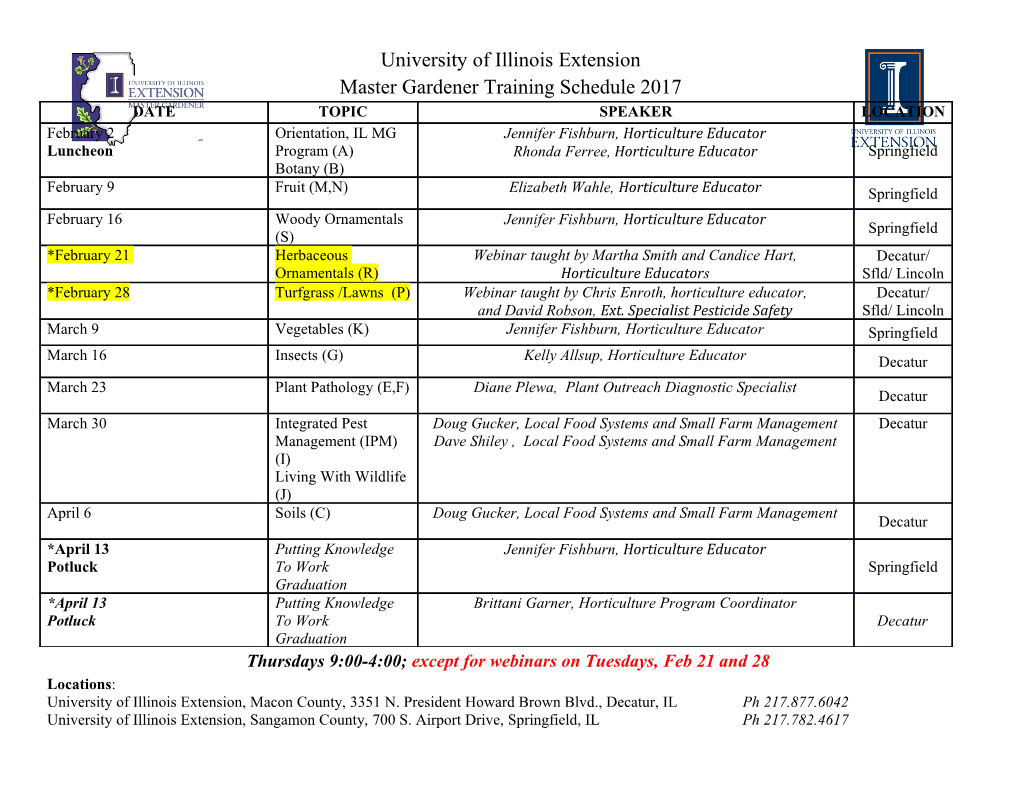
Recycling certain types of digital prints can pose challenges This paper will illustrate the current and future demand for paper and the reasons why recycled paper is becoming necessary to fill the supply gap. It will also explain why all printing technologies are not equally compatible with paper recycling efforts as well as the reasons a small fraction of certain types of ink in the paper load can be problematic. Paper demands for the future In a recent study, “The Future of Paper Recycling in Europe, a final report of COST Action E48,” future trends for the European paper industry were investigated and forecasted. In 2005, 100 million tons of paper was produced. By comparison, in 2015 (or 2020 depending upon the economic situation), the need for paper will increase to 120 million tons. Million ton of EU paper 2005 2015/2020 Communication paper 49 (49%) 54 (45 %) Tissue 6.5 (6.5 %) 9 (7.5 %) Packaging grades 44.5 (44.5 %) 57 (47.5 %) The bulk of the increased demand for paper fiber is expected to be supplied by an increase in collection and reuse of paper fibers. The following text is an excerpt from this report: “Paper recycling has its limits. Each time paper passes around the recycling loop, a certain percentage of the postconsumer paper cannot be recycled due to contamination, inefficient collection systems, process losses, other uses and exports to outside Europe, etc. This lost material must be replaced with either local virgin fibers or papers imported from distant producers. At a regional level, virgin fiber injected into the production sector is necessary to replace the occurring fiber gap. On the other hand, on a company level the overall target frequently is to minimize costs by maximizing recovered paper utilization. The optimum solution for the European market is to try to utilize the recovered paper recycling potential as much as is possible by intensifying collection activities, keeping different recovered paper grades separated during the collection process and improving sorting systems and utilization techniques. The recycling of imported virgin fiber based papers produced in the Nordic countries and the Americas, combined with increasing virgin pulp imports from fast crop rotation regions (such as Latin America and Africa) will ensure the European paper industry maintains a long term, viable and sustainable supply of fiber .” Based on this study, the entire paper recycling industry wants to ensure that the maximum amount of paper can be used as many times as possible in order to guarantee that enough paper is available to fulfill the future demand at affordable prices. Printing technologies that reduce the efficiency or the yield in the paper recycling process can, therefore, be a threat to the industry. This will not only create problems for businesses, but could also result in an inability to fulfill future paper demands. How does paper recycling work? The first step in the deinking process is to mix the paper with water and some detergent. Mechanical energy is then applied to make paper pulp at a slightly increased pH level (8-9). This mechanical action, called pulping, is crucial so that the fibers swell and break off the ink into smaller particles. The next step consists of blowing small air bubbles through the pulp mixture. This process is called flotation, and the foam that is created separates ink particles from the fibers. Most ink materials respond to the air phase better than the water phase; and due to this, the colored particles are removed from the pulp mixture creating a grey foam which is then skimmed. The end product is pure white paper pulp which can be used to create new paper. This process works well with offset inks and is established in all paper recycling plants producing high quality paper throughout the world. Dry toners are OK Dry toners are made from polymers and pigments. These polymers are specially chosen to make the pigments adhere very well to the paper surface after the fusing step. They are also chosen and specially designed to have a certain degree of brittleness. This brittleness is used during the toner manufacturing where the polymer particles are accelerated above the speed of sound and collided into each other. During this collision the particle size is reduced and the right sized and shaped particles are further used in the toner making process. In the pulping phase of the deinking process, these same toner particles are again reduced in size by mechanical means and have the right hydrophobicity to be separated from the paper fibers by soap bubbles. In which cases does it go wrong? There are several cases where this deinking process encounters a lot of difficulties or becomes impossible to perform. The first case is flexo newspaper printing. The binder of these inks is soluble under alkaline conditions releasing very small pigments which do not have the ability to go to the air phase because of their affinity to water. This results in a darkening of the