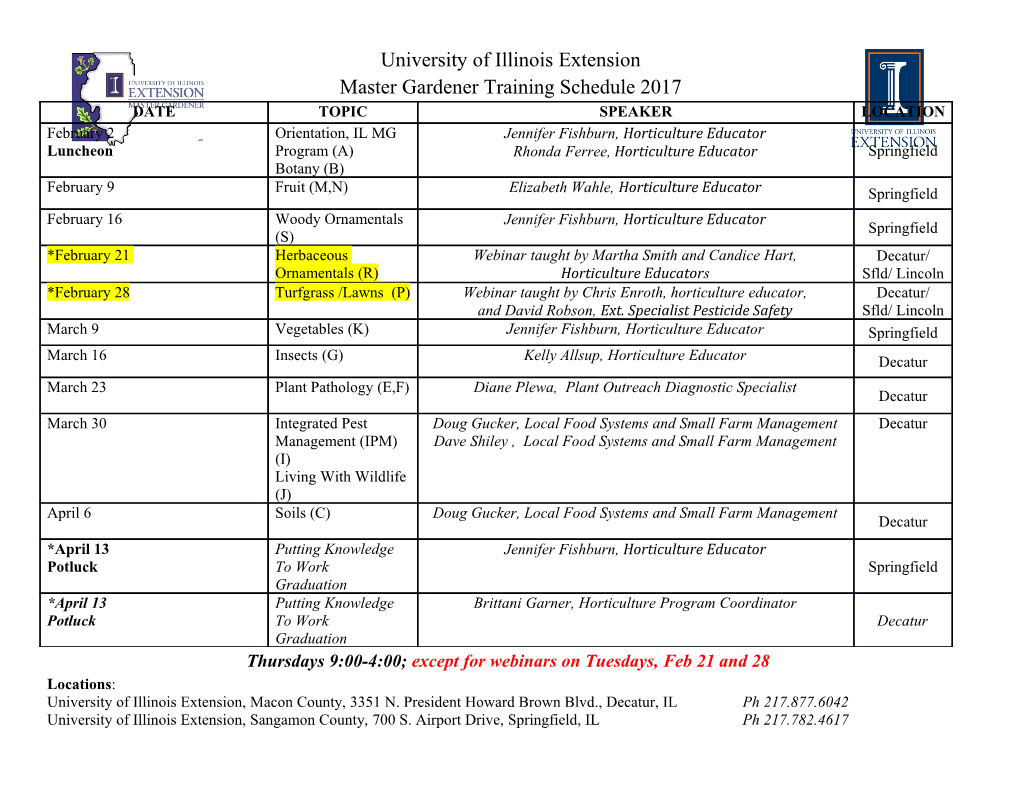
NTIS #PB2000-108442 SSC-410 FATIGUE OF ALUMINUM STRUCTURAL WELDMENTS This document has been approved For public release and sale; its Distribution is unlimited SHIP STRUCTURE COMMITTEE 2000 SHIP STRUCTURE COMMITTEE RADM Robert C. North U.S. Coast Guard Assistant Commandant, Marine Safety and Environmental Protection Chairman, Ship Struchlre Committee Mr. Robert McCarthy Dr. Donald Liu Director, SeniOl' Vice President Survivability and Structural Integrity Group Naval Sea Systems Command American Bureau of Shipping Mr. Joseph Byme Mr. Bud Streeter Director, Office of Ship Construction Director General, Marine Safety, Safety & Security Maritime Administration Transport Canada Mr. Thomas Connors Dr. Neil Pegg Director of Engineering Group Leader - Structural Mechanics Military Sealift Command Defence Research Establishment Atlantic CONTRACTING OFFICER TECHNICAL REP, EXECUTIVE DIRECTOR Lieutenant David J. Martyn I Ms. Dinah Mulligan Lieutenant David J. Martyn U.S. Coast Guard R & D Center U. S. Coast Guard SHIP STRUCTURE SUB-COMMITTEE AMERICAN BUREAU OF SHIPPING DEFENCE RESEARCH EsTABLISHMENT ATLANTIC Mr. Glenn Ashe Mr. Layton Gilroy Mr. Yung Shin Mr. John Porter Mr. Phil Rynn LCDR Stephen Gibson Mr. William Hanzalek Dr David Stredulinsky MARITIME ADMINISTRATION MILITARY SEALIFT COMMAND Mr. Chao Lin Mr. Edward Meade Mr. Rick A. Anderson Mr. Jeffery E. Beach Mr. Michael W. Touma NA VAL SEA SYSTEMS COMMAND TRANSPORT CANADA Mr. W. Thomas Packard Mr. Nico Pau Mr. Edward E. Kadala Mr. James Reid Mr. Allen H. Engle Mr. Charles L. Null UNITED STATES COAST GUARD CANADIAN COAST GUARD Captain Mark VanHaverbeke Mr. Justus Bunckhuysen Mr. Rubin Sheinberg Mr. Walt Lincoln Commander Ray Petow Member Agencies: Address Correspondence to: American Bureau of Shipping Executive Director Defence Research Establishment Atlantic Ship Structure Committee Maritime Administration U.S. Coast Guard {G-MSE/SSC) Military Sealift Command C 2100 Second Street. SW Naval Sea Systems Command Washington, D.C. 20593-0001 Society of Naval Architects & Marine Engineers Ph: (202) 267-0003 Transport Canada Email: [email protected] United States Coast Guard Ship Structure Committee An lnteragency Advisory Committee SR-1395 SSC-410 September 2000 l<'ATIGUE OF ALUMINUM STRUCTURAL WELDMENTS As the speed and displacement of high-speed aluminum craft continues to increase, so do the fatigue related cracking problems. At present, most owners treat this problem as a maintenance issue and simply repair the cracked structure. This report altempts to shift the emphasis of this problem from maintenance to design. It allows owners to address fatigue related cracking problems during the design of the vessel and avoid the costly repairs associated with continued re-welding of fatigue cracks in structures. This report addresses loads acting on high-speed craft and identifies the state-of-the-art as well as "holes" in the data required to develop a complete and consistent set of fatigue calculations for aluminum in the marine environment. The report also addresses the damage tolerances of cracked aluminum structures and provides information that ·will help designers and engineers determine the urgency with which a specific crack may need