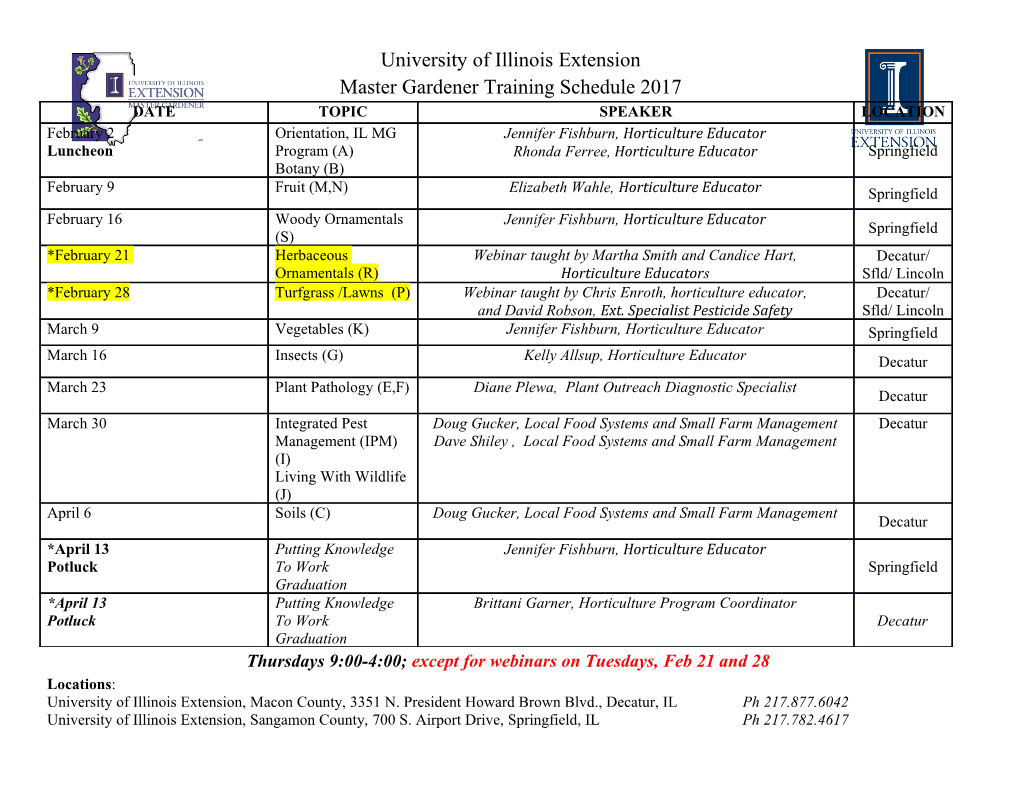
Profile Plastics —Strong engineering adds value to projects for medical THERMOFORMING By Mark Shortt Thermoforming Giant Opens up on Work for Medical, other Industries isten to Steve Murrill give an overview of Profile Plastics, the company that he serves as president, and you’re sure Lto get much more. Murrill, a degreed chemical engineer with an MBA in finance, has been actively involved in working to advance not just his company, but the entire thermoforming industry since he bought Strong engineering Profile Plastics in 1986. In a December phone interview, adds value to projects Murrill traced his company’s for medical and beyond progress from the mid-’80s against a backdrop of techni- cal milestones and trends—the evolution of pressure forming and 5-axis CNC machining, for example, and the greater use of These thermoformed enclosures earned Profile Plastics one of molded-in features—all the while explaining what they’ve meant its many awards from the SPE Thermoforming Division Parts to the success of thermoformers everywhere. Competition. Photo courtesy of Profile Plastics. Profile Plastics (www.thermoform.com), a custom thermo- forming company in Lake Bluff, Illinois, specializes in produc- Profile’s 100,000-square-foot facility includes more than a ing highly engineered plastic parts to close tolerances and high dozen dedicated thermoforming cells and a similar number cosmetic requirements. The company has reportedly won top of 5- and 6-axis CNC trimming cells, providing the capacity honors at 19 of the annual SPE Thermoforming Parts Competi- and flexibility to meet a variety of fast-changing production tions, sponsored by the Thermoforming Division of the Society and product design requirements. The company offers custom of Plastics Engineers, since SPE began sponsoring them in the vacuum forming, pressure forming, and twin sheet forming, and 1980s. Murrill himself was honored as Thermoformer of the Year can manufacture parts up to 8 feet by 12 feet from thermoplastic by the Division in 2011 after winning a Lifetime Achievement sheet up to 0.5-inch thick. Award in 2001. The ISO 9001:2008 certified company also takes pride in We asked Murrill if he had enough room at his facility to hold its success in expanding the viability of thermoforming, largely all those awards. He wasn’t biting. through use of what it calls value added engineering. A good “We don’t rest on our laurels,” he replied, adding that al- example, Murrill said, is the increased use of molded-in fea- though many of the winners were state of the art at the time that tures. “By being able to mold more features in, that often times they were awarded, time marches on and new challenges continue cuts costs,” he said. “Because one option is to not have many to emerge with each passing year. “It’s fun to look back at the old features molded in, and either machine them in or bond them ones, and we have some, believe it or not, that are actually still on separately afterwards. That raises the cost and increases the in production. The very first one, in fact, is still in production.” opportunity for rejects. Murrill was referring to an air conditioner plenum for a main- “A significant push is towards a lot of tooling creativity to mold frame computer room, which requires very precise temperature in features,” Murrill added. “The other part is in this attention control. “The part we make has nothing to do with the air condi- to detail on the backside, developing the 5-axis CNC machining tioning system, but they needed a 2-foot by 4-foot, complete air strategies to capture a part repeatedly in a nest or a fixture, and distribution and air intake plenum to put as the room interface programming the 5-axis machine to trim it consistently, and then between the air conditioning unit and the ceiling and the room,” have ways to QC and monitor the process of the parts to be sure he explained. “So this unit is 2 feet by 4 feet, and it has the air that the consistency is maintained.” filters for the return air and the air distribution network, if you Murrill also said that the breakthrough of 5-axis CNC machin- will, to distribute the conditioned air very efficiently. We devel- ing helped thermoformers compete with injection molders by en- oped it in 1986 and it’s still being sold today.” abling them to produce parts with the consistent fit and function 66 February 2014 • www.d2pmagazine.com 67 required of precision injection vantageous. Pressure form- molded parts. “To go after that ing has higher cosmetics, market, the part had to have a which means more expen- consistent trim and a consistent sive tooling. You can get fit. And in the early days, it was higher cosmetics having all being hand trimmed, which the sheet molded against was not only very labor inten- the tool—the