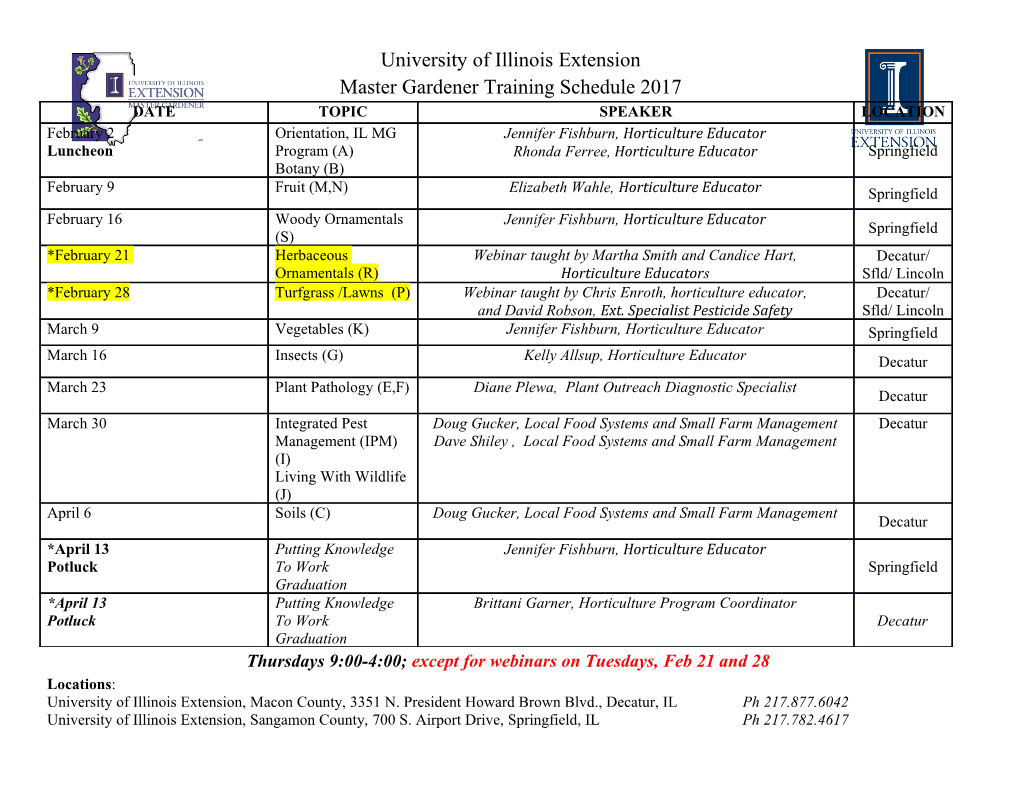
Fumaric Acid Fermentation by Rhizopus oryzae with Integrated Separation Technologies Dissertation Presented in Partial Fulfillment of the Requirements for the Degree Doctor of Philosophy in the Graduate School of The Ohio State University By Kun Zhang, M.S., B.S. Graduate Program in Chemical and Biomolecular Engineering The Ohio State University 2012 Dissertation Committee: Shang-Tian Yang, Advisor Jeffrey J. Chalmers David Wood Copyright by Kun Zhang 2012 ABSTRACT Fumaric acid is a dicarboxylic acid and an indispensible intermediate in the metabolism of many microorganisms. It is used mainly as a food acidulant and as the chemical feedstock for the production of paper resins, unsaturated polyester resins, alkyd resins, plasticizers, and miscellaneous industrial products. Currently, fumaric acid is produced through a petroleum-based chemical method. However, limited deposits of petroleum, increasing production costs and serious environmental repercussions have prompted chemical companies to find an alternative. Fungal fermentation provides a promising solution due to its advantages in environmental friendliness and availability of widespread renewable biomass feedstock. However, conventional fumaric acid fermentation processes suffer from low product yield, low productivity, and high production cost, whereas the competing chemical production methods are currently more economical. Therefore, the goal of this research was to develop effective and economic fermentation and recovery methods for improved fumaric acid production by Rhizopus oryzae. One of the major technical challenges is to control the fungal morphology and physiology for the overproduction of fumaric acid in a sustainable and scalable way. First, an effective fermentation process with good morphology control was developed using soybean meal hydrolysate as the nitrogen source for cell growth and fumaric acid production by R. oryzae. To improve the iii productivity, in situ product recovery by coupling the fermentation with an ion exchange column for fumaric acid adsorption was investigated. In addition, an alternative separation process using adsorption with activated carbon followed with desorption and crystallization with acetone was developed to increase the recovery yield and reduce the production cost. The main results and conclusions are summarized below. First, a simple seed culture medium was developed with soybean meal hydrolysate (SMH) as the nitrogen source for controlling the morphology of R. oryzae ATCC 20344. Uniformly dispersed mycelial clumps with a diameter of ~0.1 mm were formed with enhanced subsequent fumaric acid production. The optimal seed culture conditions were initial pH of 3.0, SMH concentration of 30% (v/v), spore concentration of 8×104/mL and glucose concentration of 10 g/L. With an inoculation size of 25%, the fermentation reached a fumaric acid titer of 50.2 g/L with yield of 0.72 g/g glucose. SMH with a high protein content was a good nitrogen source and the formation of protein precipitate acted as the immobilization carriers for cells. The solid-phase protein also provided a novel method for slow/controlled release that allowed the utilization of the nitrogen source by cells for an extended period without losing cell activity. The fermentation was then studied in a 5-L stirred tank bioreactor (STB) and the results also showed that using SMH as the nitrogen source improved fumaric acid production with increased yield and productivity compared to urea and yeast extract. The effect of CO2 on fumaric acid fermentation was studied. Aeration with air containing 16.7% CO2 increased the productivity by 76% and final product titer by 13%. A product titer of 35.6 g/L, yield of 40% and productivity of 0.4 g/L∙h were obtained in batch fermentation with an initial seeding density of ~5000 mycelial clumps/ml. With CO2 addition, similar iv fumaric acid production in the fermentation was obtained with either CaCO3 or NaOH as the neutralizing agent, indicating that CaCO3 can be replaced with NaOH and CO2 to simplify the downstream process. Separation of fumaric acid from the fermentation broth by adsorption was studied with a strong-basic anion exchange resin IRA900, which was selected because of its high adsorption capacity at the fermentation-favored pH of 5, high selectivity against byproducts (glucose and malic acid) and easy desorption with a high recovery yield. The adsorption isotherm and the mechanism involved in the fumaric acid adsorption onto IRA900 were investigated. The results showed that fumaric acid adsorption onto IRA900 followed the Langmuir isotherm. Also, the adsorption reaction rate between fumaric acid and functional groups of the resin followed the second-order kinetics, indicating a mechanism of two-site-occupancy adsorption reaction between FA2- and resin