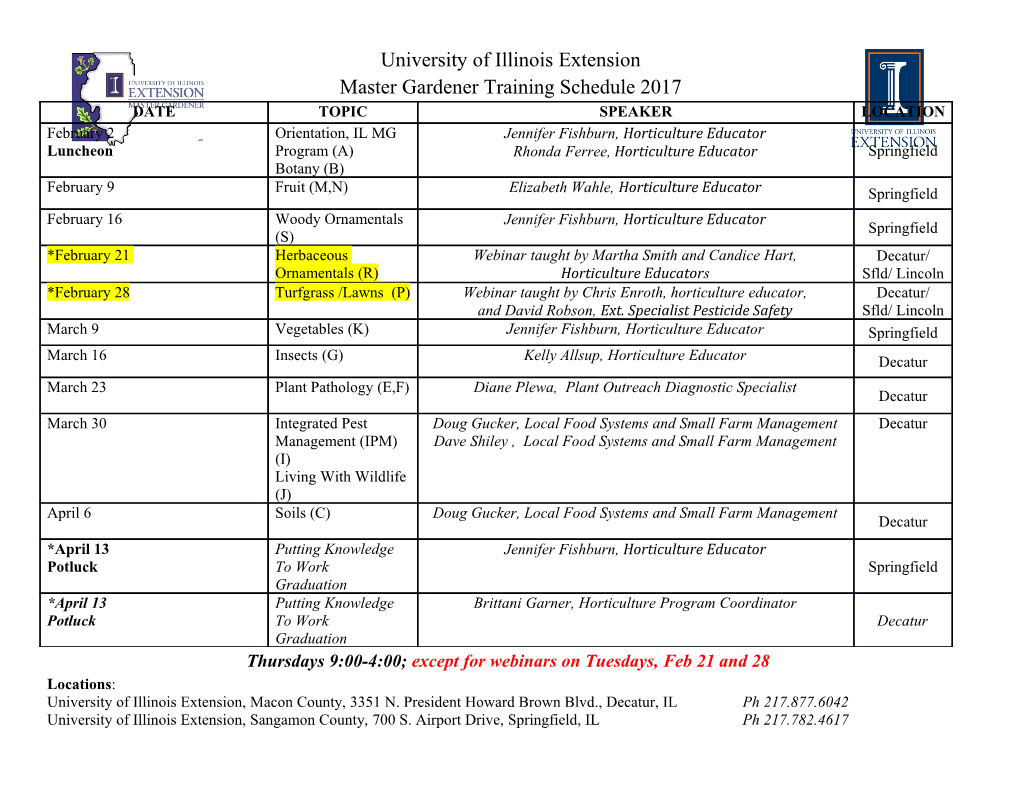
NASA Contractor Report 198531 rJ Chemical Microthruster Options Wim de Groot and Steve O1eson NYMA, Inc. Brook Park, Ohio October 1996 Prepared for Lewis Research Center Under Contract NAS3-27186 National Aeronautics and Space Administration Trade names or manufacmre_" names are used in this relx_ for identification only. This usage does not constitute an official endorsement, either expressed or implied, by the National Aeronautics and Space Admini_ation. Chemical Microthruster Options Wim de Groot° and Steve Oleson_ NYMA, Inc., Engineering Services Division Brookpark, OH Abstract gas jet. It typically consists of nitrogen pressurized to approximately 21 MPa and, Chemical propulsion systems with potential depending on the thrust level, provides a application to microsatellites are classified maximum specific impulse (Isp)of 76 s in a blowdown mode. by propellant phase, i.e. gas, liquid, or solid. Four promising concepts are selected based An excellent review of the status of on performance, weight, size, cost, and reliability. The selected concepts, in varying microthrust technology in the mid 60s was stages of development, are advanced given by Suthedand and Maes. 1 Some of the technology items have since fallen out monopropellants, tridyne TM, electrolysis, and of favor, such as radio isotope heating of solid gas generator propulsion. Tridyne TM the working fluid to enhance thruster and electrolysis propulsion are compared vs. existing cold gas and monopropellant performance. Other technologies, not sufficiently developed for serious systems for selected microsatellite consideration at the time, could present missions. Electrolysis is shown to provide a attractive choices for some missions. significant weight advantage over Among such thrusters are gas-solid hybrid monopropellant propulsion for an orbit thrusters and gas generator type thrusters. transfer and plane change mission. Tridyne TM is shown to provide a significant The term microthrust refers to the thrust advantage over cold gas thrusters for orbit level and not to the physical size of the trimming and spacecraft separation. thruster. Typically,. rockets with a thrust between 10" and 10 N fall within this class. Introduction Depending on the type of energy that is supplied to provide the thrust, The desire to reduce the size and weight of microthrusters can be classified as satellites, especially those planned for chemical, electrical, or electro-chemical. future NASA missions, creates a renewed interest in microthrusters for trajectory Recent developments in electronics and corrections and attitude control. Previously, energy storage have made the application the most important parameters in the choice of electric thrusters, with their high specific of microthruster type were the performance impulse, more attractive in the microthrust and reliability. With the current trend toward region.2 In many applications where high small inexpensive satellites, however, cost, impulse bits are required or where electric size, and weight have been added as dominant considerations. Both reliability power is scarce or not available (missions to the outer solar system), chemical systems improvement and reduction in size, weight, are an attractive option. This paper only and cost can be accomplished by means of covers the chemical class. Electrolysis is reduced system complexity. These included because the nature of the energy enhancements, however, often occur at the provided to the working fluid to generate expense of performance. A standard simple thrust is chemical. system for microthrust propulsion is the cold "Senior Propulsion Specialist, Senior Member AIAA # ResearchEngineer,Member AIAA TMTfidyne is a registeredTrademark of Rockwell Intemational/Rocketdyn¢ Division. Chemical microrockets can be classified and thrust level are less important for such variously. The clearest distinction, missions. In a system designed for attitude analogous to that of Suthedand et al., 1is by control, response time becomes more the phase in which the propellant is stored. important. If attitude control needs to be These are referred to as solid, liquid, and provided over a period of several years, a gaseous rockets, as well as some hybrid high total impulse is required favoring a high systems, where the fuel and oxidizer appear specific impulse thruster. This often implies, in different phases. however, that system complexity increases as well as the weight and size, and that In general, solid propellant systems reliability issues become important. represent a minimum system dry weight and complexity as the result of the absence of Propellant phase has been chosen as the high pressure tanks, propellant lines and primary classification for this paper. valves. The need for a thermal source to Problems associated with propellant