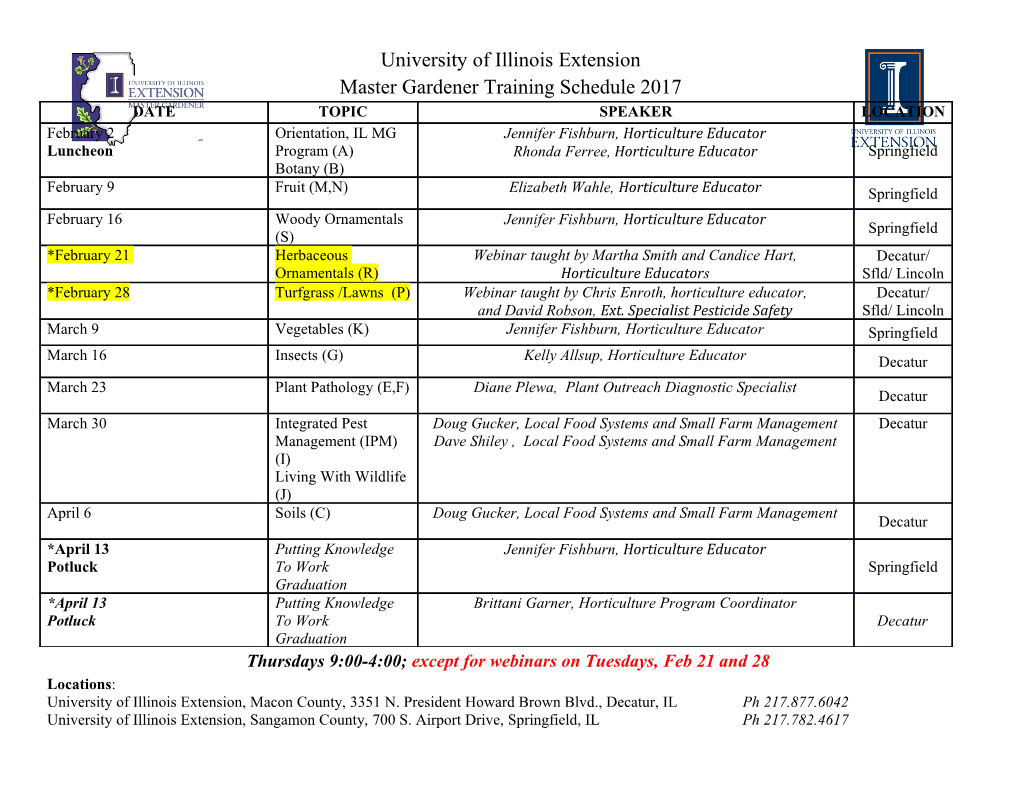
March 3, 1970 D. H. REIGHTER 3,497,951 BUS-BAR JOINTS AND METHODS FOR PRODUCING THEM Filed Nov. 1, 1967 2 Sheets-Sheet 1 s s s s s s S. INVENTOR. Aa2/47 a M72/Ga/724? gal//22 A1227t/A-1M2A ZMM/2/ BY 4724%, 174aeg2%a arzy 27,7264/ay? March 3, 1970 D, H. REIGHTER 3,497,951 BUS-BAR JOINTS AND METHODS FOR PRODUCING THEM Filed Nov. 1, 1967 2 Sheets-Sheet 2 INVENTOR. A4 v/a A. az/GA/7ZA BY (27teazawe, aaa..e62seaf hazy a 772AM296 3,497,951 United States Patent Office Patented Mar. 3, 1970 2 3,497,951. area of the bolts joining the bus-bars where the pres BUS-BAR JOINTS AND METHODS FOR Sure is in excess of that in other parts of the joint. Thus, PRODUCING THEM since there is such a relatively small contact area car Dayid H. Reighter, Roslyn, Pa., assignor, by mesne as rying the electrical load of the bus-bar, the normal signments to I-T-E Imperial Corporation, Philadelphia, rises in temperature which are experienced in ordinary Pa., a corporation of Delaware 5 operation of bus-bars are considerably amplified in Filed Nov. 1, 1967, Ser. No. 679,806 these local spots, giving rise to a deleterious effect upon int, CE. H.Or 43/00 the mechanical quality of the bus-bar joint which is U.S. C. 29-628 3 Claims reflected in an even greater deterioration of electrical conductivity, thus initiating a cycle of deterioration O which, under high load operation conditions, may lead ABSTRACT OF THE DISCLOSURE to the complete breakdown of the joint. Bus-bar ends which are later to be joined in a bus A second disadvantage of the silver coating is that bar assembly, are coated with a low melting solder. under normal atmospheric conditions the silver will be Upon assembly of the bus-bar system the pressure of 5 tarnished by the formation of a thin film of silver sul adjacent bus-bars upon each other, caused by the as fide. Since thin films of silver sulfide have substantially Sembling bolts, is sufficient to maintain electrical con the same electrical conductivity as silver itself under tact. Such a system, however, has a comparatively high most circumstances, this tarnish does not affect the oper resistance, and as the electrical load upon the bus-bar ation of the joint. However, where the bus-bar system increases, the temperature of the joint is raised, causing 20 is installed in a location containing a high percentage the solder to melt thus producing a fused joint. This of Sulfur in the atmosphere, a situation not at all un joint possesses the desirable characteristics of low elec common in many chemical processes, the amount of trical resistance, and low mechanical strength. sulfide formed by the atmosphere may reduce seriously the quality of the electrical contact within the joint. 25 Hence, it was found desirable to search for a means FIELD OF THE INVENTION of joining bus-bars, by a different method, which would This invention relates to a method of providing good still meet the specifications of the NEMA for a silver electrical contact between sections of electrical bus surface or equivalent joint which does not have the S. problems associated with silver-to-silver joints, particu 30 larly silver-to-silver joints on aluminum backing, the DESCRIPTION OF THE PRIOR ART NEMA standards being those accepted in the industry. In assembling electrical bus-runs, it is necessary to A method of providing an efficient connection for provide bus-bars which will carry a substantial load of high density currents is disclosed in NASA Technical current, without a great rise in temperature during oper Brief No. 67-10140 published in May 1967, and avail ation and also to provide a simple method of joining able from the Clearing House for Federal Scientific and the bus-bars to each other, in such a way that the bus Technical Information, Springfield, Virginia 22151. In runs may be readily assembled and good electrical con the method disclosed in this publication, electrical con tact achieved between the bars. Since it is customary tact is provided between stainless steel tubing and a bus in this field of manufacture to assemble bus-runs for bar by means of a lead solder film placed between the testing in the location of manufacture, followed by 40 stainless steel tube and the bus-bar. Electrical contact disassembly and reassembly in the field, it is necessary is obtained by clamping the bus-bar upon the tube in to provide a means of jointing wherein the joints are such a manner that the lead solder film flows about readily broken apart, but which at the same time exhibit the tube to produce an essentially 100% contact Sur all of the electrical characteristics of the finally as face efficiency. This method, however, would not