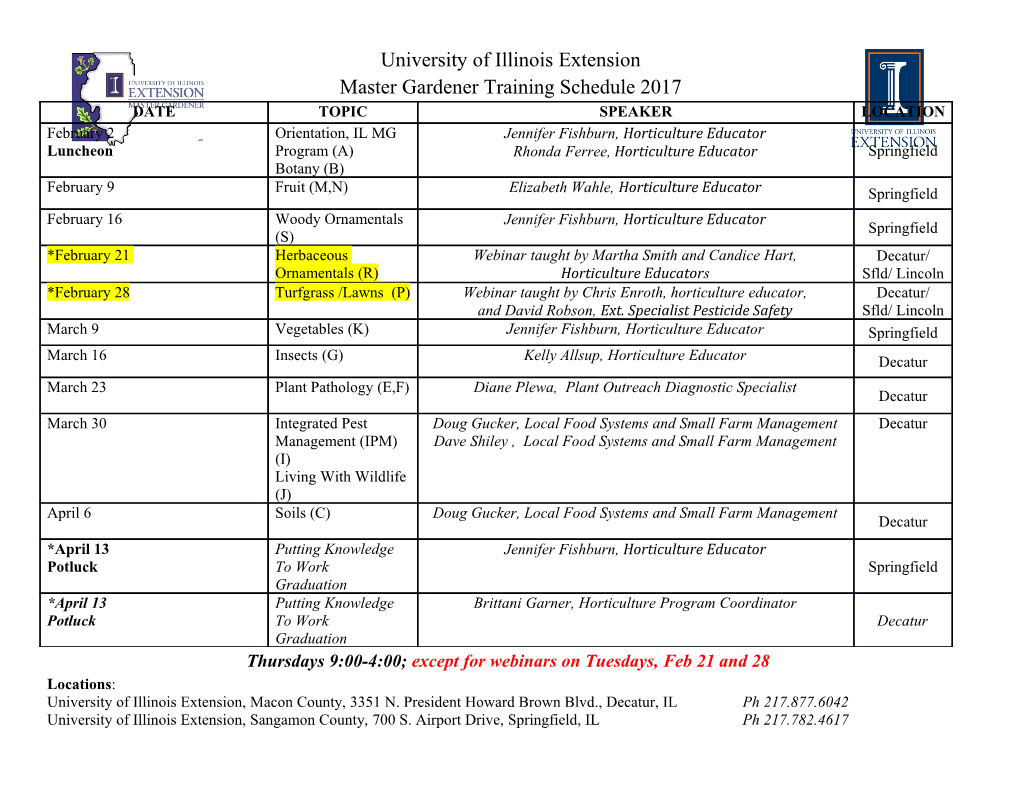
Development of the Hybrid Sulfur Thermochemical Cycle William A. Summers and John. L. Steimke Savannah River National Laboratory Aiken, SC USA 3rd OECD Information Exchange Meeting on Nuclear Hydrogen Oarai, Japan October 5-7, 2005 Outline Hybrid Sulfur Cycle Description Process Design and System Performance Hydrogen Production Economics Electrolyzer Development and Testing Conclusions Thermochemical water-splitting Series of coupled chemical reactions Water consumption only; all intermediates regenerated Thermal input only (pure cycles) or thermal & electric (hybrid cycles) Extensively studied in 1970s Over 3000 potential cycles have been suggested with 115 cycles reported in literature Status of Thermochemical Cycles Major design challenges due to large material flows, corrosive chemicals, impurities, reactant separation, high temperature heat exchange, and costs Thermodynamic limitations require high temperature (800-900 ºC peak heat input) Currently in lab-scale development stage Three leading cycles: – Sulfur-Iodine (SI) process – Hybrid Sulfur (HyS) or Westinghouse process – Ca-Br process (ANL modification of UT-3 cycle) Sulfur Family of TC Cycles Common high temperature reaction to liberate oxygen Thermal decomposition of sulfuric acid: H2SO4 → H2O + SO2 + ½O2 Temperature > 900 °C Various lower temperature hydrogen production and regeneration steps Pure thermal cycles require minimum of 3 reaction steps Sulfur-Iodine (SI) is the most developed (or researched) thermochemical cycle Source: U.S. Department of Energy Hybrid Sulfur (HyS) Cycle is a simpler alternative All fluids, two-step hybrid process Chemistry involves only S-O-H species Developed by Westinghouse Electric in 1970’s Also known as Westinghouse Sulfur Cycle or Ispra Mark 11 Cycle Closed-loop 120 lph bench-scale demonstrated in 1978 Key development issues are performance and cost for electrochemical step HyS Reactions H2SO4 ↔ H2O + SO2 + ½O2 (1) (thermochemical; 800-900 °C) SO2 + 2 H2O → H2SO4 + H2 (2) (electrochemical; 80-120 °C) Net Reaction: H2O → H2 + ½O2 (3) HyS Electrolyzer Concept • Direct water electrolysis requires min. anode membrane cathode 1.23 volts and produces H2 and O2 H2SO4 H2O H2 • SO2 anode-depolarization reduces SO3 + reversible cell voltage to 0.17 Volts per 2H+ cell and produces H2 and H2SO4 SO2 + H2O • Practical cell voltages are 0.45 to 0.60 volts per cell at 80-120°C, requiring up SO2 (l) + H2SO4 H2SO4 Solution Solution to 75% less electricity than direct water (optional) electrolysis SO2 anode-depolarized electrolysis Hybrid Sulfur Block Process Schematic Requires electric & thermal input Electric Power High-temp Generation Heat Source High temperature (>900°C) heat Electric Power Thermal Energy source could be nuclear reactor >900°C H Product or solar thermal 2 Conc. H SO Thermochemical system has 2 4 Electrolyzer Sulfuric Acid and Auxiliaries Concentration & three main processing units Decomposition Dilute – SO2-depolarized electrolyzers H2SO4 – Sulfuric Acid concentration and SO2 SO2 Recycle O2 decomposition H2O Feed – SO2/O2 separation SO2 and O2 Separation O2 By-Product SRNL improvements to HyS process design Optimized overall system design and integration