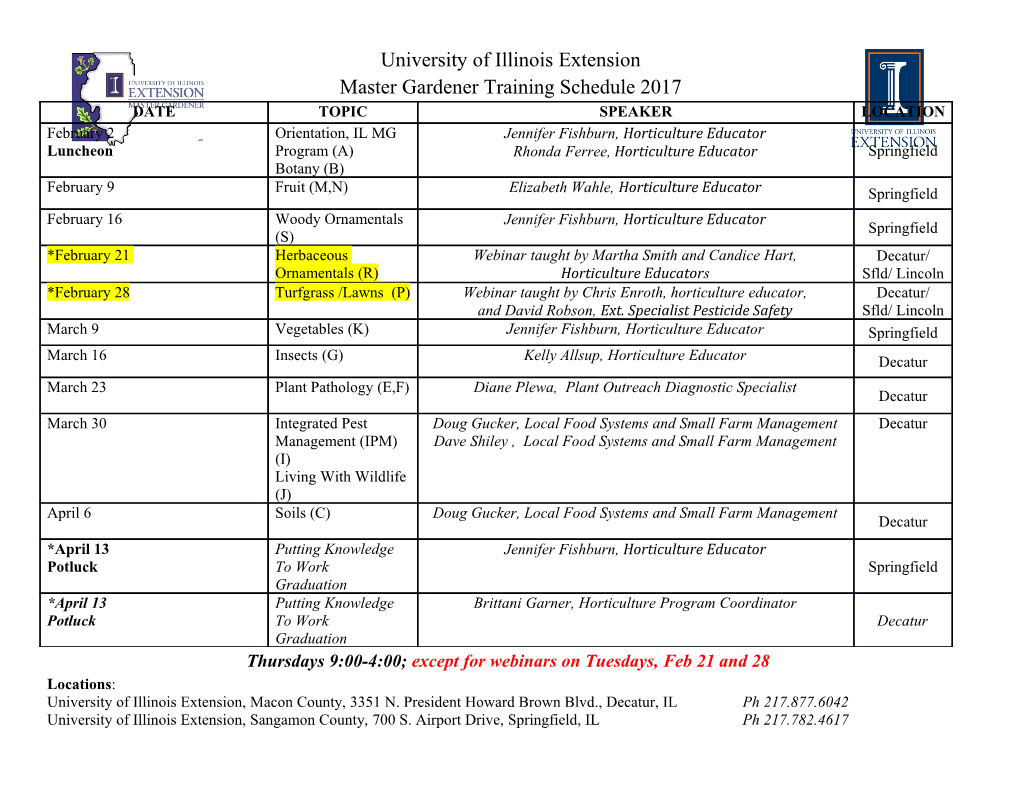
ARH** ST-124 Distribution Category UC-4 FIXATION OF RADIOACTIVE WASTE BY REACTIONS WITH CLAYS: PROGRESS REPORT Calvin H. Delegard G. Scott Barney Chemical Technology Laboratory Research Department Research and Engineering Division July 1975 ATLANTIC RICHFIELD HANFORD COMPANY RICHLAND, WASHINGTON 99352 ii ARH-ST-124 TABLE OF CONTENTS Page ABSTRACT..................... ............ .. iii INTRODUCTION ................................ SUMMARY AND CONCLUSIONS ................... EXPERIMENTAL ................................ MATERIALS................................................ ANALYSES ...................... ......... PROCEDURES............................................ RESULTS AND OISCUSSION ........ ......... REACTION CHARACTERISTICS ....... Stoichiom etry . ........................... K in etics ............. Heats of Reaction ........ CONCEPTUAL PLOW DIAGRAM FOR ALTERNATIVE PROCESSES ........................................ ........ 10 PRODUCT PROPERTIES .............. 21 Rich Clay Process ............ 21 Lean Clay Process ............ 26 Clay Calcination Process ......... jj ACKNOWLEDGMENTS ................... ........ n REFERENCES ..................... .......... 35 i i i ARH-ST-124 ABSTRACT Reactions of clay with Han ford-i'^ne radio- active wastes ( liq u id s , salt cake, and sludge) war*# studied aa a means of immobilisation of radionuclides contained in the waste* Products of these reactions were identified aa the crystal- lin e sodium alum inosilicates, aanarinite and nepheline. Radionuclides are entrapped in these crystalline minerals. Conceptual flow diagrams for conversion of high-salt wastes to cancrinite and nephelinn were defined and tested. The mineral products were evaluated fo r use as forms for long-term storage of radioactive waste. ARH-ST-124 FIXATION OF RADIOACTIVE WASTE BY REACTIONS WITH CLAYS: PROGRESS REPORT INTRODUCTION This work is a continuation of that reported in 1974t1? concerning the immobilization of radioactive waste generated by reprocessing of nuclear fuel at Hanford. Conversion of present wastes to a more immobile form may be necessary to prevent migration of hazardous radionuclides into the bio­ sphere during long-term storage. Prior work showed that the major radioactive elements in the waste, cesium and stron­ tium, could be fixed by reactions of aqueous waste with aluminum silicate clays. These reactions yielded cancri­ nite, a sodium aluminosilicate mineral which entraps waste salts in its crystalline lattice structure. Some of the relevant chemical and physical properties of the cancrinite product were determined, such as leach rate, thermal sta­ bility, volume, hardness, and crystal size. These studies showed cancrinite to be a promising storage form for radio­ active waste. The objectives of the present work were to further evaluate cancrinite as a waste form, identify and quantify important reaction variables, and evaluate process alter­ natives. Application of clay reactions to fixation of the thraa major types of waste stored at Hanford [salt cake, sludga, and caustic terminal liquor (from