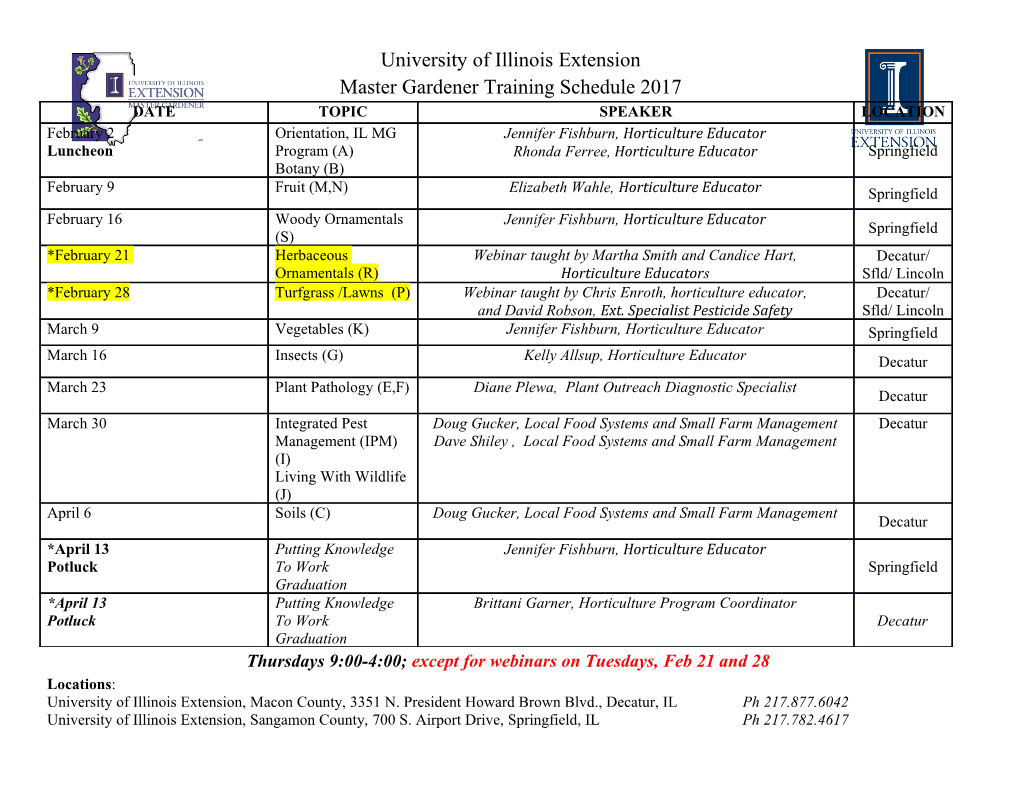
Appl. Phys. A 85, 11–14 (2006) Applied Physics A DOI: 10.1007/s00339-006-3672-3 Materials Science & Processing y. cheng1 Fabrication of 3D microoptical lenses h.l. tsai1,u k. sugioka2 in photosensitive glass k. midorikawa2 using femtosecond laser micromachining 1 Laser-Based Manufacturing Laboratory, Department of Mechanical & Aerospace Engineering, University of Missouri-Rolla, 1870 Miner Circle, Rolla, MO 65409, USA 2 Laser Technology Laboratory, RIKEN – The Institute of Physical and Chemical Research, Hirosawa 2-1, Wako, Saitama 351-0198, Japan Rapid communication Received: 9 May 2006/Accepted: 20 July 2006 can be patterned using UV lithography Published online: 10 August 2006 • © Springer-Verlag 2006 (290–330 nm). In this case, the cerium (Ce3+) ion play the important role of ABSTRACT We describe the fabrication of microoptical cylindrical and hemispheri- photosensitizer, which releases an elec- cal lenses vertically embedded in a photosensitive Foturan glass by femtosecond (fs) + tron to become Ce4 by exposure to laser three-dimensional (3D) micromachining. The process is mainly composed of four steps: (1) fs laser scanning in the photosensitive glass to form curved surfaces UV light irradiation. Some silver ions (spherical and/or cylindrical); (2) postannealing of the sample for modification of the then capture the free electrons to form exposed areas; (3) chemical etching of the sample for selective removal of the modi- silver atoms. In a subsequent heat treat- fied areas; and (4) a second postannealing for smoothening the surfaces of the tiny ment, the silver atoms first diffuse and lenses. We examine the focusing ability of the microoptical lenses using a He-Ne laser agglomerate to form clusters at a tem- ◦ beam, showing the great potential of using these microoptical lenses in lab-on-a-chip perature of around 500 C; and then the applications. crystalline phase of lithium metasili- cate grows around the silver clusters as PACS 42.62.-b; 81.05.Kf; 82.50.Pt the nucleus in the amorphous glass ma- trix at a temperature of around 600 ◦C. Since this crystalline phase of lithium 1 Introduction cal waveguides [3], microoptical grat- metasilicate has an etching rate in a di- ings [4], optical fibers [5], microoptical lute solution of hydrofluoric (HF) acid The concept of lab-on-a-chip mirrors [6], and microoptical cylindrical which is much higher than the glass ma- has created a revolution in chemical, lenses [7], have been used in the con- trix, it can be preferentially etched away, biological, and medical sciences [1]. struction of fluidic photonic integrated leaving behind the engraved pattern on A lab-on-a-chip device, which is a palm- devices. In this work, we demonstrate the glass surface. sized chip integrated with functional for the first time to our best knowledge, However, the microstructuring of components such as microfluidics, mi- the fabrication of three-dimensional Foturan glass by UV lithography is crooptics, microelectronics, and mi- (3D) microoptical cylindrical and hemi- limited to the sample surface because cromechanics, offers several advantages spherical lenses vertically embedded in of the resonant absorption of UV light over the traditional chemical and bio- glass using a home-integrated femtosec- starting