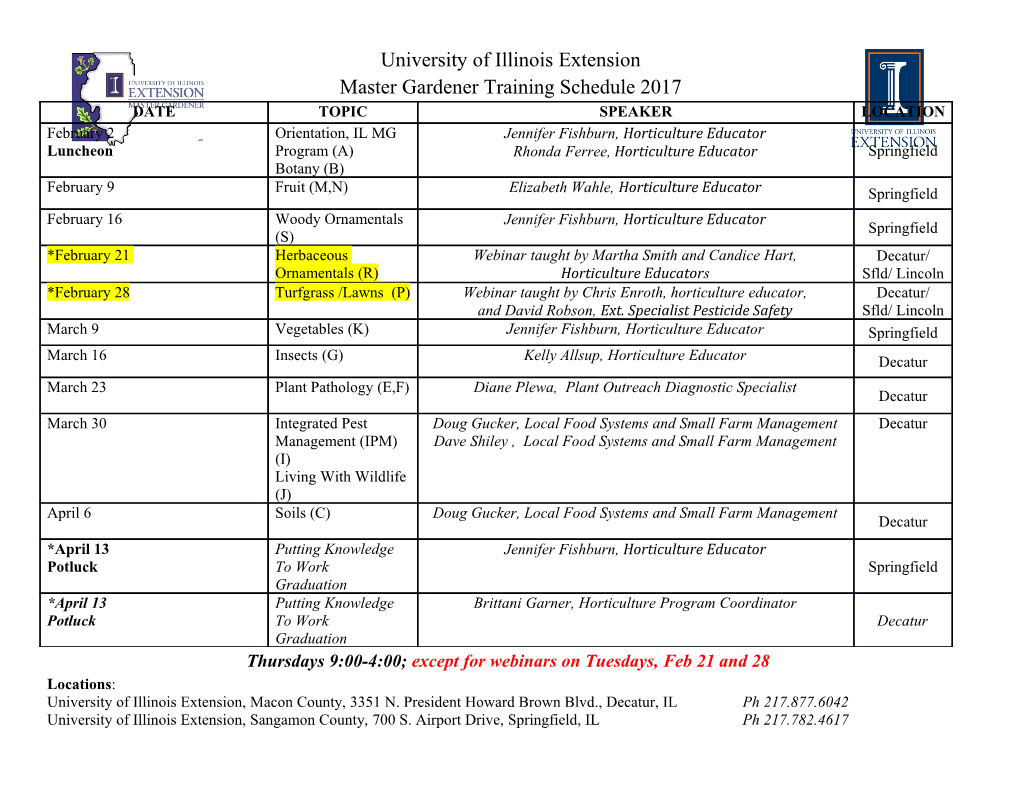
The Future of the MEMS Inertial Sensor Performance, Design and Manufacturing Michael Perlmutter1, Stephen Breit2 1 Civitanavi Systems s.r.l. Via del Progresso 5, 63827 Pedaso (FM) ITALY 2 Coventor, Inc., 1000 Centre Green Way Suite 200, Cary, NC, 27513 USA Inertial Sensors and Systems 2016 Karlsruhe, Germany 978-1-5090-2515-2/16/$31.00 ©2016 IEEE P10 Abstract The market for high-performance inertial sensors, tactical grade and above, has been dominated to date by macro-scale devices such as HRGs, RLGs and FOGs. While the size, power requirements, and cost of these sensors have decreased considerably over the past two decades and further reductions can be expected, the tactical IMU size remains on the order of 0.5l, and the cost remains in the $10k range. During the same period, micro-scale inertial sensors based on MEMS technology have been introduced for automotive and consumer electronics applications and are now produced at the rate of several million per day. MEMS IMUs have become truly ubiquitous, however they have so far fallen short of the requirements for high-performance applications. Nevertheless, there have been continuing reductions in their size, power and particularly cost, to less than $3 for an IMU. There is great interest in understanding future trends for MEMS and their potential threat to traditional sensors for tactical and navigation grade applications. One author has many years of experience in developing macro-scale high-performance sensors and IMUs. The other author has many years of experience in supplying design tools to leading MEMS organizations worldwide. We will first describe trends that are affecting MEMS inertial sensors, including commoditization, consolidation of advanced CMOS manufacturing, market demands for increasing package- and chip-scale integration, the Internet of Things (IoT), and the entry of mainstream CMOS foundries to MEMS manufacturing. We’ll speculate on the direction that could lead to greatest business success for foundries and their customers. We will then survey promising approaches to improving the performance of MEMS sensors and we will conclude with speculations on the roadmap and timeline for a possible crossover for MEMS in high- performance applications. Introduction High-performance (tactical grade –1 deg/h day-to-day bias stability – and above) inertial sensors have always been macro-scale devices. While macro-scale devices that meet high-performance specifications have shrunken in size and cost over recent decades, they remain relatively large and costly compared to inertial sensors micro-machined on silicon wafers, known as MEMS. Over the past two decades, MEMS inertial sensors have become highly successful and are now manufactured at very high volume and very low cost. MEMS performance, though improving, remains at or below tactical grade. This paper explores whether MEMS inertial sensors can ultimately displace macro-scale sensors in high-performance applications. [2] 2. A Brief History of MEMS Commercialization An excellent general introduction to MEMS can be found in [1]. After nearly two decades of academic and commercial R&D, the first commercialization of a MEMS inertial sensor was the introduction by Analog Devices of a single-axis accelerometer for crash detection in cars which entered volume production in 1993 [2]. Bosch introduced the first MEMS gyro electronic stability control in cars, entering volume production in 1997. Automotive applications of MEMS generally, and MEMS inertial sensors in particular, drove the industry from 1993 through the mid 2000s. The introduction of the Nintendo Wii in 2006 marked a breakthrough of MEMS inertial sensors into consumer electronics. The first-generation Wii had a 3-axis accelerometer in its handheld controller. The ability to sense a user’s arm motions was key to a new generation of computer games not possible with competing gaming systems. There had been other applications of MEMS in consumer electronics prior to the Wii, but motion sensing made the product a run-away hit. The introduction of the Apple iPhone in 2007 closely followed the Nintendo Wii and, it’s fair to say, was a watershed event in modern life generally and MEMS in particular. The first- generation iPhone incorporated a 3-axis accelerometer. Initially, it enabled a critical feature of the device: automatic rotation of the display from portrait to landscape mode. Subsequent versions, starting with the iPhone 4 [3], included a so-called 9-axis Inertial Measurement Unit (IMU), consisting of a 3-axis MEMS accelerometer, a 3-axis MEMS gyroscope, and 3-axis magnetometer (based on non-MEMS technology). The improved motion sensing capabilities made possible more sophisticated applications such as augmented reality. A 9-axis IMU is now a mandatory feature of all smart phones. 