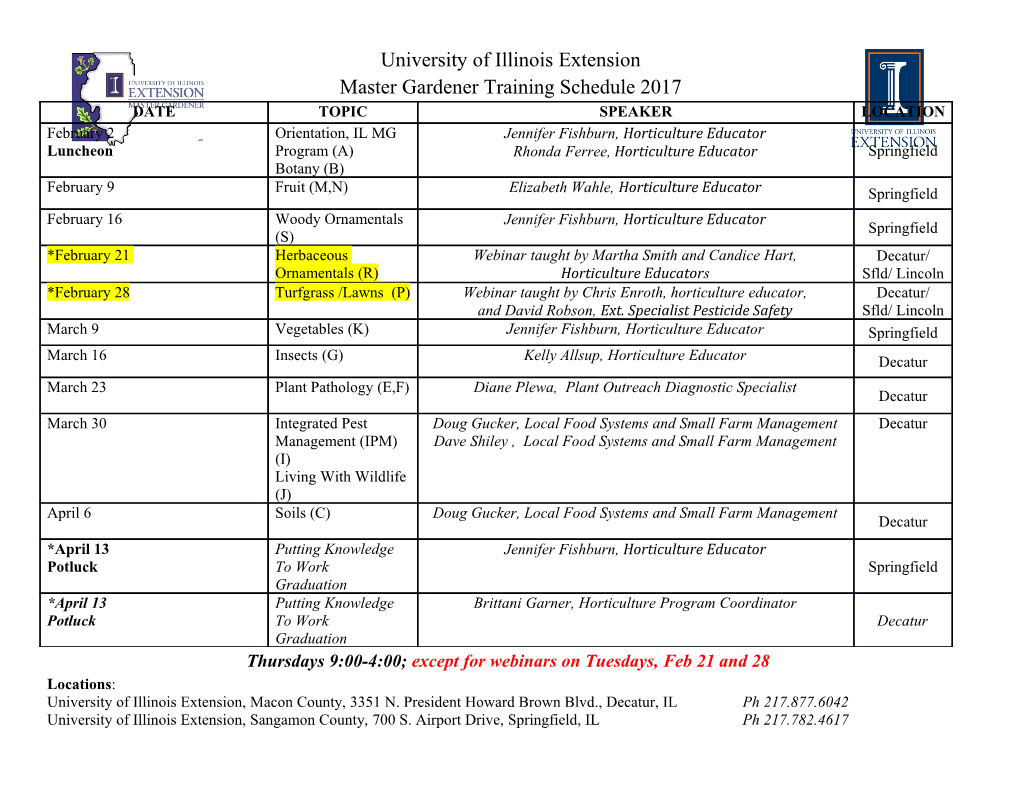
NUCLEAR – 2013 █ ███████████████████████████████████████████████████████████████████████████████████████████████████████████████████████████████████████████████████████████████████████████████████████████████████████████████████ CORROSION MECHANISMS OF TUBES FROM THE CANDU HIGH PRESSURE FEED WATER HEATERS M. FULGER*, M. MIHALACHE*, L. VELCIU*, I. VITELARU** *Institute for Nuclear Research Pitesti, Romania, [email protected] ** Cernavoda Nuclear power Plant, Romania ABSTRACT This study has been carried out to investigate the corrosion mechanism developed on stainless steel tubes from HP Feed Water Heater in a CANDU NPP. With this goal in mind, specimens of the failed tubes removed from HP Feed Water Heater were analyzed in laboratory by different methods (visual examination, scanning electron microscopy (SEM) and optical microscopy). The corrosion deposits from the surfaces of tubes were examined by energy dispersive X-ray spectrometry method (EDX) to identify the chemical composition. The results of the laboratory tests showed that the tubes failed by OD (outside diameter) chloride induced stress corrosion cracking mechanism. Stress corrosion cracking (SCC) is a form of slow crack growth that occurs when a susceptible alloy is stressed in a specific corrosive environment. Cracks were independent of tube support locations and welds. The corrosion mechanism and possible causes identified are presented, followed by conclusions and recommendations for corrosion minimization Key words: HP feed water heater, stress corrosion cracking, SEM, EDS Introduction The Feedwater Heating System uses extraction steam to preheat the feedwater in order to optimize thermodynamic efficiency and to raise the temperature at the desired value for admission in the steam generators. Feedwater heaters normally operate as counterflow heat exchangers. Malfunctioning of feedwater heaters can significantly affect power plant efficiency by increasing heat rate and/or decreasing generation capacity. These heaters can fail due to vibration, flashing of drain flow, inadequate level control, steam impingement, erosion, and/or corrosion. Failures have been identified in the following major physical locations: tubes, condensing, and drain cooler zones [1]. The major mechanisms identified to affect the feed water heaters are as follows: Uniform or General Corrosion - characterized by a chemical or electrochemical reaction that proceeds uniformly over the entire exposed surface or a substantial portion of that surface. The metal becomes progressively thinner and eventually fails because of the stress loadings imposed on it. Crevice Corrosion and Pitting are partly discussed together because they are mechanically similar and partly because, in feed water heater tubes, they are often phenomenologically similar. The term "pitting" should be used to describe the corrosion that follows the local breakdown of a protective (e.g., passive) ███████████████████████████████████████████████████████████████████████████████████████████████████████████████████████████████████████████████████████████████████ █████████████████████████████████████████████████ 125 ████████████████████████████████████████████████████████████████████████████████████████████████████████████████████████████████████████████████████████████████████████████████████████████████████████████████████ NUCLEAR – 2013 █ ███████████████████████████████████████████████████████████████████████████████████████████████████████████████████████████████████████████████████████████████████████████████████████████████████████████████████ film on a metal surface. Crevice corrosion, on the other hand, is a localized corrosion of a metal surface adjacent to an area shielded from full exposure to the environment. Crevice corrosion may occur, under porous scales, corrosion products, mud or debris. When the creviced areas are small, the resulting localized corrosion may resemble pitting attack. In pitting and crevice corrosion, chlorides play a critical role, tubes presenting localized corrosion when the environment contain more than 10000 ppm chlorides. [2]. Galvanic Corrosion - is the accelerated corrosion of a metal that occurs because of an electrical contact with more noble metal in a corrosive solution. The less resistance metal is described as anodic and the more resistance metal as cathodic.