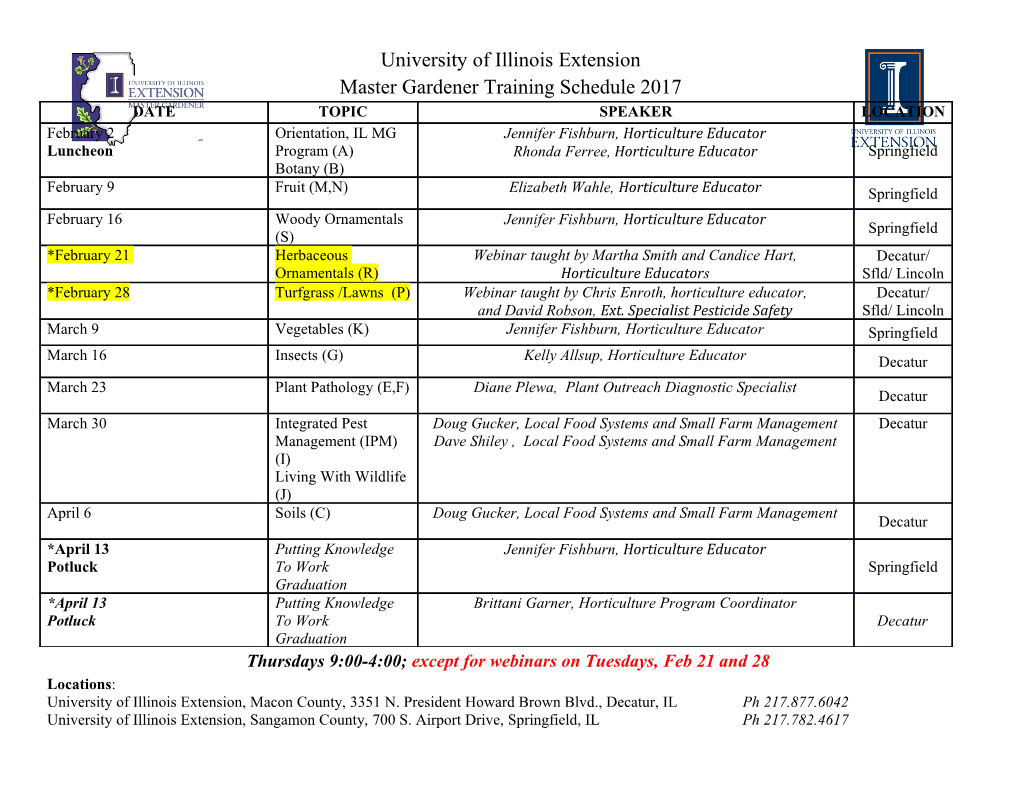
Copyright © 1991 ASM International® ASM Handbook, Volume 4: Heat Treating All rights reserved. ASM Handbook Committee, p 601-619 www.asminternational.org Defects and Distortion in Heat-Treated Parts Anil Kumar Sinha, Bohn Piston Division MOST OF THE PROBLEMS in heat- ature and effectiveness of the proprietary treated parts are attributed to faulty heat- grain inoculants applied to the mold surface), treatment practices (such as overheating and in heavily ground parts, and in affected zones burning, and nonuniform heating and quench- of welds (Ref 4). The usual practice is to ing), deficiency in the grade of steels used, reject the overheated products as being un- part defect, improper grinding, and/or poor suitable for service. part design. This article discusses overheat- It has now been established that over- ing and burning, residual stresses, quench heating is essentially a reversible process cracking, and distortion in some detail and caused by the solution of MnS particles in offers some suggestions to combat them. austenite during heating or reheating at high Most of these conditions result in a charac- temperatures; the amount increases with teristic appearance of the treated parts that temperature, and its subsequent reprecipi- can be easily recognized by simple inspec- tation during cooling occurs at intermediate tion. Some of these factors do not produce rates as very fine (-0.5 i~m) arrays of any distinguishing features in the semifin- a-MnS particles on the austenite grain ished or finished part. In particular, some of boundaries. On subsequent heat treatment the visual evidence does not recognize the the intergranular network of sulfides may presence of overheating and burning and the provide a preferential, lower-energy frac- 166,6 ~rn development of residual stresses leading to ture path in contrast to a normal transgran- distortion, quench cracking, and eventual ular fracture path. As a result, when impact failure of the heat-treated parts; metallurgical loaded, a ductile intergranular fracture de- laboratory examination is needed to establish velops due to decohesion of the MnS/matrix these problems that contribute significantly to interface and progress of microvoid coales- the service performance of the part. Tool cence. Figures 1 (a) and (b) show the usual designers must also be aware of the problems appearance of the fracture surface at differ- and difficulties in manufacture, heat treat- ent magnifications (Ref 1). ment, and use. When the low-alloy steel is preheated prior to hot working at too high a tempera- Overheatin 8 and Burning of ture (normally > 1400 °C, or 2550 °F), local melting occurs at the austenite grain bound- Low-Alloy Steels aries as a result of the segregation of phos- When low-alloy steels are preheated to phorus, sulfur, and carbon (Ref 5). During high temperature (usually > 1200 °C, or 2200 cooling, initially dendritic sulfides (proba- °F), prior to hot mechanical working (such as bly type II-MnS) form within the phospho- forging) for a long period, a deterioration in rus-rich austenite grain boundary, which the room-temperature mechanical properties then transforms to ferrite. This results in I I (particularly tensile ductility and impact excessively weak boundaries. Subsequent 12.5 p,rn strength or toughness) can be obtained after heat treatment provides a very poor impact Fracture surface of an impact loaded speci- the steel has been given a final heat treatment strength and almost completely intergranu- Fig 1 men. (a) Appearance of intergranular fracture (comprising reaustenitizing, quenching, and lar fracture surface after impact failure. of 4.25Ni-Cr-Mo steel containing 0.34% Mn and tempering) (Ref 1-3). Linked with the im- This phenomenon is termed burning. Burn- 0.008% S, in fully heat-treated condition but after paired mechanical properties is the appear- cooling from 1400 °C (2550 °F) at 10 °C/min (20 °F/rain). ing thus occurs at a higher temperature than (b) Same specimen as in (a) but at higher magnifica- ance of intergranular matte facets on the overheating. If this occurs during forging, tion, showing ductile dimples nucleated by MnS par- normal ductile fracture surface of an impact the forging will often break during cooling ticles precipitated at austenite grain boundaries. specimen. This phenomenon is known as or subsequent heat treatment (Ref 4). Courtesy of The Institute of Metals overheating and has been a matter of con- cern, especially in the case of steel forgings. Detection of Overheating heating, namely, fracture testing and metal- Overheating has also been noticed in steel There are two basic methods for the lography (or etch testing). Overheating may castings (due to variation in pouring temper- determination of the occurrence of over- also be detected by a decrease in mechani- 602 / Process and Quality Control Considerations Table 1 Etching characteristics of overheated and burned steels Reagent Method Action on overheated steel Action on burned steel 2.5% nitric acid in ethyl Swab surface for 30 s May produce grain contrast, but White boundaries outlining alcohol not indicative of overheating preexisting austenite grains Saturated aqueous solution Electrolytic, specimen anode, White boundaries outlining Black boundaries outlining of ammonium nitrate current density 1.0 A cm -2 preexisting grains preexisting austenite grains (6.5 A in. -2) Aqueous 10% nitric acid + Etch for 30 s, swab surface; Black boundaries outlining White boundaries outlining 10% sulfuric acid repeat three times, then preexisting austenite grains preexisting austenite grains repolish lightly 85% orthophosphoric acid Electrolytic, specimen anode, Does not differentiate between Attacks inclusions at grain (Fine's reagent) current density 0.15 A cm -2 overheated and nonoverheated boundaries (1.0 A in.-2), etching time 15 steel min Oberhoffer's reagent Swab surface for 30 s Does not differentiate between Shows phosphorus segregation at overheated and nonoverheated grain boundaries steel Source: Ref 13 cal properties. But such changes are not ed with a lowering of impact strength (Ref acid and ammonium nitrate solution) used very marked unless overheating tempera- 12). for overheating can be successfully em- ture is high or overheating is too prolonged Metallography (or Etch Testing). The most ployed for detecting burning. When applied or severe; in some instances the mechanical widely used etchant technique uses to burned steels, these etchants react in a properties do not change, even after the Austin's reagent (aqueous solution of 10% manner opposite to that of overheated observation of extensive faceting. Usually nitric and 10% sulfuric acids), ammonium steels. Preece and Nutting (Ref 13) found the two methods mentioned above should persulfate, molten zinc chloride, saturated ammonium nitrate solution to be the ideal be used in conjunction with some measure solution of picric acid at 60 °C (140 °F), and reagent to detect this phenomenon. Other of toughness by impact or other testing in an electrolytic etch based on saturated reagents are Stead's and Oberhoffer's re- order to get a clear understanding of the aqueous ammonium nitrate. Table 1 shows agents, which may also be used to check the degree and severity of overheating (Ref 2). the etching characteristics of overheated burning effect. However, these etchants are Fracture Testing. The direction of fracture and burned steels (Ref 13). The etchant unable to differentiate between overheated testing is important in steels manufactured procedure with Austin's etchant is as fol- and nonoverheated steels. by conventional methods. It has been ob- lows: The sectioned specimen is etched for served by some workers (Ref 6) that the 30 s in the etchant, removed, washed off, Factors Affecting Overheating longitudinal fracture test specimens parallel and repeated three times. If the steel has The occurrence and severity of overheat- to the rolling direction do not exhibit face- been overheated, the original austenite ing depend principally on important factors, ring until the corresponding transverse frac- grain boundaries will be preferentially at- notably steel composition, temperature, tures display extensive faceting. However, tacked, and a black network of etch pits will cooling rate, and method of manufacture. the testing direction in electroslag-refined be observed under the microscope (Ref 14). Composition. Sulfur is the constituent (ESR) steels has been found to be insignif- According to Preece and Nutting (Ref 13), that greatly influences overheating. For icant (Ref 7). the best results are obtained when ammoni- steels with less than 0.002 wt% sulfur, over- The scanning electron microscope is con- um nitrate etch is applied on the sectioned heating does not occur; this is because of sidered to be the best and most convenient steel specimen in the fully heat-treated con- the very low volume fraction of sulfides tool to detect the facets on the overheated dition where this etchant preferentially at- formed. However, the commercial produc- fracture surfaces. These facets are charac- tacks the matrix (original austenite grains), tion of such very-low-sulfur steels (for ex- terized by small, well-defined, ductile dim- leaving the grain boundary unaffected ample, ESR steels) is expensive. Above this ples; each dimple is usually nucleated, pre- (which appears as a white network). level of sulfur, the overheating onset tem- sumably by fine arrays of inclusion Bodimeade (Ref 15) concluded that all these perature rises with the increasing
Details
-
File Typepdf
-
Upload Time-
-
Content LanguagesEnglish
-
Upload UserAnonymous/Not logged-in
-
File Pages19 Page
-
File Size-