors are described together with attempts to 30 Sep 2021 at 19:00:31 characterize these compounds by determining their physical properties (physical state, density, chromatographic behaviour), their hydrolysis by rumen contents and their relative potency as inhibitors. 3. The results of preliminary studies with trichloroethanol and its ester with pivalic acid are given. 4. The inhibitory activities of several groups of related compounds are reported. These include the polyhalogenated alcohols and their esters with pivalic acid, the esters of tri- , subject to the Cambridge Core terms of use, available at halogenated alcohols and monobasic fatty acids from C2to CISand the trihalogenated alcohol esters of dibasic acids. The results of experiments with esters of alcohols and polyhalogenated carboxylic and sulphonic acids are also given. 5. It is concluded that the mechanism of action of the inhibitors might be similar to that of known polyhalogenated methane analogues (e.g. chloroform). The relative activity of various compounds might be partly governed by the ease of their absorption into the microbial cells and by the extent to which the esters can be hydrolysed by rumen contents. -
Synthesis of Neoalkanes
Europalsches Patentamt European Patent Office @ Publication number: 0180 240 A1 Office europeen des brevets EUROPEAN PATENT APPLICATION @ Application number: 85113920.4 © mt. ci- c 07 C 1/22, C 07 C 1/253, C07C 9/18 @ Date of 31 .1 0.85 filing : // B01J23/80 ® Priority: 01.11.84 US 687173 @ Applicant: AIR PRODUCTS AND CHEMICALS, INC., P.O. Box 538, Allentown, Pennsylvania 18105 (US) @ Inventor : Butter, Stephen Allan, 2432 Pennsylvania ® Date of publication of application : 07.05.J Street, Allentown, PA 18104 (US) Bulletin 86/1 9 Inventor: StoH, llse, 220 W. Langhorne Avenue, Bethlehem, PA 18017 (US) @ Representative : Kador ft Partner, Corneliusstrasse 1 5, @ Designated Contracting States : BE DE FR QB NL D-8000 Mtinchen 5 (DE) @ Synthesis of neoalkanes. @ Neoalkanes of the formula R1R2R3CCH3 are synthesized by hydrogenation of a neoacid of the formula R1R2R3CCOOH or a neoalcohol of the formula R1R2R3CCH2OH, wherein R1, R2 and R3 are the same or different alkyl of 1-10 carbon atoms, at a temperature of 250-500 °C over a copper oxide/ zinc oxide catalyst. Technical Field This invention relates to processes for the synthesis of neoalkanes from corresponding neoacids or neoalcohols. Neoalkanes are compounds of the formula R1R2R3CCH3. Typically, each R is alkyl of 1-10 carbon atoms. The lowest member of this series of compounds, in which each R is methyl, is neopentane, (CH3)4C. Neopentane is of commercial interest because it is a condensible gas (b.p. +9°C), which can be used as a heat exchange fluid in solar panels. Neopentane occurs in concentra- tions below about 0.1% in refinery streams, so that its isolation from these sources usually is not economical. -
University of Illinois
UNIVERSITY OF ILLINOIS THIS IS TO CERTIFY THAT THE THESIS PREPARED UNDER MY SUPERVISION BY ENTITLED IS APPROVED BY ME AS FULFILLING THIS PART OF THE REQUIREMENTS FOR THE DEGREE OF. A pproved: *:'X T ‘ AD OF DEPARTMENT OF. O 1364 The Synthesis of Deuterium Labelled Precursors for Their Use in Mechanistic Studies of Chemical Vapor Deposition By Michael E. Smith Thesis for the Degree of Bachelor of Science in Chemistry College of Liberal Arts and Sciences University of Illinois Urbana, Illinois 1988 ACKNOWLEDGEMENTS This thesis is the culmination of three semesters of work in the Girolami group* I'd like to thank all of the members of the group for being supportive and always being there to answer my questions. I would especially like to thank the follwingt Jim Jensen for being a terrific source of advice and giving an undergraduate the chance to shoulder the load and do some real chemistry? Debbie Pollina for doing the groundwork