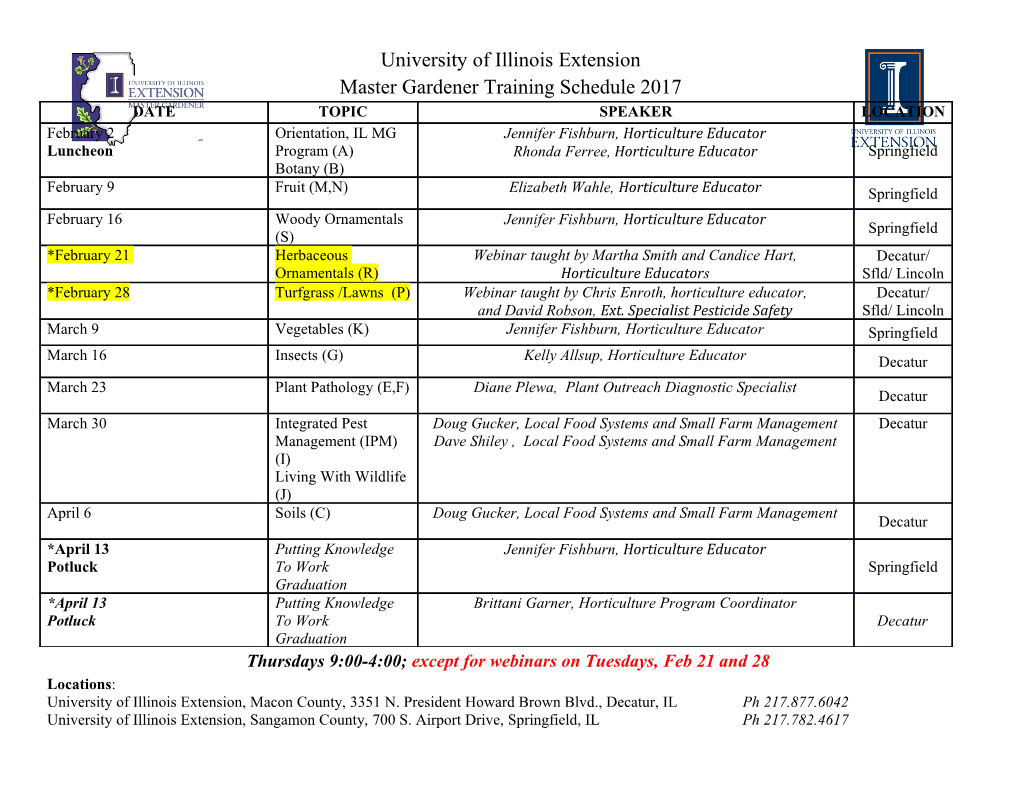
Materials Transactions, Vol. 44, No. 1 (2003) pp. 181 to 187 #2003 The Japan Institute of Metals EXPRESS REGULAR ARTICLE Control of Equilibrium Phases (M,T,S) in the Modified Aluminum Alloy 7175 for Thick Forging Applications Seong Taek Lim1;*, Il Sang Eun2 and Soo Woo Nam1 1Department of Materials Science and Engineering, Korea Advanced Institute of Science and Technology, 373-1Guseong-dong, Yuseong-gu, Daejeon, 305-701,Korea 2Agency for Defence Development, P.O. Box 35-5, Yuseong-gu, Daejeon, 305-600, Korea Microstructural evolutions, especially for the coarse equilibrium phases, M-, T- and S-phase, are investigated in the modified aluminum alloy 7175 during the primary processing of large ingot for thick forging applications. These phases are evolved depending on the constitutional effect, primarily the change of Zn:Mg ratio, and cooling rate following solutionizing. The formation of the S-phase (Al2CuMg) is effectively inhibited by higher Zn:Mg ratio rather than higher solutionizing temperature. The formation of M-phase (MgZn2) and T-phase (Al2Mg3Zn3)is closely related with both constitution of alloying elements and cooling rate. Slow cooling after homogenization promotes the coarse precipitation of the M- and T-phases, but becomes less effective as the Zn:Mg ratio increases. In any case, the alloy with higher Zn:Mg ratio is basically free of both T and S-phases. The stability of these phases is discussed in terms of ternary and quaternary phase diagrams. In addition, the modified alloy, Al–6Zn–2Mg–1.3%Cu, has greatly reduced quench sensitivity through homogeneous precipitation, which is uniquely applicable in 7175 thick forgings. (Received October 7, 2002; Accepted November 12, 2002) Keywords: aluminum alloy 7175, large ingot, Zn:Mg ratio, S-phase, T-phase, homogenization, thick forging, quench sensitivity 1. Introduction system owing to the extended solubility of copper into the precipitates. Besides the minor phases ( =Al2Cu, Z = Aluminum alloy AA7175, one of the newer variants of the Mg2Zn11), the resulting microstructure is generally charac- baseline alloy AA7075, has primarily been designed for the terized by equilibrium phases of soluble M (MgZn2 = ), T 1–3) forging requiring higher strength and damage tolerance. (Al2Mg3Zn3) and their isomorphous phases, S (Al2CuMg), 4,5,11–17) Because of the same alloy composition with AA7075 and insoluble Al7Cu2Fe particles. These phases (5.6Zn–2.5Mg–1.6Cu–0.23Cr) except the lowered impuri- constitute most of the microstructure and govern the general ties, AA7175 is well characterized in the casting, hot working properties. M-phase and its precursors GP zone and inter- and heat treatment areas in the case of small section mediate precipitate (0) are responsible for high strength. thickness. Low melting point T- and S-phases affect hot workability and As a thick forging, however, AA7175 with conventional fracture properties.4,8,10,12,17,18) S-phase has been a main alloy composition is not a good choice due to the massive target to be prevented in the