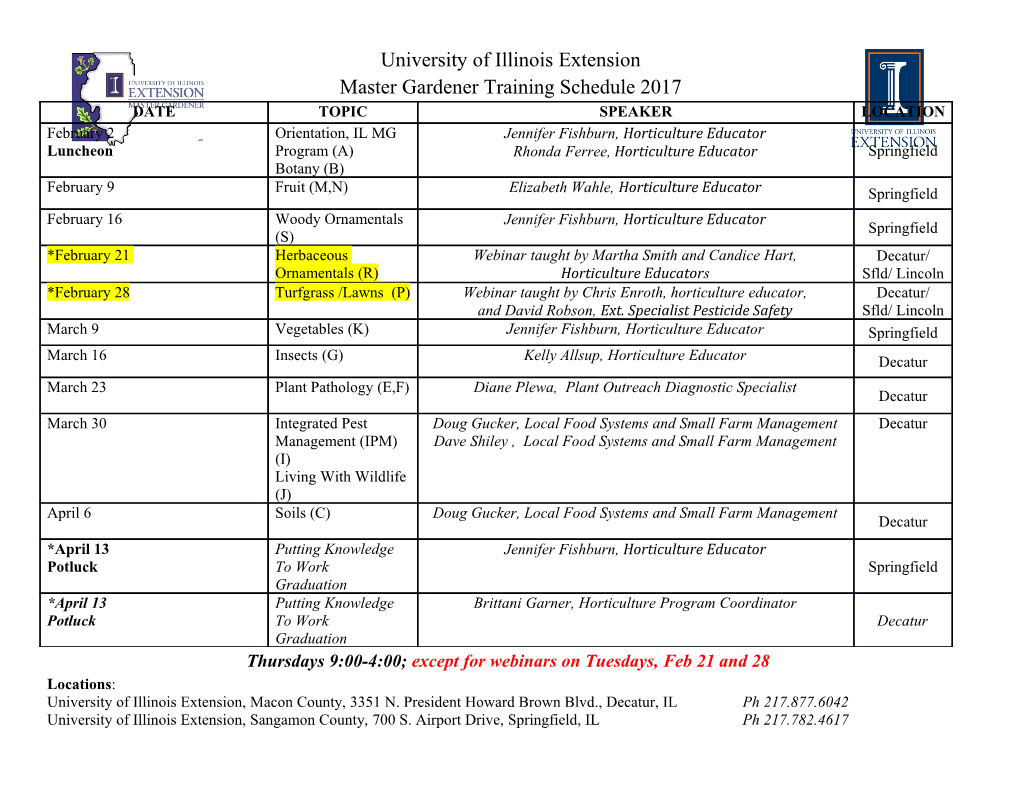
In: Wiley Encyclopedia of Composites, Second Edition. Edited by Luigi Nicolais and Assunta Borzacchiello. © 2012 John Wiley & Sons, Inc. Published 2012 by John Wiley & Sons, Inc. 2012 WOOD-BASED COMPOSITE BOARD regenerated, intensively managed), the type of adhesive, geometry of the wood elements (fibers, flakes, strands, ZHIYONG CAI particles, veneer, lumber), and density of the final product USDA Forest Service, Madison, [9]. Many of the mechanical properties of wood-based com- WI posites tabulated in this article were originally reported in technical and scientific literature. Consequently, they should not be used for direct computation of design values. INTRODUCTION They do, however, provide excellent baseline information on the properties of wood-based composites. The term wood-based composite is used to describe any There are a wide range of engineering properties that wood material bonded together with adhesives. The basic are used to characterize the performance of wood-based wood elements in the production of wood-based compos- composites. Mechanical properties are frequently used ites can be in a great variety of sizes and geometries: to evaluate wood-based composites for structural and fibers, sawdust, shavings, larger particles composed of nonstructural applications. Static elastic and strength many fibers, flakes, strands (Fig. 1), and veneers. These properties are the primary criteria to select materials or to elements can be used alone or in combination. The choice is establish design/product specifications. Elastic properties almost unlimited. Wood-based composite boards are made include modulus of elasticity (MOE) in bending, tension, from these wood elements in a panel form. and compression. Strength properties usually reported Maloney [1] proposed a logical basis for classifying include modulus of rupture (MOR) in bending, compres- wood composites in a bigger family of the wood composite sion strength parallel to surface, tension strength paral- (Table 1). For purposes of this article, these classifi- lel to surface, tension strength perpendicular to surface cations have been slightly modified from those in the (internal bond strength), shear strength, fastener-holding original version to reflect the latest product develop- capacity, and hardness. ments. This article covers only the subgroup listed under Many of the questions that arise with wood-based ‘‘composite materials’’ and processes used to manufacture composites have to do with their mechanical proper- wood-based composite materials. It describes conventional ties; especially how the properties of one type of material wood-based composite panels and structural composite compared to clear wood and other wood products. While materials intended for general construction and/or interior an extensive review that compares all the properties of use. This article also describes wood–nonwood composites. wood-based materials and products is beyond the scope Conventional wood-based composite products are man- of this article, Table 3 provides some insight into how ufactured primarily from wood with only a few percent the static bending properties of these materials vary, and resin and other additives. Product types can be subcatego- how their properties compare with clear wood. Although rized on the basis of the physical configuration of the wood most wood composites might not have as high mechanical elements used to make these products: veneer, particle, properties as solid wood, they provide very consistent and strand, or fiber (Fig. 2). Morphology of the wood elements uniform performance [10]. influences the properties of composite materials, and can be controlled by selection of the wood raw material and by the processing techniques used to generate the wood WOOD ELEMENTS elements. Composite properties can also be controlled by segregation and stratification of wood elements having Conventional wood-based composites are composed pri- different morphologies in different layers of the composite marily of wood elements (often 90% or more by mass) material. In conventional wood-based composites, prop- bound together with a resin and other additives. Figure 1 erties can also be controlled by the use of adhesives shows the relative size of the common wood elements used with different curing rate in different layers. Varying the in wood-based composites from top, left clockwise: shav- physical configuration of the wood element, adjusting the ings, sawdust, fiber, large particles, flakes, and strands. density profile of the composite, adjusting adhesive resin, Figure 2 shows the various composite products. or adding chemical additives is just a few of the many ways to influence the properties. Wood-based composites ADHESIVES are used for a number of structural and nonstructural applications including panels