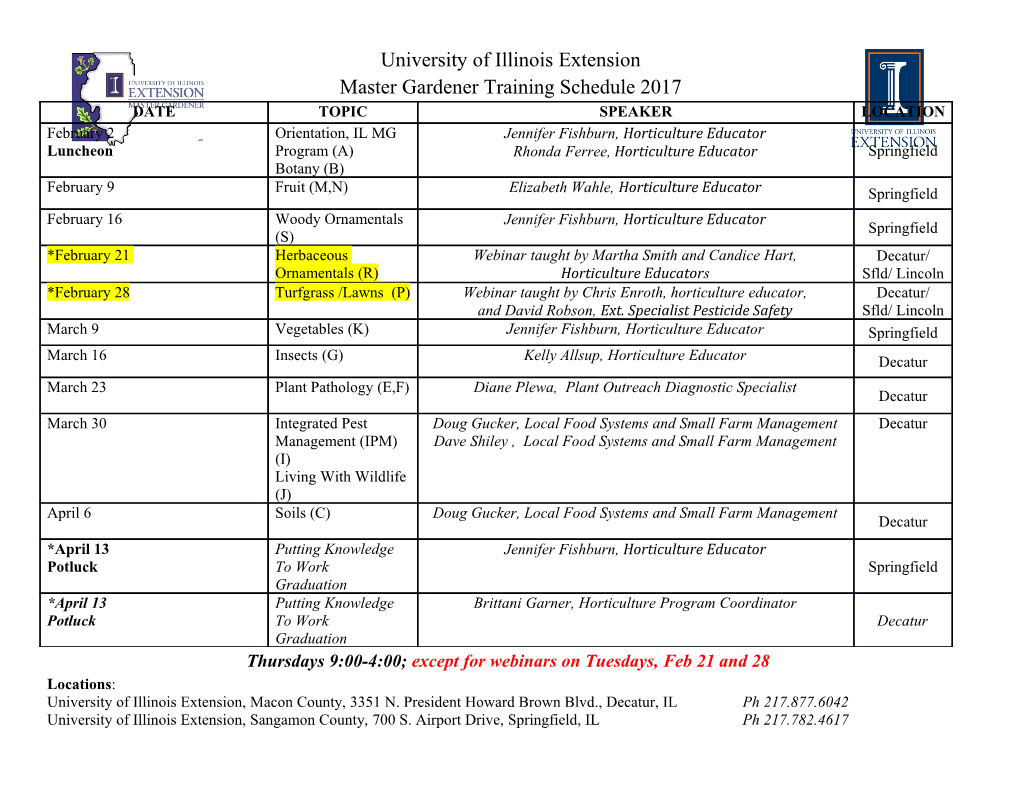
Modeling Temperature Dependence in Marangoni-driven Thin Films by Harrison David Parke Potter Department of Mathematics Duke University Date: Approved: Thomas P. Witelski, Supervisor J. Thomas Beale Anita T. Layton James Nolen Dissertation submitted in partial fulfillment of the requirements for the degree of Doctor of Philosophy in the Department of Mathematics in the Graduate School of Duke University 2015 Abstract Modeling Temperature Dependence in Marangoni-driven Thin Films by Harrison David Parke Potter Department of Mathematics Duke University Date: Approved: Thomas P. Witelski, Supervisor J. Thomas Beale Anita T. Layton James Nolen An abstract of a dissertation submitted in partial fulfillment of the requirements for the degree of Doctor of Philosophy in the Department of Mathematics in the Graduate School of Duke University 2015 Copyright c 2015 by Harrison David Parke Potter All rights reserved except the rights granted by the Creative Commons Attribution-Noncommercial Licence Abstract Thin liquid films are often studied by reducing the Navier-Stokes equations using Reynolds lubrication theory, which leverages a small aspect ratio to yield simpli- fied governing equations. In this dissertation a plate coating application, in which polydimethylsiloxane coats a silicon substrate, is studied using this approach. Ther- mal Marangoni stress drives fluid motion against the resistance of gravity, with the parameter regime being chosen such that these stresses lead to a stable advancing front. Additional localized thermal Marangoni stress is used to control the thin film; in particular, coating thickness is modulated through the intensity of such localized forcing. As thermal effects are central to film dynamics, the dissertation focuses specifically on the effect that incorporating temperature dependence into viscosity, surface tension, and density has on film dynamics and control. Incorporating tem- perature dependence into viscosity, in particular, leads to qualitative changes in film dynamics. A mathematical model is developed in which the temperature dependence of vis- cosity and surface tension is carefully taken into account. This model is then studied through numerical computation of solutions, qualitative analysis, and asymptotic analysis. A thorough comparison is made between the behavior of solutions to the temperature-independent and temperature-dependent models. It is shown that us- ing localized thermal Marangoni stress as a control mechanism is feasible in both models. Among constant steady-state solutions there is a unique such solution in iv the temperature-dependent model, but not in the temperature-independent model, a feature that better reflects the known dynamics of the physical system. The in- teraction of boundary conditions with finite domain size is shown to generate both periodic and finite-time blow-up solutions, with qualitative differences in solution behavior between models. This interaction also accounts for the fact that locally perturbed solutions, which arise when localized thermal Marangoni forcing is too weak to effectively control thin film thickness, exist only for a discrete set of bound- ary heights. Modulating the intensity of