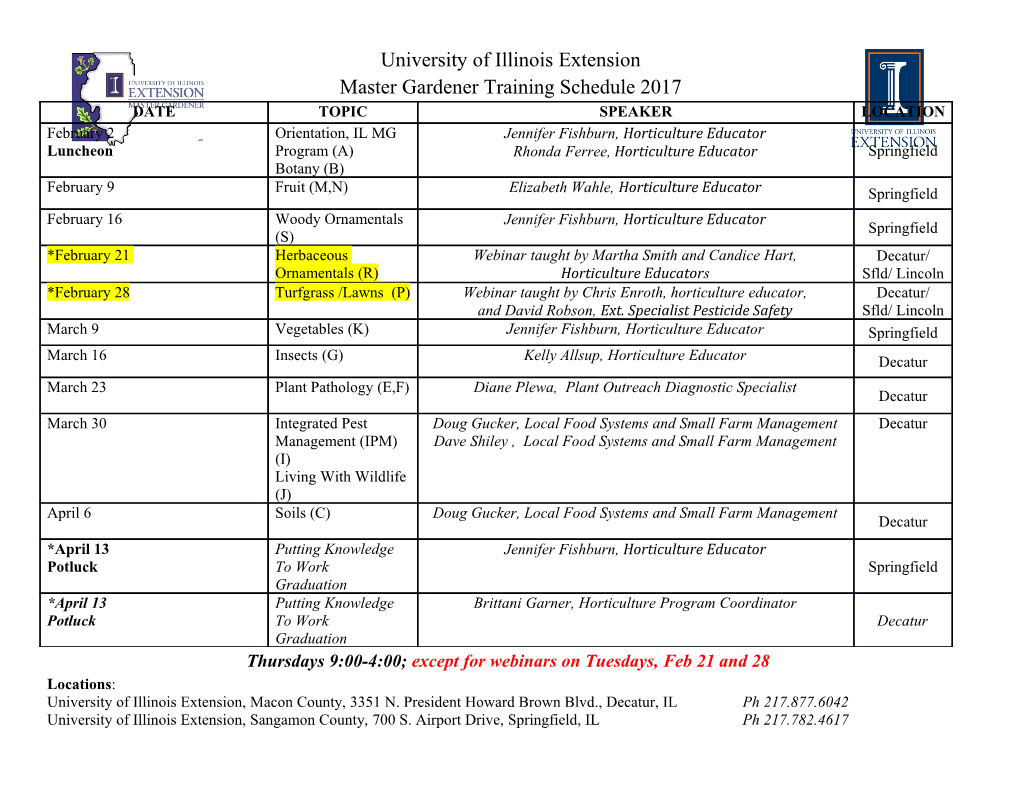
As appeared in October 2018 PBE Copyright CSC Publishing powderbulk.com SIX KEY CONSIDERATIONS FOR PROPER DUST COLLECTION SYSTEM DESIGN When it comes to industrial dust collection, it’s important to take a “system design” engineering approach versus the more common “component selection” method. This article will discuss six considerations when designing a dust collection system to help ensure a properly functioning system for your application. Eric Maynard Jenike & Johanson hough the concept for dust collection seems The dust collector operates by either inertial or phys- simple, many things can go wrong if you don’t ical barrier means, for example, a cloth “sock” or fabric Tpay careful attention to the details. There are four or sintered metal, to retain the particles while the air key components in a dust collection system: the filter, leaves the collector to travel to the air mover. The heart ductwork, pickup hoods, and the air mover. Many of the dust collection system is the air mover and filter suppliers provide excellent components that can do combination. The symbiotic relationship between these “their job,” but the key to a successful dust collection two components is important; for instance, if the filter system is to get the components to work well together becomes clogged with dust, the fan (air mover) per- in a cohesive unit. formance will likely be reduced and can cause major system problems. Dust collection basics In my experience, designing a proper dust collection Figure 1 shows an example of a typical dust collec- system can be broken down into six key considerations. tion system. Dust that’s generated at a point source is These six considerations are: pulled into pickup hoods, which is the start of the dust • Ensure sufficient conveying velocity collection system. Airflow through the hoods can be • Use balance-by-design for system balancing controlled by either blast gates (common) or by duct • Install the right air mover sizing (less common but more effective). The ductwork • Avoid plugging (also called branch and trunk lines – these are closer to • Choose an appropriate dust collector the dust collector) is routed through the facility, often • Consider combustible dust hazards changing directions multiple times and likely increas- ing in diameter along its length. The trunk (main line) Ensure sufficient conveying velocity of the duct terminates at the dust collector where the Sufficient conveying velocity is required to pick up the particles are separated from the airstream. dust from the pickup hoods and transport the material to the dust collector for separation from the air stream. This first consideration is fairly simple – if you can’t effectively FIGURE 1 convey the dust, then you won’t collect the dust. Illustration of components for a dust collection system Particles that are sticky, have high moisture content, are heavy or oddly shaped, or are very fine can present conveying difficulties in the dust collection system. Duct Air cleaning For example, wet saw dust, metal powder, fiberglass, device and toner generate dusts that are known for being Fan difficult to convey. Moving air (pneumatic conveying) is relatively inefficient at transporting bulk solids, as demonstrated by the drag force equation, which states Hood that the drag force on a particle is proportional to the coefficient of drag, particle area, the square of the gas’s velocity, and the density of the fluid. Based on the fact that air is more than 800 times less dense than water, it Dust source becomes obvious why using air to move solids instead of water is challenging. Copyright CSC Publishing Most bulk solids will require significant air velocity uations where dust toxicity or heavy production rates in the ductwork to convey the material in full suspen- may apply. For example, for wet sanding where heavy sion — usually an air velocity of about 4,000 fpm (67 particles are released from a high-speed grinding ft/s or about 45 mph). In some cases, it may not only be wheel, the higher capture velocity of 2,000 fpm within dust that is conveyed, as additional material like fumes the range shown in the table may be needed. Note that or vapors may be included in the material stream. As with high-momentum particles, you should try to ori- shown in Table 1 from the American Conference of ent the pickup hood to capture the particle trajectory, Governmental Industrial Hygienists (ACGIH), there thereby using the stream energy to introduce the dust are a wide range of minimum duct design velocities, into the conveying duct. which are strongly based on the material conditions1. Keep in mind that the maximum air velocity occurs Note that these recommendations are based on con- at the open face of the pickup point in the duct, and veying velocity and not cfm, which is a common mea- as you move away from the duct opening farther into surement among HVAC designers where only air is the duct, the velocity reduces drastically. For example, being transported and no