for the chloride synthesis and pulling the magical Vielsmier reagent out of thin air (well, almost); Hans Gozum for teaching me the finer art of destructive chemistry and helping me get rid of my Austrian accent; and Dave Dempsey for making my excursions to 350B the stuff that legends are made of. Finally, my deepest thanks to Greg Girolami, who showed me what chemistry is all about, and helped put my feet firmly on the road to graduate school. TABLE OF CONTENTS Page Number Introduction 1 Results and Discussion 4 Experimental 10 Appendix* Use of AutoCAD Introduction 12 Menus 12 Display Capabilities 14 Drawing Modes 17 Editing 19 Hardcopy 20 Design Techniques 21 Conclusion 23 References 24 1 INTRODUCTION The synthesis of inorganic materials has traditionally involved high temperatures. -
Radioiodination Via Isotope Exchange in Pivalic Acid
AppL Radiat. 1sot. Vol. 37, No. 8, pp. 907-913, 1986 0883-2889•86 $3.00 + 0.00 Int. J. Radiat. AppL lnstrum, Part A Pergamon Journals Ltd Printed in Great Britain Radioiodination via Isotope Exchange in Pivalic Acid JAMEY P. WEICHERT, MARCIAN E, VAN DORT, MICHAEL P. GROZIAK, and RAYMOND E. COUNSELL* Departments of Medicinal Chemistry and Pharmacology, The University of Michigan, Ann Arbor, MI 48109, U.S.A. A variety of benzoic and aryl aliphatic mono and polyiodinated acids and esters (sterol, triglyceride) were radioiodinated in 55-99% radiochemical yield by isotope exchange with Naf25I in a melt of pivalic acid. In general, the reaction was complete in 1 h at 155°C with little or no substrate decompostion. High specific activity studies afforded 125I-labelediopanoic acid with a specific activity of over 700 Ci/mmol. Introduction Although isotope exchange of aliphatic iodides introduction of radioiodine into organic molecules is usually conducted in a refluxing solvent such as ~:an be accomplished by a variety of techniques acetone, methyl ethyl ketone (MEK), water, or depending on the structure of the compound to be ethanol, °) unactivated aryl iodides generally require labeled. Excellent reviews of radioiodination methods higher reaction temperatures to effect the exchange. I~ave recentlybeen reported/~'2~ Aromatic compounds Accordingly, high boiling solvents such as propylene possessing electron donating groups (e.g. phenols glycol have been utilized with some success. °~) In ~nd anilines) are easily radiolabeled by electrophilic another method, the. substrate and radioiodide are iodination in the presence of radioiodine, iodine reacted at elevated temperatures (100--200°C) in a raonochloride, chloramine-T, iodogen, etc/~) A "melt" fashion. -
Direct Synthesis of Amides from Nonactivated Carboxylic Acids Using Urea As Nitrogen Source and Cite This: Chem
Chemical Science View Article Online EDGE ARTICLE View Journal | View Issue Direct synthesis of amides from nonactivated carboxylic acids using urea as nitrogen source and Cite this: Chem. Sci., 2020, 11,5808 †‡ All publication charges for this article Mg(NO3)2 or imidazole as catalysts have been paid for by the Royal Society a b c a of Chemistry A. Rosie Chhatwal,§ Helen V. Lomax,§ A. John Blacker, * Jonathan M. J. Williams a and Patricia Marce´ * A new method for the direct synthesis of primary and secondary amides from carboxylic acids is described using Mg(NO3)2$6H2O or imidazole as a low-cost and readily available catalyst, and urea as a stable, and Received 4th March 2020 easy to manipulate nitrogen source. This methodology is particularly useful for the direct synthesis of Accepted 16th May 2020 primary and methyl amides avoiding the use of ammonia and methylamine gas which can be tedious to DOI: 10.1039/d0sc01317j manipulate. Furthermore, the transformation does not require the employment of coupling or activating rsc.li/chemical-science agents which are commonly required. Creative Commons Attribution 3.0 Unported Licence. Introduction have been recently reported.5,6,44,56–60 Transamination61–64 reac- tions to convert primary amides into more complex amides, and The importance of the amide functional group emerges from the acylation of amines to produce secondary amides are also their presence in many crucial compounds such as proteins, important transformations reported in this eld.65 fabrics, fertilizers, insecticides, plastics, drugs, and in a vast The direct synthesis of secondary amides from nonactivated number of synthetic structures. -
