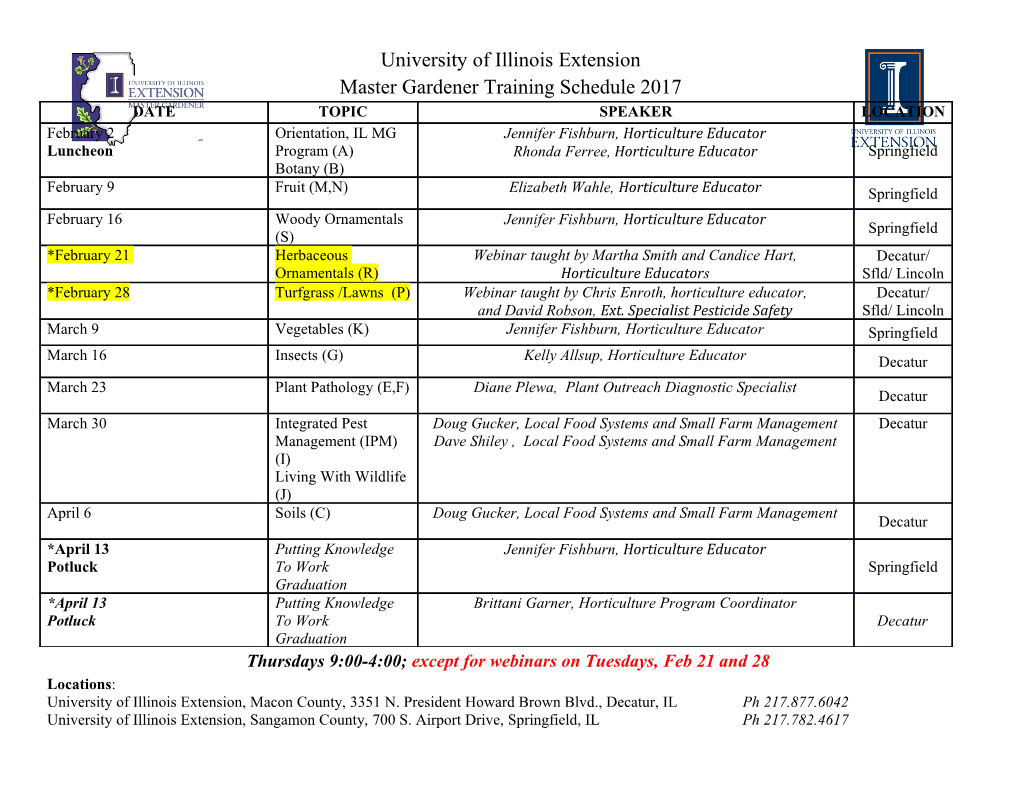
23. - 25. 5. 2012, Brno, Czech Republic, EU ANALYSIS OF NONRANDOM PATTERNS IN CONTROL CHART AND ITS SOFTWARE SUPPORT Darja NOSKIEVIČOVÁ FMMI, VŠB-TU Ostrava, 17. listopadu 15, 708 33 Ostrava – Poruba, Czech Republic, [email protected] Abstract Identification of assignable causes of the process variability and restriction and elimination of their influence are the main goals of statistical process control (SPC). Identification of these causes is associated with so called tests for special causes or runs tests. From the time of formulation of the first set of such rules (Western Electric rules) several different sets have been created (Nelson rules, AIAG rules, Boeing AQS rules, Trietsch rules). This paper deals with the comparison analysis of these sets of rules and with the analysis of the computer support of them. At the end of this paper some recommendations for the correct use of these rules are formulated. Keywords:, Common causes, special causes, runs tests, natural pattern, unnatural pattern 1. INTRODUCTION Statistical process control (SPC) is an approach to process control that has been widely used in any industrial or non-industrial fields. It is primarily a tool for understanding process variation [1]. SPC is based on so called Shewhart´s conception of the process variability. This conception distinguishes variability caused by obviously effected common causes (process is considered to be statistically stable) from variability caused by abnormal special (assignable) causes (process is considered not to be statistically stable) using control charts. The main goals of SPC is an identification of abnormal variability caused by special (assignable) causes with the aim to make the process stable, minimize the process variability, improve the process performance. To meet these goals SPC must be built as the problem solving instrument and the sequence of the subprocesses “Out-of control signal revelation – Root cause identification – Action acceptance – Verification of action” must be the axis of the SPC application. In this paper the stress is put on the first subprocess applying to so called Shewhart control charts. Control chart is the main SPC instrument for the analysis of the process variation over time. It is a graphical depiction of the process variation and its natural and unnatural patterns. Control chart displays a value of the quality characteristic that has been measured or some sample statistics that has been computed from measured values in sample versus the sample number or time. Central line in the control chart represents the average value of the quality characteristic corresponding to the statistically stable process (only natural pattern is presented and only common causes influence the process). Control limits are set so that when the process is statistically stable, nearly all the points in control chart fall between them (for mostly applied ±3σ control limits and assumed normal distribution it is 99,73% points). As long as the points are within the control limits and they show natural random pattern, the process is considered to be statistically stable. But if some points are out of the control limits or the points inside the limits show nonrandom (unnatural) pattern it is assumed that assignable cause of the abnormal process variation is present and must be removed from the process via searching for it and corrective action or some improvement must be realized. In general the points plotted on a control chart form an irregular up-and-down pattern – natural or unnatural. An advantage of using control charts is that it enables observation of the process behaviour over time to search for occurring of any unnatural pattern [2] as a symptom of the special (assignable) cause and as a signal for the reduction of the process variation and for improvement. 23. - 25. 5. 2012, Brno, Czech Republic, EU Natural pattern is such pattern where the points fluctuate randomly. It can be characterized as follows [3]: most points lie near the central line; only few of the points spread out and reach the control limits; very rarely some point goes out of the control limit. When some or all these attributes are missing the pattern will be classified as unnatural. Many types of unnaturalness can be recognized in control charts. But several generic patterns that can be detected for various processes were defined. In table 1 we can find mostly recommended (for instance in [3], [4], [5], [6], [7]) and applied nonrandom patterns for Shewhart control charts with their description and their typical symptom in control chart. To standardize and simplify the process of the typical unnatural patterns recognition statistical tests (rules) that quantify the length of the unnatural patterns were formulated. Table 1 Unnatural