active sites. However, such a mechanism cannot explain the high adsorption capacity at pH 3 with a high initial fumaric acid concentration. Using an intraparticle diffusion model, it was found that the higher adsorption at pH 3 could be attributed to the higher hydrophobic interaction between neutral fumaric acid molecules and the hydrophobic resin backbone. The separation process using IRA900 ion exchange resin was then scaled up in a fixed bed column with the optimal conditions identified as: the resin in the chloride form, flow rate of 4.10~5.34 ml/min, initial fumaric acid concentration of ~5.0 g/L, and desorption solution of 0.7 mol/L NaCl. It was also found that end product inhibition occurred when the fumaric acid concentration in the medium reached >20 g/L. Therefore, intermittent in situ recovery was used to alleviate the product inhibition and facilitate the subsequent v product separation. A preliminary study showed that fermentation with in situ recovery enhanced product yield by 25% and productivity by 59%. Fermentation produced fumaric acid is usually recovered by precipitation and crystallization of the acid at room temperature. In order to recover the low-concentration fumaric acid (<6.3 g/L) present in the filtrate after crystallization, an integrated separation process was developed for fumaric acid recovery and purification by adsorption with activated carbon followed with desorption and crystallization with acetone. Fumaric acid adsorption on activated carbon was found to be governed by non-electrostatic interactions between the undissociated fumaric acid and the activated carbon. The desorption of fumaric acid from activated carbon was studied using acetone to strip all fumaric acid from activated carbon. After removing acetone by evaporation at 70 oC, fumaric acid crystals were obtained with a high purity and recovery yield. Both activated carbon and acetone can be recovered and reused in the adsorption process. The adsorption and desorption process was then evaluated in a fixed bed column to recover fumaric acid from the fermentation broth, achieving a high recovery yield of 93%. Finally, water sweeping was used to further increase the purity of fumaric acid crystals to >98%. A comparative economic analysis showed that this process could significantly reduce the operational costs and enhance the recovery yield, although it would require additional capital investment. Compared to the conventional recovery process using precipitation, the new process is economically and environmentally favorable with good potential for industrial application. vi DEDICATION Dedicated to my wife and parents vii ACKNOWLEDGEMENTS First, I want to give my special thanks to my advisor, Professor Shang-Tian Yang. Not only his guidance and support throughout my research enabled me to develop a thorough understanding of the subject, but also his patience, understanding and forgiveness taught me how to be a fantastic advisor. It would not have been possible to complete my Ph.D. degree without his invaluable guidance and mentoring. I would like to thank Dr. Jeffrey Chalmers and Dr. David Wood for their time being on my committee and their valuable advices on my research project. I want to give my sincere thanks to all the previous and current laboratory members in our group, especially Dr. Baohua Zhang, Dr. Xiang Zou, Dr. Lijie Zhang for their helpful suggestions and support. Also, I want to thank Ms. Yu Chen for her good job in helping some of my experiments. Financially supports from the United Soybean Board and the Consortium for Plant Biotechnology Research Inc to this project are also acknowledged. Finally, I would like to thank my parents and my parents-in-law for all their support. Special thanks to my wife Qing Zhang as well as our beloved two babies. Without their support, I would have achieved nothing. viii VITA November 1982 ………………………………………………Born-Qingdao, PR China June 2005 ………………………………………………………… B.S. Bioengineering Nanjing University of Technology, Nanjing, PR China June 2008 …………………………………………………………… M.S. Microbiology Nanjing University of Technology, Nanjing, PR China PUBLICATIONS 1. Yang, S.T., Zhang, K., Zhang, B., Huang, H. 2011. Bio-Based Chemicals | Fumaric Acid. In: Murray Moo-Young (ed.), Comprehensive Biotechnology, Second Edition, Volume3, pp.163-177. Elsevier. 2. Zhang, K., Gao, Z., Li, S., Fu, Y., Huang, H., Wei, P., Ji, S. 2008. Multiple target optimizations on the fumaric acid production by Rhizopus oryzae based on Desirability function, China Biotech 28(4): 59-64. 3. Zhang, K., Xu, Q., Li, S., Fu, Y., Gao, Z., Huang, H., 2008. Integrated mutagenesis to screen high fumaric acid producing mutant of Rhizopus oryzae with propylene alcohol resistance.
Details
-
File Typepdf
-
Upload Time-
-
Content LanguagesEnglish
-
Upload UserAnonymous/Not logged-in
-
File Pages230 Page
-
File Size-