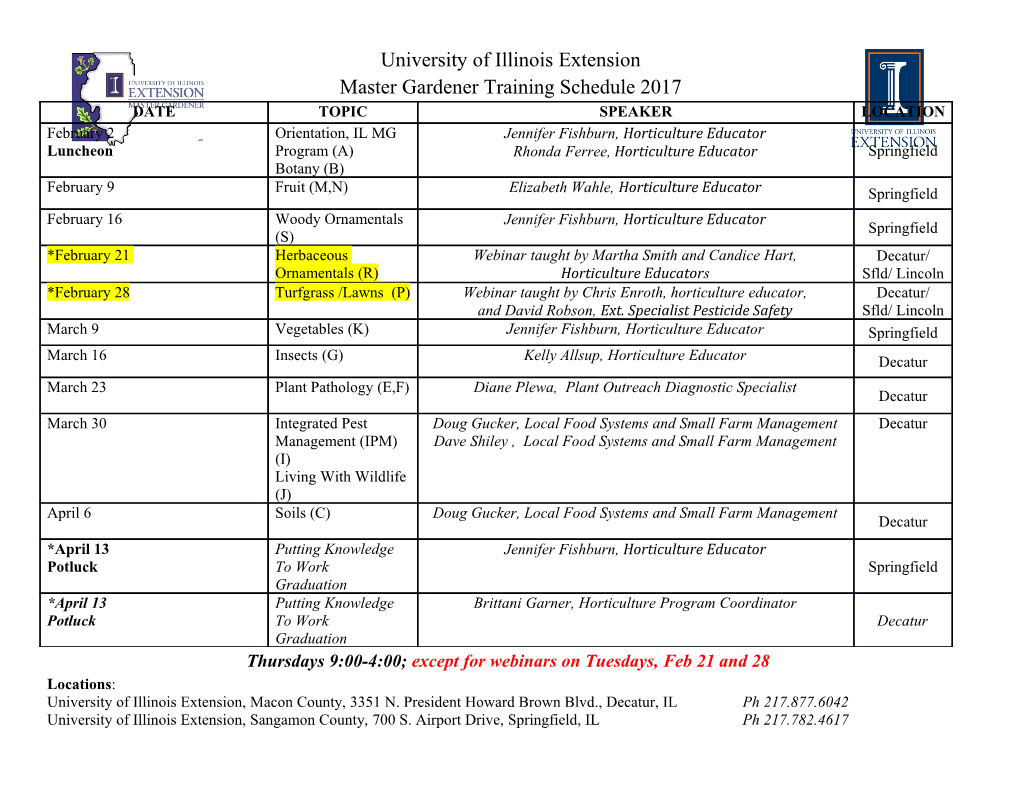
Solid Oxide Fuel Cells by Subhash C. Singhal olid oxide fuel cells (SOFCs) offer a clean, low-pollution technology Sto electrochemically generate electricity at high efficiencies; since their efficiencies are not limited by the Carnot cycle of a heat engine.1-3 These fuel cells provide many advantages over traditional energy conversion systems including high efficiency, reliability, modularity, fuel adaptability, and very low levels of NOx and SOx emissions. Quiet, vibration-free operation of SOFCs also eliminates noise usually associated with conventional power generation systems. Up until about six years ago, SOFCs were being developed for operation primarily in the temperature range of 900 to 1000oC; in addition to the capability of internally reforming hydrocarbon fuels (e.g., natural gas), such high temperature SOFCs provide high quality exhaust heat for cogeneration, and when pressurized, can be integrated with a gas turbine to further increase the overall efficiency of the power system. However, reduction of the SOFC FIG. 1. Operating principle of a solid oxide fuel cell. operating temperature by 200oC or more allows use of a broader set of materials, is less-demanding on the seals cell functions; adequate chemical and electronic conductivity and dimensional and the balance-of-plant components, structural stability at high temperatures change due to the formation of oxygen simplifies thermal management, aids encountered during cell operation as vacancies and the associated reaction of in faster start up and cool down, and well as during cell fabrication; minimal Ce4+ to Ce3+. Operation at temperatures results in less degradation of cell and reactivity and interdiffusion among below about 600oC overcomes this stack components. Because of these different components; and matching problem, and ceria based materials are advantages, activity in the development thermal expansion among different successfully being used as electrolyte of SOFCs capable of operating in the components. in SOFCs by Ceres Power Limited (UK). temperature range of 650 to 800oC has In addition to the traditionally used increased dramatically in the last few Materials and Cell Designs fluorite structure oxides such as zirconia years. However, at lower temperatures, and ceria, perovskite structure (ABO3) electrolyte conductivity and electrode also offers an opportunity to develop Yttria-doped zirconia (YSZ) remains kinetics decrease significantly; oxide ion conducting electrolytes the most widely used material for the to overcome these drawbacks, by selectively substituting either the electrolyte in SOFCs because of its alternative cell materials and designs A or B ion by isovalent or aliovalent sufficient ionic conductivity, chemical are being extensively investigated. cations. (La,Sr)(Mg,Ga)O (LSMG)4,5 stability, and mechanical strength. 3 An SOFC essentially consists of two has attracted attention as an electrolyte The only drawback of stabilized ZrO porous electrodes separated by a dense, 2 since its discovery. LSMG electrolytes, is the low ionic conductivity in the oxide ion conducting electrolyte. The however, have two drawbacks: uncertain lower cell operation temperature regime operating principle of such a cell is cost of gallium, and uncertain chemical (below about 750oC). Two solutions illustrated in Fig. 1. Oxygen supplied at and mechanical stability of LSMG. In that have been tried to resolve this the cathode (air electrode) reacts with spite of these drawbacks, Mitsubishi problem are to decrease the thickness incoming electrons from the external Materials Corporation (Japan) is using of the YSZ electrolyte and to find other circuit to form oxide ions, which LSMG as the electrolyte in its SOFCs acceptors to replace Y. Scandia-doped migrate to the anode (fuel electrode) and has successfully built and tested up zirconia has higher conductivity than through the oxide ion conducting to 10 kW size SOFC power systems. YSZ but high cost of scandium and electrolyte. At the anode, oxide ions The oxidant gas is air or oxygen at the detrimental ageing effects in scandia- combine with H (and/or CO) in the fuel SOFC cathode, and the electrochemical 2 doped ZrO make it less attractive in to form H O (and/or CO ), liberating 2 reduction of O requires a series of 2 2 commercializing SOFCs. Gadolinium- or 2 electrons. Electrons (electricity) elementary reactions and involves the samarium-doped CeO materials possess flow from the anode through the 2 transfer of multiple electrons. The SOFC higher oxide ion conductivity (e.g., external circuit to the cathode. The cathode must meet the requirements Ce Gd O : 0.025 Ω-1•cm-1 at 600°C) materials for the cell components are 0.9 0.1 1.95 of high catalytic activity for oxygen compared to zirconia based materials selected based on suitable electrical