paper pulp making it impossible to use for the desired grade of paper. In order to prevent this from happening, flexo printed newspapers in Italy and the UK are collected separately from the other paper waste wherever possible and are avoided in the rest of Europe. This can be done because of their clear origin which is clearly displayed in the title of these newspapers. Water based inkjet printed material creates basically the same problem; the colorants (dyes or pigments) have an affinity to the water phase. In case of dyes, there is no solution to solve the problem. These colorants are designed to be lightfast and cannot be bleached even in special plants that have bleaching equipment (standard newsprint plants don’t). In any event, pigments as solid materials are not bleachable. Bonding agents Fortunately there are a few prototypes of new pigmented inks that can coagulate or stick together after printing to form larger aggregates. These aggregates then form the right size and are hydrophobic enough to be removed (to be transported by air to the surface). For dye-based inkjet inks, no solution is in sight. The crucial problem is that neither users nor sorting plants can make a distinction between offset, dye- pigmented inkjet and dry-liquid toner based printing, so in these cases it isn’t possible to remove the print from the regular waste stream unless the specific type of print used is clearly marked. Inkjet manufacturers, pigment providers, paper makers and deinking chemical suppliers are working hard to solve this dilemma by using specially coated paper or special agents during printing which make the pigments stick together and, therefore, water insoluble. This helps in removing the ink particles during the flotation step. They only have to make sure that this coagulation on top of the paper surface is sufficiently irreversible, so that the agglomerates do not become soluble again in the pulping phase. This is crucial for this technology since most of the current inkjet inks are not capable of performing this irreversible coagulation. The scientific explanation for this is as follows. The surface of the pigment particles are made hydrophilic by adhesion of specially designed polymeric molecules, one side of which absorbs onto the pigment surface and another part which remains in the water phase. These water phase portions consist mainly of carboxylic groups that are deprotonated to increase the polarity of the pigment and hence the hydrophilicity. The addition of calcium ions in the paper surface during the manufacturing of the paper (Colorlok) helps to improve the image quality but does not improve deinkability because it does not allow the pigments to aggregate. Application of calcium salt solutions through a colorless ink or a precoating just prior to printing, allows the formation of larger insoluble calcium carboxylates that changes the pigment from hydrophilic to hydrophobic. These pigment clusters can then be removed easily by the common deinking procedures. Has the problem been resolved? Not in all cases. In the early days of inkjet, jetting a calcium solution through a fifth nozzle to allow instantaneous coagulation on the paper was attempted. But these calcium ions also have the tendency to react with carbon dioxide in the atmosphere forming insoluble calcium carbonate salts. These insoluble crystals can block the nozzles in the event that the agent is jetted via an inkjet system. In order to prevent this from happening, some manufacturers have changed the calcium ion containing solution with an acidic solution. This has the same effect during printing keeping the pigments on the surface of the paper, avoiding penetration of the color through the paper which creates ghost images on the back side, and creating better color strength. Unfortunately this process is reversible under the alkaline conditions of the deinking process. The carboxylic acids are deprotonated during the pulping phase and become water soluble again with no improvement in terms of deinkability. Adding Acid The only successful way to improve both image quality and deinkability by adding calcium ions is to fully coat the paper with a roller immediately before printing. This allows the wet-in-wet diffusion of particles towards each other to form larger aggregates that are hydrophobic and stable enough to float with the bubbles. Liquid polyethylene based toner and UV inks UV cured inks create a completely different set of problems in the deinking process. UV flexo, UV offset or UV inkjet are all problematic. The same is true for polyethylene-based liquid toner such as electroink. Each of these inks form cross-linked large ink particles that behave totally different from other inks. The large, thin and, in case of liquid toner, very flexible polymer film pieces slip through the screens intended to separate larger impurities from the thin fibers.
Details
-
File Typepdf
-
Upload Time-
-
Content LanguagesEnglish
-
Upload UserAnonymous/Not logged-in
-
File Pages6 Page
-
File Size-