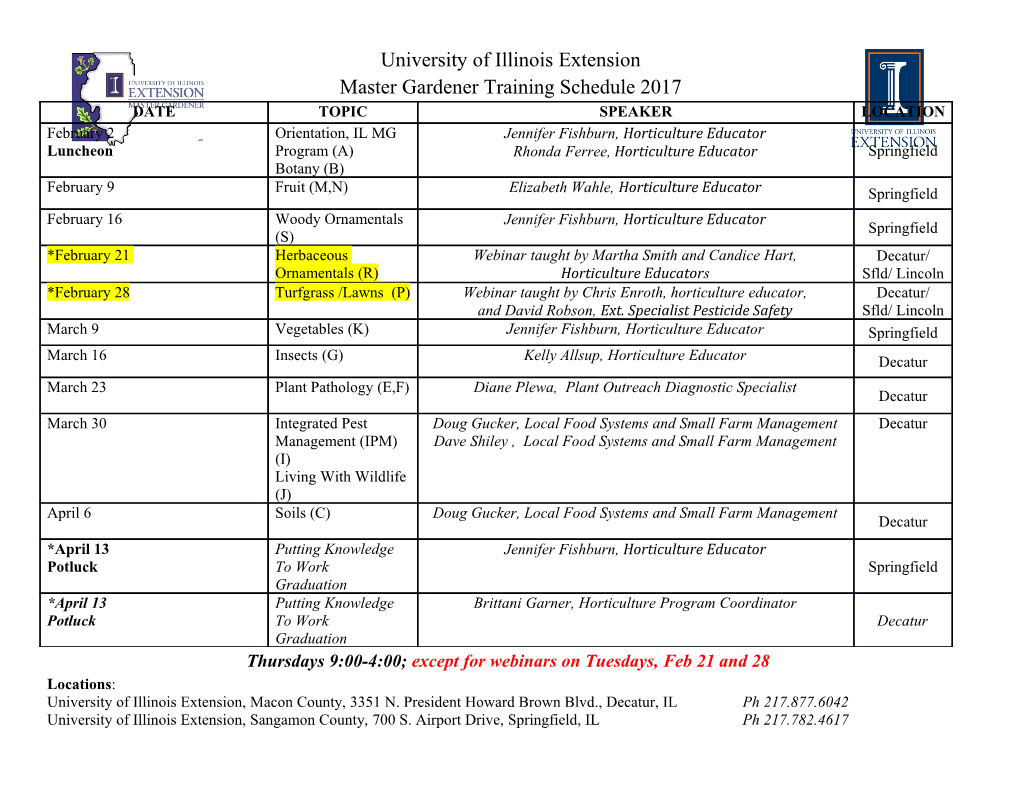
MANAGING QUALITY in GRAPHIC COMMUNICATION G.A. RIVERA Managing Quality in Graphic Communication: Lean Six Sigma Methodologies and Metrics for the Graphic Communication Indus- try Copyright © 2019 by G.A. Rivera All rights reserved. This book or any portion thereof may not be reproduced or used in any manner whatsoever without the express written permission of the publisher except for the use of brief quota- tions in a book review. Printed in the United States of America Third Edition, December 2019 ISBN PENDING Published by Certified Freaken Genuis Productions [email protected] Preface In 2010, my journey in managing for quality officially began. Attending a color certification seminar for large national printers, I was taken-aback that I was the only “printer” in a class full of IT employees with no print- ing experience. It appeared that print organizations were deferring the responsibility for quality management to computer engineers rather than print production employees. Call me old-school, but I would assert that the best people to manage quality in the graphic communication industry are the people who actually run the equipment, manage the technology, and respond to the myriad of problems that occur daily in the logistics of graphic communication. As the GRC industry becomes more reliant on digital technology, it is im- perative that our processes be defect-free and able to adapt to the changing needs of our customers. No longer are were merely designers or printers; we are engineers of technology and as such, we need to learn how to man- age for quality by thinking like an engineer. Since the 1980s, the quality management system, Lean Six Sigma, has transformed manufacturing and service organizations into world class examples of operational efficiency. Having filtered hundreds of Lean Six Sigma tools and methodologies, herein are those I consider most useful for improving and maximizing efficiencies as well as implementing GRC improvement and opportunity projects. While I am a printer by trade, the topics and tools covered in this publica- tion can be applied to any graphic communication segment – UX/UI, App development, offset, heat-set, in-plant, packaging, electronic printing, etc. The overarching methodology employed throughout this publication is the Define-Measure-Analyze-Improve-Control (DMAIC) problem-solving tool of Lean Six Sigma. Ultimately, we want to get to the place where this is our default methodology. In order to effectively manage for quality, we must be able to address and answer the following questions: • What evidence is there that a problem exists? • Can we identify and articulate what the problem is? • What is the cause of the problem? • How do we propose to solve the problem and how will we test our solution? • How do we prevent the problem from reoccurring? The chapter outline for this book follows a linear progression in theMan - aging for Quality in Graphic Communication class I teach at Cal Poly, San Luis Obispo. Students will cover and apply most of the methodologies and tool throughout the quarter. Obviously, casual readers are free to skip to tools and methodologies that most interest them. I wish to acknowledge and thank Dr. Jill Speece from Business Excellence Enterprise, Templeton CA., and Dr. Malcolm Kief from Cal Poly, San Luis Obispo CA., for their instruction, mentorship, and friendship in my Lean Six Sigma journey. I would also like to recognize my wife and editor of 23 years, Candace, whose patience, support, and sacrifice I cannot repay. For those who wish to dig deeper, there are a number of excellent resources included in the bibliography that will help you reach the next level in your understanding and competency of Lean Six Sigma. Table of Contents Chapter 1 The Culture of Quality........................................................................ 1 What does Six Sigma Mean?............................................... 6 Companies that use Lean Six Sigma.................................. 6 The Seven Total Quality Tools: 1) Process Mapping/Flowchart............................. 8 2) Fishbone Diagram - Why/Why Diagram...... 8 3) Process Capability Study (PCS)....................... 8 4) Pareto Chart....................................................... 8 5) Scatter Plot/Regression Analysis..................... 8 6) Control (Process Behavior) Charts................. 8 7) Check Sheet........................................................ 8 Case Study: The Diva’s Pen.................................................. 9 Chapter 2 History of Quality, Quality Defined................................................. 10 A Very Brief Overview of Quality...................................... 