initiate combustion or decomposition will management systems, such as phase slightly reduce this weight advantage. A separation in the absence of gravity, slosh, disadvantage of solid propellant thrusters is and vaporization, are largely similar across the difficulty in accurately controlling the each class of propellants. A review is given thrust and cycling. of the currently available propulsion options including propellant properties and thruster Vaporizing liquid propellant rockets also do performance characteristics. From the not require high pressure tankage and available systems, four promising concepts propellant lines, but are more complex than for microthrust propulsion are selected for solid propellant rockets because of the need further analysis. Example mission analyses for phase separation between liquids and for two of these concepts, tridyne TM and gas, and, for applications with a lack of electrolysis, has been done. A substantial inertia, the need to restrain the liquid improvement in weight, size, cost, and (slosh). Gaseous systems carry the highest performance over currently available penalty in system weight, but will sometimes commercial propulsion systems is shown. be needed to deliver the response and/or thrust level that the solid and liquid systems Types of microthrust systems lack with great system simplicity. Each propellant class (gas, liquid, solid) All three propellant types produce thrust represents a number of different propulsion based on the same principle. A gas is concepts. In this section, concepts in each generated inside a chamber with sufficient class are summarized, roughly in order of pressure to choke a nozzle. To provide an complexity. The advantages and acceptable Isp, the molecular weight of the disadvantages of each type are listed, gas needs to be sufficiently low for a without details on specific mission significant acceleration in the nozzle. As an applications. Pertinent properties of addition to each of these three systems, an propellants, such as chemical composition, electrical heater can be provided (resistojet) specific density, and product composition to heat up the gas in order to provide a are listed by phase in Table 1. Projected higher acceleration and higher specific performance characteristics for the impulse while adding only slightly to system described propulsion systems are listed in complexity. The heater system requires a Table 2. power supply, which might be prohibitive for specific applications. In order to obtain a more complete comparison of the different concepts, other The propulsion system selection requires a criteria were taken into consideration and detailed analysis of each mission. A mission will be discussed. Some are quantitative, that requires a large AV for trajectory such as duty cycle, pulse response, cost, corrections, for example, will require a and development status. Others are more system that can provide a large total subjective, e.g. safety and reliability and impulse. This clearly favors a higher will not be addressed here. specific impulse thruster. Response time GASEOUSPROPELLANTS the absence of propellant slosh, liquid/gas Cold Gas. A cold gas (nitrogen or helium) is separation problems, and potentially simple stored at high pressure (~21 MPa). A injector design. Disadvantages of the use of regulator brings the pressure down to the gaseous bipropellants in low thrust desired pressure (0.1-1 MPa) after which applications include the poor mixing the gas is fed by means of check valves to efficiency due to short residence time in the a nozzle. The advantages are safety, low combustor, material incompatibility with cost, rapid response, and a simple system oxidizer, and high temperature material with high reliability. Although the thrusters issues,s Mixing problems limit the lower are low in weight, the overall system weight level of thrust that can reliably be obtained will be moderate due to the need for high to 0.1 N. The low propellant density requires pressure tanks and a distributed feed relatively large tankage. As a result, system. The system is volumetrically gaseous bipropellants are limited to inefficient due to the large tankage needed moderate total impulse missions. A higher for gaseous storage. Typical thrust levels degree of complexity than the cold gas range from 0.005 to 250 N. 3 Specific thrusters is inherent and this reduces impulse depends on thrust level and varies reliability. Poor mixing can cause a pulse to from 45 to 75 sec at 295 K for a nozzle area pulse variation in both magnitude and time ratio of 100, due to increasing nozzle losses history of thrust pulses, which is undesirable for decreasing thruster size. This system for many applications.
Details
-
File Typepdf
-
Upload Time-
-
Content LanguagesEnglish
-
Upload UserAnonymous/Not logged-in
-
File Pages20 Page
-
File Size-