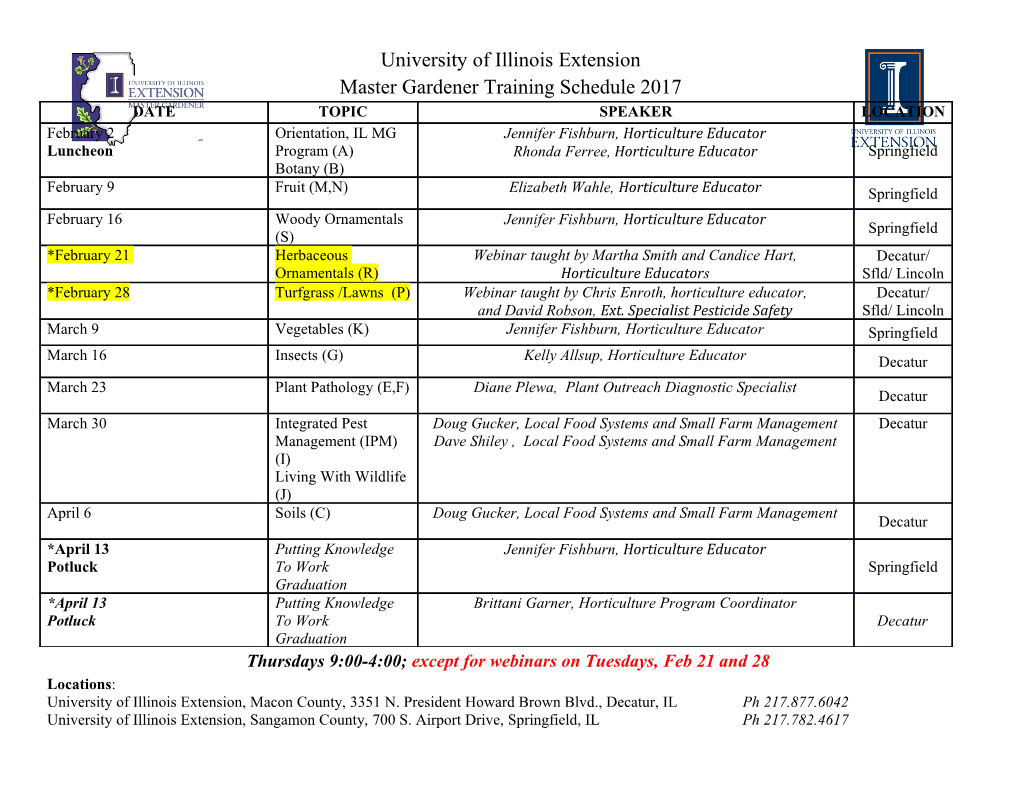
PROCESSING OF CARBON–SILICON CARBIDE HYBRID FIBERS Dissertation Submitted to The School of Engineering of the UNIVERSITY OF DAYTON In Partial Fulfillment of the Requirements for The Degree of Doctor of Philosophy in Engineering By Saja M. Nabat Al-Ajrash Dayton, Ohio December 2019 PROCESSING OF CARBON–SILICON CARBIDE HYBRID FIBERS Name: Al-Ajrash, Saja M. Nabat APPROVED BY: ________________________________ __________________________________ Khalid Lafdi, Ph.D. Donald A. Klosterman, Ph.D. Advisory Committee Chairman Committee Member Professor, Wright Brothers Endowed Associate Professor, Torley Endowed Chair in Nanomaterials Chair in Composite Materials Department of Chemical and Materials Department of Chemical and Materials Engineering Engineering ________________________________ __________________________________ Erick S. Vasquez, Ph.D. Youssef Raffoul, Ph.D. Committee Member Committee Member Assistant Professor Professor Department of Chemical and Materials Department of Mathematics Engineering ________________________________ __________________________________ Robert J. Wilkens, Ph.D., P.E. Eddy M. Rojas, Ph.D., M.A., P.E. Associate Dean for Research and Dean, School of Engineering Innovation Professor School of Engineering ii © Copyright by Saja M. Nabat Al-Ajrash All rights reserved 2019 iii ABSTRACT PROCESSING OF CARBON–SILICON CARBIDE HYBRID FIBERS Name: Al-Ajrash, Saja M. Nabat University of Dayton Advisor: Dr. Khalid Lafdi Two processing methods were used to fabricate carbon-SiC hybrid fibers. The first approach utilized various ratios of a silicone polymer (polydimethylsiloxane) as a silicon source and polyacrylonitrile (PAN) as a carbon source. The second approach used a mixture of silicon nanoparticles at various concentrations in PAN. The two formulations were independently converted into fiber form using an electrospinning process. Nanofibers with several hundred of nanometer diameters were successfully fabricated and subsequently stabilized and carbonized at 1000 oC. In the first approach, three phases were found to be present: nanocrystalline SiC, turbostratic carbon and SiOC. The resulting fibers showed a core-skin structure with the skin rich in carbon and a core dominated by silicon- based phases in the form of SiC or SiOC phases. A significant improvement in both tensile strength and elastic modulus was observed for C-SiC hybrid fibers as compared to SiC- free carbon fibers produced in this study. In the second approach, one of the key issues identified for the study was particle distribution during the electrospinning. The analysis revealed that large silicon particles were located in the skin and the smaller ones were located at the core. The migration rate from the core was the fastest for large particles and was diminished as the particles became smaller in size due to inertial effects. The threshold for the Stokes number was found to be around 2.2 x 10-4 with a critical particle size of 1.0 x 10-7m in diameter. The current results iv are very promising, as it demonstrated a novel way for the fabrication of PAN/SiC ceramic nanofiber with a gradient of particle size and properties from the skin to the core. In addition, the ratio of Si to carbon precursor and heat treatment procedure were optimized to process hybrid nanofibers with high oxidation resistance. After pyrolysis to 1250 oC, the nanofibers showed two-dimensional ordered carbon and SiC nano phases. Samples with 90 wt%PAN/10 wt% Si showed approximately four-time improvement in char yield as compared with 100 wt% PAN. It was concluded that the SiC phase played a major role in ordering the carbon phase. The carbon and SiC crystallinities had a great impact on improvements in the mechanical properties and the oxidation resistance, respectively. The SiC grain growth was predicted using Scherrer formula, and its exponent was found to be around n = 4 with activation energy around 35 KJ/mol.K. For such growth, the dominant grain growth mechanism was concluded to be grain boundary diffusion. Furthermore, a complete transformation of Si to SiC occurred at 1250 °C. However, for heat treatments below 1000 °C, three phases, including Si, C, and SiC were present. The effect of microstructural changes due to the heat treatment on oxidation resistance was determined using thermogravimetric analysis. The char yield showed linear increasing growth as the carbonization temperature ranged from 850 °C to 1250 °C. Increasing the holding times at higher temperatures produced a significant increase in thermal stability because of SiC grain growth. At long holding times, the SiC phase was observed to function as both an antioxidation coating and a mechanical reinforcing phase. Such structural changes lead to changes in fiber mechanical properties. The tensile strength was the highest for fibers carbonized at 850 °C, while the modulus increased monotonically with increasing carbonization temperature. v Dedicated to my Parents Modher Nabat & Kawakib Hameed Brothers Ahmed and Manar Sisters Zahraa and Reyam Lovely Daughters Sarah and Sally vi ACKNOWLEDGEMENTS My special thanks to Dr. Khalid Lafdi, my advisor, for providing the time, material and equipment necessaries, for guiding me to be a competent researcher, for directing this dissertation and bringing it to an accomplishment patiently and professionally, for being an inspiring mentor. I would also express my appreciation to everyone who helped me. This includes but not limited to my parents, my committee, Faculty including: Dr. Charles Browning, Dr. Donald A. Klosterman, Dr. Erick S. Vasquez, Dr. Youssef Raffoul, Dr. Cao Li, Dr. Francisco Chinesta, Dr. Abdulaziz Baçaoui, and Friends including: Robyn Braford, Qichen Fang, Yuhan Liao, Jean-Baptiste Dumuids, Nuha Al Habis, Chang Liu, Robert Busch, Rose Eckerle and Shuangshan Li. Last but foremost, I would like to thank my family, especially my parents (Dr. Modher Nabat) and Kawakib. No words expressing my love and gratitude to the best, first and wisest man I have ever seen, my father. His hard working, ethics, and courage shaped me into what I am today. The sacrifices from my mother, including quitting her job to support us are never limited. Finally, I would like to thanks my six-year-old daughter, Sarah, and three-year-old daughter, Sally. Just looking to their innocent face inspires and motivates me to work hard and being a successful woman who they admire. I also genuinely apologize for spending less time with them and, hopefully, when they understand what life is, will help them to appreciate the struggle I went through. vii TABLE OF CONTENTS ABSTRACT .................................................................................................................. iv DEDICATION ………………………………..…………………………..…………………vi ACKNOWLEDGEMENTS ......................................................................................... vii LIST OF FIGURES ....................................................................................................... xi LIST OF TABLES ........................................................................................................xv LIST OF ABBREVIATIONS AND NOTATIONS .................................................... xvi CHAPTER I INTRODUCTION .....................................................................................1 1.1 Introduction ...........................................................................................................1 CHAPTER II MATERIALS AND BACKGROUND ....................................................5 2.1 Carbon-Based Material .........................................................................................5 2.1.1 Carbon Fibers ............................................................................................ 7 2.2 Hybrid Carbon- Preceramic Polymer Materials ..................................................16 2.3 Hybrid Carbon Materials with Solid Particles ....................................................18 CHAPTER III FABRICATION OF HYBRID NANOFIBER USING POLYDIMETHYLSILOXANE AND POLYACRYLONITRILE POLYMER BLENDS ....................................................................................................................20 3.1 Introduction .........................................................................................................20 3.2 Materials and Method..........................................................................................24 3.2.1 Electrospinning of PDMS/PAN Nanofiber ............................................. 24 3.2.2 Stabilization and Pyrolysis of PDMS/PAN Nanofiber ........................... 25 3.2.3 Characterizations ..................................................................................... 26 3.3 Results and Discussion ........................................................................................27 3.3.1 Nanofiber Morphologies ......................................................................... 27 3.3.2 Energy Dispersive Spectroscopy ............................................................. 29 3.3.3 Fourier Transform Infrared Spectroscopy ............................................... 30 3.3.4 Raman Spectroscopy ............................................................................... 32 viii 3.3.5 X-Ray Diffraction ................................................................................... 33 3.3.6 Transmission Electron Microscopy ......................................................... 34 3.3.7 Tensile Test ............................................................................................
Details
-
File Typepdf
-
Upload Time-
-
Content LanguagesEnglish
-
Upload UserAnonymous/Not logged-in
-
File Pages134 Page
-
File Size-