Enthalpies of Vaporization of Organic and Organometallic Compounds, 1880–2002
Enthalpies of Vaporization of Organic and Organometallic Compounds, 1880–2002 James S. Chickosa… Department of Chemistry, University of Missouri-St. Louis, St. Louis, Missouri 63121 William E. Acree, Jr.b… Department of Chemistry, University of North Texas, Denton, Texas 76203 ͑Received 17 June 2002; accepted 17 October 2002; published 21 April 2003͒ A compendium of vaporization enthalpies published within the period 1910–2002 is reported. A brief review of temperature adjustments of vaporization enthalpies from temperature of measurement to the standard reference temperature, 298.15 K, is included as are recently suggested reference materials. Vaporization enthalpies are included for organic, organo-metallic, and a few inorganic compounds. This compendium is the third in a series focusing on phase change enthalpies. Previous compendia focused on fusion and sublimation enthalpies. Sufficient data are presently available for many compounds that thermodynamic cycles can be constructed to evaluate the reliability of the measure- ments. A protocol for doing so is described. © 2003 American Institute of Physics. ͓DOI: 10.1063/1.1529214͔ Key words: compendium; enthalpies of condensation; evaporation; organic compounds; vaporization enthalpy. Contents inorganic compounds, 1880–2002. ............. 820 1. Introduction................................ 519 8. References to Tables 6 and 7.................. 853 2. Reference Materials for Vaporization Enthalpy Measurements.............................. 520 List of Figures 3. Heat Capacity Adjustments. ................. 520 1. A thermodynamic cycle for adjusting vaporization ϭ 4. Group Additivity Values for C (298.15 K) enthalpies to T 298.15 K.................... 521 pl 2. A hypothetical molecule illustrating the different Estimations................................ 521 hydrocarbon groups in estimating C ........... 523 5. A Thermochemical Cycle: Sublimation, p Vaporization, and Fusion Enthalpies........... -
Catalytic Pyrolysis of Aliphatic Carboxylic Acids Into Symmetric Ketones Over Ceria-Based Catalysts: Kinetics, Isotope Effect and Mechanism
catalysts Article Catalytic Pyrolysis of Aliphatic Carboxylic Acids into Symmetric Ketones over Ceria-Based Catalysts: Kinetics, Isotope Effect and Mechanism Tetiana Kulik 1,* , Borys Palianytsia 1 and Mats Larsson 2 1 Chuiko Institute of Surface Chemistry, NAS of Ukraine, 17 General Naumov Str., 03164 Kyiv, Ukraine; [email protected] 2 Department of Physics, AlbaNova University Center, Stockholm University, SE-106 91 Stockholm, Sweden; [email protected] * Correspondence: [email protected]; Tel.: +38-044-422-9676 Received: 29 November 2019; Accepted: 21 January 2020; Published: 3 February 2020 Abstract: Ketonization is a promising way for upgrading bio-derived carboxylic acids from pyrolysis bio-oils, waste oils, and fats to produce high value-added chemicals and biofuels. Therefore, an understanding of its mechanism can help to carry out the catalytic pyrolysis of biomass more efficiently. Here we show that temperature-programmed desorption mass spectrometry (TPD-MS) together with linear free energy relationships (LFERs) can be used to identify catalytic pyrolysis mechanisms. We report the kinetics of the catalytic