[2,3]. Erosion Corrosion or water side "impingement attack" is a form of localized corrosion that occurs on the water side of the tubes in areas where the turbulence intensity at the metal surface is high enough to cause mechanical disruption of the protective oxide film. Stress Corrosion Cracking (SCC) is a form of slow crack growth that occurs when a susceptible alloy is stressed in a specific corrosive environment. Generaly, in feed water heaters, most of the SCC failures are initiated on the steam side of the stainless stel tubes, though a limited number of SCC failures are reported in water side[2,3]. This study has been carried out to investigate the degradation mechanism developed on plugged tubes removed from Cernavoda Unit 1 HP feed water heater after 15 years of operation. The specifications of the tubes and operation parameters were as follows: - On the outer side of tubes, flow steam and condense with an inlet temperature of 190oC, outlet temperature of 151.2o C and pressure of 15 bar. - On the inner side of tubes, flow demineralized water with inlet temperature of 145.7oC, outlet temperature of de 167.2o C and pressure of 90 bar. - The tubes are made of SA 213 TP 304 stainless steel with 1.25mm wall thickness. The heat exchange surface of the feed water heater contains a number of 1200 U-tubes with a radiant surface of 2013m2. The total length of the feed water heater is nearly 15 m with tubing supports at 1.5m distance. Experimental To investigate the damage mechanism of tubes the following analyses have been performed: Visual examination - preliminary visual examination of the degraded components with extensive photographic documentations precedes any mechanical testing or any metallurgical examination. A photographic record is useful for subsequent reference or comparison Metallography analysis includes a macroscopic examination of the surface of the selected specimen followed by a microscopic examination of etched and unetched material as well as transverse and longitudinal cross sections. Has been used a metallographic microscope OLYMPUS GX 71 type which permits magnifications in the range of x 12.5 - x 2000. For microscopic examination which include analysis of damaged surfaces, secondary cracks, abnormalities, origin of fracture, and direction of the crack growth, has been used a TESCAN VEGA II LMU electron microscope operating up to 30 kV. This device is equipped with 3 detectors: a secondary electron (SE) detector, a back-scattered electron (BSE) detector and energy dispersive X – ray spectrometer (EDS). Chemical analysis of the corrosion products composition- may follow the metallurgical analysis for surface characterization, depending on the investigation. ███████████████████████████████████████████████████████████████████████████████████████████████████████████████████████████████████████████████████████████████████ █████████████████████████████████████████████████ 126 ████████████████████████████████████████████████████████████████████████████████████████████████████████████████████████████████████████████████████████████████████████████████████████████████████████████████████ NUCLEAR – 2013 █ ███████████████████████████████████████████████████████████████████████████████████████████████████████████████████████████████████████████████████████████████████████████████████████████████████████████████████ Results and discussions Visual examination has been made on the entire length of tubes and was recorded photographs for a better comparison. After visual examination, for an easier manipulation in further analyses, the tubes have been cut in pieces of 2 cm of length (Figure 1). At the first visualization the information was following: - the tube noted T1 is curved at one extremity which indicates the proximity to the U–bend (Figure 1). - on the both tubes surfaces there are scratches probably resulted from manipulation and marks resulted from friction with supports of tubes . - only on the one side of both tubes have been remarked red oxides and hard deposits formed above a continuous black oxide (magnetite) while on the reverse side there is a magnetite layer maintained almost intact (Figure 2). T1 T2 Figure 3 Photographs showing the tubes T1 and T2 segmented for analysis T1 T2 Figure 4 Photographs showing the degraded side and reverse outside of tubes T1 and T2 The first conclusion was that the degraded faces of tubes were up warded being subjected to small droplets of water which eroded tubes while the reverse sides were safely, just dry steam was in contact with its. Metallography analysis Using an optical microscope there were visible corrosion products deposits covering the most of the outside diameter (OD) surface as shown in Figure 3. On the inside surface of tubes there were not observed deposits, only an adherent oxide layer. Scanning the tubes out side surfaces at higher magnifications has been put in evidence small pits coated by red oxides (Figure 4). In Figure 5 are shown the morphologies of the inside surfaces of tubes which appeared covered with a black oxide. The spalling of the oxides occured owing to flowing of internal fluid. Another disturbances of the internal surfaces not been
Details
-
File Typepdf
-
Upload Time-
-
Content LanguagesEnglish
-
Upload UserAnonymous/Not logged-in
-
File Pages9 Page
-
File Size-