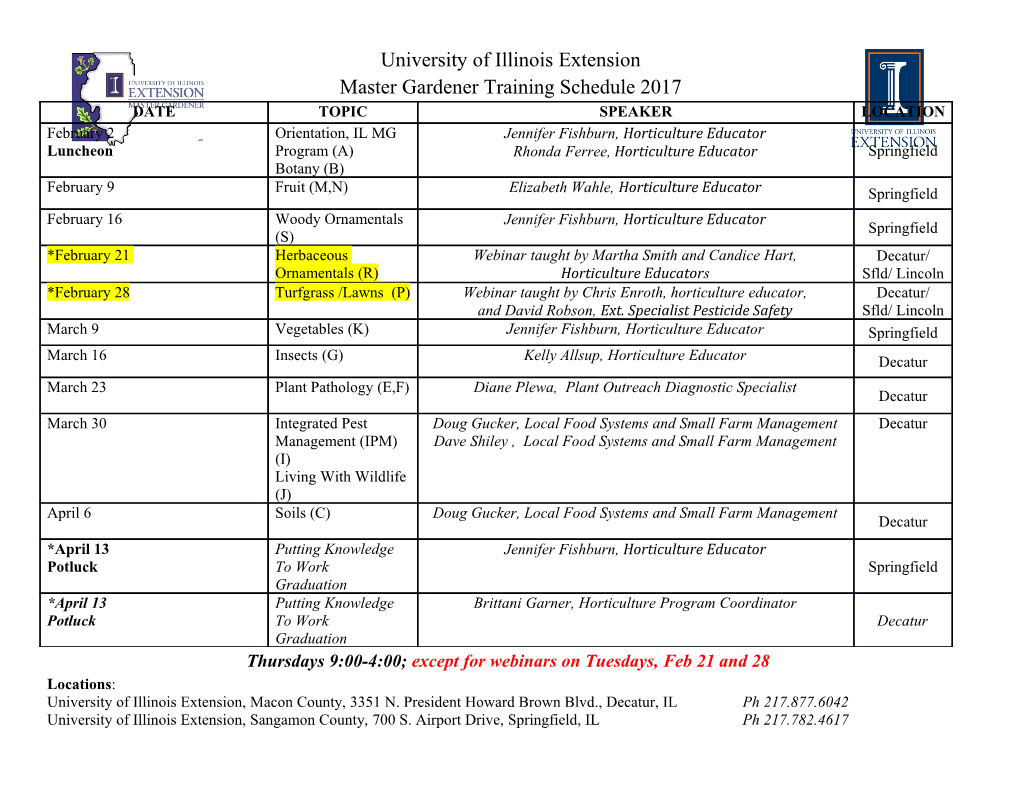
ExxonMobil Catalysts and Technology Licensing Creating a particle of difference Catalysts and Technology Licensing offers Building on more than 125 years of experience, ExxonMobil operates in three core businesses: its customers a portfolio of high-performing catalysts and advanced process technologies backed by a legacy of continuous innovation and a commitment to maintaining strong customer relationships. ExxonMobil offers decades of operational expertise to ensure that our customers have access to the industry’s best solutions: The same world- class innovations and technologies we use Chemical Gas Refining in our own facilities. Our role as an owner Our decades of expertise in chemical ExxonMobil Catalysts and Technology Our high-performance catalysts and operator uniquely positions us as experts production allow us to offer innovation Licensing also bring our experience in advanced process technologies can bring in this area. From planning and installation and expertise to the chemical industry. innovation to offer cost-effective, low-risk big benefits to refining companies. We can to plant startup and beyond, we continue Our high-quality catalysts and process solutions for H2S cleanup and syngas offer industry-leading advantages in fuel to offer our services and know-how to technologies offer methods to upgrade production. Gas-treating technology can production, resid conversion and lubes customers well after implementation. low-value chemicals into high-value enable customers to meet stringent production. Our technologies can offer Whether it’s for producing paraxylene, products in innovative and cost-effective emissions standards. Our technologies can higher product yields, convert low-value lubricants, fuels or other products, ways. They can be used to manufacture also assist in the production of high-quality products to higher-value end products and ExxonMobil would like to partner with chemicals and polymers used in creating synthetic fuels from methanol derived from enable the production of high-quality base you on your success. polyethylene, nylon, styrene and other natural gas. stocks for engine oil production. They can high-performance materials. also help to meet regulatory requirements Welcome to a world of opportunity! for sulfur and benzene removal. We’re committed to delivering industry-leading, innovative process technologies, specialty catalysts and expertise that exceeds customer expectations and provides differentiated value. Our main goal is to help customers increase production capacity, decrease operating costs and lower emissions, so they can achieve greater operational success. Most importantly, we collaborate with our customers as long-term partners — taking on challenges, finding solutions together and providing guidance on best practices that help achieve customer goals. Shaping the future As a technology innovator and Solving shared challenges through Toluene alkylation with methanol a proprietary high-activity, co-extruded manufacturer with close our experience (EMTAM℠ process technology) dual zeolite catalyst with low precious ExxonMobil is committed to its customers’ ExxonMobil’s EMTAM process uses metal content — offers superior yields, relationships to its customers, operational success, focusing on increasing inexpensive methanol to upgrade toluene to longer cycles, lower operating costs and ExxonMobil has developed the value generated by our customers’ paraxylene. It’s a breakthrough technology increased profitability. fundamental insights that optimize processes and plants. Used in over 150 that maximizes production of valuable and improve customers’ operations commercial facilities around the world, paraxylene product while lowering feed and Selective toluene disproportionation (PxMax℠ process technology) through technology development. ExxonMobil catalysts and technologies offer energy costs. The highly paraxylene- a number of potential advantages, over a selective process is built from commercially ExxonMobil’s PxMax process technology is range of technology categories. proven technologies. Unlike other toluene the industry benchmark for selective toluene conversion processes, there is no benzene disproportionation. Based on an ex-situ co-product and no hydrogen co-feed. It is selectivated catalyst, the PxMax process the only process that can tune the methyl- offers unmatched paraxylene selectivity and to-ring ratio based on market conditions product yields (superior xylenes-to-benzene and allows unlimited benzene co-feeding to ratio), which improve over an exceptionally produce paraxylene. long and stable catalyst cycle. Heavy aromatics transalkylation Xylene isomerization (TransPlus℠ 5 process technology) (XyMax℠ -2 process technology, ExxonMobil’s TransPlus 5 process is the low- LPI process technology) ExxonMobil