consideration is made to the at the length of only one-half of a duct diameter away type of bulk solid being conveyed with the air. In some from the pickup point, the air velocity drops by 70 cases, velocities greater than 75 ft/s (4500 fpm or about percent. At a full duct diameter away, it drops to only 50 mph) are required to convey the dust-air mixture. In about 10 percent of the inlet velocity. This demonstrates addition to the air velocity in the ductwork, the capture the DallaValla equation2, whereby doubling the dis- velocity at the pickup hoods is an important consider- tance between the dust point source and the hood inlet ation. Again, ACGIH provides some helpful guidelines requires a flowrate increase of 400 percent to maintain for recommended capture velocities at pickup hoods, the necessary capture velocity. as shown in Table 2. ACGIH also provides helpful guidance on the type Note that a range of capture velocities is provided and design of pickup hoods recommended for a myriad for each condition depending upon type of dust (larger of applications. In most situations, a standard round or small, sticky or not-sticky, for example) and energy duct is not suitable for adequately capturing a standard (particles that include momentum when generated or dust emission, so understanding what pickup hoods are not) associated with the dust dispersion, as well as sit- available is essential to dust collection system design. TABLE 1 Range of minimum duct design velocities Nature of Contaminant Examples Design Velocity Vapors, gases, smoke All vapors, gases, and smoke Any desired velocity (economic optimum velocity usually 1000-2000 fpm) Fumes Welding 2000-2500 Very fine light dust Cotton lint, wood flour, litho powder 2500-3000 Dry dusts & powders Fine rubber dust, Bakelite molding powder dust, 3000-4000 jute lint, cotton dust, shavings (light), soap dust, leather shavings Average industrial dust Grinding dust, buffing lint (dry) wool jute dust 3500-4000 (shaker waste), coffee beans, shoe dust, granite dust, silica flour, general material handling, brick cutting, clay dust, foundry (general), limestone dust, packaging and weighing asbestos dust in textile industries Heavy dusts Sawdust (heavy and wet), metal turnings, foundry 4000-4500 tumbling barrels and shake-out, sand blast dust, wood blocks, hog waste, brass turnings, cast iron boring dust, lead dust Heavy or moist Lead dusts with small chips, moist cement dust, 4500 and up (≈ 75 ft/s or 23 m/s ) asbestos chunks from transite pipe cutting machines, buffing lint (sticky) quick-lime dust Copyright CSC Publishing TABLE 2 Range of capture velocities Condition of Dispersion of Example Capture Velocity, fpm Contamination Released with practically no Evaporation form tanks; degreasing, etc. 50-100 velocity into quiet air. Released at low velocity into Spray booths; intermittent container filling; low 100-200 moderately still air. speed conveyor transfers; welding; plating; pickling Active generation into zone Spray painting in shallow booths; barrel filling; 200-500 of rapid air motion. conveyor loading; crushers Released at high initial Grinding; abrasive blasting; tumbling 500-2000 velocity into zone at very rapid air motion. In each category above, a range of capture velocity is shown. The proper choice of values depends on several factors: Lower End of Range Upper End of Range 1. Room air currents minimal 1. Disturbing room air currents. or favorable to capture. 2. Contaminants of low 2. Contaminants of high toxicity. toxicity or of nuisance value only. 3. Intermittent, low 3. High production, heavy use. production. 4. Large hood-large air mass 4. Small hood-local control only. in motion. Implement balance by design static pressure loss calculations in ASHRAE, ACGIH, When balancing the airflow (and more importantly air and Crane’s technical paper #410. Keep in mind that velocity) in a dust collection system, there are two main these calculations are based principally on airflow approaches: the balance by design method and the losses only and don’t account for particle loss effects. blast gate method. In the balance by design method, In other words, if your dust collection system will have the duct size and layout is engineered to balance the a heavy particle load, using air-only calculations will airflow in the system’s branches, pickups, and trunk significantly undersize the fan, cause pressure losses, based on static pressure loss through each section. If and may result in system failure. each branch has a similar static pressure loss, then the After determining the static pressure loss per seg- airflow, and thus velocity, through each branch will be ment, then the duct diameter, elbows, etc., are adjusted equal. This method doesn’t use blast gates to manually to generate equal static pressure at junctions so that the adjust airflow at each branch, in contrast to the alterna- airflow is balanced.
Details
-
File Typepdf
-
Upload Time-
-
Content LanguagesEnglish
-
Upload UserAnonymous/Not logged-in
-
File Pages9 Page
-
File Size-