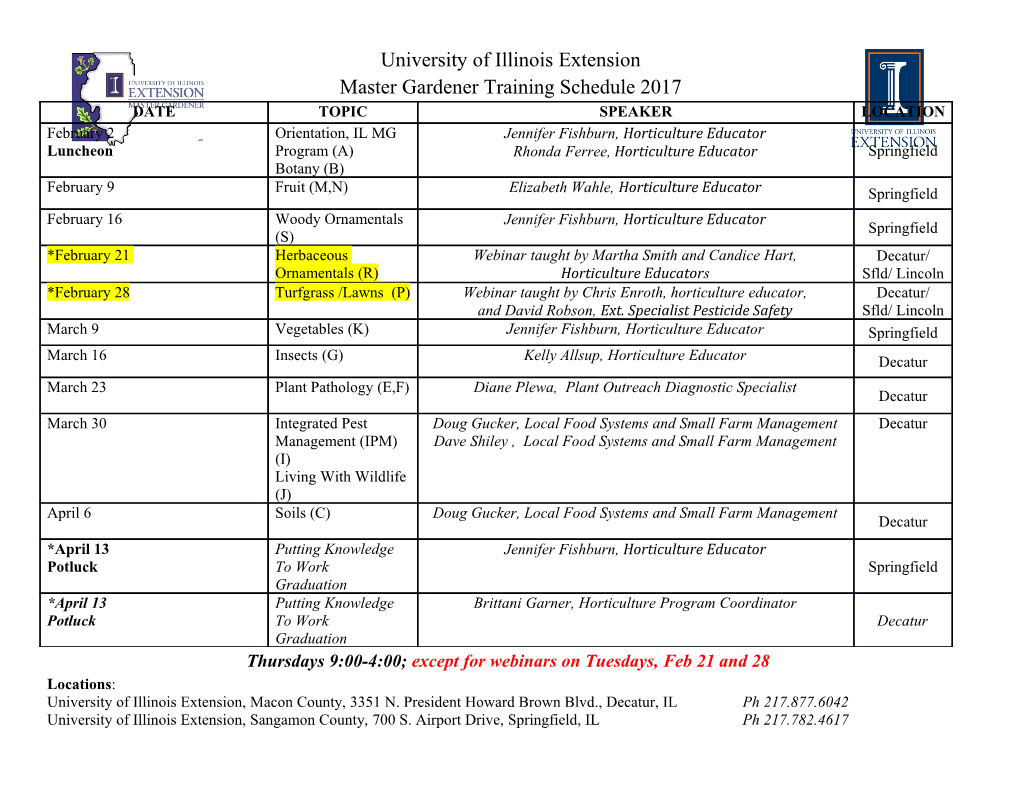
A LEVEL 3 FITNESS FOR SERVICE ASSESSMENT OF SHELL PLATE DEFORMATION IN A STORAGE TANK Arash Zamani , Yong Wang Saunders International Limited November 2016 Introduction • Storage tanks are one of the most massive steel structures used in industries. Varying from <10m to >100m in diameter and up to 30m in height. • Widely used in petrochemical and power plants, oil refineries and water facilities for decades. • Store liquids for different purposes such as transportation, storage, process and etc. Background • Steel storage tanks are composed of a flat floor, a cylindrical shell and either fixed or floating roof. • Shell thickness reduces as tank height increases. • Construction material: carbon steel, stainless steel and aluminium. Typical tank configuration (Cone roof / Floating roof) Shell Buckling • As thin wall structures, storage tanks are very sensitive to buckling due to small thickness to radius ratio. • Causes of shell buckling: Vacuum and wind pressure External forces Uneven settlement Inappropriate welding process • Shell buckling could result in tank collapse. Maintenance and Repair • Tanks shell should be inspected regularly for possible buckling, damages and deformation. • Deformed area should be repaired or replaced by new plates. • Repair can be done by adding stiffeners to the tank shell and reshape the damaged area. • Replace can be done by accessing the damaged area, supporting the shell, cut and replace the damaged plates. • Tanks need to be out of service during repair. • Profit loss and repair costs are expected. Can Equipment Operate Without Repair? Fitness For Service (FFS) • Fitness for service assessment (FFS) is an engineering method to evaluate equipment condition. • FFS assessments are quantitative engineering evaluations, which are performed to demonstrate the structural integrity of an in- service component containing a flaw or damage. • Such an engineering assessment should be able to evaluate the equipment circumstances and recommend whether remedial work is needed. • Using an appropriate FFS approach can save time and money. • API 579: provides rules and procedures for FFS assessment. • API 579: discusses assessment procedure for different damage scenarios. • API 579: appoints guidelines to determine whether tank shell deformation is acceptable and if the tank is safe to continue API 579 Fitness-For-Service operation without any repair for a certain period of time. FFS Levels Of Assessments • API 579 prescribes three levels of structural integrity evaluations for equipment. Level 1 Assessment • Level 1 assessment is the most conservative and simplified criterion that generally includes the use of charts and tables. Fitness for Service Level 2 Assessment • Level 2 assessment involves detailed calculations Assessment using relatively simple formulas with some (API 579) assumptions. • Level 3 assessment requires a comprehensive Level 3 Assessment analysis where advanced computational procedures such as nonlinear FEA are engaged. Problem Definition • Tank under study is a 45.72 x 16.9 m Cone roof. • Tank was built in late 1960s. • Tank was under periodic repair schedule. • After replacing a strake plate a deformation appeared between 6th and 7th strake. • Pre existing deformation as well as thermal stresses imposed by welding suspected to be the reason for shell deformation. • Shell deformation was assessed to check whether the tank is Fit For Service. Deformation Contour • The first step in the FFS assessment is to determine the pattern and amount of shell deformation. • Some methods to measure deformation: - String and weight - Surveying and use of mathematical calculation - Laser reference and manual measurement - Laser scanning • A 200mm by 200mm grid was marked on shell. • The grid covers 2.8m in height and 1.8m in width. Deformation Contour • According to API 579, a numerical interpolation is needed for extra node generation. • The interpolation is required to obtain a smooth shell curvature by producing interpolated nodes between measured points. • API 579 recommends using piece wise cubic spline curve fitting method. • A cubic spline curve fit was applied in both vertical and circumferential directions. Site measured pattern Interpolated pattern • In total 1716 nodes were generated and imported to FEA package. Cubic Spline Curve Fitting FEA Modelling • Strand7 package was used for FEA. • The tank shell was modelled by four nodes plate element. • Beam element represents curb angle. • Shell deformed area modelled by importing