liquid waste evaporation)] was studied. BLANK PAGE 2 ARH-ST-124 SUMMARY ANO CONCLUSIONS Additional characteristics of reactions of clays with Hanford wastes were studied. The rate of cancrinite forma­ tion by reaction of caustic waste liquor with calcined clays (kaolin, bentonite) is 5 to 30 times greater than for uncal­ cined clays. Half-times for the calcined kaolin reactions at 100# 75, and 50° C are, respectively, <0.2, 0.7, and 4 hours. The corresponding half-times for calcined bentonite reactions are 0.1, 0.6, and 6 hours. Measurements of cesium uptake during cancrinite formation show that the amount of cesium entrapped increases as more cancrinite is formed. There is, however, a lc.rge initial amount of cesium on bentonite due to ion exchange. Heats of reaction were measured for reactions of synthe­ tic caustic waste solution with calcined and uncalcined clays (kaolin and bentonite). Values for the uncalcined clays were significantly less (kaolin ■ -49.5 ±3.6 cal/g, bentonite = -46.7 ± 1.3 cal/g) than for the same clays after calcination (kaolin = -190.7 ± 3.5 cal/g, bentonite = -105.9 ± 3.2 cal/g). Results of measurements using several different com­ mercially available calcined kaolins show that the source of the clays significantly affects the heat of reaction. Estimated values for the rise in temperature of a 1 g clay/ml waste range from 38 to 41° C for uhcalcined clays to 87 to 156° C for calcined clays (assuming adiabatic conditions). A conceptual flow diagram is presented in which caustic (terminal) liquor, salt cake, and dissolved salt cake are converted to cancrinite or nep'neline. Three basic process alternatives are given: 1. The Rich Clay process in which a stoichiometric excess of clay is mixed with liquid waste and reacted to form a cancrinite-clay-salt mixture. 3 ARH-ST-124 2. The Lean Clay process in which clay and liquid waste are converted to relatively pure cancrinite by control of the mole ratios of reactants. A binder is used to form a massive product from the small cancrinite crystals. 3. The Clay Calcination process in which solid or liquid waste is mixed with clay and fired at 600 to 1000° C to form a nepheline product. Products from each of these processes were evaluated with respect to leach rate, thermal and radiation stability, mechanical strength, volume, and density. A comparison of product properties (Table I) shows that application of the Lean Clay process to salt cake yields an unmanageably high volume of product. Thus, the Lean Clay process can be eliminated from further consideration except, perhaps, for applications where product volume is not important. The Clay Calcination alternative yields a product with improved leachability, mechanical strength, thermal and radiolytic stability, and a significantly lower volume than the other processes. The principal disadvantages are, of course, the higher processing temperature and the necessity for off-gas treatment. EXPERIMENTAL MATERIALS Forty-nine commercially available bentonites and cal­ cined and uncalcined kaolins were screened for product quality. In addition, some calcined bentonites and