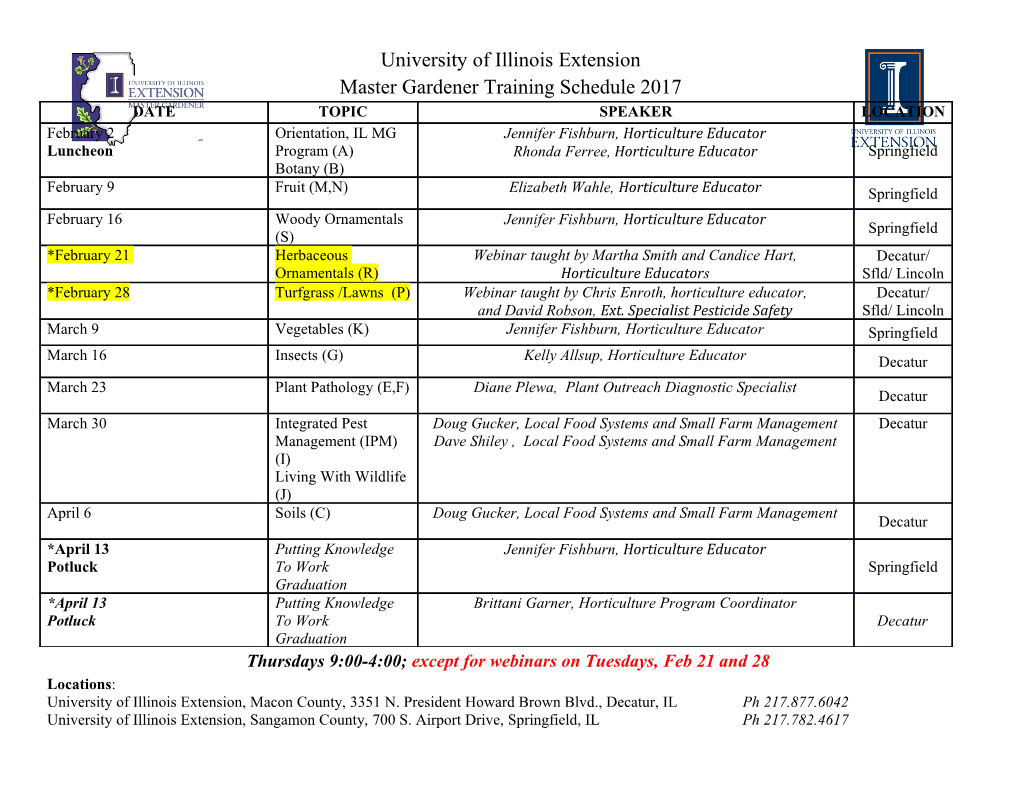
A WELDING RESEARCH SUPPLEMENT TO THE WELDING JOURNAL, FEBRUARY 1990 Sponsored by the American Welding Society and the Welding Research Council - - All papers published in the Welding Journal's Welding Research Supplement undergo Peer Review before publication for: 1) originality of the contribution; 2) technical value to the welding community; 3) prior publication of the material being reviewed; 4) proper credit to others working in the same area; and 5) justification of the conclusions, based on the work performed. The names of the more than 170 individuals serving on the AWS Peer Review Panel are published periodically. All are experts in specific technical areas, and all are volunteers in the program. Electrode Geometry Resistance Spot Welding Ma thema tical model predicts current distribution as a function of electrode geometry BY R. J. BOWERS, C. D. SORENSEN AND T. W. EAGAR ABSTRACT. The effect of electrode ge- tance to the industry is the resistance The roles of welding parameters such as ometry on current distribution has been welding of various galvanized sheet steel upslope, preheat and weld time also have investigated. A mathematical mode! was products, which have become established been analyzed to determine their effects developed to evaluate current distribu- for use in automotive manufacture due to on weldability. Aspects of the electrode tion in both truncated cone (TC) and pim- their corrosion resistance. However, this itself, such as material (Ref. 1) and geom- ple-tipped (PT) electrodes. Electrode life increased corrosion protection is offset by etry (Ref. 2), have been studied as well. and lobe curve tests were conducted to the increased difficulty of welding galva- Friedman and McCauley (Ref. 3) con- substantiate the results of the modeling nized as opposed to uncoated steel. Al- cluded in their study that an uneven heat- effort. Results of the computational inves- loying of the zinc coating with the copper ing condition across the electrodes was tigation showed that electrode sheet in- electrodes used in spot weldingpromotes one. factor that contributed to an in- terface angles approaching 90 deg- pro- rapid wear, subsequently reducirtg elec- creased rate of electrode tip deformation. vide more uniform current distribution at trode life. They explained this uneven heating in the electrode face. Electrode geometry Improving the weldability of galvanized terms of variations in surface resistance was shown to affect wear and life by its steel has been approached by many meth- due to nonuniformities in the steel coat- influence on local current distribution. ods, mainly those concerning the physical ing. The present study approached the Also, electrode geometry shifted the po- properties of the steel, such as coating weldability of galvanized steel in terms of sition of the welding lobe. It was con- composition, type and surface condition. this uneven heating at the electrode face. cluded that efficient electrode design must However, unlike Friedman and McCauley, balance mechanical and thermal proper- electrode geometry and its effect on cur- ties as well as maintain current uniformity. rent uniformity were considered as a KEY WORDS source of uneven heating across the elec- Introduction trode face. Nonuniform current in this re- Resistance Welding gion would give rise to uneven heating, With an average automobile containing Spot Welding which could promote localized wear. approximately 5000 spot welds, the auto- Electrode Geometry Kaiser, et at. (Ref. 4), in a study of weld motive industry is a major user of resistive Current Distribution nugget formation, noted an annular mol- welding technology. Of particular impor- Mathematical Model ten zone around the periphery of some Lobe Curve . welds. This phenomenon was noted by Welding Lobe Lane, eta/.(Ref. 5), who hypothesized that Electrode Design R. 1. BOWERS, C. D. SORENSEN and T. W. Ea- current distribution and electrode geom- Electrode Life Tests etry significantly affect heat generation in gar are with the Materials Processing Center, Galvanized Steel Massachusetts Institute of Technology, Carn- the molten zone. Holm (Ref. 6) explained bridge, Mass. that a current constriction occurs at the WELDING RESEARCH SUPPLEMENT 1 45-s effect of this angle on the degree of cur- rent constriction has not been studied previously. This study used mathematical WATER modeling to quantify effect of electrode - JACKET geometry on current distribution at the ------ electrode face and tested the results to I I determine a relationship between elec- I I trode geometry and electrode life. 1 I I I Mathematical Modeling I I I I Mathematical modeling, based on a fi- 1 I nite element analysis (FEA) program de- veloped by Segerlind (Ref. 9), was used to map the potential distribution along two electrodes in face contact. Only one quad- rant of this configuration was required for modeling due to the ability of the model to accommodate axisymmetric