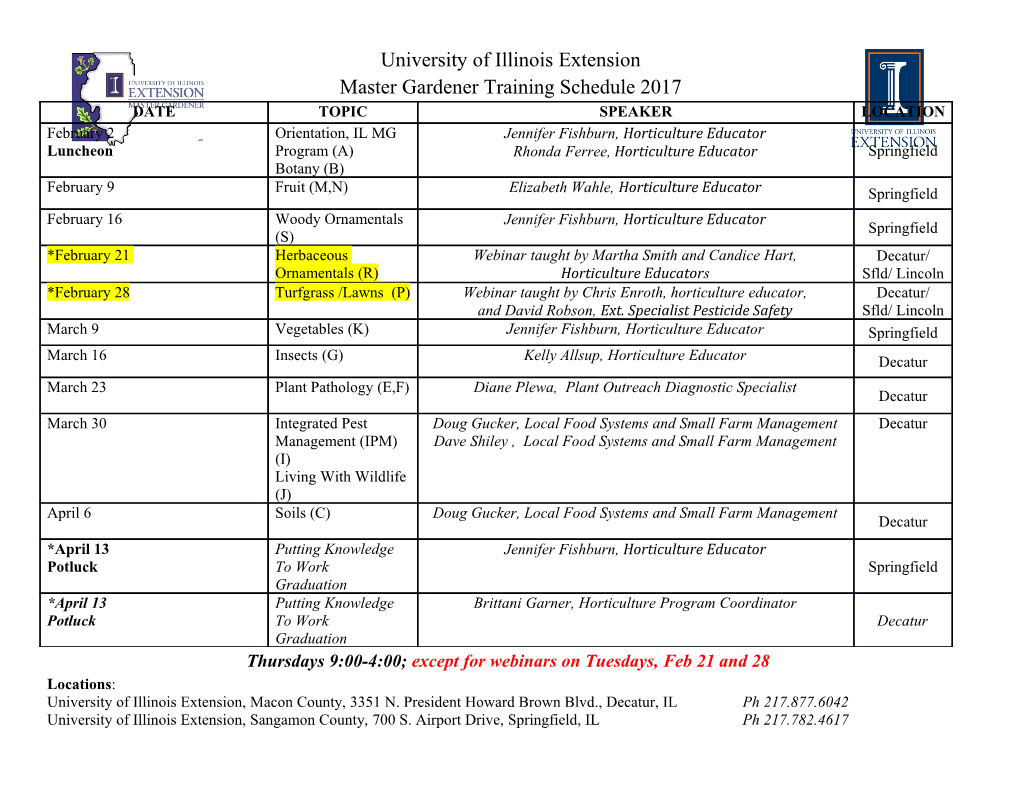
Paper ID #29350 Cloud Based Computer-Aided Engineering Education: Finding the Silver Lining Dr. Derek M Yip-Hoi, Western Washington University Dr. Yip-Hoi received his Ph.D. from the Department of Mechanical Engineering at the University of Michigan in 1997. Following his Ph.D. he worked for several years with the NSF Engineering Research Center for Reconfigurable Machining Systems also at the University of Michigan. His work involved supervision of sponsored research projects that focused on developing software applications to assist manufacturers design and plan operations on manufacturing systems that could be rapidly reconfigured to meet changes to a product’s design or production volume. Sponsors of this work included Ford, GM and Chrysler. In 2003 he joined the faculty of the Mechanical Engineering Department at the University of British Columbia as junior chair of an NSERC sponsored research program in Virtual Machining. After 3 years at UBC, he moved to the Department of Engineering Technology at Western Washington University to focus on teaching. His teaching and scholarship interests lie in the areas of design, CAD/CAM, CAPP, and CNC machining. Dr. Yip-Hoi is currently director of Western’s Manufacturing Engineering Program. c American Society for Engineering Education, 2020 Cloud Based Computer-Aided Engineering Education: Finding the Silver Lining Abstract The availability of cloud-based technologies to support engineering education has seen significant growth in recent years. This includes design (CAD), analysis (FEA), and manufacturing (CAM and Digital Mock-Up) capabilities. The availability of affordable and broadly accessible 3D-printing is one major driver of this trend. This has created demand for cheaper, easier to learn and more simply deployed CAD systems for authoring parts that can be 3D-printed. Industry 4.0 is another driver. To support the Internet-of-Things high levels of information automation are needed throughout the product development process. CAx software developers have noted these trends and have brought to market new systems that are configured to be profitable in this new era. However, these systems present unique challenges in an educational setting that impact the choice of platform and how they are deployed for instruction and project work. Depending on the system, one challenge may be the level of IT support that is needed. The cost of use for systems is also a major consideration for universities. Some vendors have adopted the Software-as-a-Service business model, while others still require paying a hefty one-time licensing fee for student and faculty accounts and data storage. As a result, there can be a significant variation in cost for access to the available platforms. This cost can be justified partly by the difference in capabilities. Though most systems now bundle in basic analysis tools and some manufacturing, others provide additional capabilities in advanced manufacturing planning and simulation, advanced analysis, integrated product lifecycle management, process planning and project management tools, and systems engineering. Finally, though some may argue otherwise, there are employment advantages for graduates in some industries that do their CAx work using a preferred platform. This paper will present the plans, efforts and experiences to date in deploying and use of Dassault Systemes 3DExperience® platform within a Manufacturing Engineering curriculum. This is a multi-year effort starting with CAD and Analysis that will over time incorporate into the curriculum many of the additional capabilities mentioned above. Rationale for the choice of this system will be discussed along with the challenges encountered to date and those that need to be overcome in fully implementing the plan. The experiences of students taking their first class using this platform will be presented along with those of faculty who have needs for CAx in their teaching and research. Introduction Cloud-based infrastructures have found their way into the realm of CAD/CAM/CAE (CAx) and promise to revolutionize the way in which engineers engage in using these tools. In the same way that computers and CAD revolutionized the approach to creating engineering drawings, cloud-based solutions are revolutionizing how information is automated throughout engineering problem-solving and design processes. This can be viewed as part of the direction being set by Industry 4.0 and the drive to support the Internet-of-Things which necessitates high levels of information automation throughout product development. This includes all information related activities from content generation to management, retrieval, analysis and dissemination. In addition to the impact of Industry 4.0, the availability of cheap 3D Printing machines and services is driving the