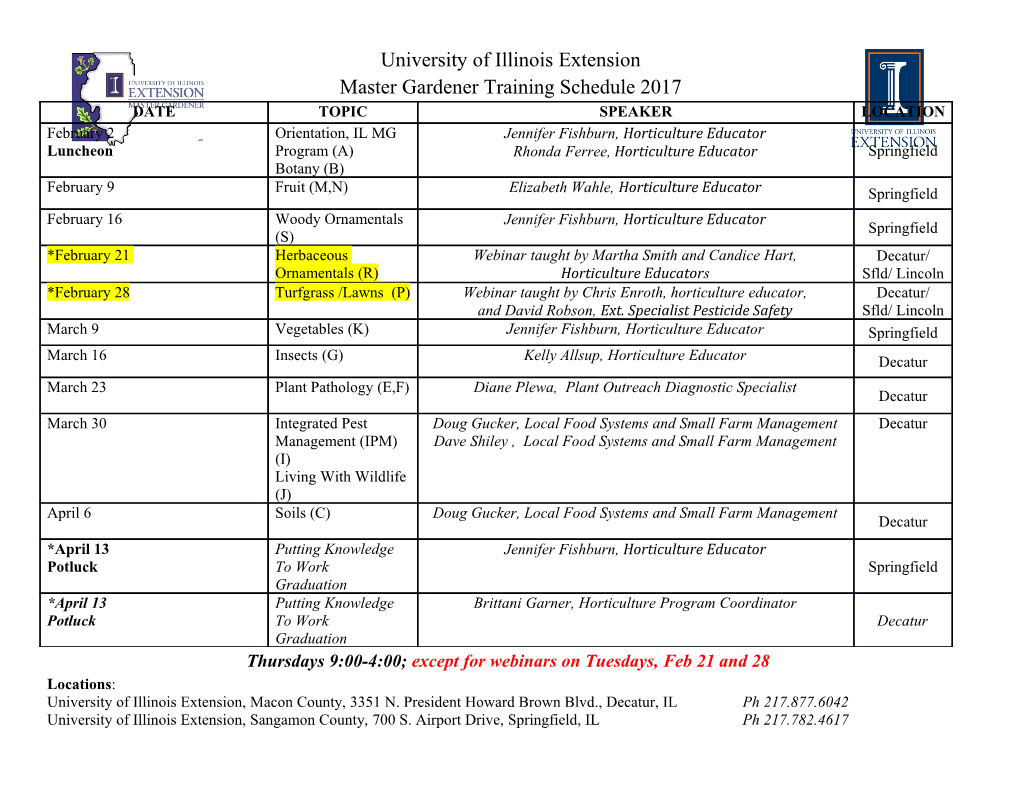
View metadata, citation and similar papers at core.ac.uk brought to you by CORE provided by ethesis@nitr STUDY OF DIFFERENT OPERATING PARAMETERS OF FCC UNIT WITH ASPEN-HYSYS A thesis submitted in partial fulfillment of the requirements for the degree of Bachelor of Technology in Chemical Engineering by ASHISH S. KHANDEPARKER Roll No: 108CH022 Under the Guidance of Prof. Arvind Kumar DEPARTMENT OF CHEMICAL ENGINEERING NATIONAL INSTITUTE OF TECHNOLOGY, ROURKELA May, 2012 1 CERTIFICATE This is to certify that the project report entitle “Study of different operating parameters of FCC unitwith Aspen-HYSYS” submitted by ASHISH S. KHANDEPARKER (ROLL NO: 108CH022) in the partial fulfillment of the requirement for the degree of the B.Tech in Chemical Engineering, National Institute of Technology, Rourkela is an authentic work carried out by him under my super vision. To the best of my knowledge the matter embodied in the report has not been submitted to any other university/institute for any degree. DATE: 11th May 2012 Dr. Arvind Kumar Department Of Chemical Engineering National Institute of Technology, Rourkela, Pin-769008. 2 ACKNOWLEDGEMENT I avail this opportunity to express my indebtedness to my guide Dr. Arvind Kumar, Chemical Engineering Department, National Institute of Technology, Rourkela, for his valuable guidance, constant encouragement and help at various stages for the execution of this project. I also express my sincere gratitude to Prof. R. K. Singh (HOD) and Prof. Dr. H.M. Jena (Project Coordinator), of Department of Chemical Engineering, National Institute of Technology, Rourkela, for their valuable guidance and timely suggestions during the entire duration of my project work, without which this work would not have been possible. Submitted By: Ashish S. Khandeparker Roll No: 108CH022 Chemical Engineering Department National Institute Of Technology, Rourkela Rourkela-769008 3 ABSTRACT Fluid catalytic cracking unit (FCCU) is known as the heart of the modern refinery process. An FCC gives a product specific process eliminating undesired products to a larger extent. While it is mostly used to increase the production of gasoline, it also has the ability to give different products like propylene and butylene under different conditions. Crude oil contains hundreds of hydrocarbons from light gases to molecules boiling above 343 °C, most of the molecules being in the higher end. About 30 % of the feed to the distillation column cannot be separated into usable fractions in the market. FCC uses this as its feed, the atmospheric gas oil and vacuum gas oil. An FCC is used to produce low molecular weight compounds like gasoline from heavier molecules by the process of catalytic cracking. In this project, a basic refinery process was designed and the atmospheric gas oil from the distillation column was used as feed in the FCC unit.The plant data was referred from the plant data collected by Theologous et al. in which few changes were made in order to achieve proper simulation. A variation of certain parameters was also carried out to give a view of the effect of these parameters on the production of Naphtha, coke and the total conversion in the FCC unit. Two different catalysts were also used and product yield was noted. The effect of dual riser with respect to one riser was also carried under a specific range. Keywords: Fluidized Catalytic Cracking Unit, Naphtha, Coke, Conversion, catalyst, riser. 4 Table of Contents ACKNOWLEDGEMENT ............................................................................................................................. 3 ABSTRACT ................................................................................................................................................ 4 LIST OF FIGURES ...................................................................................................................................... 6 LIST OF TABLES ........................................................................................................................................ 7 1. INTRODUCTION ............................................................................................................................... 8 2. LITERATURE REVIEW ..................................................................................................................... 11 2.1. Prominent Components in a Typical Refinery ...................................................................... 11 2.1.1. Crude distillation unit (CDU): ........................................................................................ 11 2.1.2. Vacuum distillation unit: ............................................................................................... 12 2.1.3. Separators: .................................................................................................................... 