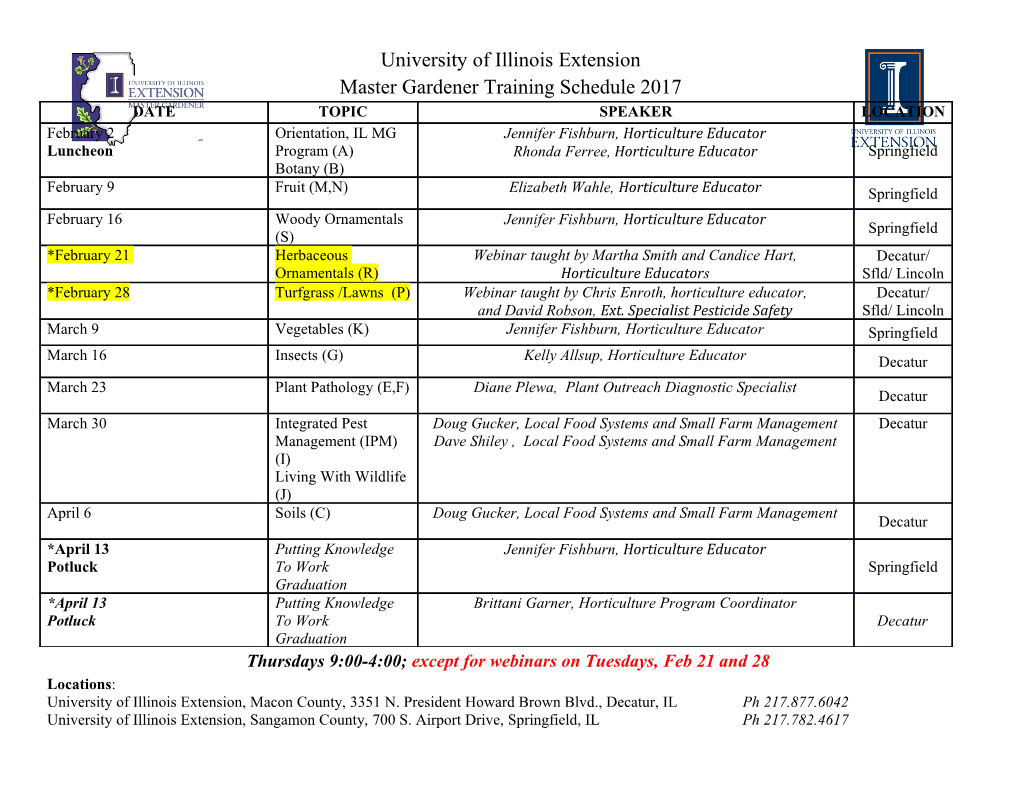
The Recent Trends in Production: 1. Flexibility: The ability to adapt quickly to changes in volumes of demand, in the product mix demanded, and in product design or delivery schedules, has become a major competitive strategy and a competitive advantage to the firms. This is sometimes called as agile (move quickly) manufacturing. 2. Total Quality Management: TQM approach has been adopted by many firms to achieve customer satisfaction by a never ending quest for improving the quality of goods and services. 3. Time Reduction: Reduction of manufacturing cycle time and speed to marker for a new product provide a competitive edge to a firm over other firms. When companies can provide products at the same price and quality, quicker delivery (short lead time) provide one firm competitive edge over the other. 4. Worker Involvement: The recent trend is to assign responsibility for decision making and problem solving to the lower levels in the organization. This is known as employee involvement and empowerment. Examples of employee’s empowerment are quality circle and use of work teams or quality improvement teams. 5. Business Process Re-engineering: BPR involves drastic measures or break-through improvements to improve the performance of a firm. It involves the concept of clean- state approach or starting from a scratch in redesigning in business processes. 6. Global Market Place: Globalization of business has compelled many manufacturing firms to give operations in many countries where they have certain economic advantage. This has resulted in a steep increase in the level of competition among manufacturing firms throughout the world. 7. Operations Strategy: More and more firms are recognizing the importance of operations strategy for the overall success of their business and the necessity for relating it to their overall business strategy. 8. Lean production: Production system have become lean production systems which have minimal amount of resources to produce a high volume of high quality goods with some variety. These systems use flexible manufacturing systems and multi- skilled workforce to have advantages of both mass production and job production. 9. Just in time production: JIT is a ‘pull’ (not push) system of production, so actual orders provide a signal for when a product should be manufactured. Demand-pull enables a firm to produce only what is required, in the correct quantity and at the correct time. This means that stock levels of raw materials, components, work in progress and finished goods can be kept to a minimum. This requires a carefully planned scheduling and flow of resources through the production process. For example, a car manufacturing plant might receive exactly the right number and type of tyres for one day’s production, and the supplier would be expected to deliver them to the correct loading bay (time gap) on the production line within a very narrow time slot. 10. Computer Aided Manufacturing: Computer-aided manufacturing (CAM) is the use of computer-based software tools that assist engineers and machinists in manufacturing or prototyping product components. CAM is a programming tool that makes it possible to manufacture physical models using computer-aided design (CAD) programs. CAM creates real life versions of components designed within a software package. CAM was first used in 1971 for car body design and tooling. 11. Computer Aided Design: Computer-aided design (CAD) is the use of computer technology to aid in the design and particularly the drafting (technical drawing and engineering drawing) of a part or product, including entire buildings. It is both a visual (or drawing) and symbol-based method of communication whose conventions are particular to a specific technical field. 12. E-Supply Chain Management: Supply chain management is the management of supply chain from suppliers to final customers reduces the cost of transportation, warehousing and distribution throughout the supply chain. But SCM was a traditional concept which is now being replaced by E-SCM. E-Supply chain management is a series of Internet enabled value-adding activities to guarantee products created by a manufacturing process can eventually meet customer requirements and realize returns on investment. Supply chains have advanced in the last two decades with improved efficiency, agility and accuracy. The recent advancement of Internet technology has brought more powerful support to improving supply chain performance. In this context, e-supply chain management becomes a new term that distinguishes itself by net-centric and real-time features from traditional supply chain management. 13. 14. Enterprise Resource Planning: Enterprise resource planning (ERP) is an enterprise- wide information system designed to coordinate all the resources, information, and activities needed to complete business processes such as order fulfilment or billing. 