catalysts are used in over 150 cost, high-conversion solution to upgrade ExxonMobil’s XyMax-2, and LPI processes commercial facilities worldwide. C9+ heavy aromatics and toluene into isomerize para-depleted xylenes effluents higher-value mixed xylenes and high-purity from the paraxylene recovery section into benzene products. The TransPlus 5 process equilibrium mixed xylenes, thereby — which is based on upgrading lower-value isomers to manufactured today. The process is built Synthetic fuels upon ExxonMobil’s proprietary zeolite (Methanol to gasoline technology) catalyst that drives a very high selectivity ExxonMobil’s methanol-to-gasoline to ethylbenzene and enables a low-capital, technology converts methanol to gasoline highly energy-efficient design that is that minimizes offsite and logistic applicable to grassroot, expansion and complexity. MTG creates a single, fungible retrofit opportunities. The EBMax process liquid product with virtually no sulfur and produces ethylbenzene with exceptional low benzene, which can be sold as-is or product purity for the manufacture of styrene. blended with ethanol, methanol, conventional gasoline or gasoline Cumene alkylation components. (Cumene process technology) The Badger cumene process was designed Lube dewaxing by Badger Licensing LLC to upgrade (MSDW™ technology, MWI™ technology, propylene and benzene to cumene for use MAXSAT™ technology) in the phenolics/bisphenol-A value chain. ExxonMobil’s MSDW, MWI and MAXSAT It has been commercially deployed over 29 catalyst technologies are ideal solutions for times and represents ~55% of all the producing base stocks for high-quality higher-value paraxylene product. The Aromatics treatment cumene manufactured today. The process is engine oils. These high-performance XyMax℠-2 process provides unmatched (Olgone℠ process technology) built upon ExxonMobil’s proprietary zeolite catalytic technologies offer premier lube performance, stable yields and catalyst ExxonMobil Olgone process technology is catalyst that drives a very high selectivity to catalytic dewaxing and hydrofinishing cycles. The ultra-low xylenes losses, high designed to extend cycles of existing cumene and enables a low-capital, highly benefits capable of processing a very wide ethylbenzene conversion, higher benzene aromatic streams treaters to reduce or energy-efficient design that is applicable to range of feedstocks — from hydrotreated purity and high WHSV allow customers to eliminate the amount of solid waste grassroot, expansion and retrofit VGOs and DAOs to hydrotreated raffinates reduce capital costs, inexpensively generated from an aromatics complex. opportunities. The Badger cumene process and slack waxes. debottleneck existing facilities and reliably At the heart of this high-performance produces cumene with exception product increase profitability over the extremely long technology is a highly stable and reusable purity for the manufacture of phenol, Diesel dewaxing (MIDW™ technology) catalyst cycle. catalyst. The outstanding performance of acetone and subsequently bisphenol-A. ExxonMobil’s MIDW catalyst technology the Olgone process can lead to significant enables higher yields of low cloud-point The LPI process also isomerizes para- operating-cost savings, better protection of Gas treating (FLEXSORB™ technology) diesel. Through isomerizing paraffins depleted xylenes effluents from the downstream units, fewer treater ExxonMobil’s FLEXSORB technology instead of cracking them, this diesel paraxylene recovery section into equilibrium changeouts, as well as debottlenecking enables customers to process increasingly dewaxing technology may also enhance mixed xylenes, but the reactions take place opportunities. sour gas streams while helping to meet cetane and volume swell compared to other in the liquid phase — offering a number of stringent emission regulations and sulfur technologies that rely only on cracking. unique benefits, including significant energy Ethylbenzene alkylation recovery objectives. The highly selective H2S savings, low temperature operation and (EBMax℠ process technology) removal process has also been used in tail ultra-low xylenes losses. These unique The EBMax process was designed by gas treating (TGT), acid gas enrichment benefits allow customers to reduce capital Badger Licensing LLC to upgrade ethylene (AGE) and high-pressure acid gas removal costs, inexpensively debottleneck existing and benzene to ethylbenzene for use in the (AGR) units. The technology provides a facilities and reliably increase profitability styrenics (polystyrene) value chain. It has cost-effective way to meet low H2S over the long catalyst cycle. been commercially deployed over 35 times specifications while minimizing
Details
-
File Typepdf
-
Upload Time-
-
Content LanguagesEnglish
-
Upload UserAnonymous/Not logged-in
-
File Pages8 Page
-
File Size-