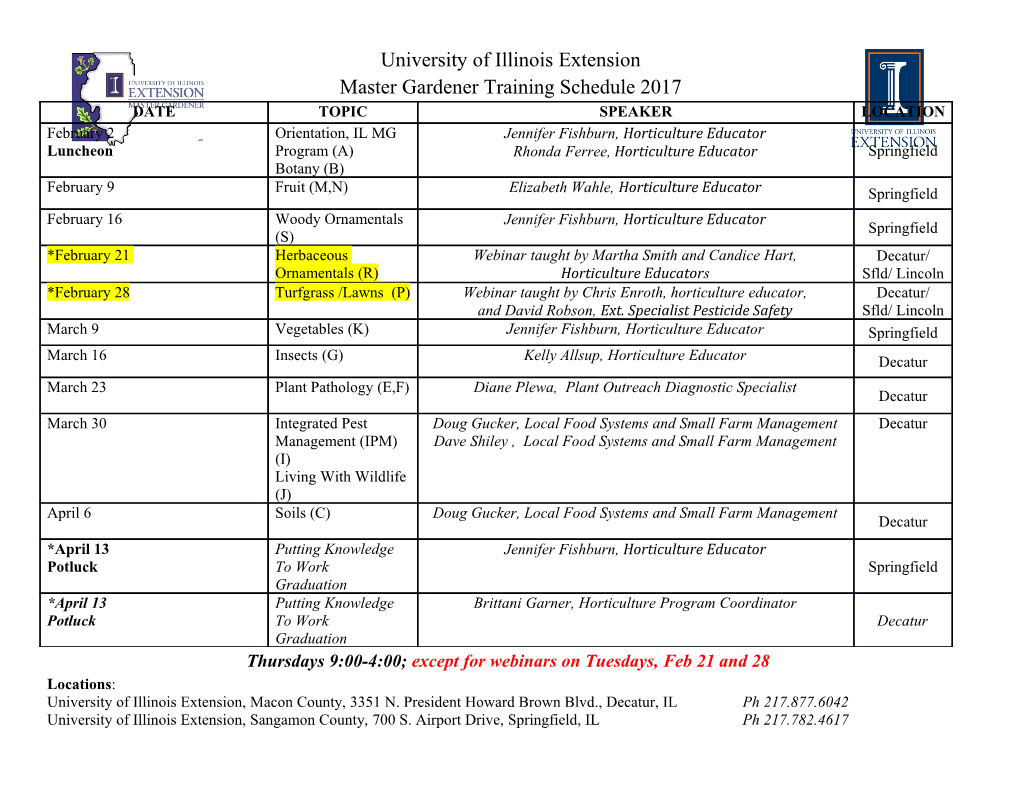
Transactions on the Built Environment vol 12, © 1995 WIT Press, www.witpress.com, ISSN 1743-3509 A general CAD concept and design framework architecture for integrated microsystems^ A. Poppe," J.M. Kararn,*) K. Hoffmann," M. Rencz/ B. Courtois,^ M. Glesner/V. Szekely" "Technical University of Budapest, Department of Electron Devices, H-1521 Budapest, Hungary *77M4/77MC, 46 av. F ^bZ/eA F-J&OJ7 GrgMo6/g Ce^x, France *THDarmstadt, Institute of Microelectronic Systems, D-64283 Darmstadt, Germany Abstract Besides foundry facilities, CAD-tools are also required to move microsystems from research prototypes to an industrial market. CAD tools of microelectronics have been developed for more than 20 years, both in the field of circuit design tools and in the area of TCAD tools. Usually a microelectronics engineer is involved only in one side of the design: either he deals with application design or he is par- ticipating in the manufacturing design, but not in both. This is one point that is to be followed in case of microsystem design, if higher level of design productivity is expected. Another point is that certain standards should also be established in case of microsystem design too: based on selected technologies a set of stan- dard components should be pre-designed and collected in a standard component library. This component library should be available from within microsystem de- sign frameworks which might be well established by a proper configuration and extension of existing 1C design frameworks. A very important point is the devel- opment of proper simulation models of microsystem components that are based on e.g. the FEM results of the pre-design phase and are provided in the form of an analog VHDL script. 1 Introduction In the last decades Computer Aided Design has gained a key importance in the field of microelectronics. Nowadays no 1C can be designed and manufactured without CAD support due to the extremely high level of integration (which is work was supported by the ESPRIT project BARMINT-8173 (Basic Research for Microsystem Integration) Transactions on the Built Environment vol 12, © 1995 WIT Press, www.witpress.com, ISSN 1743-3509 260 Microsystems and Microstructures the result of sophisticated and highly optimized technological processes) and the very small size of individual components. In case of integrated microsystems today we face such a rapid progress in manufacturing and design technologies that have been observed in case of micro- electronics years ago. The increasing level of integration and the small size of the individual components is also characteristic to integrated microsystems, that is one reason, why in searching for integrated microsystems design methodologies and corresponding CAD system architectures the structure of the CAD support of the conventional 1C world seems to be a good pattern to be followed. The following major trends could be observed in case of microelectronics: The design of manufacturing processes and basic construction of components is well separated from the application (circuit) design. The former is performed within the silicon foundries, the application design is performed at users's sites, e.g. in 1C design centers. Process and device design nowadays are coupled in an optimization loop. The CAD tools applied are process simulators (e.g. SUPREM) and device simulators (e.g. MINIMOS). For the optimization loop TCAD frame- works are used (e.g. NORMAN/DEBORA). The design on the application side (circuit design) assumes a given manufac- turing technology and a set of components allowed by the chosen technology. The result of the design process is an abstract representation of the 1C. A very high level of abstraction is e.g. a VHDL description. A lower level of abstraction is the circuit schematic, and finally the circuit layout. The circuit design process is usually speeded up by the application of the prefabrication or pre-design principles. As the level of prefabrication and pre-design decreases, the custom feature increases. A good trade off between the pre-design/prefab and custom features is represented by the standard cell design style. Here the application designer has a limited set of building blocks (standard cells) but has a virtually unlimited freedom in using as many standard elements as he wishes and has got the freedom of interconnecting them as he wishes. Due to the standardization (standard technology such as CMOS, standard circuit building blocks with standard functions such as an AND gate or a flip- flop) in the digital VLSI field, the completely automated design is at a very high level, while in most cases analog VLSI design is performed on transistor level, in a full custom manner. However, it is still true that the application design and the manufacturing design are well separated. The link between the manufacturing design and application design is repre- sented by the design rules, component parameters and simulation models, which are included in standard cell libraries in case of the standard cell de- sign style. The design sent for manufacturing is usually given in a standard