thick 7X49 and 70X0 heavy evolution of coarse equilibrium phases and high quench plates due to its massive appearance and brittleness.8,10,12,18) sensitivity, and therefore usually replaced by 7X50 type The decompositions of these phases are strongly dependent alloys.1–6) In this respect, the alloy should entail the special on the constitution of alloying elements such as controls on the alloy composition and processing for (Zn+Mg+Cu) and Zn:Mg ratio, and on the cooling rate microstructural homogeneity. following solutionizing.3,4,8,10–13,17) Furthemore, the amount There has been a strong tendency for 7xxx alloys to be of equilibrium phases (M,T,S) is essentially determined at the used as large and thick semiproducts.7–10) These thick primary processing stages such as casting and homogeniza- materials, however, often have poor mechanical and fracture tion, eapecially in the less deformed thick materials.4,8–10) properties since they receive less deformation during hot From the backgound mentioned above, the modification of working and slower quench cooling.8–10) This is especially alloy composition for the specific purpose of thick 7175 due to that thick (open die) forgings are usually made of large forging is attempted to control the equilibrium phases. diameter ingots, reaching several hundred milimeters, which Recent studies on this area are concentrated on the 70X0 accompany large dendrite size and concurrent heavy segre- (X ¼ 1; 4; 5) type plate alloys8–10,18) and mostly regarded as gations owing to slow casting speed.4) Through the many proprietaries.9,10) The constitutional study on the 7X75 alloy slow processes, there are frequent evolutions of the coarse forging is not reported yet. In this respect, the effects of alloy equilibrium phases and constituent particles which have an redesign, especially Zn:Mg ratio, and the cooling rate on the adverse effect on strength, damage tolerance and hot work- microstructural evolutions are investigated using real scale ability.8–10,17,18) big ingots and thick forgings of 7175 alloys. From the earlier studies by Strawbridge et al.11) to the recent studies by Li and Starink,12,13) complex phases are 2. Experimental Procedure evolved in the commecial quaternary (Al–Zn–Mg–Cu) The materials used in this study are large forging ingots of *Graduate Student, Korea Advanced Institute of Science and Technology. 7175 type alloys with 700 mm in diameter prepared by DC Present address: Agency for Defence Development, P.O. Box 35-5, semicontinuous casting at Dooray Air Metal in Korea (now Yuseong-gu, Daejeon, 305-600, Korea. 182 S. T. Lim, I. S. Eun and S. W. Nam Table 1 Chemical compositions of 7175 type alloys used in this study. Alloy Si+Fe Cu Mg Zn Cu+Mg Zn+Mg+Cu Zn:Mg AA7175 0.35 max 1.2–2.0 2.1–2.9 5.1–6.1 3.3–4.9 8.4–11.0 1.8–2.9 Alloy A 0.21 1.74 2.80 5.47 4.54 10.01 1.9 Alloy B 0.16 1.50 2.65 5.63 4.15 9.78 2.1 Alloy C 0.13 1.63 2.43 5.78 4.06 9.84 2.4 Alloy D 0.14 1.54 2.05 5.80 3.59 9.39 2.8 Alloy E 0.14 1.32 2.01 6.04 3.33 9.37 3.0 Alcoa Korea) as a 7xxx big ingot feasibility study program. 