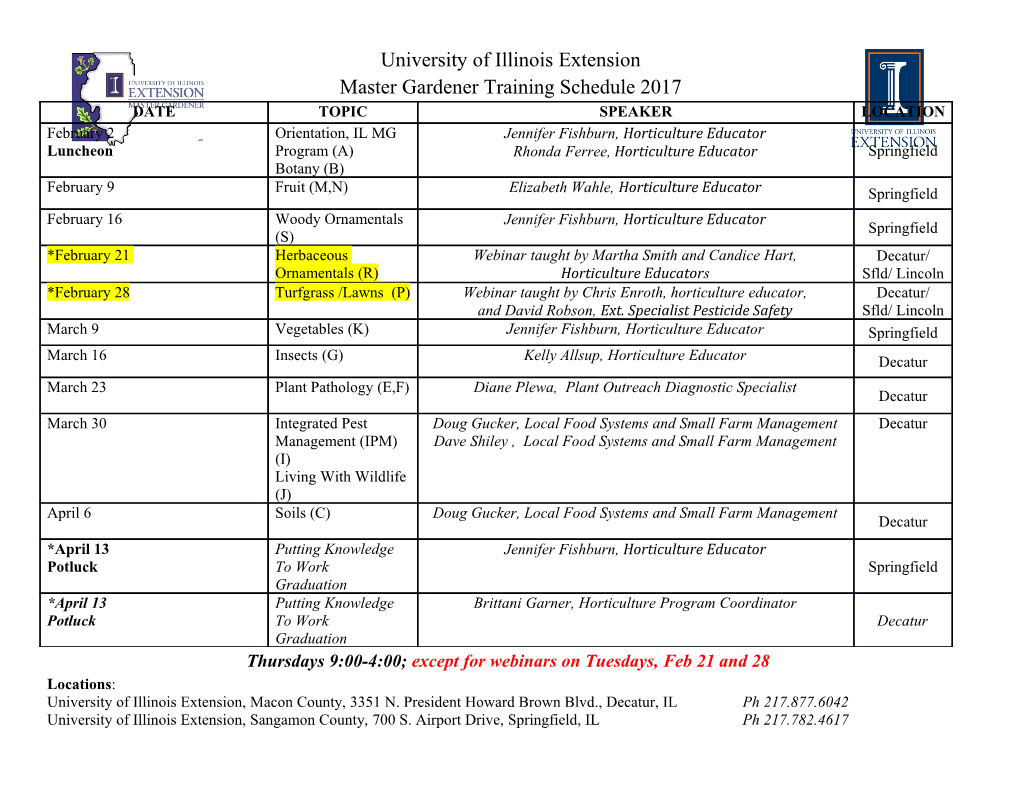
Preamble After more than 20 years, we finally understand how all problems of CD audio are originating from CD's analog and mechanical aspects. Analog? Philips and Sony and all their followers always told us that CD is digital and has perfect sound forever! If this is/was true, why do all kind of tweaks in the analog domain make such great differences in the perception of the reproduced music? Stop Light applied on the edge of a CD; circumcising the edge of the disc; various clamping techniques; all kind of polishing compounds and fluids; various power supply enhancements; demagnetizing and of course the subject of this article, making a completely new copy of a disc - all these adjustments are 100% analog and most are actually mechanical. To get a better understanding of how and why these tweaks and improvements work, we must take a closer look at CD and its inner workings. Analog The inventors of the CD did an incredible job. The amount of work that has been put into the creation of this medium is enormous. It is said that the error correction mechanism took 10 years of research alone. Many people believe the result of all this effort is a digital representation of the analog waveform. Simply put, this assumes that all the 1s and 0s on the disc result in the original waveform when converted through a DAC. Any dropouts due to minor scratches are fully recovered by the error correction system. Only the worst cases create audible hiccups when a scratch is too big. Unfortunately, this image of the workings of CD is not entirely correct. The CD only carries a part of the digitized analog waveform and even that part is only a representation of the actual waveform. First, only the amplitude information is encoded on the CD. The other part of what makes up a waveform -- the time domain information -- is not represented. When you see a normal sine wave, the vertical axis represents amplitude or power while the horizontal axis represents time. Together, the information of time and amplitude creates a tone. With a CD, the time portion is considered to be a constant. A clock provides timing cues at a constant rate. The same clock frequency is used for disc recording and playback. With each clock 'tick', the CD player should read one sample. This idea is perfectly acceptable in a perfect world. Alas, we don't live in a perfect world - but let's assume we do for a moment. CDs encode amplitude information in pits. Contrary to popular belief, a pit does not represent a digital 1. CDs work on such a small scale that a string of ever-changing 0-to-1 and 1-to-0 transitions would be nearly impossible to read correctly. What happens when a word ends with a 1 and the next starts with a 1? Where does one sample end and the next begin? To counter this problem, the engineers at Philips and Sony introduced a modulation technique called Eight-to-Fourteen. In EFM, every possible 8-bit word -- the length agreed upon for the RedBook standard and ranging from 0000 0000 to 1111 1111 -- has a 14-bit equivalent. These 14-bit equivalent words are generated such that there are always more than two but less than ten consecutive zeros. The result? Information stored on a CD is never shorter than 3 bits or longer than 11 bits. These pit lengths are called T3 to T11. The transition from pit to flat is now easy to track to represent the amplitude information of a waveform. Like the groove of an LP, CD stores all of its data in a single string. This string of data consists of the already mentioned EFM words in the form of pits and flats plus the so-called sub code. The sub code carries information about the laser location to enable track selection. The Table of Contents or TOC code directs the laser to the correct spot on the disc (we'll see later that 'correct' can vary). Besides the sub code, CD protocol requires a synchronization prompt, which is inserted into the string at various places. This synchronization word helps to regulate the CD player's drive motor. Unlike an LP, a CD does not spin at one constant velocity. As you can imagine, the start of the spiral 'groove' near the hole at the center of the CD is much shorter for one revolution than the end of the groove near the outer edge. RedBook specifications demand constant linear speed. To achieve that, the CD spins faster at the beginning of the spiral track and slows down gradually towards the outer edge. The rotational speed thus varies from 500 to 200 rpm. Back to the representation of the waveform. We have seen