3. Current Industry Trends Affecting MEMS We can identify at least four industry trends that affect the future of MEMS inertial sensors: commoditization, proliferation of MEMS technology, consolidation of advanced CMOS suppliers, and increasing integration of heterogeneous technologies through chip-scale packaging. We will describe each of these four trends in more detail and then discuss likely consequences of the trends. Commoditization of MEMS motion sensors: Market research firms that follow the MEMS industry, such as Yole Development [4] and IHS iSuppli [5], state that the shipment volume of MEMS continues to grow exponentially [4],[5]. The growth in unit volume is [3] driven not only by mobile devices (smart phones and tablets) but by new applications such as wearables (activity sensors, for example) and IoT devices. Their projections show continued growth in units shipped for at least the next 5 years. However, IHS data shows that total revenue from MEMS-based motion sensors in consumer electronics has decreased since 2014 and is projected to continue dropping through the end of this decade [6]. The implication is that unit prices for MEMS-based motion sensing components are dropping faster than volume is increasing, leading to the overall decline in revenue. Proliferation of MEMS know-how and manufacturing technology: Due to the commercial success of MEMS, a whole eco system for MEMS development exists today that was not available to the industry pioneers. The eco system includes suppliers of materials, manufacturing equipment, metrology equipment, testing equipment and services, and packaging technology and services, not to mention design software. The existence of this eco system greatly lowers the barrier to entry for new entrants in both time and cost. While pioneering companies spent a decade or more going from initial feasibility to production, newer entrants can get there in a few years. Consolidation of advanced CMOS manufacturing: Since the 1960’s, semiconductor technology nodes have followed Moore’s law. Staying competitive in CMOS means staying on Moore’s law, and this has gotten progressively more costly with each new technology node, leading to consolidation of advanced CMOS manufacturing. Currently, there are only 4 companies capable of manufacturing the latest CMOS logic nodes [7]. This means that a lot of older fabs and equipment are becoming obsolete each year. MEMS manufacturing does not require the latest equipment, so it offers a way of extending the productive life of this fully amortized capital equipment. Increasing chip-scale integration, aka More than Moore integration: Chip-scale integration means combining heterogeneous technologies at the die and package levels. Benefits of chip-scale integration include reduced form factor, lower power consumption, higher performance, more functionality, and lower manufacturing cost. Some markets, such as wearable devices can only be accessed through chip-scale integration. Chip-scale integration has been happening for a while in MEMS motion sensors. MEMS accelerometers have progressed from single- to dual- to tri-axis sensing in a packaged, board-mountable component. The same progression has occurred for MEMS gyroscopes. MEMS IMUs now include multiple 3-axis sensors, as well as analog/mixed-signal and [4] digital CMOS ICs, and memory to provide 6- and 9-axis digital output. This trend is only intensifying. The Apple Watch has over 30 dies in Apple’s S1 package. Interestingly, the 6- axis MEMS IMU is separately packaged. At the Consumer Electronics Show (CES) 2016, Intel announced the Intel Curie, a single System-in-Package component with 13 dies including a 6-axis MEMS IMU. Combined, these industry trends provide strong motivation for mainstream CMOS foundries such as TSMC and GlobalFoundries to enter the MEMS market. Both companies have publically stated these motivations and their intentions of supplying MEMS. This will likely mean strong new competition for today’s leading suppliers and further commoditization. Business will become even more competitive for MEMS suppliers, causing some to consolidate or exit and others to pursue niche strategies, such as focusing on high performance, to survive. MEMS consumers, i.e. system integrators, will benefit from even lower costs and a wider selection of components if not suppliers. 4. Are MEMS Inertial Sensors a Disruptive Technology? We will explore this question through the lens of the technology adoption framework described by Clayton Christensen in his classic book The Innovator’s Dilemma [9]. According to Christiansen, suppliers of an incumbent technology focus on pleasing their best customers, which inevitably means evolutionary refinements to the technology
Details
-
File Typepdf
-
Upload Time-
-
Content LanguagesEnglish
-
Upload UserAnonymous/Not logged-in
-
File Pages13 Page
-
File Size-