pattern description No. Unnatural (non- Pattern Description Symptom in control chart random) pattern 1 Large shift Sudden and high change Points near and or beyond control limits (strays, freaks) 2 Smaller sustained Sustained smaller change Series of points on the same side of the central shift line 3 Trends A continuous changes in one Steadily increasing or decreasing run of points direction 4 Stratification Small differences between values in A long run of points near the central line on the a long run, absence of points near both sides the control limits 5 Mixture Saw-tooth effect, absence of points A run of consecutive points on both sides of near the central line central line, all far from the central line 6 Systematic Regular alternation of high and low A long run of consecutive points alternating up Variation values and down 7 Cycle Recurring periodic Cyclic recurring patterns of points movement 2. TESTS FOR UNNATURAL PATTERNS RECOGNITION Tests for unnatural patterns supplement the evidence of the unnatural pattern given by the position of the points relative to the control limits or central line with evidence based on the statistical theory of runs [8] except the Shewhart rule (point out of the control limit). They are based on the probability calculations that tell us the portion of points lying near the central line, near the control limits, etc. We will discuss tests that cover unnatural patterns no. 1 - 6 (see the former table), i.e. shifts, trends, mixtures, systematic variation and stratification. Table 2 contains sets of the rules that are the most well – known and applied (Shewhart rule [9], Western Electric rules [3], Nelson tests [10], ISO 2859 tests [11], special sets formulated by large companies (Boeing [12], AIAG [13]) and the most new set by Trietsch [2]. Rules 1 - 4 were defined to quickly recognize patterns linked to the shifts in the process. Rule 5 is connected with the trends, rule 6 and 8 with patterns caused by incorrect sampling and rule 7 with abnormal oscillation. Historically first rule for the detection of the assignable cause developed W. S. Shewhart – in table 2 it is Rule 1. Set of Western Electric Rules added to the Shewhart criterion run tests covering such unnatural patterns as smaller or sustained shifts (called zone tests), mixtures, stratification and systematic variation. To be able to apply these tests the region between control limits in control chart must be divided into 6 zones each of 1 sigma width and the location of the predefined sequences of the points in relation to these zones must be evaluated. As normal distribution of the applied sample statistics is supposed, in zones C 68,27% values, in zones B 27,18% values and in zones A 4,28% values are expected when process is statistically 23. - 25. 5. 2012, Brno, Czech Republic, EU Table 2 Tests for unnatural patterns Tests for unnatural Shewhart Western Nelson ISO AIAG Boeing Trietsch patterns Rule Electric Tests 8258 Rules ASQ Rules Rules Rule 1 1 1 1 1 1 1 One or more points more than 3 sigma from the mean (beyond zone A) Rule 2 2 5 5 2 5 2 of 3 consecutive points between 2 and 3 sigma from the mean (in zone A or beyond) Rule 3 3 6 6 3 6 4 of 5 consecutive points between 1 and 3 sigma from the mean (in zone B or beyond) Rule 4 4 2 2 2 4 2 8 consecutive points on one side of the mean (in 9 points 9 points 7 points 9 points zone C or beyond) Rule 5 3 3 3 3 Six consecutive points steadily increasing or decreasing Rule 6 7 7 7 15 consecutive points both above and below central 13 points line ( in zones C) Rule 7 4 4 4 14 consecutive points alternating up and down 13 points Rule 8 8 8 8 Eight points in a row on both sides of the central 5 points line with none in zones C stable. Rules 2, 3 and 4 were designed for quicker identification of the shifts from the mean as compared to the test 1 (early warning indicators). As it can be seen in table 2 the most complex as to the rate of covering all eight defined rules are Nelson rules [10]. In addition to the Westerns Electric set Nelson defined run test for the oscillation and for the trends. In rule 4 he changed the length of the run from 8 to 9 points. As compared to the Western Electric rules the sequence of the rules had been changed by Nelson, too. Standard for Shewhart control charts ISO 8250 has wholly copied the Nelson set of rules. Also Trietsch in his publication works with the Nelson rules but in rules 6, 7, 8 he has changed the length of the runs to reach better statistical properties of these tests. 23. - 25. 5. 2012, Brno, Czech Republic, EU Rules of the companies Boeing and AIAG have less complex sets of rules based on the first four Western Electric zone rules.
Details
-
File Typepdf
-
Upload Time-
-
Content LanguagesEnglish
-
Upload UserAnonymous/Not logged-in
-
File Pages8 Page
-
File Size-