6.6 KÁminÀ1 from 733–743 K to 523 K are obtained. Casting speed and other variables are carefully controlled to Microstructural characterizations are performed by using avoid ingot cracking and ensure internal structure. Five kinds optical microscopy (OPTIPHOT 100S, NIKON), scanning of alloys given in Table 1 are designed to have different electron microscopy (XL30FEG, PHILIPS) with EDS, and Zn:Mg ratio ranging from 1.9 (alloy A) to 3.0 (alloy E) within transmission electron microscopy (JEOL 4000FX). Thin foils or around the specification limit of commercial AA 7175. for TEM are prepared by mechanical polishing to 150 mm and Contents of chromium are kept minimum (0.18%), and final twin-jet electropolishing in a solution of Fe+Si as low as 0.15 mass% except alloy A. The richer alloy 25%HNO3+75%CH3OH at À20 K and 10 V. group (B,C) and the more dilute alloy group (D,E) have Calorimetric studies are performed in the 2910 DSC respectively the similar total alloying contents. The dilute module in TA Instrument with pure aluminum reference and alloy E has relatively lower Cu and higher Zn:Mg ratio. the sample discs (about 80 mg) at the rate of 10 KÁminÀ1 from The 25 mm square samples are taken at the mid-radius 303 to 803 K. The results are average of three runs. location of ingots and are homogenized at 733 or 743 K for a given time. On the other hand, the 700 mm ingots subject to 3. Results and Discussion open die forging into the intermediate forgings (380 mm diameter, " 1:2) at between 673 and 623 K using 2000 ton 3.1 General Microstructures hydraulic press. The 25 mm square samples are taken at the Figure 1 shows the microstructures of 700 mm diameter mid-radius location of the forgings. Homogenizing treat- ingot (alloy B) in as-cast and as-homogenized conditions at ments and subsequent coolings are also performed in the mid-radius, indicating the change of the microstructure with DSC module where precise coolings at the rate of 0.1– homogenizing procedures. In as cast state (Figs. 1a, b), due to Fig. 1 General micrographs of the large ingots in the alloy B at mid-radius: a) as-cast, b) interdendritic region in a), c) partly homogenized at 733 K for 1 h, and d) fully homogenized at 733 K for 24 h and 743 K for 16 h. Control of Equilibrium Phases (M,T,S) in the Modified Aluminum Alloy 7175 for Thick Forging Applications 183 slow casting speed, cell size reaches about 95 mm and -0.275 Alloy E boundary thickness 25 mm, which is much larger than those -0.300 of small ingots typically 30 mm and 10 mm, respectively. D The large cell is difficult to be homogenized due to the large -0.325 B interdendritic segregations. The main constituents of inter- A dendritic network are identified by EDS mostly as Al–Cu -0.350 T-phase lamella eutectic with very limited amount of magnesium and -0.375 zinc, and Al–Cu–Fe compounds. The former is generally E (Zn / Mg=3.0) 4) W / g Heat Flow, designated by eutectic [M] or T [Al–Cu–Mg–Zn].
Details
-
File Typepdf
-
Upload Time-
-
Content LanguagesEnglish
-
Upload UserAnonymous/Not logged-in
-
File Pages7 Page
-
File Size-