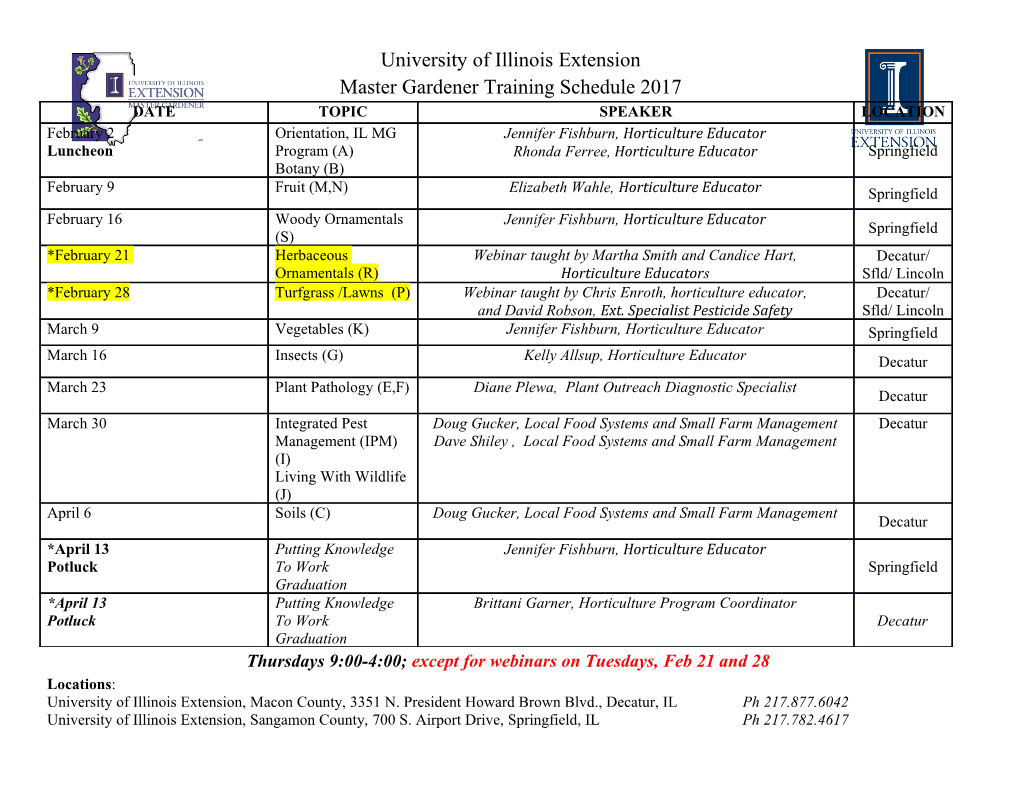
DefectDefect StructureStructure && MechanicalMechanical BehaviourBehaviour ofof NanomaterialsNanomaterials Defect structure in nanomaterials The defect structure in nanomaterials can be altered with respect to their bulk counterparts. This in turn can lead to profound differences in the mechanical behavior of nanomaterials as compared to bulk materials. Vacancies Vacancies are equilibrium thermodynamic defects and at a temperature T (in K) there exists an equilibrium concentration of vacancies (nv) in bulk crystals. nV the number of vacancies, H nV f . N number of sites in the lattice (for nV/N << 1) exp NkT. Interaction between vacancies can be ignored (Hformation (n vacancies) = n . Hformation (1 vacancy) . Hf enthalpy of formation of 1 mole of vacancies T (ºC) n/N 500 1 x 1010 1000 1 x 105 1500 5 x 104 2000 3 x 103 18 Hf = 1 eV/vacancy = 0.16 x 10 J/vacancy Close to the melting point in FCC metals Au, Ag, Cu the fraction of vacancies is about 104 (i.e. one in 10,000 lattice sites are vacant) Vacancies in nanocrystals . In free-standing nanocrystals of below a critical size, the benefit in configurational entropy does not offset the energy cost of introduce a vacancy. This implies that below the a critical size (dc), vacancies are not thermodynamically stable. Hence, below dc the crystal becomes free of vacancies (assuming that the kinetics permits so!). This size (dc) is given by [1]: 1/3 3exp(QKT / ) dc 2 4 nv . Where, nv is the number of atoms per unit volume and Q is the energy for the formation of a vacancy. For . Al at 900 K (with Q = 0.66 eV), dc is 6 nm (i.e. Al crystals below 6 nm in size will be free of vacancies- in equilibrium). Cu with a higher energy for the formation of a vacancy (of 1.29 eV), has a d of 86 nm at c 900 K. It is to be noted that bulk statistical thermodynamics, which is based on the assumption of large ensembles, is (strictly speaking) not applicable to small systems like nanocrystals. However, it is seen that the results of statistical thermodynamics can be applied to particles ~100 nm in size with only little errors. [1] J. Narayan, J. Appl. Phys., 100 (2006) 034309. MechanicalMechanical BehaviourBehaviour ofof MaterialsMaterials OverviewOverview && NanomaterialsNanomaterials Density and Elastic properties Plasticity by slip Motion of dislocations & dislocations in finite crystals Strengthening mechanisms Grain boundaries in nanocrystals Twinning versus slip Grain size and strength Superplasticity Nanocomposites Creep Testing of Nanostructures and Nanomaterials Mechanisms / Methods by which a can Material can FAIL Elastic deformation Creep Chemical / Physical Fatigue Electro-chemical degradation Fracture degradation Slip Microstructural changes Wear Twinning Erosion Phase transformations Grain growth Particle coarsening Failure can be considered as change in desired performance- which could involve changes in properties and/or shape Density and Elastic properties Often obtaining full density in a nanostructured bulk material is a challenge. Residual porosity* can affect the density- which is an artifact of specimen preparation. The