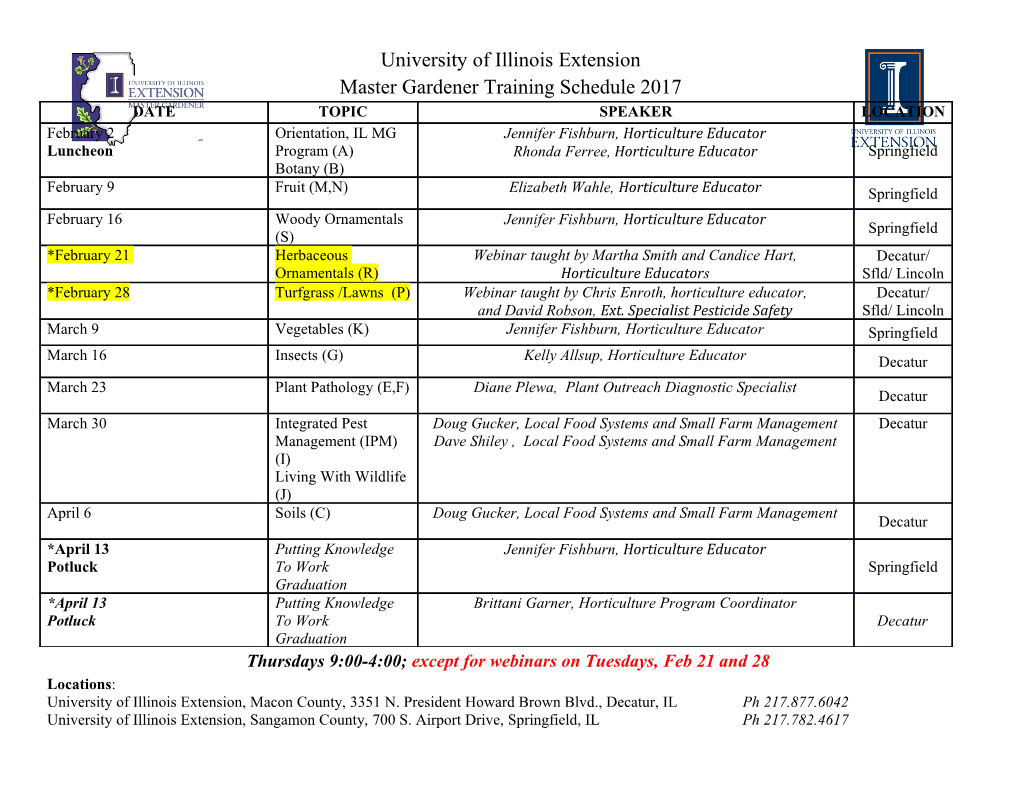
Copyright © 2013 photographs by Gerard Brown Copyright © 2013 text by Graeme Fife Copyright © 2013 photograph of Paul Smith by Alistair Strong 3002 Sterling Circle, Suite 100 Boulder, Colorado 80301-2338 USA (303) 440-0601 • Fax (303) 444-6788 E-mail [email protected] Distributed in the United States and Canada by Ingram Publisher Services. For information on purchasing VeloPress books, please call (800) 811-4210, ext. 2138, or visit www.velopress.com. ISBN 978-1-937715-08-3 A CIP record for this book is available from the Library of Congress. All rights reserved. No part of this publication may be reproduced or used in any form or by any means – photographic, electronic or mechanical, including photocopying, recording, taping or information storage or retrieval systems – without permission of the publishers. This book is produced using paper that is made from wood grown in managed sustainable forests. It is natural, renewable and recyclable. The logging and manufacturing processes conform to the environmental regulations of the country of origin. Design by XAB Design Printed in China by C&C 10 9 8 7 6 5 4 3 2 1 4 The Elite Bicycle Elite bicycle prelims US.indd 4 15/05/2013 15:30 &217(176 )25(:25'%<6,53$8/60,7+ ,1752'8&7,21 %522.6 6(//(,7$/,$ 5(<12/'6 &2/80%86 &,1(//, *858 &+$652%(576 5285.( &<)$& $/(;6,1*(5 )$**,1 3(*25(77, ,1'(3(1'(17)$%5,&$7,21 5,&+$5'6$&+6 %(16(5277$ &21'253$5,6 6(9(1 ',18&&, ,5$5<$1 721<3(5(,5$ :,17(5 63e&,$/,7e67$ 6$3,0 &+5,6.,1* 52<&( 0$9,& )0% &217,1(17$/ 7,0( &217$&76 ,1'(; $&.12:/('*0(176 ,1752'8&7,21 The modern bicycle can, thanks to the availability of a rich variety of frames and components, be adapted to the needs and purposes of many different types of cyclist: for sport, (on road, track, country), commuting, touring, modest excursion … for pleasure, for leisure as well as for extreme levels of athletic discipline. The diversity of bicycle manufacture reflects the burgeoning popularity of and interest in a machine whose essential design has not changed since its invention. At one end of the spectrum, the Asian mass production factories, relatively new on the scene, have brought efficient and enjoyable cycling to millions at very reasonable prices. At the other end, the specialist market and the individual constructeur who makes or builds one bicycle specifically for one buyer at a time. There is, too, the larger specialist enterprise, the hi-tech operation which applies aerospace engineering and production methods and quality. They, as all the people included here, compromise neither on materials nor technical values in the making of what they consider to be the best bicycle that can be made. Today’s cyclists are fortunate indeed to have their needs and wants supplied by such a large and diverse industry dedicated to their safety and comfort and performance. Elite identifies the very best, and the following series of profiles is a snapshot of the top end of the bicycle production industry, focusing on 29 companies which merit that epithet. The selection is not comprehensive. It is, rather, a portrait of a small cadre of exceptional makers and enterprises which combine traditional craftsmanship and new technology in the manufacture of the essential component parts of a bicycle. From the production of a 500g leather aluminium, carbon and titanium, is being used again, with superior modern saddle which hasn’t changed for almost a century, to the fashioning of a production methods, and thus introduced to a new generation. HG Wells carbon-fibre frame which weighs a mere 800g. Nor is élite the monopoly of said ‘Every time I see an adult on a bicycle, I no longer despair for the future professional racing. Superlative materials and technology have been applied of the human race.’ to every facet of cycling. Now we may add to that sentiment, with a flourish and delight, children. The people we’ve met in the course of researching this book, all highly- Here, then, are men and women who, in workshops small and large, with skilled exponents of their respective crafts, are dedicated and passionate hand tools and machines, celebrate and grace the culture of the bicycle men and women who understand the value, and not simply the price, of and impart to it a singular dose of their enthusiasm, intellectual and manual what they produce. Quality before cost. We felt that these craftsmen, brilliance, their creative drive and devotion to the making of the élite bicycle. artists and engineers should be celebrated more widely and generously. They fuse traditional values with a constant thirst for innovation. Steel, for Gerard Brown example, once the darling of the bicycle industry but long since overtaken by Graeme