localized thermal Marangoni forcing is an effective means of modulating the thickness of a thin film for a plate coating application; however, such control must be initiated before the film reaches the full thickness it would reach in the absence of such localized forcing. This conclusion holds for both the temperature-independent and temperature-dependent mathematical mod- els; furthermore, incorporating temperature dependence into viscosity causes qual- itative changes in solution behavior that better align with known features of the underlying physical system. v To Donna Smith vi Contents Abstract iv List of Tablesx List of Figures xi Acknowledgements xvi 1 Introduction: Historical Context1 1.1 Foundations of Modern Fluid Dynamics................2 1.1.1 History of premodern fluid dynamics..............2 1.1.2 Modern developments......................5 1.2 Thin Liquid Films............................8 1.2.1 Recent viscous thin liquid films research............9 1.2.2 Outline of dissertation...................... 11 2 Development of Mathematical Model 13 2.1 Navier-Stokes Equations......................... 15 2.2 Heat Transfer............................... 21 2.3 Temperature Dependence of Parameters................ 25 2.4 Boundary Conditions........................... 29 2.5 Thin Film Partial Differential Equation................. 33 2.6 Boundary Value Problem......................... 37 2.7 a posteriori Verifications......................... 39 vii 3 Temperature-independent Parameters: β “ 0, Σ “ 0 40 3.1 Temperature-independent Model..................... 41 3.2 M “ 0: Constant Steady-state Solutions................ 42 3.2.1 Lh0 is not self-adjoint....................... 43 3.2.2 Eigenvalues are computed numerically............. 44 3.2.3 Neutral stability......................... 48 3.2.4 Stability analysis......................... 52 3.2.5 Eigenfunction perturbations decay as expected......... 54 3.2.6 M “ 0 conclusion......................... 57 3.3 M ¡ 0: Steady-state Solutions...................... 60 3.3.1 Type II solutions......................... 61 3.3.2 Type I-A solutions........................ 67 3.3.3 Type I-B solutions........................ 78 3.4 M ¡ 0: Non-steady-state Solutions................... 84 3.4.1 Periodic solutions......................... 85 3.4.2 Finite-time blow-up solutions.................. 89 3.4.3 Validity of implication (3.27)................... 92 3.5 Conclusion................................. 95 4 Temperature-dependent Parameters: β “ 1:9 ˆ 10´3, Σ “ 3 ˆ 10´4 97 4.1 Temperature-dependent Model...................... 98 4.2 M “ 0: A Unique Constant Steady-state Solution........... 99 4.3 M ¡ 0: Steady-state Solutions...................... 107 4.3.1 Type II solutions......................... 108 4.3.2 Type I-B solutions........................ 116 viii 4.3.3 Type I-A solutions........................ 120 4.4 M ¡ 0: Non-steady-state Solutions................... 125 4.4.1 Periodic solutions......................... 125 4.4.2 Finite-time blow-up solutions.................. 128 4.5 Conclusion................................. 130 5 Conclusion: Future Directions for Research 132 5.1 Coating Applications........................... 132 5.2 Boundary Conditions........................... 