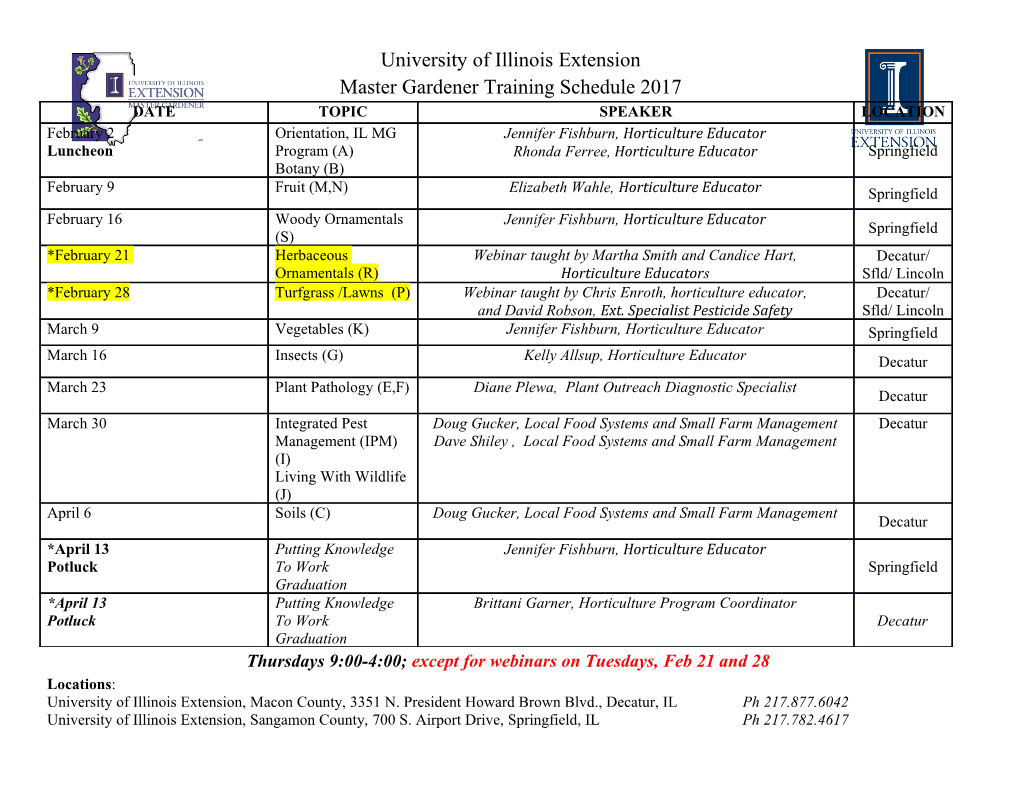
Requirements for Active Resistive Wall Mode (RWM) Feedback Control Yongkyoon In1 In collaboration with M.S. Chu2, G.L. Jackson2, J.S. Kim1, R.J. La Haye2, Y.Q. Liu3, L. Marrelli4, M. Okabayashi5, H. Reimerdes6, and E.J. Strait2 1FAR-TECH, Inc., San Diego, CA, USA 2General Atomics, San Diego, CA, USA 3UKAEA, Culham Laboratory, UK 4Consorzio RFX, Padua, Italy 5Princeton Plasma Physics Laboratory, Princeton, NJ, USA 6Columbia University, New York, NY, USA 14th Workshop on MHD Stability Control, November 9-11, 2009 Princeton Plasma Physics Laboratory, Princeton, New Jersey Active feedback control safeguards high performance plasmas against the uncertainty of RWM stability boundary • The RWM stabilization is essential to sustain high performance plasmas in ITER or reactor- grade devices • The uncertainty of stability boundary of pressure-driven RWM challenges the evaluation of RWM stabilization process • Even if RWM is passively stabilized, a coupling of marginally stable RWM with other MHD activities readily leads to the unstable RWM, requiring active feedback control1 1M. Okabayashi et al, Nucl. Fusion (2009) 1 Reproducible current-driven RWM helps us clarify both physics requirements and control specifications for feedback control • Highly reproducible current-driven RWM enables us to explore the RWM feedback control (no or little external torque source) – The RWM feedback control can be assessed using a reproducible RWM target at q95 ~ 4. • A systematic thorough investigation of various control parameters allows us to benchmark both RWM theory and control aspects • BUT, the optimization of RWM feedback control is ultimately determined by the minimal level of plasma fluctuation beyond magnetics 2 Outline • Introduction • Schematic of active RWM feedback control • Optimized feedback control (limited to PD controller for now) – Gain scans – Bandwidth requirements – Phase-shifts – Efficacy of active feedback control • Physics requirements – Internal vs external feedback coils – Direct RWM feedback vs error field correction (EFC) – Simplified Feedback control model – Mode structure – Possibility of 2nd least-stable RWM • Discussion • Conclusions and future works 3 The helical structure of the feedback is configured to match the structure of the n=1 RWM 4 Active feedback control system in DIII-D fully stabilizes current-driven RWM in parallel with EFC • Tools • Ohmic discharge with high – Internal coils (“I-coils”): current ramp-up rate Direct Feedback + Dynamic error field • Feedback loop (τp << τw) correction (EFC) n=1 n=1 – External coils (“C-coils”): VFB (τw,τL/R, δIFB ) Feed-forward EFC Power Supply Plant (DIII-D/RWM) n=1 δB + ? Controller 1 ⎡ Gsd ⎤ Ks()=+⎢ G τ d ⎥ 11++ssp τ p ⎣⎢ τ d ⎦⎥ Gp,d : Gain τp,d : time constant where p - proportional, and d - derivative ? : Unknown n=1 error field 5 Current-driven RWM was obtained, diagnosed, and controlled with no external torque source present Plasma shape, p, q, and • Upper Single Null Ωφ @ 405 ms on 133021 (close to Double Null shape) • Monotonic pressure and q- profiles • Plasma rotation profile is nearly