cosmetic side sive; it was very imprecise,” he against the tool. So it’s gen- said. “So the 5-axis CNC machin- erally a tooling issue that ing, which came largely from separates the two. the woodworking industry in Twin sheet is an innova- the late 80s, was really kind of tion that allows two-sided the breakthrough to solidifying forming that you can’t get the quality of the fit.” in pressure forming versus Thermoformed parts pro- injection molding, which duced by Profile Plastics are is two sided by definition. used in a range of application The folks in the automo- areas requiring large, highly tive industry started call- cosmetic parts that are manu- ing it (twin sheet) sheet factured to tight tolerances blow molding, and that’s a and in relatively low volumes. pretty good definition of it One of the company’s core because it really now can do markets is medical equipment, products that blow molding including covers and enclosures for Profile Plastics concurrently developed nine mating and would do. But blow molding has two imaging machines and carts. But the matching parts for the dental imaging unit. Engineers significant advantages: At very high company also does work for OEMs in optimized points of attachment so that the product could be volume, it’s low cost, and if polyethyl- assembled easily. Photo courtesy of Profile Plastics. the industrial, transportation, food ene will work for an application, they and beverage, and recreation sectors. (blow molders) will be very cost effec- One project for a medical OEM challenged Profile Plastics to tive. But if it’s not polyethylene, and the volume’s not that large, provide multiple parts for what was intended to be an aesthetically the blow molders aren’t really set up to handle those situations. appealing dental imaging unit without any hint of trimmed edges Twin sheet forming can operate underneath that gap or void in its final assembly. Profile’s engineers designed the tooling for in the market with lower run, shorter run requirements. Any nine of the component parts, most of them using articulated resin we can find in sheet form, we can twin sheet. We can have undercuts to ensure that trimmed edges weren’t visible in the the advantages of two different types of materials, two different finished product. Pressure forming was used to ensure that final thicknesses of materials, two different colors. It also creates a parts showed consistency in color, texture, and gloss throughout hollow space between two parts, which is useful many times for the entire product. And with a view to final assembly, engineers insulation—either sound insulation or temperature insulation. optimized the points of attachment to ensure that it could be By creating that space, you also create places you can run wires; assembled easily. you can use the part to be an air duct. When all was said and done, Profile completed the complex There are some headliners that have twin sheet ducting sys- project on time and on budget, enabling its customer to meet tems in them that are very sophisticated. It’s like an airplane— its production and marketing goals. But although it neatly rep- how you have the air drop over every passenger’s seat. Well, you resents Profile’s ability to meet the stringent requirements of can do the same kind of thing in automotive or truck, having medical equipment OEMs, its relevance extends beyond that. a web, if you will, or a network of one big twin sheet part that Over the years, customers have come to recognize that Profile will duct the heat or cool to specific areas in the vehicle. That’s Plastics, sharpened by its experiences in the medical arena, brings generally not a cosmetic application. You just want to get wires to each project the same manufacturing know-how, the same or air—hot or cold—from one part of the product to another commitment to engineering excellence, and the same thirst for part of the product. creative problem solving that it turns loose when working for D2P: Medical is one of your core markets. Do you see any medical equipment OEMs. major trends in the medical industry that are impacting the “There’s not too big of a difference in terms of the way we types of products being developed, or the way they’re being deal with the customers,” says Murrill. manufactured? Following is an edited transcript of our conversation with SM: I see two. One is the one we all know of, but it can’t be Steve Murrill. overlooked. We tell the story that we made the covers for GE D2P: As a provider of heavy-gauge thermoforming, Profile Medical’s first ultrasound machine, and it was approximately 5 Plastics offers vacuum forming, pressure forming, and twin feet tall, 3 feet wide, and 3 feet deep.
Details
-
File Typepdf
-
Upload Time-
-
Content LanguagesEnglish
-
Upload UserAnonymous/Not logged-in
-
File Pages6 Page
-
File Size-