Improved efficiency of acid processing scheme Developed high-efficiency SO2/O2 separation system Conducted tradeoff studies to determine – electrolyzer acid feed concentration – sulfur dioxide conversion and recycle – cell temperature and pressure – acid decomposition temperature and pressure Thermal Efficiency over 50% deemed likely 53.00 52.00 20% per-pass SO2 conversion 50% per-pass SO2 conversion 51.00 75% per-pass SO2 conversion 50.00 49.00 48.00 Net thermal efficiency, thermal Net % 47.00 Projected thermal efficiency is 46-53% 46.00 (HHV basis) 45.00 400 450 500 550 600 650 SO2 anode-depolarized cell potential, mV Target is high efficiency at reasonable reactor helium outlet temperatures 0.9 ideal efficiency He coolant ∆T: 0.8 ∆T = 250°C ∆T = 300°C ∆T = 350°C 0.7 ∆T = 400°C Target Operating Range 70% of ideal efficiency 0.6 0.5 2004 Hybrid Sulfur at 897°C 2005 Hybrid Sulfur at 900°C 2005 SI (GA calculation) Fractional thermal efficiency 2003 SI at 875°C (GA calculation) 0.4 1976 Hybrid Sulfur at 875°C 0.3 700 750 800 850 900 950 1000 1050 He-cooled reactor temperature, °C Commercial Plant Energy Balance 1,200 MW HT HT th 2 x 600 MWth HyS 952 MWth 576 MWe 341 MWe Process 2 x 600 MW GT GT 580 tpd H th (electrolyzers) 2 19 MWe (auxiliaries) Net thermal efficiency = 216 MWe Export Power 48.8% (HHV) HyS Energy Requirement: • 62% thermal energy • 38% heat value of electricity (48% efficiency) Higher efficiency projected with optimized flowsheets HyS hydrogen production costs may be somewhat lower than SI SI* HyS Plant Rating MWth 2400 2400 Plant Efficiency % (HHV basis) 52-42 48.8** Hydrogen Output Tonnes/Day 760-614 580 Electric Output MWe 0 216 Reactor System Cost $M 1,150 1,198 Electrolyzer Cost $ per m2 N/A 2000 Hydrogen Plant Cost $M 819 516 Electricity @ 3¢/kWh $M/yr N/A (51) Total Annual Cost $M/yr 413-399 306 Net Hydrogen Cost $ per kg 1.65-1.98 1.60 - with O2 credit 1.36-1.69 1.31 *W.A. Summers et al., US DOE NERI Topical Report, Project No. 02-160, 07/31/2004 **Current flowsheet; >50% expected. Delivered NuH2 is competitive with natural gas reforming at current fuel prices Breakeven Price for NG vs. NuH2 for Industrial H2 User 3 No CO2 Removal CO2 Sequestration Nuclear H2 2.5 2 1.5 1 April 2005 0.5 Hydrogen, $ per kg 0 024681012 Natural Gas Price, $ per MMB NG price real escalation = 2% per year SO2-depolarized Electrolysis + - Anode: SO2 (aq) + 2 H2O (aq) H2SO4 (aq) + 2 H + 2 e + - Cathode: 2 H + 2 e H2 (g) Sulfur dioxide is oxidized at the anode to form sulfuric acid Reversible cell voltage reduced to 0.17 volts per cell Practical cell voltages 0.5 – 0.6 volts (60-75% less than direct) Economic design requires high current density and low voltage Process design dictates electrolyzer operation at 100-120 °C and 20 bar with 50-60 wt% sulfuric acid Work in 1970’s Resulted in Test Electrolyzers With Reasonable Performance Current Density 200 mA/ cm2 H2SO4 Concentration 50 % Cell Temperature 49.4 °C Anode Potential 456 mV Cathode Potential 0 mV IR Drop 112 mV Total Cell Voltage 568 mV *Data taken after 140 hrs. of operation Westinghouse Laboratory Bipolar Cell Source: Westinghouse Electric Electrolyzer Development Program Original Westinghouse cells – Two compartment design with