flat according to CER measurement using carbon-VI line [nearly “zero”: (Ω0/ωA)< 0.1 %)] 6 Complete feedback stabilization of current-driven RWM at q95~4 has been achieved in DIII-D 133021 133018 • RWM is observed to be 6 q No feedback vs feedback 5 95 i) non-rotating or moving 4 slowly in co-Ip direction 3 30 δ n=1 at its birth, but Bp (G) 20 ii) flips to the counter-I 10 p 0 direction as the mode 180 grows up 0 n=1 φ (deg) -180 • Balanced beam-pulse 500 IU (A) every 100 msec for 12 0 30 -500 60 ms msec duration to 400 420 440 460 480 500 520 measure q-profile and Time (ms) plasma rotations 7 Optimized feedback control –Gain scans (Gp only vs Gp/Gd) –Bandwidth requirements –Phase-shifts –Efficacy of active feedback control 8 An optimized gain has been found in the vicinity of “unit” flux gain (applied δΨr∼ measured δΨθ) Maximum Mode Amplitudes (Gauss) vs G p 25 20 15 10 Optimized 5 Unit flux gain Optimized 0 0 50 100 150 Proportional Gain G p • As the gain approaches the optimal level, the mode growth rate decreases as expected • The higher coil currents at low gains are primarily attributable to an inadequate EFC to unknown error field 9 The optimized RWM feedback control minimizes the plasma fluctuations beyond the plasma boundary No feedback (133021) Feedback (133018) n=1 Amp. [G] [keV] Nov.08,2008 10:06:26 e 0.05 1.8 1.8 1.7 R Core maj 1.7 1.6 1.6 1.5 0 R [m] R [m] 1.5 q~2 1.4 1.4 1.3 δTe 1.3 1.2 1.2 −0.05 Edge 0.44 0.45 0.46 0.47 0.48 0.49 0.5 0.44 0.45 0.46 0.47 0.48 0.49 0.5 Time [s] Time [s] • RWM-induced edge fluctuations are also suppressed. 10 The use of derivative gain broadened the effective gain range for RWM feedback stabilization Maximum Mode Amplitudes vs Gp Unit flux gain • Similarly finite amplitude of the coil currents at various Gp values are associated with the EFC portion necessary for effective RWM stabilization. 11 The addition of Gd minimizes the phase lag in time between RWM and the applied field Without Gd (133017) With Gd (133014) [keV] e 0.05 1.8 1.8 1.7 Core 1.7 Rmaj 1.6 1.6 0 R [m] 1.5 R [m] 1.5 1.4 1.4 Gp=40 1.3 δTe 1.3 Edge 1.2 1.2 −0.05 0.44 0.45 0.46 0.47 0.48 0.49 0.5 0.44 0.45 0.46 0.47 0.48 0.49 0.5 Time [s] Time [s] • A value of Gd =10Gp is chosen to use voltage controller ‘effectively’ as current controller, based on τd and τL/R of the feedback system. 12 The voltage controller used for RWM feedback could work as current controller using derivative gain =>Still the bandwidth is limited -1 -1 by minimum (τp , τd ) δI Plant,P(s) δB Controller,K(s) δV K K =>The high frequency role-off L/R PCS due to L/R time could be 1 where Ks()= and compensated by the LR/ 1+s τ L/R choice of Gd, which helps 1 ⎡ Gsd ⎤ the system function as Ks()=+⎢ G τ d ⎥ PCS11++ss p current controller. τ pd⎣⎢ τ ⎦⎥ 13 Impact of DEFC on RWM feedback can be fully explored by the bandwidth scan • Transition from DEFC to RWM-dominant regime - RWM: τp < τw - Dynamic EFC: τp > τw – Feed-forward EFC: pre- programmed • The low frequency EFC is necessary but not sufficient for RWM stabilization 14 The RWM feedback action should be taken faster than the mode growth time, as predicted1 τg : 3 - 4 