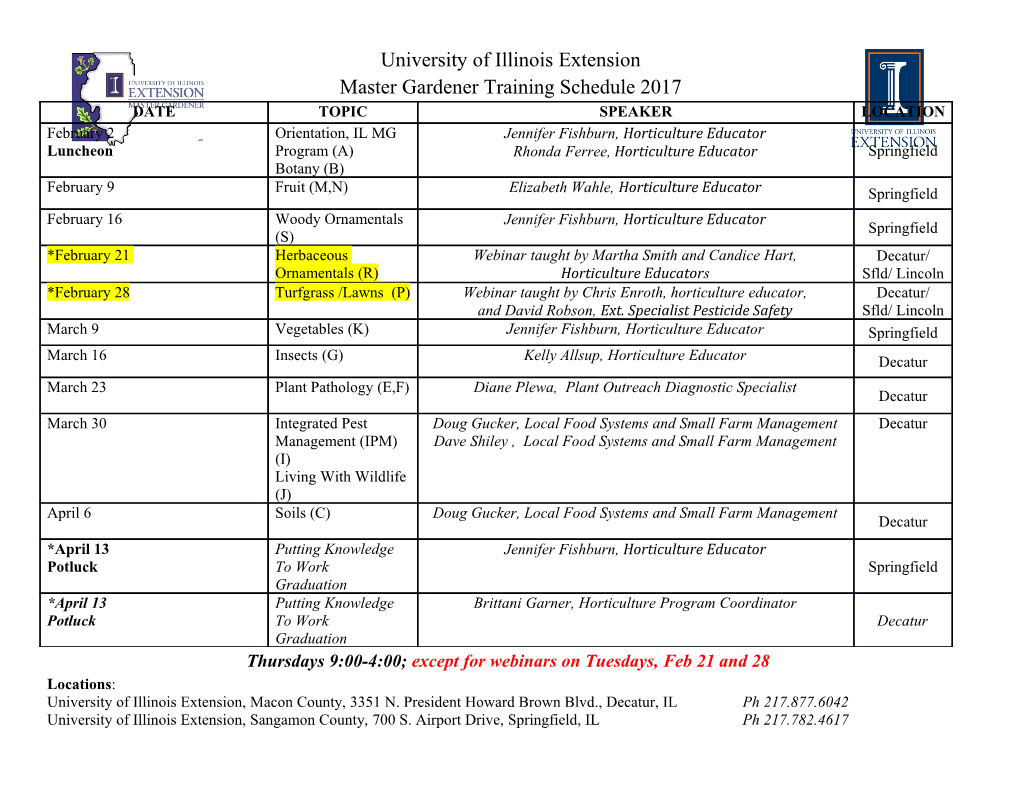
University of Tennessee, Knoxville TRACE: Tennessee Research and Creative Exchange Masters Theses Graduate School 12-2017 Monitoring the Metal Additive Manufacturing Process through Thermographic Data Analysis Jacob B. Raplee University of Tennessee, [email protected] Follow this and additional works at: https://trace.tennessee.edu/utk_gradthes Recommended Citation Raplee, Jacob B., "Monitoring the Metal Additive Manufacturing Process through Thermographic Data Analysis. " Master's Thesis, University of Tennessee, 2017. https://trace.tennessee.edu/utk_gradthes/4993 This Thesis is brought to you for free and open access by the Graduate School at TRACE: Tennessee Research and Creative Exchange. It has been accepted for inclusion in Masters Theses by an authorized administrator of TRACE: Tennessee Research and Creative Exchange. For more information, please contact [email protected]. To the Graduate Council: I am submitting herewith a thesis written by Jacob B. Raplee entitled "Monitoring the Metal Additive Manufacturing Process through Thermographic Data Analysis." I have examined the final electronic copy of this thesis for form and content and recommend that it be accepted in partial fulfillment of the equirr ements for the degree of Master of Science, with a major in Mechanical Engineering. Sudarsanam S. Babu, Major Professor We have read this thesis and recommend its acceptance: Ryan R. Dehoff, Chad E. Duty, William R. Hamel Accepted for the Council: Dixie L. Thompson Vice Provost and Dean of the Graduate School (Original signatures are on file with official studentecor r ds.) Monitoring the Metal Additive Manufacturing Process through Thermographic Data Analysis A Thesis Presented for the Master of Science Degree The University of Tennessee, Knoxville Jacob B. Raplee December 2017 Dedication This thesis is dedicated to my mother and father, Scott and Margee Raplee; siblings Joshua and Sarah and to my girlfriend Rachel whom all supported me through my graduate studies and research. ii Acknowledgements I would like to express my gratitude to all of the members of my thesis committee, Dr. Suresh Babu, Dr. Ryan Dehoff, Dr. Bill Hamel, and Dr. Chad Duty. I would especially like to thank my committee chairperson and advisor Dr. Babu, for all of his encouragement and support during my research. I would also like to thank Oak Ridge National Labs and everyone at the Manufacturing Demonstration Facility who offered support and guidance and for allowing me to use their facilities to complete this research. I would like to individually thank the following people: Dr. Alex Plotkowski, Dr. Ralph Dinwiddie, Dr. Mike Kirka, Dr. Fred List III, Dr. Alfred Okello, Dr. Vincent Paquit, Keith Carver, Larry Lowe, Scott Marlow, Michael Massey, Jared Bell, Josh Arnold, Naren Raghavan, Curtis Fredrick, and Sarah Foster for their friendship and helping to support this research. iii Abstract Metal Additive Manufacturing (AM) is the formation of a solid metal part through the layer-wise melting of metal powder, wire, or thin sheets using various heat sources or other bonding methods. This manufacturing method provides nearly limitless complexity with decreased waste, energy needs, and lead time. However, the process faces challenges in part consistency and validation especially for high precision fields such as aerospace and defense. Research has sought to implement robust process monitoring techniques to increase consistency and the reliability of the AM process and detect vital information about the part such as microstructural development, and porosity formation so that eventually the proper control systems can be created to control the desired outcome. The research performed in this thesis seeks to utilize one of the more promising monitoring techniques for the metal PBF processes (selective laser sintering and electron beam melting), infrared (IR) thermography. However, little research has been performed using the technology, and therefore few monitoring applications for AM have been developed. The methods and results in this research will show two potential applications for the use of IR thermography to monitor AM materials: microstructural monitoring and porosity detection. The research will also discuss an algorithmic method for calibrating IR signals for in-situ emissivity change of the material to obtain a more accurate temperature history of a part during the build and direction for future work that needs to be addressed to advance the technology further. iv Table of Contents Chapter One : Introduction..................................................................................................................... 1 Chapter Two : Literature Review and Background ....................................................................... 