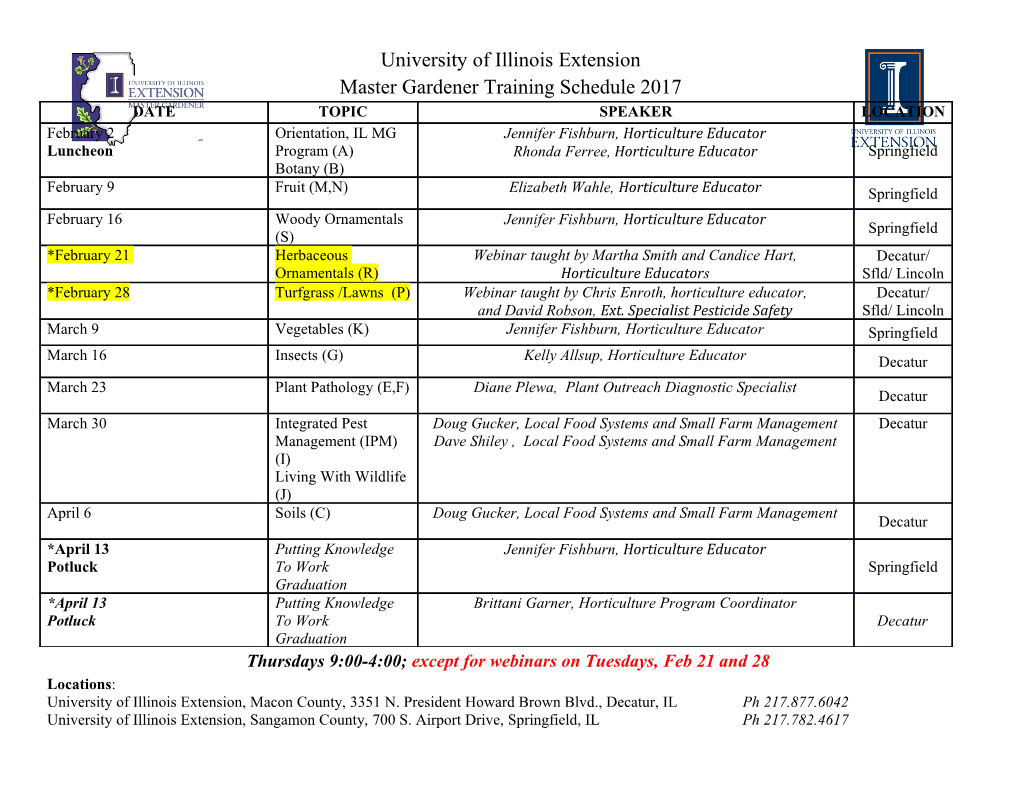
Downloaded from orbit.dtu.dk on: Oct 01, 2021 FLOW DISTRIBUTION IN A SOLAR COLLECTOR PANEL WITH HORIZONTAL ABSORBER STRIPS Fan, Jianhua; Shah, Louise Jivan; Furbo, Simon Published in: Solar Energy Publication date: 2007 Document Version Early version, also known as pre-print Link back to DTU Orbit Citation (APA): Fan, J., Shah, L. J., & Furbo, S. (2007). FLOW DISTRIBUTION IN A SOLAR COLLECTOR PANEL WITH HORIZONTAL ABSORBER STRIPS. Solar Energy, 81, 1501-1511. General rights Copyright and moral rights for the publications made accessible in the public portal are retained by the authors and/or other copyright owners and it is a condition of accessing publications that users recognise and abide by the legal requirements associated with these rights. Users may download and print one copy of any publication from the public portal for the purpose of private study or research. You may not further distribute the material or use it for any profit-making activity or commercial gain You may freely distribute the URL identifying the publication in the public portal If you believe that this document breaches copyright please contact us providing details, and we will remove access to the work immediately and investigate your claim. FLOW DISTRIBUTION IN A SOLAR COLLECTOR PANEL WITH HORIZONTALLY INCLINDED ABSORBER STRIPS Jianhua Fan∗, Louise Jivan Shah, Simon Furbo Department of Civil Engineering, Technical University of Denmark, Brovej, DK-2800 Kgs. Lyngby, Denmark Abstract The objective of this work is to theoretically and experimentally investigate the flow and temperature distribution in a solar collector panel with an absorber consisting of horizontally inclined strips. Fluid flow and heat transfer in the collector panel are studied by means of computational fluid dynamics (CFD) calculations. Further, experimental investigations of a 12.5 m² solar collector panel with 16 parallel connected horizontal fins are carried out. The flow distribution through the absorber is evaluated by means of temperature measurements on the backside of the absorber tubes. The measured temperatures are compared to the temperatures determined by the CFD model and there is a good similarity between the measured and calculated results. Calculations with the CFD model elucidate the flow and temperature distribution in the collector. The influences of different operating conditions such as flow rate, properties of solar collector fluid, solar collector fluid inlet temperature and collector tilt angle are shown. The flow distribution through the absorber fins is uniform if high flow rates are used. By decreased flow rate and decreased content of glycol in the glycol/water mixture used as solar collector fluid, and by increased collector tilt and inlet temperature, the flow distribution gets worse resulting in an increased risk of boiling in the upper part of the collector panel. Keywords: Solar collector; Flow distribution; Computational Fluid Dynamics (CFD); Buoyancy effects 1 Introduction The thermal performance of flat-plate collectors is strongly related to the flow distribution through the absorber tubes (Duffie and Beckman, 1991). Investigations have conclusively shown that the collector efficiency decreases as the uniformity of flow distribution diminishes (Chiou, 1982). The more uniform the flow distribution, the higher collector efficiency. However, uniform flow