be sembled system. satisfactory in the field of bus-bar jointing since the Most of the bus-bars utilized in the industry are pressures required to cold flow lead solder would be made of copper or aluminum. such as to physically deform the aluminum bus-bar. The classical method of joining bus-bars has beers Furthermore, it will be noted that in the NASA method to silverplate the area to be joined followed by the the problem to be solved is directed to a relatively small bolting together of the bus-bars. It is relatively simple contact area, whereas in a bus-bar joint, it is desirable to to silverplate copper bars, however, the process of plat obtain electrical contact over as large an area as poS ing aluminum is a multi-stage procedure which does not sible. always give rise to reliable results. In this process, SUMMARY OF THE INVENTION known as the "Zincate process,' the aluminum bus bar is coated with zinc, the zinc coating removed, a 55 In the process of the present invention the contact sur second zinc coating applied, upon which is laid a coat face of a bus-bar is coated with a low melting solder in ing of copper, followed by a silverplating in the usual such a manner that under ordinary operating conditions, manner. Due to the rise in price of copper, it has that is to say under low load conditions, the mere clamp been found desirable to make the bus-bars out of ing together of two bus-bars provides sufficient electrical aluminum rather than copper, where such a proceed 60 contact. However, under high load conditions, under ing is feasible within the general concept of the bus which the bus-bar will normally warm up, the solder will bar system. Hence, a way has been sought to avoid melt, flow across the entire surface of the joint by capil the well-known problems of silver coating aluminum lary action and thus form a complete and efficient elec surface. trical contact. As a result of this sudden and highly in There are other problems associated with the silver 65 creased electrical contact, the total resistance of the bus coated system. Although silver-to-silver provides an bar system drops, hence, the temperature will also fall excellent electrical conducting surface, such conduc whereupon the solder will freeze, yielding a joint which tivity is only provided where the metals are in actual is highly satisfactory electrically and still possesses mod contact. Thus, it has been found that in a bus-bar erate mechanical strength. On the other hand, if the joint, the desired silver-to-silver contact is not made 70 level of current in the bus-bar system is such that even the over the entire area of the silver-to-silver interface of drop in resistance of the system caused by the aforemen the contacting bus-bars, but only in the immediate tioned improved contact is not sufficient for the system 3,497,951 3 4. to cool down to the extent necessary to freeze the solder, operating conditions above ambient temperature, a solder excellent electrical contact is still maintained since the should be chosen which melts approximately within this capillary action of the adjacent bus-bar surfaces will be range. Thus, a suitable melting range would be from sufficient to maintain the solder as a film between them. about 45 C. to about 100° C. Any solder composition Low mechanical strength is an advantage since on the which falls within this approximate temperature range one hand the mechanical juxtaposition of the members may be employed in the process of this invention. How of the bus-bar system is not dependent solely upon the ever, it is desirable to exclude those low melting solders connecting joints and yet when it is desired to disas which include mercury in their composition. The reason semble the system, upon unbolting, the surfaces may be for this exclusion is not inoperability, but rather that such readily pried apart with a prying tool and upon reassem solders at temperatures above their melting point give bling in the same or another system will, under high cur O rise to mercury vapour, the presence of which is highly rent conditions, again yield the desired soldered joint. undesirable. This so-called “auto soldering system” is highly desir Among those solders suitable for the purposes of this able since under normal assembly conditions of a bus-bar invention are eutectic solders such as Cerrollow-117, Cer System it is not practical to use conventional soldering 5 rollow-136, and Cerrobend which have a melting point of means, neither is it desirable to weld together sections of 47 C., 58 C., and 70° C.
Details
-
File Typepdf
-
Upload Time-
-
Content LanguagesEnglish
-
Upload UserAnonymous/Not logged-in
-
File Pages5 Page
-
File Size-