15. Environmental Issues: Today’s production managers are concerned more and more with pollution control and waste disposal which are key issues in protection of environment and social responsibility. There is increasing emphasis on reducing waste, recycling waste, using less-toxic chemicals and using biodegradable materials for packaging. 5S principles The original 5S principles were stated in Japanese. Because of their proven value, they have been translated and restated in English. The 5S is a mantra of sorts designed to help build a quality work environment, both physically and mentally. The 5S condition of a work area is critical to the morale of employees and the basis of customers’ first impressions. Management’s attitude regarding employees is reflected in the 5S condition of the work area. The 5S philosophy applies in any work area. The elements of 5S are: Sort—Eliminate whatever is not needed Straighten—Organize whatever remains Shine—Clean the work area Standardize—Schedule regular cleaning and maintenance Sustain—Make 5S a way of life How does 5S help? Eliminates waste that results from a poorly organized work area (e.g. wasting time looking for a tool). Kaizen (Continuous Improvement) A strategy where employees work together proactively to achieve regular, incremental improvements in the manufacturing process. How does Kaizen help? Combines the collective talents of a company to create an engine for continually eliminating waste from manufacturing processes. Kanban (Pull System) A method of regulating the flow of goods both within the factory and with outside suppliers and customers. Based on automatic replenishment through signal cards that indicate when more goods are needed. How does Kanban help? Eliminates waste from inventory and overproduction. Can eliminate the need for physical inventories (instead relying on signal cards to indicate when more goods need to be ordered). Poka-Yoke (Error Proofing) Design error detection and prevention into production processes with the goal of achieving zero defects. How does Poka-Yoke help? It is difficult (and expensive) to find all defects through inspection, and correcting defects typically gets significantly more expensive at each stage of production. Total Productive Maintenance (TPM) A holistic approach to maintenance that focuses on proactive and preventative maintenance to maximize the operational time of equipment. TPM blurs the distinction between maintenance and production by placing a strong emphasis on empowering operators to help maintain their equipment. How does Total Productive Maintenance help? Creates a shared responsibility for equipment that encourages greater involvement by plant floor workers. In the right environment this can be very effective in improving productivity (increasing up time, reducing cycle times, and eliminating defects). Lean Manufacturing Lean manufacturing or lean production, often simply "lean", is a systematic method for waste minimization ("Muda") within a manufacturing system without sacrificing productivity. Lean also takes into account waste created through overburden ("Muri") and waste created through unevenness in work loads ("Mura"). Working from the perspective of the client who consumes a product or service, "value" is any action or process that a customer would be willing to pay for. Lean manufacturing makes obvious what adds value, by reducing everything else (which is not adding value). This management philosophy is derived mostly from the Toyota Production System (TPS) and identified as "lean" only in the 1990s. TPS is renowned for its focus on reduction of the original Toyota seven wastes to improve overall customer value, but there are varying perspectives on how this is best achieved. The original seven mudas are: Transport (moving products that are not actually required to perform the processing) Inventory (all components, work in process, and finished product not being processed) Motion (people or equipment moving or walking more than is required to perform the processing) Waiting (waiting for the next production step, interruptions of production during shift change) Overproduction (production ahead of demand) Over Processing (resulting from poor tool or product design creating activity) Defects (the effort involved in inspecting for and fixing defects) Lean principles are derived from the Japanese manufacturing industry. The term was first coined by John Krafcik in his 1988 article, "Triumph of the Lean Production System", based on his master's thesis at the MIT Sloan School of Management. Lean Production Advantages Less infrastructure: A manufacturer
Details
-
File Typepdf
-
Upload Time-
-
Content LanguagesEnglish
-
Upload UserAnonymous/Not logged-in
-
File Pages41 Page
-
File Size-