distributions are not always present in solar collectors, as shown by Wang and Wu ∗ Corresponding author. ISES member Tel: +45-42251889 Fax: +45-45883282 Email addresse: [email protected] (Jianhua Fan) 1 (1990), Shen (1992), Jones and Lior (1994), Weitbrecht et al. (2002) and Gunnewiek et al. (1996, 2002). Gunnewiek et al. investigated flow distribution in unglazed transpired plate collectors of large area both with (2002) and without the effect of wind (1996). The investigations were carried out by means of a commercial CFD code TASCFlow. It is shown that the flow of air through the collector surface is not uniformly distributed due to the buoyancy effects and that outflow of air may occur over part of the collector surface if suction flow is low enough. Shen (1992) studied the flow maldistribution in dividing and combining flow manifolds due to the effect of friction. Weitbrecht et al. (2002) investigated isothermal flow distribution in solar collectors with laminar flow conditions by means of LDV (laser Doppler velocimetry) measurements and numerical analysis. Jones and Lior (1994) presented the numerical investigations of flow distribution in solar collectors consisting of two horizontal manifolds connected by a number of parallel riser tubes without considering thermal effects. Wang and Wu (1990) presented flow distribution in solar collectors with thermal effects such as longitudinal heat conduction and buoyancy. Both collectors with U type configuration and collectors with Z type configuration were investigated. Although there is no contradictory from physical point of view, the flow distribution pattern of Z type collectors found by Jones and Lior does not match the results of Wang and Wu. The flow pattern found by Jones and Lior is increasing with the increase of the distance along the inlet manifold (Fig. 6 and 7 of Jones and Lior, 1994), while the flow pattern found by Wang and Wu is first decreasing with the increase of branch number and then increasing with the increase of branch number (Fig. 5 of Wang and Wu, 1990). This type of behaviour is not the result of buoyancy, but of a greater role of inertia in the manifolds (vs. friction). For frictionally dominant manifolds, the riser flow rates tend to be monotonic with distance along the inlet manifold. As the number of branches are increased and/or distance between the branches reduced, the pressure distributions in the manifolds tends to become dominated by inertial pressure changes in the branch regions. The riser flow distribution then behaves in a non-monotonic manner, where there is a region of flow starved risers away from the ends of the collector. The aim of this work is to theoretically and experimentally investigate the flow and temperature distribution in a solar collector panel with an absorber consisting of horizontally inclined fins. Fluid flow and heat transfer in the collector panel are studied by means of computational fluid dynamics (CFD) calculations. A simplified model is built, where the geometry including the manifolds and the quadrangular absorber tubes are fully modelled, while the existence of the fins is represented by a heat flux into the absorber tube walls. The model includes heat transfer and buoyancy effects. The influences of the flow and temperature distributions by different operation conditions such as flow rate, properties of solar collector fluid, solar collector fluid inlet temperature and collector tilt angle are investigated, while the influence of the flow distribution on collector thermal efficiency is not considered. 