molecule dissociation and oxygen (< 0.005 Ω-1•cm-1). However, CeO based conducting properties required of these 2 reduction, high electronic conductivity, materials, under reducing conditions at components to perform their intended chemical and dimensional stability high temperatures, exhibit significant The Electrochemical Society Interface • Winter 2007 41 Singhal (continued from previous page) the fuel, electronically conducting, and sulphur, hydrocarbon and/or redox must have sufficient porosity to allow the tolerance are counterbalanced by other in environments encountered during transport of the fuel to and the transport limitations (such as the difficulty of cell fabrication and cell operation, of the products of fuel oxidation away integrating such materials with existing thermal expansion match with other from the electrolyte/anode interface cell and stack fabrication processes and cell components, and compatibility and where the fuel oxidation reaction takes materials). Copper cermet anodes have 7 minimum reactivity with the electrolyte place. The other requirements include also been proposed for intermediate- o and the interconnection. Finally, the matching of its thermal expansion temperature (< 800 C) SOFCs intended cathode must have a stable, porous coefficient with that of the electrolyte to operate directly on hydrocarbon 7 microstructure so that gaseous oxygen and interconnect; integrity of porosity fuels without prior reformation, can readily diffuse through the cathode for gas permeation; chemical stability but the lack of catalytic activity to the cathode/electrolyte interface. with the electrolyte and interconnect; for oxidation of fuel in copper and These stringent electrochemical and and applicability to use with versatile sintering of copper at the cell operating mechanical requirements greatly fuels and impurities. In addition, cost temperatures have limited their use restrict the number of suitable candidate effectiveness is always a factor for in practical SOFCs. Ceramic anodes materials. Conducting perovskites commercialization. Ni-YSZ cermets such as doped perovskites, (La,Sr)TiO3, are the preferred cathode materials. are the most commonly used anode (La,Sr)CrO3, with addition of CeO2 materials for SOFCs. Ni is an excellent have also been investigated as anodes,7 Lanthanum manganite (LaMnO3), which, when substituted with low- catalyst for fuel oxidation; however, but they suffer from higher electronic valence elements such as Ca or Sr, it possesses a high thermal expansion resistance. -6 has good p-type electronic conduction coefficient (13.4 × 10 /°C), and exhibits Since a single cell only produces due to the formation of large amount coarsening of microstructure due to voltage less than 1 V and power 4+ metal aggregation through grain growth around 1 W/cm2, many cells are of Mn . Moreover, doped LaMnO3 possesses adequate electrocatalytic at cell operation temperatures. YSZ in electrically connected together in a activity, a reasonable thermal expansion the anode constrains Ni aggregation cell stack to obtain higher voltage match to YSZ, and stability in the and prevents sintering of the nickel and power. To connect multiple cells SOFC cathode operating environment. particles, decreases the effective thermal together, an interconnection is used in For SOFCs operating at substantially expansion coefficient bringing it closer SOFC stacks. The requirements of the lower temperatures, such as 650- to that of the electrolyte, and provides interconnection are the most severe of 800°C, alternative cathode materials, better adhesion of the anode with the all cell components and include: nearly typically containing transition electrolyte. In the Ni/YSZ cermet anode, 100 percent electronic conductivity; metals such as Co, Fe, and/or Ni on nickel has dual roles of the catalyst for stability in both oxidizing and reducing the B site, have been developed and hydrogen oxidation and the electrical atmospheres at the cell operating optimized for better performance. In current conductor. In addition, it is also temperature since it is exposed to air (or general, these materials offer higher highly active for the steam reforming oxygen) on the cathode side and fuel oxide ion diffusion rates and exhibit of methane. This catalytic property on the anode side; low permeability faster oxygen reduction kinetics at the is exploited in the so-called internal for oxygen and hydrogen to minimize cathode/electrolyte interface compared reforming SOFCs that can operate on direct combination of oxidant and with lanthanum manganite. However, fuels composed of mixtures of methane fuel during cell operation; a thermal the thermal expansion coefficient of and water. Although
Details
-
File Typepdf
-
Upload Time-
-
Content LanguagesEnglish
-
Upload UserAnonymous/Not logged-in
-
File Pages4 Page
-
File Size-