nodes to FEA. • Boundary condition. • API 579 analysis approaches: Elastic Analysis, Elastic Plastic Analysis • Elastic Plastic FEA analysis was used in this assessment. • Nonlinearity in geometry & nonlinearity in material. Portion of shell with deformation Boundary conditions Stress – Strain Relationship • API 579 suggests below models for stress-strain curve: MPC Model. Ramberg Osgood Model. • AS3678 Gr 250 plate: Module of elasticity: 200GPa Yield stress: 250MPa Tensile strength: 410MPa MPC Model Coefficients: API 579 Annex F Load Cases • Tank understudy is subject to dead load, hydrostatic pressure, internal pressure and wind force. • API 579 Global loading cases: (for API 650 storage tanks) • API 579 Local loading cases: (for API 650 storage tanks) FFS Assessment Elastic Method Protection Against Plastic Limit Load Method • API 579 level 3 FFS assessment requires below failure collapse scenarios to be evaluated for the defective tank. Elastic Plastic Method • Protection Against Plastic Collapse (PAPC). Elastic Method Level 3 FFS • Protection Against Local Failure (PALF). Protection Against Assessment Local Failure • Protection Against Collapse From Buckling (PACB). Elastic Plastic Method Protection Against Collapse From Buckling Protection Against Plastic Collapse (PAPC) • PAPC criterion studies the overall instability of the structure subject to Global loading cases. • PAPC defines plastic collapse load as the load that causes overall structural instability. • This load can be determined as the point that any further increment in the load will result in divergence in the analysis and inability to achieve equilibrium. • In practise, PAPC will be satisfied if FEA converges under all relevant Global loading combinations. Loading Case: Operation 2.25(P+Pso+D) PAPC: FEA • Tank shell model has been analysed subject to Global load combination cases. • Using nonlinear elastic plastic solver. Loading Case: Test 2.1375(Pst+D)+2.475Wt FEA convergence under all Global loading case: PAPC Satisfaction Protection Against Local Failure: (PALF) • In addition to PAPC, tank integrity should be investigated for another criterion called protection against local failure (PALF). • According to its definition, PALF discusses the possibility of local failure due to the emergence of an imperfection in the structure. • This criterion needs to be checked against Local loading cases. • Using the elastic-plastic method, PALF will be satisfied if Equivalent Plastic Strain in a location of the component under investigation, plus any Forming Strain due to initial forming is less than allowable strain, called Limiting Triaxial Strain. PALF: FEA • Loading case: (operation) 1.53(P+Pso+D) • Using nonlinear elastic plastic solver. • Principal stresses σ1=307.48MPa σ2= 107.39MPa Maximum principal stress σ Maximum equivalent plastic strain 2 Maximum principal stress σ1 • Equivalent plastic strain εpeq= 0.00141 PALF: Code Check Protection Against Collapse From Buckling (PACB) • Apart from PAPC and PALF, another API 579 criterion called “protection against collapse from buckling‟ should also be considered in FFS assessment. • This requirement checks the structural instability of a component with a compressive stress field under applied load cases. • For tank understudy, this part of FFS assessment will become important if tank is subject to high wind forces or vacuum. • According to API 579, for those analysis where PAPC is performed and imperfections are explicitly modeled in the FEA, the buckling factors are considered in the relevant loading combinations. • Convergence in PAPC analysis will then show that the tank is protected against buckling collapse as well. • Other loading cases producing compressive stress should be checked. Conclusions • A tank with a local shell deformation has been studied for level 3 FFS assessment according to API 579. • PAPC, PALF and PACB satisfied. • Resultantly, the tank under consideration met all FFS requirements and is able to undergo its service again. Tank is ‘‘Fit For Service’’! • FFS helps to predict whether a tank with such an imperfection is able to operate safely until the next repair interval by using similar assessment and predicting the shell thickness at the end of interval. • Loading combinations must be carefully considered in each individual assessment in accordance with the actual condition of the equipment. Thanks For Your Attention Questions?.
Details
-
File Typepdf
-
Upload Time-
-
Content LanguagesEnglish
-
Upload UserAnonymous/Not logged-in
-
File Pages22 Page
-
File Size-