2 Measurements are carried out with a 12.5 m² solar collector panel with 16 parallel connected horizontal fins. The flow distribution through the absorber is evaluated by means of temperature measurements on the backside of the absorber tubes. The measurements are carried out for different flow rates, temperature levels and solar irradiances. The measurements are compared to the results of the CFD calculations. 2 Experimental work Steady state measurements are carried out with a 12.5 m2 flat-plate solar collector panel from Arcon Solvarme A/S. The solar collector is a high temperature HTU solar collector designed for medium and large solar heating systems. The collector has also with advantage been used recently in small solar heating systems. Fig. 1 shows the design of the HTU solar collector. The collector consists of two manifolds (one dividing and one combining manifold) with a diameter of 0.0256 m and 16 horizontally inclined absorber tubes in a “U” type configuration (Vejen et al. 2004), see Fig. 2. The quadrangular absorber tubes have a hydraulic diameter of 0.0067 m. A propylene glycol/water mixture is used as the solar collector fluid. Properties of the mixture and their dependences on temperature for 40% (weight %) glycol solution are shown as follows (Furbo, 1997): 2 Density, [kg/m3] ρ =1042− 0.479*T − 0.00185*T T + 273.15 Dynamic viscosity, [kg/(ms)] μ = 0.0016*( )−8 333.15 2 Specific heat, [J/(kgK)] C p = 3721+1.629 *T + 0.0101*T Thermal conductivity, [W/(mK)] λ = 0.419 + 2.032×10−4 *T where T is fluid temperature, [°C]. The solar collector fluid is circulated through the collector panel by a pump. The circulating flow rate, in the range of 2.5-25.0 l/min, is measured using a QEC type Clorius flow meter. The flow distribution through the absorber tubes is evaluated by fluid temperature distribution just before the fluid enters the combining manifold. Copper-constantan thermo couples (type TT) are attached to the backside of the absorber tubes and used for the temperature measurements. The positions of the measurement points are schematically shown in Fig. 2 as circles on the left side. Since the absorber tube wall has a higher temperature than the fluid inside, small corrections are made to the temperature measurements to get the fluid temperatures. The corrections are determined based on the difference between the measured solar collector fluid outlet temperature and the mean of the measured absorber tube wall temperatures, see the following approximated equation: 3 16 ∑Twall,i ⋅Qi i =1 (1) Tfluid ,i = Twall,i − ( − Toutlet ) Q0 where Tfluid,i is the fluid temperature in i th tube, ºC; Twall, i is the temperature of the ith tube wall, ºC; Toutlet is the outlet temperature from the collector, ºC; Qi is the volume flow rate through the i th tube, l/min, while Q0 is the overall volume flow rate for all the tubes, l/min. The fluid velocities in the absorber tubes used in the equation are obtained from CFD simulation. Since the correction is small, the error introduced by this method will not significantly influence the credibility of the determination of the fluid temperature.
Details
-
File Typepdf
-
Upload Time-
-
Content LanguagesEnglish
-
Upload UserAnonymous/Not logged-in
-
File Pages28 Page
-
File Size-