pyrolysis of deuterated acetic acid and a reaction series of linear and branched fatty acids into symmetric ketones on the surfaces of ceria-based oxides. A structure–reactivity correlation between Taft’s steric substituent constants Es* and activation energies of ketonization indicates that this reaction is the sterically controlled reaction. Surface D3-n-acetates transform into deuterated acetone isotopomers with different yield, rate, E,, and deuterium kinetic isotope effect (DKIE). The obtained values of inverse DKIE together with the structure–reactivity correlation support a concerted mechanism over ceria-based catalysts. These results demonstrate that analysis of Taft’s correlations and using simple equation for estimation of DKIE from TPD-MS data are promising approaches for the study of catalytic pyrolysis mechanisms on a semi-quantitative level. -
United States Patent (19) 11 Patent Number: 4,528,400 Cryberg Et Al
United States Patent (19) 11 Patent Number: 4,528,400 Cryberg et al. (45) Date of Patent: Jul. 9, 1985 54) PREPARATION OF KETONES (56) References Cited U.S. PATENT DOCUMENTS (75) Inventors: Richard L. Cryberg, Chardon; 2,612,524 9/1952 Zellemoyer et al. ............... 568/397 Russell M. Bimber, Painesville, both 2,697,729 12/1954. Ohlson et al. ........... ... 568/397 of Ohio 3,075,016 1/1963 Hammerberg et al. ... 568/397 3,466,333 9/1969 Young et al. ........... ... 568/397 (73) Assignee: SDS Biotech Corporation, 3,574,703 4/1971 Hogemeyer et al. ... 568/397 Painesville, Ohio 4,224,252 9/1980 Kyo et al. ........................... 568/388 OTHER PUBLICATIONS 21 Appl. No.: 323,262 Thermal Behavior of Aliphatic and Alicyclic Ketones, Furukawa and Naruchi, Nihon Kagaku Zasshi (Journal 22) Filed: Nov. 20, 1981 of the Chemical Society of Japan, Pure Chemistry Sec tion), vol. 87, No. 10, (1966), pp. 1108-1110, (102-104). Primary Examiner-James H. Reamer Related U.S. Application Data Attorney, Agent, or Firm-John P. Hazzard; John J. Freer (63) Continuation-in-part of Ser. No. 159,309, Jun. 9, 1980, abandoned, which is a continuation of Ser. No. (57) ABSTRACT 876,334, Feb. 9, 1978, abandoned, which is a continua Disclosed is a method for the preparation of ketones by tion of Ser. No. 716,142, Aug. 20, 1976, abandoned. a catalytic vapor phase reaction of using reactants such as ketones with carboxylic acids and/or carboxylic acid 51) Int. Cl. .............................................. CO7C 45/48 precursors. An example of such a reaction is that of 52) U.S. -
Safety Assessment of Monoalkylglycol Dialkyl Acid Esters As Used in Cosmetics
Safety Assessment of Monoalkylglycol Dialkyl Acid Esters as Used in Cosmetics Status: Draft Final Report for Panel Review Release Date: August 18, 2017 Panel Meeting Date: September 11-12, 2017 The 2017 Cosmetic Ingredient Review Expert Panel members are: Chair, Wilma F. Bergfeld, M.D., F.A.C.P.; Donald V. Belsito, M.D.; Ronald A. Hill, Ph.D.; Curtis D. Klaassen, Ph.D.; Daniel C. Liebler, Ph.D.; James G. Marks, Jr., M.D.; Ronald C. Shank, Ph.D.; Thomas J. Slaga, Ph.D.; and Paul W. Snyder, D.V.M., Ph.D. The CIR Interim Director is Bart Heldreth, Ph.D. This report was prepared by Lillian C. Becker, Scientific Analyst/Writer. © Cosmetic Ingredient Review 1620 L Street, NW, Suite 1200 Washington, DC 20036-4702 ph 202.331.0651 fax 202.331.0088 [email protected] Commitment & Credibility since 1976 MEMORANDUM To: CIR Expert Panel and Liaisons From: Lillian C. Becker, M.S. Scientific Analyst and Writer Date: August 18, 2017 Subject: Safety Assessment of Monoalkylglycol Dialkyl Acid Esters as Used in Cosmetics Attached is the Draft Final Report of Monoalkylglycol Dialkyl Acid Esters as used in cosmetics. [magdae092017Rep] These ingredients are structurally related to each other as alkyl esters of monoalkyl diols that vary by type of diol and lengths of the fatty acid residues. In June 2017, the Panel concluded that 25 of the 28 ingredients are safe as used in cosmetics. The Panel also concluded that the data on 3 of the 28 ingredients are insufficient to come to a conclusion of safety. The data needs, as described in the December 2016 -
