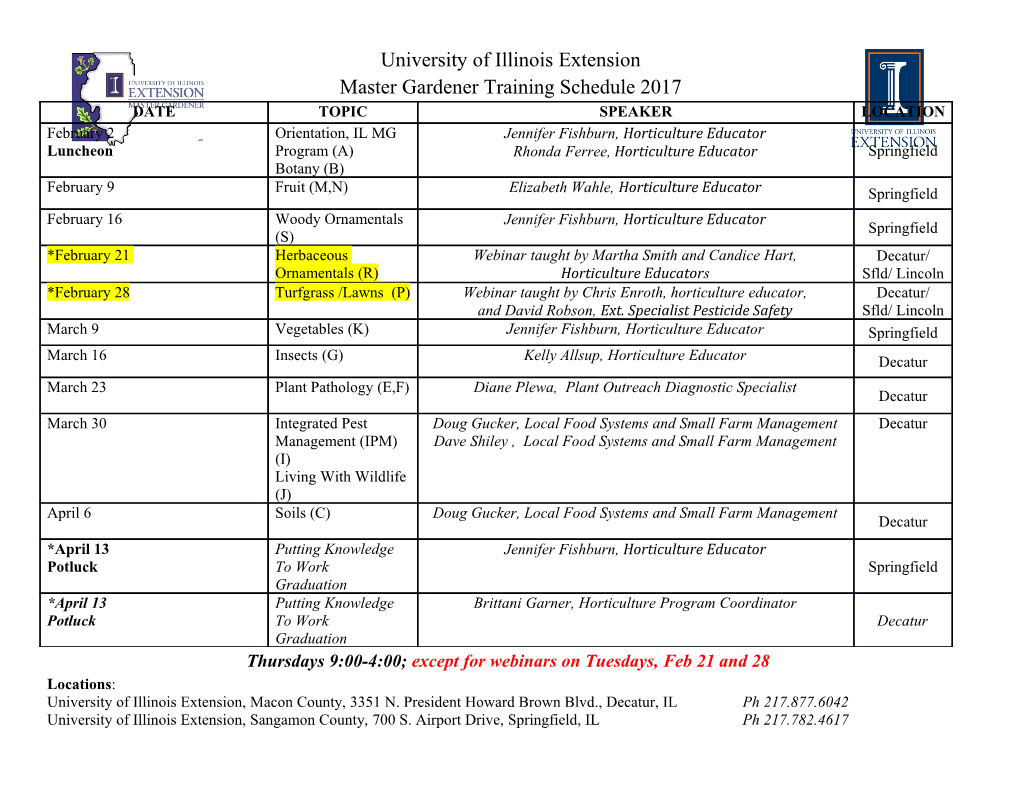
12/12/2019 Enabling better blasting - Mining Magazine Enabling better blasting Ailbhe Goodbody examines how the eciency of blasting at mining operations can be improved or optimised According to Metso’s Adrian Imre, blasting optimisation is a complex process that perfectly illustrates how a multi-faceted problem can be solved with teamwork Surface Mining > At mine sites, the primary aim of blast optimisation is to achieve the optimum fragmentation for downstream operations and Development processes with a minimum cost. 12 November 2019 However, improving the eciency of blasting means dierent things to dierent mines at dierent times. Vicente Huélamo, advance applied solutions director at Maxam, says: "Each mine is unique, with its particular set of challenges which keep changing. Therefore, Comments our rst task is to listen to our customers, and explain how drilling and blasting can be tailored to address their priorities." Share Russell Lamont, national consulting manager at Dyno Nobel, states that the optimisation of blasting eciency is a process which Ailbhe Goodbody occurs continuously at most mine sites. He says: "The ‘perfect' blast design will never be achieved, in large part due to the constantly variable geology encountered during the mining process, as well as the high number of variables and constraints inherent to any single blast. "Seeking to identify, characterise and address each of these factors in a way which enhances a site's successful operation is the process of blast optimisation. Technology advances have given the mining industry extremely improved capabilities to perform this function, particularly over the last few decades." Adrian Imre, drilling and blasting senior consultant at Metso, notes that optimisation studies around the world have proven that feeding the process plant with the optimum fragmented run-of-mine ore is the most important source for savings in mining operations. According to him, the principal techniques to improve blasting eciency are: Increasing the accuracy of the information on rock blastability, including structural and rock mechanic properties and ore domain denition based on blastability - these are key factors for a successful blast; Carefully planning blasting activities. In open-pit mining, the use of blast-masters, by designing the shape and size of the blasting polygons for the whole bench in the initial planning stages, is essential to increase eciency; Blast design optimisation by adapting the drill and blast parameters to the blasting polygon conditions will achieve the fragmentation target in a continuous and sustainable way; Increasing the accuracy of drill and blast design implementation and establishing a reliable blast reporting system; https://www.miningmagazine.com/development/news/1375573/enabling-better-blasting 1/7 12/12/2019 Enabling better blasting - Mining Magazine Collecting and analysing the information related to blast performance including fragmentation and outcomes such as yrock, ground vibration, back break, etc. Constructing a blasting database, including a complete set of data for each blast, represents the foundation for continuous improvement by ‘ne tuning' the blasting operation; and Feedback from the process plant (changes in dierent operational parameters linked with dierent plant feed) is also important and a driving factor for continuous improvement, allowing for maximum operational benets. Imre notes that blasting optimisation is a complex process that perfectly illustrates how a multifaceted problem can be solved with teamwork. He says: "I would like to stress the importance of collaboration between all professionals, from various departments, for a successful blast." Angus Melbourne, chief commercial and technology ocer at Orica, explains: "The downstream impact of variable and poorly controlled blast outcomes today can impact as much as 80% of the total mine processing costs; this, combined with the current non- digitised and manual practices involved with the drill and blast segment of the value chain, presents a signicant opportunity for the industry to digitise drill and blast." Additionally, he points out that as mines go deeper, and orebodies become more remote, automated and digitally enabled better blasting presents a signicant productivity opportunity for the industry. Explosive and detonator suppliers have focused on electronic detonator systems for more precise blasting delays, as well as advanced software programs to optimise blast patterns and delays for various rock structures. In addition, technology providers such as MST Global have concentrated on the remote initiation of the blast using various