133 A Parameter Values 135 A.1 Dependence Upon ` of Scales and Parameters............. 135 A.2 Incorporating `-Dependence Into a posteriori Verifications...... 139 A.3 Fixing ` and Related Parameters.................... 140 B Numerical Methods 142 B.1 Computing PDE Solutions........................ 142 B.2 Computing ODE Solutions and Eigenvalues.............. 146 B.3 Implementation Details.......................... 148 Bibliography 150 Biography 158 ix List of Tables 3.1 Eigenvalue λ with largest real part for each Type I-A solution shown in figure 3.12................................ 72 A.1 Physical properties and scales whose values are fixed......... 136 A.2 Dimensionless parameters whose values are fixed............ 138 A.3 In order to complete the specification of the physical system being studied through the use of our mathematical model we need to specify values for scales and parameters that are related to `. The values given in this table are those that best correspond to a plate-coating application in which PDMS oil covers a silicon substrate........ 141 x List of Figures 2.1 A cross-section of the physical system showing axes, the underlying temperature gradient τ, the localized Marangoni forcing M, gravity ~g, and computational domain r´`; `s................... 15 3.1 Eigenvalues for flat steady-state solution with h0 “ 0:4, ` “ 10. Con- vergence of eigenvalues with largest real parts is confirmed....... 45 3.2 Eigenvalues for flat steady-state solutions for (a) ` “ 10 and (b) ` “ 50 with h0 “ 0:4 and identical ∆x. Increasing ` leads to slower conver- gence and attendant difficulties in resolving eigenvalues......... 47 3.3 Shape of spectrum for ` P t10; 30; 50u with h0 “ 0:4 and ∆x “ 0:25.. 48 3.4 (a) Rerλs and (b) pairs of Imrλs for those eigenvalues with the 2 largest nonzero Rerλs for ` “ 10, Nx “ 400, and h0 P t0:001; 0:002;:::; 1:200u. Convergence is poor for h0 P t0:025; 0:026;:::; 0:199u. Numerically, 2 0 has multiplicity 1 for every h0 ‰ 3 ................... 53 3.5 Eigenvalue calculation is verified by determining rate of exponential ´3 decay at the right boundary for δ “ 10 with h0 “ 0:4, ` “ 10, Nx “ 400. The slope is the real part of the nonzero eigenvalue with largest real part.............................. 57 3.6 Eigenfunction calculation is verified through (a) direct calculation of perturbation decay and (b) verification of oscillatory envelopes when adjusted for exponential decay as given by (3.24)............ 58 3.7 Time series from flat initial condition h0 “ 0:4 with ` “ 10, Nx “ 400 for M “ 1:6. Dashed lines indicate both the flat initial condition and the final film profile. Evolution to a Type II steady-state solution is shown. At t « 60 a transient profile reminiscent of a Type I-B solution forms. This slowly evolves to the final Type II solution, which forms at t « 770.................................. 62 xi 3.8 Type II solutions for M P t0:1; 0:2;:::; 1:6u with ` “ 10, Nx “ 400. Solutions were obtained by letting PDE (3.1) evolve from (3.28).... 63 ´5 3.9 Type II solutions for M P t1; 2; 4; 8; 16uˆ10 with ` “ 10, Nx “ 400. Solutions were obtained
Details
-
File Typepdf
-
Upload Time-
-
Content LanguagesEnglish
-
Upload UserAnonymous/Not logged-in
-
File Pages175 Page
-
File Size-