ms • When τp < τg : effective , while τp > τg :ineffective • The used fixed gain provides δΨr ~ 5 x δΨθ on the midplane magnetic sensor 1 T. Strait et al, Nucl. Fusion (2003) 15 A phase-shifted n=1 field in the direction of co-Ip rotation is more effective than in the opposite direction Maximum Mode Amplitudes [G] vs δφFB Phase-shift dependency in MARS-F Stabilized • A range of preferred toroidal phase shifts ahead of the RWM exists for effective feedback, consistent with theory 16 The efficacy of the feedback stabilization needs to be cautiously assessed based on magnetics alone Gd= 10Gp Gp= 80 (133011) Gp= 160 (133012) Gp= 320 (133013) e e e 0.05 1.8 .8 .8 1.7 Rmaj .7 .7 Core 1.6 .6 .6 0 R [m] 1.5 .5 .5 q~2 1.4 .4 .4 1.3 δT .3 .3 Edge e 1.2 .2 .2 −0.05 0.44 0.45 0.46 0.47 0.48 0.49 0.50.44 0.45 0.46 0.47 0.48 0.49 0.5 0.44 0.45 0.46 0.47 0.48 0.49 0.5 Time [s] Time [s] Time [s] • Similar plasma responses based on magnetics may not reflect the detailed evolution of the RWM-associated internal structures. • The choice of Gd may not be optimal yet (likely due to mode coupling to coil currents,≠ ) (τ L //RLR)eff τ 17 Physics Requirements – Internal vs external feedback coils – Direct RWM feedback vs error field correction (EFC) – Simplified feedback control model – Mode structure – Possibility of 2nd least-stable RWM 18 The RWM feedback coils external to the vessel was found ineffective in stabilizing RWM • The internal coils (“I-coils”) merit more effective coupling of the feedback field due to the proximity to the plasmas than the external coils (“C-coils”) • This suggests that the error-field (EF) correction coils in ITER might not be a good choice for the purpose of RWM feedback control, though the investigation was not exhaustive. RWM growth time, τ : 3 ms g 19 Even after RWM stabilization, finite coil currents remain working as error field correction • While the gain K increases, the δB gets smaller, but the time-averaged δIrarely changes • Both DEFC and RWM feedback are working inside closed-loop but their roles are distinctive - DEFC: minimize the lack of axisymmetry of external DEFC field (low freq.) - RWM feedback: nullify the perturbed δB coming from unstable RWM (high freq.) 20 RWM feedback cannot be replaced by error-field correction (EFC) RWM growth is not influenced by EFC (i.e. no slope change) RWM growth time, τg : 3 - 4 ms 21 Simplified feedback model is based on idealized current controller • Measured perturbed field δB = δBRWM+δBEF+AδBFB where δBRWM: RWM, δBEF : Error field, A : Plasma response (amplification), and δBFB = -K δB = -αIcoil K: Normalized gain (=Gp/Gp0) Icoil : feedback current (=IEFC+δIRWM), contributing to EFC and direct RWM FB 22 The key components in feedback control can be explicitly represented in modeling • Assumptions – Open loop K=0 shows finite δB = δBRWM+ δBEF where δBRWM > 0 only for unstable RWM (δBRWM = 0 for stable RWM) – δBEF > 0 can remain finite even when δBRWM = 0 – Feedback is configured to oppose measured δB.
Details
-
File Typepdf
-
Upload Time-
-
Content LanguagesEnglish
-
Upload UserAnonymous/Not logged-in
-
File Pages33 Page
-
File Size-