recirculating acid anolyte and catholyte – Carbon briquetted electrodes – Platinum electrocatalyst – Microporous rubber diaphragms – Positive flow of acid from cathode to anode Current design approach – Build on development of PEM fuel cells and electroyzers – Nafion or other proton-exchange-membrane – Gas diffusion carbon electrodes – Membrane-Electrode-Assembly (MEA) construction – Carbon flow fields – No acid catholyte required Ambient Pressure Testing of Electrolyzer Test Purposes – Verify reduced cell voltages based on SO2-depolarization – Verify applicability of MEA and PEM concepts – Examine issues of SO2 crossover and cell Modified PEM Water Electrolyzer degradation with time (84 cm2 active cell area) – Acquire data for modeling (Manufactured by Proton Energy Systems, Inc. with SRNL specified materials and and system scale-up changes) SO2-depolarzied Electrolyzer Test Facility Test Electrolyzer Designs Electrolyzer 1 procured from commercial PEM manufacturer – Based on standard water electrolyzer – Wetted parts changed to Teflon and Hastelloy B vs 316 SS – Pressure rated to 300 psig – Porous Titanium electrodes (could not be modified) Modified Commercial PEM Water – Nafion membrane; 4 mg/cm2 Pt loading Electrolyzer (84 cm2 active cell area) Electrolyzer 2 fabricated by Univ. of SC – Reseach type cell design – 50% smaller active cell area – Square plates; 60 psig rating – Carbon gas-diffusion electrodes – Pt on carbon electrocatalyst – Nafion membrane; 0.5 mg/cm2 Pt loading Research-type Electrolyzer (40 cm2) Test Results for Commercial-type Electrolyzer 2.0 1.5 Water only 1.0 SO2 + 30% H2SO4 SO2 + 70% H2SO4 Cell Voltage, V 0.5 0.0 0 200 400 600 800 Current Density, mA/cm2 Test Results for Research Electrolyzer 1.5 0.3 L/min, 1 bar 1.0 0.3 L/min/ 2 bar 0.9 L/min, 1 bar 0.9 L/min, 2 bar 1.5 L/min, 1 bar 0.5 Cell Voltage, V 1.5 L/min, 2bar Elect. No. 1 0.0 0 50 100 150 200 Current Density, mA/cm2 Test Result Summary Proof-of-concept for SO2-depolarized operation was confirmed Hydrogen generation observed at less than 0.5 volts per cell for low current density Severe corrosion measured in conventional PEM cell due to metal parts (titanium electrodes) Flow and mass transfer resistance in cell with gas diffusion electrodes limited operating current density Some sulfur formation observed at cathode Cell design and optimization program initiated Conclusions HyS Cycle is a viable thermochemical process – All major process steps and unit operations defined – Simplest known cycle with least equipment requirements – Plant thermal efficiency equals or exceeds other cycles – Hydrogen production costs are attractive Major technical issues associated with electrolyzer – High-temperature acid step common with S-I cycle – Proof-of-concept for PEM cell design established – Cell optimization and scale-up in progress Acknowledgements This work was sponsored by the U.S. Department of Energy under Contract No. DE-AC09-96SR18500 Funding provided by DOE Office of Nuclear Energy, Science and Technology under Nuclear Hydrogen Initiative Mr. David Henderson, technical program monitor.
Details
-
File Typepdf
-
Upload Time-
-
Content LanguagesEnglish
-
Upload UserAnonymous/Not logged-in
-
File Pages27 Page
-
File Size-