Fife The Elite Bicycle 6$''/(66PHWKZLFN:HVW0LGODQGV8. Brooks now make a wide range of leather goods as well as saddles: bar tape, toolbags, trouser bands and other items, all manufactured economically from off-cuts. %522.6 In 1865, a harness-maker, John Boultbee Brooks, with, reputedly, £20 in his pocket, left his native Leicestershire town of Hinckley for Birmingham. He established a business in horse harnesses and general leather goods in Great Charles Street under the name JB Brooks & Co. and rode to and from the works on his horse. In 1878, his faithful old horse died and because, it’s said, he could not afford (or, perhaps choose) to replace the beloved steed, he accepted the loan of a friend’s bicycle, a machine that was, at the time, dubbed ‘the horse that eats no hay’. It was fitted with a wooden saddle. Brooks found the wretched thing so excruciatingly uncomfortable* that he resolved to make a seat as lenient as that which he’d enjoyed on the horse which did eat hay. On 28 October 1882, his first patent – Saddles for Bicycles and Tricycles – launched the manufacture of what became, until the 1950s, the best selling saddle in the world. The company’s first logo shows a bee with outspread wings beneath a single word – Industria. This may be glossed ‘Busy as a bee’. Brooks applied the expertise of making equine saddles to a comfy seat for the new-fangled machine, in particular, the moulding of thick cow leather to the form of the human buttocks. The process he evolved is still in use and one of the saddles, the B17 model, first included in the 1890s Brooks catalogue, is still being sold, billed originally, as now, as ‘a neat saddle * Ghenghis Khan insisted that his Mongol cavalry ride angular wooden saddles as a constant reminder that their job was ruthless conquest, not comfort. I can vouch personally for the efficacy of the Khan’s message. The 5mm thick hides have to be soaked in water to make them pliable enough to work. Stiff sheets of leather sit in the warehouse awaiting Immense pressure forces the rawhide blanks into selection and working. the smooth flowing moulds. Having been cut to the correct shape the leather awaits ‘the process’ . Most of the machinery required to make a Brooks saddle is old, heavy and noisy. The physics of this sort of manufacture demands both precision and force; lightweight doesn’t get a look in. The Elite Bicycle 723/()7 The moulded leather is trimmed with a knife before the saddle shapes are gently oven-dried. $%29( As they await the process of fixing them to the frame, the saddle tops have an alluring sensual quality. They’re hard, shiny and the form flows beautifully along the length. /()7 Every Brooks saddle passes through up to a dozen pairs of hands before leaving the factory. Champfering requires the cutting skills of a bespoke tailor, the eye of a interstices are made into washers – soaked for an hour in water, drip dried watchmaker and the precision of a micro-engineer. A mere slip can ruin a and given the first moulding while still damp. This process combines a Brooks saddle. That such a delicate procedure comes almost at the end of the production process means that a very experienced hand is required. Eric Murray mechanical press and the skilled hands of a Trimmer. Next to the trimmer’s has such a hand. table, a hand-written placard: Qualifications for being a Trimmer: Grip like a Vice, Strength of a 800lb Gorilla, Stamina of a Viking rower. of best quality’. Indeed, the whole ethos of the Brooks operation – and it extends beyond saddles* – is very old-school, even slightly antiquated. The moulded leather, dried in two different ovens at different temperatures Yet, when the present Works Manager arrived in 1999 and decided that for a further two hours, passes to the next procedure: the fitting of the frame. he needed to bring this renowned company ‘not just into the 21st century Boultbee Brooks’ introduction of the coiled spring (a comparatively recent but into the 20th century’, he discovered that the traditional methods of development) into the making of his saddle was a stroke of genius. Early manufacture are just right for Brooks. Change has no intrinsic virtue and the bicycles had all been fitted with solid seats as unforgiving as the solid tyres. first aim remains the principal aim – ‘to use the best materials, designs and The marriage of moulded leather to a sub-frame supported on a strong construction that experience, skill and money can procure’. spring which gave slightly under the pressure of bumps in the road suddenly turned the bicycle into a quite different machine.
Details
-
File Typepdf
-
Upload Time-
-
Content LanguagesEnglish
-
Upload UserAnonymous/Not logged-in
-
File Pages14 Page
-
File Size-