for exterior, interior, and fur- Commonly used resin or binder systems in wood-based niture uses. Performance standards are in place for many composites include phenol-formaldehyde (PF), urea- conventional wood-based composite products (Table 2). formaldehyde (UF), melamine-formaldehyde, and iso- Generally, wood-based composites provide uniform cyanate. The selection of the resin system is dependent on and predictable in-service performance, largely as a the process, cost, product standards, and applications. consequence of standards used to monitor and control their manufacturing process. The mechanical properties of Phenol-formaldehyde wood composites depend on a variety of factors, including PF resins, commonly referred to as phenolic resins,are wood species, forest management regimes (naturally typically used in the manufacture of construction ply- Wiley Encyclopedia of Composites, Second Edition. Edited by Luigi Nicolais and Assunta Borzacchiello. © 2012 John Wiley & Sons, Inc. Published 2012 by John Wiley & Sons, Inc. 1 2 WOOD-BASED COMPOSITE BOARD Figure 1. Common wood elements used in wood-based com- Figure 2. Examples of various composite products. From clock- posites from top, left clockwise: shavings, sawdust, fiber, large wise from top left: laminated veneer lumber, parallel strand particles, flakes, and strands. lumber, laminated strand lumber, plywood, oriented strand board, particleboard, and fiberboard. Table 1. Classification of Wood-Based Compositesa Veneer-based material material shortly after emergence from the press is a fairly Plywood common industrial practice, used to attain adequate resin Laminated veneer lumber (LVL) cure without greatly extending press time. Significant Parallel-strand lumber (PSL) heat exposure associated with pressing of phenolic-bonded Laminates composites commonly results in a noticeable reduction in Glue-laminated timbers their hygroscopicity. Cured phenolic resins remain chem- Overlayed materials ically stable at elevated temperatures, even under wet Laminated wood–nonwood compositesb Multi wood composites (COM-PLYc) conditions. The PF resin bonds are sometimes referred to as being boil-proof because of their ability to maintain Composite boards the structural integrity and adequate bonding after boil- Fiberboard (low-, medium- or high-density) ing water test. The inherently darker color of PF resin Hardboard compared with other resins may make them aestheti- Particleboard Waferboard cally unsuitable for product applications such as interior Flakeboard paneling and furniture. Oriented strand board (OSB) Laminated strand lumber (LSL) Urea-formaldehyde Oriented strand lumber (OSL) UF resins are typically used in the manufacture of prod- Edge-adhesive-bonded material ucts used in interior applications, for example, particle- Edge-glued and ripped panels for lumber board and medium-density fiberboard (MDF). They cure Systems at lower temperatures than PF resins. Excessive heat I-beams exposure will result in chemical break-down of cured UF T-beam panels resins. Therefore UF-bonded panels are typically cooled Stress-skin panels after emergence from the press. UF resins are the lowest Trusses-metal tooth connected cost thermosetting adhesive resins. They offer light color, Box-beams Structural insulated panels (SIPS) which often is a requirement in the manufacture of dec- orative products. However, the release of formaldehyde Wood–nonwood composites from products bonded with UF is a growing health and Wood fiber–polymer composites environmental concern. Inorganic-bonded composites aSource: Adapted from Ref. 1. Melamine-formaldehyde bPanels or shaped materials combined with nonwood materials such as metal, plastic, and fiberglass. Melamine-formaldehyde (MF) resins are used primarily cRegistered trademark of APA—The Engineered Wood Association. for decorative laminates, paper treating, and paper coat- ing. They are typically more expensive than PF resins. wood and oriented strand board (OSB) where exposure MF resins may, despite their high cost, be used in bonding to weather during construction is a concern. Phenolic conventional wood-based composites. When used in this resins are relatively slow-curing compared with other application, they typically are blended with UF resins. thermosetting resins. In hot-pressed wood-based compos- Melamine-UF resins are used where an inconspicuous ites, use of phenolic resin necessitates longer press times (light color) adhesive is needed, and greater water resis- and higher press temperatures. Hot-stacking of pressed tance that can be attained with UF resin is required. WOOD-BASED COMPOSITE BOARD 3 Table 2. Commercial Product or Performance Standards for Wood-Based Composites Product Applicable Standard
Details
-
File Typepdf
-
Upload Time-
-
Content LanguagesEnglish
-
Upload UserAnonymous/Not logged-in
-
File Pages11 Page
-
File Size-