12 2.1.4. Blending pools: .............................................................................................................. 12 2.1.5. Fluidized Catalytic Cracking Unit: .................................................................................. 12 2.2. Pseudo-components ............................................................................................................. 14 2.3. Catalysts ................................................................................................................................ 15 3. DESCRIPTION OF THE SIMULATION .............................................................................................. 17 3.1. PROBLEM DESCRIPTION ........................................................................................................ 17 3.2. ASPEN HYSYS SIMULATION ................................................................................................... 17 3.3. SIMULATION.......................................................................................................................... 17 3.3.1. Process Flow Diagram ................................................................................................... 17 3.3.2. The Process ................................................................................................................... 20 3.3.3. The components or the blocks or the equipments ....................................................... 21 4. RESULTS AND DISCUSSION: .......................................................................................................... 24 4.1. Effects of C/O Ratio ............................................................................................................... 24 4.2. Effect of Feed Temperature .................................................................................................. 26 4.3. Effect of Flowrate .................................................................................................................. 27 4.4. Effect of Reactor Pressure .................................................................................................... 28 4.5. Effect of Flowrate on Reactors.............................................................................................. 29 4.6. Comparison between One-Riser and Dual Riser ................................................................... 30 4.7. Effect of Riser Height ............................................................................................................ 32 5. CONCLUSION ................................................................................................................................. 33 6. REFERENCES: ................................................................................................................................. 34 7. APPENDIX ...................................................................................................................................... 36 5 LIST OF FIGURES Figure 1: Schematic of the Fluid Catalytic Cracking Unit…………………………………...10 Figure 2: Boiling Temperature vs. Liq. Vol. % for pseudo components……………….........15 Figure 3: PFD of the simulation carried out in ASPEN HYSYS……………..……………..19 Figure 4: Effect C/O Ratio on Naphtha Yield.……………………….……………………...25 Figure 5: Effect C/O Ratio on Conversion.……………………….………………………....25 Figure 6: Effect C/O Ratio on Coke Yield.…....…………………………………….............26 Figure 7: Effect of Feed Flow Rate on Naphtha Yield.......………………………….............27 Figure 8: Effect of Feed Flow Rate on Conversion…….......………………………………..28 Figure 9: Effect of reactor pressure on Naphtha yield....……………….…………..……….28 Figure 10: Effect of Feed Flow rate on of naphtha yield of One riser and Dual Riser...........29 Figure 11: Effect of riser height on naphtha yield……………………………………..........32 6 LIST OF TABLES Table 1: Fluid Catalytic Cracking Unit Conditions……………………………………….....11 Table 2: Comparison of Amorphous and Zeolite catalysts ………………………………….15 Table 3: Crude Petroleum Simulation Feedstock Properties …………………………….....22 Table 4: Bulk Crude Properties………………………………………………………………22 Table 5: Light Ends Liquid Volume Percent of Crude Petroleum Feedstock…………….....22 Table 6: API Gravity Assay of Crude Petroleum Feedstock …………………………….....22 Table 7: Viscosity Assay of Crude Petroleum Feedstock……………………………………22 Table 8: TBP Distillation Assay of Crude Petroleum Feedstock…………………………….23 Table 9: Atmospheric Distillation Tower Product Properties…………………………….....23 Table 10: Outlet Composition Results from FCC simulation…………………………...…...24 Table 11: Variation of naphtha & coke yield, total conversion with feed temperature…......26
Details
-
File Typepdf
-
Upload Time-
-
Content LanguagesEnglish
-
Upload UserAnonymous/Not logged-in
-
File Pages47 Page
-
File Size-