University of Groningen Mass Transfer Effects in the H2SO4
University of Groningen Mass transfer effects in the H2SO4 catalyzed pivalic acid synthesis Brilman, D.W.F.; Meesters, N.G.; Swaaij, W.P.M. van; Versteeg, Geert Published in: Catalysis Today DOI: 10.1016/S0920-5861(00)00618-0 IMPORTANT NOTE: You are advised to consult the publisher's version (publisher's PDF) if you wish to cite from it. Please check the document version below. Document Version Publisher's PDF, also known as Version of record Publication date: 2001 Link to publication in University of Groningen/UMCG research database Citation for published version (APA): Brilman, D. W. F., Meesters, N. G., Swaaij, W. P. M. V., & Versteeg, G. F. (2001). Mass transfer effects in the H2SO4 catalyzed pivalic acid synthesis. Catalysis Today, 66(2), 317-324. DOI: 10.1016/S0920- 5861(00)00618-0 Copyright Other than for strictly personal use, it is not permitted to download or to forward/distribute the text or part of it without the consent of the author(s) and/or copyright holder(s), unless the work is under an open content license (like Creative Commons). Take-down policy If you believe that this document breaches copyright please contact us providing details, and we will remove access to the work immediately and investigate your claim. Downloaded from the University of Groningen/UMCG research database (Pure): http://www.rug.nl/research/portal. For technical reasons the number of authors shown on this cover page is limited to 10 maximum. Download date: 11-02-2018 Catalysis Today 66 (2001) 317–324 Mass transfer effects in the H2SO4 catalyzed pivalic acid synthesis D.W.F. -
Kinetics of the Alkylation and Acylation of Nickel Dipivaloyimethide Kenneth Eugene Johnson Iowa State University
Iowa State University Capstones, Theses and Retrospective Theses and Dissertations Dissertations 1959 Kinetics of the alkylation and acylation of nickel dipivaloyimethide Kenneth Eugene Johnson Iowa State University Follow this and additional works at: https://lib.dr.iastate.edu/rtd Part of the Organic Chemistry Commons Recommended Citation Johnson, Kenneth Eugene, "Kinetics of the alkylation and acylation of nickel dipivaloyimethide " (1959). Retrospective Theses and Dissertations. 2181. https://lib.dr.iastate.edu/rtd/2181 This Dissertation is brought to you for free and open access by the Iowa State University Capstones, Theses and Dissertations at Iowa State University Digital Repository. It has been accepted for inclusion in Retrospective Theses and Dissertations by an authorized administrator of Iowa State University Digital Repository. For more information, please contact [email protected]. KINETICS OF THE ALKYLATION AND ACYLATION OF NICKEL DIPIVALOYmETHIDE Kenneth migene Johnson A Dissertation Submitted to the Graduate Faculty in Partial Fulfillment The Requirements for the Degree of DOCTOR OF PHILOSOPHY Major Subject: Organic Chemistry Approved: Signature was redacted for privacy. In Change of Major Work Signature was redacted for privacy. Head of Major Department Signature was redacted for privacy. Dean ui vrx-fciuuEi ue v uj-lege Iowa State University Of Science and Technology Ames, Iowa 1959 il TABLE OF CONTENTS Page INTRODUCTION 1 HISTORICAL 3 EXPERIMENTAL ll| RESULTS AND DISCUSSION 3^ SUMMARY 62 ACKNOWLEDGMENT 6%. 1 INThO LOTION The present knowledge of the chemistry of metal ion complexes has emanated principally from, two general areas of study. The first of these includes investigations of the thermodynamic and chemical properties of metal complexes with common inorganic nucleophilic ligands.