at the sample surface. To over- logical analysis techniques [2]. Because ond (fs) laser micromachining system. come this issue, lasers working at non- of its tiny dimensions, the lab-on-a-chip We will also show that these microop- resonant wavelengths, including nano- allows for performing of chemical and tical lenses can focus laser beams into second (ns) lasers at 355 nm [9] and biological analysis with ease of use, low small light spots, holding promise for fs lasers at 400 nm and 755 nm [8, 10, sample and reagent consumption, low practical applications in life sciences. 11], were employed to fabricate 3D mi- waste production, high speed of analy- We briefly introduce here the mech- crostructures buried in Foturan glass sis, and high reproducibility due to stan- anism of fs laser micromachining of without damage to the surface. Since dardization and automation. Recently, Foturan glass, because the details can these wavelengths are outside of the significant progress has been made in be found elsewhere [8–10]. The pho- absorption band of Foturan glass, photo- the incorporation of optical circuits into tosensitive glass Foturan is composed modification of glass can only be ini- the fluidic circuits, which would even- of lithium aluminosilicate glass and tiated near the focal point where the tually enable enhanced functionality doped with a trace amount of silver extremely high laser intensity induces of the lab-on-a-chip devices. A variety and cerium. Traditionally, microstruc- nonlinear optical effects like multipho- of optical structures, including opti- tures on the surface of Foturan glass ton absorption. It has been found that the photochemistry of fs laser modification u Fax: +1-573-341-4607, E-mail: [email protected] of Foturan glass is different from the 12 Applied Physics A – Materials Science & Processing established theory for UV light process- in the vertical direction, a 20× objec- tific). After this step, we etched the sam- ing, because photo-reduction of silver tive lens with NA = 0.45 was used in ple in a solution of 10% HF acid diluted with fs laser irradiation is possible even the processing. The vertical space be- in water in an ultrasonic bath for one without Ce3+ ions [12, 13]. Deeper in- tween each of the two adjacent parallel hour to remove modified areas. Lastly, vestigation is still required for building rings in the glass was reduced to 7.5 µm. we baked the etched sample again at a thorough physical understanding for fs The laser pulse energy before the ob- 560 ◦C for 5h for further smoothening laser modifications of Foturan glass. jective lens was measured as 400 nJ.In of the surfaces of the microlenses. This both of these two experiments, the scan- annealing temperature is slightly lower ◦ 2 Experimental ning speed of the rotary stage was fixed than the one (570 C) used in our previ- at 360◦/min. Lastly, to break the cylin- ous work [14], because the actual tem- The experiments were car- drical and the spherical structures into perature in different furnaces may not be ried out at a home-integrated fs laser two equal parts, we scanned the focused the same even at a same setting point. In 3D micromachining system. The repe- fs laser to form a vertical plane through the discussion (Sect. 4) of this paper, we tition rate, center wavelength and pulse the center of the rings which would will give a general principle to optimize width of the fs laser (Legend-F, Coher- eventually result in two equal parts the annealing temperature for different ent) were 1kHz, 800 nm and 120 fs,re- after the following annealing and sub- furnaces. spectively. The maximum output power sequent chemical etching of the glass of the fs laser was approximately 1W; coupon. 