coordination number and packing close to grain boundaries (& triple lines (TL), quadruple junctions (QJ)/corner junctions) is expected to be lower than that in the bulk of a single crystal/grain (SC/G). This implies that on decreasing grain size the density of the sample will decrease (albeit marginally). However, this effect (reduction in density with grain size) is expected to become noticeable when grain size is reduced to the nanoscale regime. As a first approximation we can assume that grain boundaries (& triple lines etc.) have a similar character (w.r.t to density) in a nanostructured material, as compared to a micron grain sized material. Typical value of t (= dGB) is taken to be about 1nm (for metals about 3 layers of atoms) *Often 3-5% porosity is considered to be fully dense The fraction of GB (& TL, QJ) depends on the grain morphology. For simplicity we assume cubic grain morphology to make calculations here. (in cubic grains TL are better referred to as TJ). The fraction of TL and QJ become important (for t ~ 1nm) when grain size is ~ 10nm (for the cubic morphology assumed) 1 d 3 d 3 f f 1 0.8 G 3 GB 3 f Grain ()dt ()dt t = 1nm 0.6 f GB f TL 3 2 6t 6td f QJ f 0.4 QJ 3 fTL 3 8(dt ) 4(dt ) Volume fraction 0.2 0 0 1020304050 Grain Size (nm) Effect of these defects on the density of the material (ignoring porosity) 1 y 0.98 Relative Density = polycrystal 0.96 Effects dominate G 0.94 below ~20 nm grain Relative Densit Relative 0.92 size Entity Relative density 0.9 GB 0.95 0 1020304050 Grain Size (nm) TL 0.90 QJ 0.81 Assumed relative density [(1 fffGB TL QJ). G ] [ f GB GB f TL TL f QJ QJ ] ()ffGGBTLQJ f f 1 Elastic properties For now we assume an isotropic material (i.e. properties do not change with position or direction). Note that we have already seen that density varies with position. An isotropic material can be described by two independent elastic moduli (e.g. E and ). Often ‘Modulus’ of some nanostructures are reported as below (it should be noted that Moduli are bulk macroscopic properties and their definition is extended to be applicable to these structures). Young’s Modulus Entity (GPa) Entity Young’s Modulus (GPa) Steel ~200 SW-CNT 1002 (Yu et al. 2000) Diamond ~1050 MW-CNT 11-63* (Yu et al. 2000) W ~400 ZnO nanowires 140-200 (Chen et al. 2006) Al ~70 Silica Nanowires 20-100 (Silva et al 2006) *Range of values is due to diameter differences or number of walls Moduli of composites and nanomaterials The modulus of a composite lies between that of the two components. The upper bound and lower bound are given by isostrain and isostress conditions respectively. EEVEV Under iso-strain conditions [m = f = c] c f f m m. I.e. ~ resistances in series configuration Voigt averaging . Under iso-stress conditions [m = f = c] 1 V f Vm . I.e. ~ resistances in parallel configuration E E E c f m . Usually not found in practice Reuss averaging in Ef tra sos → I s es c r st For a given fiber fraction f, the modulii of E Iso various conceivable composites lie between an E upper bound given by isostrain condition m and a lower bound given by isostress condition f A B Volume fraction → Nanocomposite of MW-CNT and alumina: Young’s modulus as high as 570 GPa (actually in the range of 200-570 GPa depending on the nanotube geometry and quality and the porosity in alumina). Yalumina ~ 350 GPa Nanocomposite of MW-CNT and alumina Modulus of nano-polycrystal There is noticeable change in the modulus only when the grain size is below about 20 nm (assuming cube morphology of grains as before and assuming the modulus of the GB is 0.7 that of the Grain). Presence of porosity can further cause a reduction in the modulus (which is a function of the processing route). Early results showed that there is reduction in modulus below even 200nm. These are perhaps because of porosity in the samples and not a characteristic of a fully dense sample. 1 0.9 E Upper bound polycrystal Lower bound Relative Modulus = 0.8 Effects EG dominate below Relative Modulus Relative Cube morphology 0.7 ~20 nm grain size Assuming EGB = 0.7E G 0.6 0 1020304050 Grain Size (nm) Supermodulus effect In early observations of elastic properties it was noticed that there is large (>100%) enhancement of the elastic moduli in multilayers. This phenomenon was termed the supermodulus effect. More work in this area have attributed this effect to artifacts or anomalies (it seems now that only about 10% enhancement in the elastic moduli may be real). Further work is needed in this area. Though plasticity by slip is the most important mechanism of plastic deformation, there are other mechanisms as well: Plastic Deformation in Crystalline Materials Slip Twinning Phase Transformation Creep Mechanisms (Dislocation motion) Grain boundary sliding Vacancy diffusion + Other Mechanisms Dislocation climb Note: Plastic deformation in amorphous materials occur by other mechanisms including flow (~viscous fluid) and shear banding Plasticity by slip The primary mode of plastic (permanent) deformation is by slip. The simplest test performed to assess the mechanical behaviour of a material is the uniaxial tension test. Variables in plastic deformation , , , T Usually expressed as (for plastic) n K → strength coefficient Low T K n → strain / work hardening coefficient ,T ◘ Cu and brass (n ~ 0.5) can be given large plastic strain more easily as compared to steels with n ~ 0.15 m High T C ,T C → a constant m → index of strain rate sensitivity ◘ If m = 0 stress is independent of strain rate (stress-strain curve would be same for all strain rates) ◘ m ~ 0.2 for common metals ◘ If m (0.4, 0.9) the material may exhibit superplastic behaviour ◘ m = 1 → material behaves like a viscous liquid (Newtonian flow) Further aspects regarding strain rate sensitivity In some materials (due to structural condition or high temperature) necking is prevented by strain rate hardening. 1/mm 1/ m m P m P 1 C C ,T A CA From the definition of true strain m 11dL dA L dt A dt 1/mm 1/ 11dA P Adt C A 1/m dA P 1 . If m < 1→ smaller the cross-sectional area, the (1mm ) / dt C A more rapidly the area is reduced. If m = 1 → material behaves like a Newtonian viscous liquid → dA/dt is independent of A.
Details
-
File Typepdf
-
Upload Time-
-
Content LanguagesEnglish
-
Upload UserAnonymous/Not logged-in
-
File Pages70 Page
-
File Size-