structure-description language such as CTF (in case of layout level represen- tation). Transactions on the Built Environment vol 12, © 1995 WIT Press, www.witpress.com, ISSN 1743-3509 Microsystems and Microstructures 261 2 Microsystem design 2.1 The present situation Today microsystem design is characterized by the lack of standards, lack of tools specifically developed for microsystem design and by the lack of sufficiently high level of system integration. If we compare the situation with 1C design then we can state that the situation of microsystem design is very similar to that of the early days of 1C design, when only a few components have been integrated on a die and the design had only a limited CAD support. Higher level of microsystem integration and larger volume of designs may be expected only in case of well established standards and after the strict separation of the process and basic component design from the application design. The present situation is the following: There exists no standard in microsystem structure descriptions (except for the electronics parts). There exists no standard simulation tool developed specifically for microsystems. Instead, standard FEM codes are used (e.g ANSYS) which have been well proven in usual mechanical designs. There is no link between the TCAD tools used for process designs and FEM codes used in structural design of microsystem components. In contrast to microelectronics there is no widely spread standard manufacturing process of microsystems. The possible components in microsystems are based on many diverse op- erational principles, but (except of digital VLSI subsystems) their operation is mainly analog. Another characteristic of integrated microsystems is that such sys- tems are very complex. While an integrated circuit consists basically of an electri- cal system with only a few and in most cases negligible parasitics, in an integrated microsystem there are inherently many co-existing subsystems with different op- erational principles. These different subsystems are interdependent through var- ious cross-coupling phenomena. These phenomena include electro-thermal cou- pling, electro-mechanical coupling, t her mo-mechanical coupling, op to-electrical coupling, etc. 2.2 Principles to be applied in microsystem CAD As stated earlier, the application design (the design of the actual microsystem) and the process and basic structure design should be strictly separated. The tasks in connection with this are the following: A set of compatible manufacturing processes is to be chosen. It may consist of a basic technology that might be e.g. CMOS or BiCMOS and some add-on technologies (such as deposition of different films or extra etching steps). Considering the chosen technologies a set of standard components should be pre-designed. The standard components may include the conventional electri- cal elements, microinechanical elements, chemFETs, elements based on thermal operational principles, optical sensors, etc. The resource intensive (CPU-power, disk, execution time) simulation may be performed only in the pre-design phase, during the development of standard component libraries, for the identification of main component characteristics Transactions on the Built Environment vol 12, © 1995 WIT Press, www.witpress.com, ISSN 1743-3509 262 Microsystems and Microstructures such as the maximal lengths of free-standing poly-Si structures [1], etc. This is the design phase where FEM simulation may be used and should be used. Based on the FEM simulation results, much simple simulation models (to be collected in the standard component libraries) should be established. These models - which are expected to be mainly lumped element equivalents of the components - should be used during the application design. The links between the foundry side and the application side of microsys- tem design should be established in the form of microsystem design rules and a standard microsystem description language. An extension of VHDL - the emerg- ing standard VHDL-A - seems to be a good candidate for being the high level microsystem description language. For physical layout level representation - if planar technologies are used - GIF or GDSII may be well applied, but in case of 3D assemblies an extension of these usual description formats may be needed. Standard links between structural description for FEM simulators, TCAD tools and microsystem layout description languages should be established in or- der to facilitate the physical design of the elements of the standard component libraries 2.3 Benefits By the application of the above principles we may benefit in the following: If we separate the design of manufacturing processes and the design of the component libraries from the application design then a, set of allowed elements may be pre- designed. During the design of the allowed elements the complex cross-coupling phenomena may be considered saving the application designers e.g. from very time consuming FEM simulation sessions.
Details
-
File Typepdf
-
Upload Time-
-
Content LanguagesEnglish
-
Upload UserAnonymous/Not logged-in
-
File Pages8 Page
-
File Size-