repair. Information on the fatigue design practices and design codes of other aluminum industries are included to provide helpful insight while more data is developed for the marine industry and aluminum high-speed craft. The report concludes with recommendations for continued research and development based on the holes identified during the development of the current effort. R. C. NORTH Rear Admiral, U.S. Coast Guard Chairman, Ship Structure Committee T cc h mca. IRenor tD ocumentahon p a"e l. Report No. 2. Government Accession No. 3. Recipient's Catalog No. 4. Title and Subtitle 5. Report Date FATIGUE OF ALUMINUM STRUCTURAL WELDMENTS May2000 6. Performing Organization Code 7. Author(s) 8. Performing Organization Report Kramer, R.K., Rampolla, B., Magnusson, A No. SR-1395 9. Performing Organization Name and Address IO. Work Unit No. (TRAIS) John J. McMullen Associates Inc. 4300 King Street l l. Contract or Grant No. Alexandria, VA 22302 DTCG39-95-D-E99010 12. Sponsoring Agency Name and Address 13. Type of Report and Period Ship Structure Committee Covered C/O US Coast Guard (G-MSE/SSC) Final Repm1 2100 Second Street, SW 14. Sponsoring Agency Code Washington, DC 20593 G-M 15. Supplementary Notes Snonsored by the Ship Structure Committee. Jointly funded by its member agencies 16. Abstract As the speed and displacement of high-speed aluminum craft continues to increase so to do the fatigue related cracking problems. At present, most owners treat this as a maintenance problem and simply repair the cracked structure. This report attempts to shift the emphasis of this problem from maintenance to design. It will allow owners to address fatigue related cracking problems during the design of the vessel and avoid the costly repairs associated with continued re-welding of fatigue cracked structure. The report addresses loads acting on high-speed craft and identifies the state of the art as well as "holes" in the data required to develop a complete and consistent set of fatigue calculations for aluminum in the marine environment. The report also addresses the damage tolerance of cracked aluminum structure and provides information that will help designers and engineers determine the urgency with which a specific crack may need repair. The report also identifies and provides information on the fatigue design practices of other aluminum industries and design codes. This provides helpful insight while more data is developed for the marine industry and aluminum high-speed craft. The report concludes with recommendations for continued research and development based on the holes identified during the development of the current effort. 17. Key Wonls 18. Distribution Statement aluminum, fatigue, damage tolerance Distribution unlimited, available through: National Technical Information Service U.S. Department of Commerce Soringfield, VA 22 I 51 Ph. (703) 487-4650 19. Security Classif. (of this report) 20. Security Classif. (of this page) 21. No. of Pages 22. Price Unclassified Unclassified CONVERSION FACTORS (Approximate conversions to metric measures) To convert from to Function Value LENGTH inches meters divide 39.3701 inches millimeters multiply by 25.4000 feet meters divide by 3.2808 VOLUME cubic feet cubic meters divide by 35.3149 