geome- tries and due to the added symmetry of the configuration about the electrode faces - Fig. 1. The geometry was discretized by the model into an array of connected ele- ments - Fig. 2. Subject to the boundary conditions imposed on the geometry and the physical equations describing its inte- 0.0 0.1 0.2 0.3 rior, a response for each element was cal- Fig. 1 -Modeled electrode configuration. Due scale in inches culated so as to maintain continuity be- to symmetry, only the boxed region is required tween all the elements. to be modeled. Fig. 2 -Finite element grid of TC electrode. Cone angle is marked as theta. The Laplace equation, V2^) = 0, where is the electrical potential, was used to describe the electrode interior. This is electrode face, with a disproportionate correct for a DC current or when the amount of current flowing through the magnetic skin depth of the electrodes is outer face edge. Such a phenomenon large with respect to the electrode radius. would aid in explaining the observation of This latter condition is valid for copper al- an annular molten zone at the periphery loy electrodes. of a spot weld. As it was not the intent of this investi- Numerical modeling of the spot weld- gation to produce an exhaustive mathe- ing process has also shown a current con- matical model describing the resistance strictionat the electrode face edge. Green- welding process, electrical conductivity wood (Ref. 7) noted that the current in was considered constant for the purposes resistance welding does not flow directly of this- model. Localized current concen- across the material being welded,, but di- trations give rise to localized resistive verges into the worksheet. Furthermore, heating, which lowers electrical conduc- he stated that most of'the current that tivity and tends to concentrate current spreads into the sheet enters near the elsewhere. This effect could be countered electrode edge, causing a current con- by decreased surface asperity at the outer striction at that location. edge of the electrode face, due to the Greenwood further stated that the ini- friction hill effect, or molten zinc at the tial temperature patterns show a maxi- periphery of the weld due to the large ini- mum in a ring around the edge of the tial current densities, giving rise to an easy electrode. He concluded that if the cur- current flow path. Since such effects oc- rent is high enough to produce a weld in cur in all electrode geometries, the as- such a short time, a ring weld will result. sumption of temperature-independent Such ring welds have been noted in the electrical conductivity was judged to be automotive industry. The results of Nied valid in comparing current uniformity (Ref. 8) concur with those of Greenwood, among different electrode geometries. showing both a current concentration at The model boundary condition consists the periphery of contact between the of a 10-V potential drop across the elec- A - 10 volts electrode and the workpiece, as well as an trode body - Fig. 3. This is not an actual initial temperature maximum in this area. welding condition; however, it was cho- The existence of a current concentra- sen to allow ease of scaling and compar- tion at the outer edge of the electrode ison of results from different electrode B - 0 volts face is in agreement with the fact that geometries. A 10-V isopotential was posi- current constricts around corners. Such a tioned along the outer 0.10 in. (0.25 cm) corner is found in the angle between the of the electrode radius in the plane where No contact resistance tapered end of a truncated cone elec- the water jacket meets the electrode Fig. 3 -Model boundary conditions. trode and the worksheet. However, the body. This condition is based on the 46-s I FEBRUARY 1990 assumption that the current density in the wall surrounding the water jacket is uni- form and axial. A zero-volt isopotential was positioned along the intersection of the electrode faces. The high contact re- sistance occurring at the electrode-sheet interface, as compared to the resistance within the copper electrode, ensures an isopotential at this interface. FEA was utilized to map the voltage po- tential within the electrode. The finite el- ement mesh was finer near the electrode face to obtain a more accurate solution in this, the region of primary interest. Upon obtaining the voltage map, postprocess- irig determined the location of isopoten- tials within the electrode geometry. The model computed voltage values at the corners or nodes of the triangular ele- ments within the geometry; the potential values within the elements were deter- mined by linear interpolation. Current density at the electrode face was calculated as the product of electrical 8.m B.10 0.2B 8.20 0.00 0.lB 0.23 B.30 conductivity and the gradient of the po- scale in inches scale In Inches tential at the electrode face.
Details
-
File Typepdf
-
Upload Time-
-
Content LanguagesEnglish
-
Upload UserAnonymous/Not logged-in
-
File Pages7 Page
-
File Size-