3Results however, we used a combination of After the laser scanning process, we a half-waveplate and a polarizer to first baked the exposed sample at 500 ◦C for First, we fabricated microop- reduce the laser power to 20 mW,and 1handthenat605 ◦C for another 1hin tical cylindrical lenses with a radius of then used several neutral density (ND) a programmable furnace (Fisher Scien- 1mm, as shown in Fig. 1. For compar- filters to further reduce the laser power to desirable values based on different experimental conditions. The attenu- ated laser beam was directed into ob- jective lenses (Olympus UMPLFL10×, and 20×) with different numerical aper- tures (NA) and finally focused into the glass samples. For fabrication of 3D microstructures, Foturan glass samples were translated by a five-axis motion stage (Aerotech) with a resolution of 1 µm. The Foturan glass sheets of 2mm thickness were bought from Mikroglas Chemtech. Before being used in the ex- periments, the glass sheet was cut into small coupons by a diamond cutter. In the first step of our experiment, we scanned the tightly focused fs laser beam inside the samples to form curved surfaces embedded in Foturan glass. To fabricate the microoptical cylindrical lens, we scanned a pile of parallel ring structures with the same radius from the top to the bottom of the glass. In this case, a 10× objective lens with NA = 0.3 was used in the processing. The vertical space between each of the two adjacent parallel rings in the glass was 15 µm. The laser pulse energy be- fore the objective lens was measured as 800 nJ, which was slightly below the ab- lation threshold as we observed in the experiment. To fabricate the microopti- cal hemispherical lens, we changed the radius of each ring structure at a dif- ferent depth to form a spherical surface inside the glass. In this case, in order FIGURE 1 SEM images of microoptical cylindrical lenses fabricated by fs laser 3D micromachining. to obtain a high fabrication resolution (a) Without a final smoothening step; (b) With a final smoothening step CHENG et al. Fabrication of 3D microoptical lenses in photosensitive glass using femtosecond laser micromachining 13 FIGURE 2 CCD camera images of (a) He-Ne laser beam; and (b)He-Ne laser beam focused by a microoptical cylindrical lens ison, we show scanning electron mi- Fig. 2b is the CCD camera image of ent materials are desirable [7]. Because croscopic (SEM) images of both the the He-Ne laser beam passing through our technique allows for fabrication of microcylindrical lenses with and with- both the microoptical cylindrical lens the 3D microoptical components as well out the final annealing step at 560 ◦C. and the 10× objective lens. Clearly, the as the 3D microfluidic structures in one It is clear in Fig.
Details
-
File Typepdf
-
Upload Time-
-
Content LanguagesEnglish
-
Upload UserAnonymous/Not logged-in
-
File Pages4 Page
-
File Size-