cubic inches cubic meters divide by 61,024 SECTION MODULUS inches2 feet centimeters2 meters multiply by 1.9665 inches2 feet centimeters3 multiply by 196.6448 inches3 centimeters3 multiply by 16.3871 MOMENT OF INERTIA inches2 feet2 centimeters2 meters divide by 1.6684 inches2 feet2 centimeters4 multiply by 5993.73 inches4 centimeters4 multiply by 41.623 FORCE OR MASS long tons tonne multiply by 1.0160 long tons kilograms multiply by 1016.047 pounds tonnes divide by 2204.62 pounds kilograms divide by 2.2046 pounds Newtons multiply by 4.4482 PRESSURE OR STRESS pounds/inch2 Newtons/meter2 (Pascals) multiply by 6894.757 kilo pounds/inch2 mega Newtons/meter2 multiply by 6.8947 (mega Pascals) BENDING OR TORQUE foot tons meter tonnes divide by 3.2291 foot pounds kilogram meters divide by 7.23285 foot pounds Newton meters multiply by 1.35582 ENERGY foot pounds Joules multiply by 1.355826 STRESS INTENSITY kilo pound/inch2 in√in) mega Newton MNm3/2 multiply by 1.0998 J-INTEGRAL kilo pound/inch Joules/mm2 multiply by 0.1753 kilo pound/inch kilo Joules/m2 multiply by 175.3 iii Table of Contents 1. Introduction ............................................................................................................................. 3 1.1 Fatigue and Damage Tolerance Analysis Background ....................................................... 3 1.2 Objectives............................................................................................................................ 6 1.3 Why Aluminum?................................................................................................................. 7 1.4 Welding of Aluminum ........................................................................................................ 8 1.5 Summary of Report ............................................................................................................. 9 1.6 Conclusions ....................................................................................................................... 11 1.7 References ......................................................................................................................... 12 2. Prediction of Loads on High Speed Craft ............................................................................. 15 2.1 Introduction ....................................................................................................................... 15 2.2 Definition of High Speed for High-Speed Craft ............................................................... 15 2.3 Definition of Primary and Secondary Loads..................................................................... 16 2.4 Loads Acting on High-Speed vice Displacement Vessels ................................................ 17 2.4.1 Increasing Length of High-Speed Craft .................................................................... 19 2.5 Loading for Fatigue and Damage Tolerance..................................................................... 20 2.6 Loads and Stresses ...........................................................................................................
Details
-
File Typepdf
-
Upload Time-
-
Content LanguagesEnglish
-
Upload UserAnonymous/Not logged-in
-
File Pages312 Page
-
File Size-