how the analog waveform is converted into a bitstream of 1s and 0s and then into EFM words that are translated into pits. In the process of creating a physical CD inside a dust-free clean room, a high-tech laser burns the pits into a layer of photo resist applied to a meticulously cleaned glass plate of 240mm diameter and 6mm thickness. The laser is called a laser beam recorder and is fed by the output of the mastered audio recording. While laser- burning the photo resist on the glass plate to create the spiral track with its 0.6 millionth/meter-wide pits, this beam recorder can burn up to about 2 billion pits. The next step develops the glass disc now called glass master just like a photo by etching away the exposed parts. All manner of laser equipment controls this process because pit depth should be neither too deep nor too shallow to conform to standardized refraction values. After the etching is completed, a process called electroforming deposits first a film of evaporated silver onto the photo resist layer, then adds a coat of nickel atop the now silvered glass master. Next our CD fabricator separates the nickel layer from the glass master and removes any photo resist material which results in the metal master or 'father' from which several positive 'mother' images are generated which lead to further negative impression stampers called 'sons'. Their use depends on the size of a run. A short production run may rely solely on the original father while large-scale duplications use the son clones/copies. The next step injects molten polycarbonate into a stamper to produce a 1.2mm thick disc with a pitted spiral track upon which a 50 to 100nm-thick layer of aluminum, silver or gold is applied to create reflectivity for the laser. This is finished up with a thin protective acrylic layer -- we think far too thin -- which also acts as the label-printing surface. This and not the data side is most vulnerable to scratching and thus signal loss! Let's now put our freshly minted new CD into a player whose task it is to read the representation of the amplitude information of the original waveform at the sample rate of the player's internal clock - the standard 44.1KHz RedBook velocity. From this readout of the pit pattern in conjunction with the clock signal, the player reassembles a 1s and 0s signal that results in an analog squared-off waveform at this intermediate stage [see above]. Each time the waveform crosses the zero line -- every time a pit-to-flat or flat-to-pit transition is encountered -- the player writes a 1 to a buffer. All other samples are 0s. Thus from just a part of the original waveform, the player is able to recreate a very close approximation in digital form. However, the newly created horizontal part of the waveform -- the time data of the clock -- isn't a digital signal at all. The clock is a constant-flow analog signal generated by an analog source, a crystal oscillator. Now this stream of 1s and 0s must be converted to analog so we can hear the music. Several things can and do go wrong during this whole process, from the glass master if generated from DAT tape or CD-R to the glass-mastering machine to the translucent quality of the actual polycarbonate, the quality of the stamper to form accurate pits, to the reflective aluminum layer which may or may not be thick enough or suffer from pin holes. In practice, it is the lack of crisp pit formation in a stamped CD that causes most of the problems. If a clock 'tick' prompts the laser to read the next sample and the wall of that pit isn't interpreted as a wall, the sample isn't misread but read just a little too late. Every transition from pit to flat and flat to pit becomes read as a digital 1. For a purely digital likeness, time delays don't pose any problems since the 1 is properly extracted. During playback, however, you will notice a peculiar harshness often associated with the medium. These offsets in time are called jitter. If we tie up all of the above -- and there are in fact many more issues that influence CDs - we can conclude that all manner of mechanical and external issues can interfere with our musical pleasure of playing back a CD. In hindsight, you might even wonder why this intermediate medium was ever invented. If we had direct digital access to the master recording on the recording engineer's hard disc, we could skip all the format and domain conversions...
Details
-
File Typepdf
-
Upload Time-
-
Content LanguagesEnglish
-
Upload UserAnonymous/Not logged-in
-
File Pages12 Page
-
File Size-