12 10,000 BC to 600 AD........................................................... 12 Middle Age/Dark Ages – 600 AD to 1400 AD................. 13 Age of Enlightenment- 1600s to 1800s.............................. 15 Early 20th Century............................................................... 16 Theory X................................................................................ 18 Theory Y................................................................................. 19 Mid-20th Century................................................................. 19 The Evolution of Managing for Quality............................. 22 Life Behind the Quality Levee............................................. 23 Case Study: The General Motors Ignition Key Recall...... 24 Chapter 3 Products & Services, Defects and the VOC..................................... 27 Voluntary Obsolescence....................................................... 28 Involuntary Obsolescence.................................................... 28 Voice of the Customer (VOC)............................................. 29 Nariaki Kana’s Three Classes of Customer Needs............ 30 Voice of the Process (VOP).................................................. 32 Voice of the Business (VOB)................................................ 32 Voice of the Employee (VOE).............................................. 32 Voice of the Stakeholder (VOS)........................................... 32 Voice of the Department (VOD)......................................... 32 3 Defective vs. Defects............................................................. 34 Fitness for Use....................................................................... 35 Freedom of Deficiency Formula (FOD)............................ 35 Product and Service Fitness for Use Metric (PSFU)....... 36 Product Dimensions............................................................ 36 Service Dimensions............................................................. 37 Case Study: iPhone 4.......................................................... 41 Case Study: The Billion Dollar Class 1 Defect................... 42 Case Study: How Not To Respond to a Quality Crisis..... 43 Chapter 4 The Quality Gurus.............................................................................. 45 Philip Crosby........................................................................ 45 Crosby’s Four Absolutes...................................................... 45 Complete Transaction Rating (CTR)................................ 46 CTR Formula....................................................................... 50 Crosby’s Maturity Grid....................................................... 52 Stage 1: Uncertainty.............................................. 53 Stage 2: Awakening............................................... 53 Stage 3: Enlightenment........................................ 55 Stage 4: Wisdom..................................................... 57 Stage 5: Certainty................................................... 57 W. Edward Deming (1900-1993)..................................... 58 Deming Chain Reaction................................................... 58 Demings 14 Points............................................................ 59-66 Deming’s Seven Deadly Sins of Management................ 67 Deming’s System of Profound Knowledge..................... 67 Appreciation for the System.............................. 67 Theory of Knowledge......................................... 68 Psychology........................................................... 70 Understanding Variation................................... 70 Types of Special Cause Variation................ 73 Major Causes of Special Cause Variation.. 74 Joseph Juran....................................................................... 76 Juran’s Quality Improvement........................................... 77 Juran’s Trilogy.................................................................... 77 Genichi Taguchi................................................................ 79 Sakichi Toyoda, Kiichiro Toyoda.................................... 80 Walter Shewhart................................................................ 82 Case Study: The Hubble Space Telescope...................... 83 Case Study: Managing Variation................................... 83 4 Chapter 5 TPS and Lean Methodology for Improvement................................ 85 TPS and Lean Goals.............................................................. 85 TPS and Lean Improvement Activities.............................. 86 Kanban/Constraints.............................................................. 90 Pull System............................................................................. 93 Work Cell..............................................................................
Details
-
File Typepdf
-
Upload Time-
-
Content LanguagesEnglish
-
Upload UserAnonymous/Not logged-in
-
File Pages232 Page
-
File Size-