kaolins were prepared by heating the clays at 600 to 700° C for 6 to 48 hours. Compositions of fired and unfired bentonites and kaolins used in most experiments are given in Table II. TABLE I COMPARISON OF ALTERNATIVE CLAY FIXATION PROCESSES Product Characteristics Rich Clay Process Lean Clay Process Clay Calcination Process Mineral form Cancrinite Cancrinite Nepheline Volume 1.3 x caustic terminal 2 x caustic terminal 0.8 x caustic terminal liquor liquor liquor 3 x salt cake 6 x salt cake 1.5 x salt cake Leachability, g/cm2-day 10"1* to 10-2 1 0 “5 to 10*3 10-5 to 1 0 “3 Thermal and radiolytic stability Good Good Excellent Mechanical strength Poor-to-good Excellent Excellent Bulk density, g/ml 1.5 to 1.7 1.6 to 2.0 1.6 to 2.0 TABLE II COMPOSITIONS OF CLAY REAGENTS* ________Weight Percent of Component in Calcined Calcined Calcined Calcined Mixed Bentonite Bentonite Bentonite bentonite Kaolin Kaolin Kaolin Kaolin Kaolin Component #1 *2 *1 #2 #1 #2 #1 ?2 Bentonite Si02 6 6 .8 59.9 72.5 64.3 45.30 46.9 52.8 54.4 49.6 AI 2O 3 16.4 19.8 17.e 21.3 38.38 38.2 44.7 44.3 33.3 NasO 2.48 2 .2 2.7 2.4 0.27 0.04 0.31 0.05 0.4 Fe203 3.4 3.9 3.7 4.2 0.30 0.35 0.35 0.41 1 .2 MgO 1.84 1.3 2 .0 1.4 0.25 0.58 0.29 0.67 0 .1 CaO 2.77 0 .6 3.0 0.05 0.43 0.06 0.50 0 .2 0 .6 U h 2o 8 .0 6.5 0 0 13.97 13.9 0 0 1 2 .8 1 TOTAL 101.7 94.2 101.7 94.2 98.52 100.4 98.5 100.3 97.6 ♦Sources of clay reagents: Bentonite #1: MC-101, Georgia Kaolin Company Bentonite #2: Wyo-Bond, Federal Bentonite Company Calcined Bentonite #1: Calcined MC-101, 700°C for 24 hours Calcined Bentonite #2: C a l c i n e d W y o - B o n d , 700° C f o r 24 h o u r s Kaolin #1: Astra-Glaze, Georgia Kaolin Company Kaolin #2: 6 -Tile, Georgia Kaolin Company Calcined Kaolin #1: Calcined Astra-Glaze, 700° C for 24 hours #2: C a l c i n e d - T i l e , 700° C f o r 24 h o u r s Calcined Kaolin 6 A R H - S T - 1 2 4 Mixed Kaolin-Bentonite: Indian Hill, Interpace Corporation. 6 ARH-ST-124 A number of synthetic and genuine waste solutions were used. The compositions of these solutions are given in Table III along with the synthetic salt cake composition used. Table IV shows the composition of the genuine Purex sludge employed in one experiment. Materials used to formu­ late the synthetic wastes were reagent grade. TABLE III COMPOSITIONS OF SYNTHETIC AND GENUINE WASTES Molar Concentrations of Components in W eight _______C a u s tic T e rm in a l L iq u o r________ P e r c e n t S y n th e tic S y n th e tic S y n th e tic G enuine Component in Component W aste #1 W aste #2 W aste #3 W aste* S a l t Cake NaOH 3 .6 3 .0 1 0 .0 3 .4 2 10 NaNO3 3 .4 2 .5 2 .0 2 .8 4 60 NaN02 2 .1 0 0 1 .6 7 20 N aA l02 1 .8 1 .0 0 1 .9 9 0 A l(O H )3 0 0 0 0 10 H20 40 - - - 0 ‘From Hanford Waste Tank 241-BX- 1 1 0 , also containing 3.47 x 10s yCi/liter l37Cs. TABLE IV COMPOSITION OF HANFORD WASTE TANK 241-A-104 SLUDGE Component Concentration H20 42% Al 2 .82 M Si 0 .8 3 m Fe 4. 99 M Mg 0 .11 Af Cd 0 .4 1 M Ba 0 .009 M Mn 0 .7 1 M Sr <0 .
Details
-
File Typepdf
-
Upload Time-
-
Content LanguagesEnglish
-
Upload UserAnonymous/Not logged-in
-
File Pages39 Page
-
File Size-