growth of cloud-based CAx technologies. Greater access to 3D Printing technology for everyday use has fueled the growth of affordable and easy to use cloud-based applications to support use of these machines. These applications are easier to use and typically more affordable than their desktop-based predecessors. They present options for authoring content and to easily use this content to create a physical product if only a prototype. Junk and Kuen [4] provide a review of different cloud-based systems and their capabilities to effectively support 3D Printing. These trends have major implications for engineering education. Educators need to understand how information automation is going to impact the skill set for graduates entering the workforce and adapt instruction to accommodate for this. Curriculums that develop student’s skills in authoring using CAx tools must look to broadening this effort to include the other aspects of information automation. Educator’s must choose from the growing number of cloud-based systems available and strategize on how they are deployed for instruction and project work. Part of this strategy includes consideration of the available level of IT support. Cloud-based systems have the advantage of externalizing the effort needed to support Product Lifecycle Management (PLM). Universities no longer need to invest IT resources in setting up the server infrastructure to support this function. However, there are still IT needs that vary with the platform adopted. For example, some platforms run completely in the cloud (i.e. both data storage and computation) and can be used through a generic browser (e.g. Onshape®). Others require a heavy client to be downloaded onto a computer and rely on the Cloud mostly for data storage (e.g. 3DExperience). The latter require more in-house maintenance though the cost for developing and supporting a PLM infrastructure has been eliminated. This situation maybe transitionary as the trend seems to be towards shifting both data storage and computation to the Cloud. In their review of Digital Design and Manufacturing in the Cloud, Wu et al. [5] provide a technology guide to assist in making decisions on how best to select a Cloud-based application for use throughout product development. Though focused on the commercial customer their insight is useful for educators to also consider. The cost of use for systems is also a major consideration for universities. Some vendors have adopted a Software-as-a-Service (SaaS) business model, while others still require paying a hefty licensing fee for student and faculty accounts and data storage. There can be a significant variation in cost for access to the available platforms. This cost can be justified partly by the difference in capabilities. Most systems now bundle in basic analysis tools (e.g. FEA, Kinematics Simulation, CFD) and some manufacturing (e.g. CAM for CNC machining). The additional capabilities typically center around access to more advanced manufacturing planning and simulation (e.g. Robotics, Virtual Factory, Ergonomics), advanced analysis (e.g. Composites FEA), integrated Product Lifecycle Management, process planning and project management tools, and systems engineering. The integration of these tools within a single platform around a common database has advantages over disparate tools that need to be integrated, even though with standards this is getting easier. This presents unique challenges that will be discussed in this paper. Finally, though some may argue otherwise, there are employment (internship and permanent) advantages for graduates in some industries that do their CAx work using a preferred platform. Literature Review Wu et al. [1] pose the question “Is cloud-based design and manufacturing (CBDM) actually a new paradigm?” To answer this question they compare existing definitions related to the field of CBDM, develop a checklist with requirements that can be used to verify the existence of appropriate capabilities and provide a comparison with other related technologies such as web- and agent-based design and manufacturing. As part of this study, they develop a drone delivery system using existing CBDM tools such as Dassault Systemes 3DExperience platform (Software-as-a Service, SaaS), Compute Cloud® (Intrastructure-as-a-Service, IaaS), Google BigQuery® (Platform-as-a-Service, PaaS) and Alibaba.com® (hardware-as-a-Service, HaaS). They conclude that CBDM is in fact a new, emerging paradigm evolving from existing technologies that will revolutionize “digital manufacturing and design innovation” [1]. In their work, Vila et al. [2] note that CAx and PLM are taught separately and that a holistic approach is needed to support Industry 4.0 skills and
Details
-
File Typepdf
-
Upload Time-
-
Content LanguagesEnglish
-
Upload UserAnonymous/Not logged-in
-
File Pages18 Page
-
File Size-