3 2.1 The powder bed fusion additive manufacturing process. .............................................................. 3 2.2 Principles of infrared (IR) thermography and emissivity .............................................................. 4 2.2.1 Infrared thermographic technology ............................................................................................... 4 2.2.2 Emissivity and its effects in the monitoring of AM processes.............................................. 6 2.3 Current state of in-situ process monitoring of powder bed fusion (PBF) processes ......... 7 2.3.1 In-situ process monitoring of selective laser sintering (SLS) .............................................. 7 2.3.2 Monitoring of the EBM process ..................................................................................................... 11 2.4 Overview of microstructural development within AM Inconel 718 and the effects on part performance. ......................................................................................................................................................... 13 2.4.1 Formation of columnar and equiaxed grains and in-situ control of microstructure13 2.4.2 Effects of grain structure on part performance ...................................................................... 15 2.5 Porosity formation and effects on strength and fatigue life of AM materials ..................... 18 2.6 Objectives of Current Research .............................................................................................................. 19 Chapter Three : Materials and Methods .......................................................................................... 21 3.1 Thermographic Camera Setup for In-Situ Process monitoring ................................................ 21 3.1.1 Camera Setup for the EBM Process on the ARCAM S12 ...................................................... 21 3.1.2 Camera Setup for the SLS Process on the Renishaw AM250 ............................................. 23 3.2 Build setup, parameters, and description for microstructure monitoring of the EBM process and porosity monitoring of SLS .................................................................................................... 25 3.2.1 Experimental Setup: microstructure monitoring ................................................................... 25 3.2.2 Experimental Setup: porosity monitoring ................................................................................ 27 3.3 Specimen preparation for microscopic analysis and electron backscatter diffraction (EBSD) ...................................................................................................................................................................... 27 v 3.4 Microscopic imaging, electron backscatter diffraction, and confocal microscopy ........... 30 3.4.1 Optical Microscopy Imaging ............................................................................................................ 30 3.4.2 Electron backscatter diffraction (EBSD) imaging .................................................................. 30 3.4.3 Surface topology measurement via confocal microscopy .................................................. 30 Chapter Four : Correcting In-Situ Temperature Measurements for Emittance Change in the EBM Process ....................................................................................................................................... 31 4.1 Calibrating the data to acquire the initial temperature curves ................................................ 32 4.2 Filtering the data to remove false positives due to signal noise .............................................. 32 4.3 Locating the powder to as-printed transition .................................................................................. 35 4.4 Methods for determining the occurrence of melting .................................................................... 37 4.4.1 Determining melting through calculation ................................................................................. 37 4.4.2 Setting the melt region using image registration. .................................................................. 39 4.5 Results .............................................................................................................................................................. 41 4.6 Limitations and Future Work ................................................................................................................. 44 Chapter Five : Microstructural Monitoring of EBM AM materials .......................................... 51 5.1 Data analysis for microstructural monitoring ................................................................................
Details
-
File Typepdf
-
Upload Time-
-
Content LanguagesEnglish
-
Upload UserAnonymous/Not logged-in
-
File Pages138 Page
-
File Size-