communication technologies. Denis Kent, product manager, mining at MST Global, says: "In particular, our underground PED ‘through-the-earth' transmission system and our AXON digital networks." Precharging using Orica's WebGen 100 system eliminates the need for personnel to work in hazardous areas Downstream processes As noted earlier, better blasting can strongly improve downstream mining processes. "As one of the rst steps in the mining process, blasting is widely understood to bear considerable inuence over subsequent stages," suggests Dyno Nobel's Lamont. "The degree and manner of this inuence depends largely on the type and conguration of a specic mining operation. In fact, ‘better' blasting is often dened by downstream functions." For example, the ideal size distribution for a quarry is substantially dierent from that of a copper operation. Lamont says: "The mine-to-mill concept has been widely accepted by the industry for decades, but the implementation of blasting principles to maximise this benet is woefully behind in many cases." Maxam's Huélamo thinks that mines are recognising that while drilling and blasting constitute a tiny portion of the mining costs, they have a signicant inuence on the safety of the mine, on the impact to the environment and on the performance of all downstream operations. He says: "For us it is instrumental to work with our partners on customising the drill and blast solutions for each specic requirement. Controlling how and when the rock is produced aects the performance of excavation, hauling, crushing and milling. "At Maxam we are already working with our partners on mining optimisation projects developing downstream productivity initiatives aligned with their KPIs. Thanks to this collaboration, we are becoming not just a blasting solutions provider but a productivity enhancer partner." In many mining methods, a signicant portion of the material blasted is waste, which is removed to expose the mineral deposit. Simon Tose, global manager - mining optimisation at AEL Intelligent Blasting, explains: "This needs to be blasted to a fragmentation size to ensure maximum ll for the bucket of the loading equipment and the optimal ll factors for the haul trucks. As the global industry looks to conveyors, hydro systems to take the blasted material out of the pit, to reduce waste-to-ore ratios, the design of blasting and managing the fragmentation curves becomes increasingly more important." The shape and looseness of the muck pile also have an immediate eect on loading and hauling productivity. Metso's Imre says: "Nowadays, blasting can be conducted to achieve the desired shape and looseness to guarantee the maximum productivity for specic loading equipment." https://www.miningmagazine.com/development/news/1375573/enabling-better-blasting 2/7 12/12/2019 Enabling better blasting - Mining Magazine However, improved blasting results can have the biggest impact in the processing plant. "Blasting operation is the rst stage of comminution," notes Imre. "Pushing the fragmentation as close as possible to optimum will cut costs in the process plant by reducing the energy consumption and cost of wear parts." By increasing throughput, the cost per tonne will decrease since xed costs remain constant. Huélamo says: "The mining process plants, once designed, installed and commissioned, have either little exibility or high cost in terms of changing operational parameters." Imre adds: "In addition, as mineral processing involves considerable water consumption, feeding the plant with optimum fragmentation can contribute to reducing this, therefore reducing the overall environmental impact of the mining operation." MST Global's Kent suggests: "The key is consistent fragmentation, and hence why the major explosive suppliers have put so much eort in electronic detonators over the last 10 to 15 years." Lamont says that Dyno Nobel is collaborating with customers in all mining industry sectors to ensure that training and tools applied on the bench or in the heading translate to cost savings and productivity improvements throughout the downstream processes. "Achieving customer understanding and buy-in from ops managers, procurement specialists and even drill and blast personnel that the lowest blasting cost rarely translates to the lowest operational cost, is a dicult but key undertaking to our business," he comments. "The digital tools, physical products and drill and blast expertise within Dyno Nobel allow us to deliver minimised overall operating costs when accepted and engaged as a true business partner with our customers." A screenshot from AEL's Designer software showing tailormaking the fragmentation of the blasted material, matching design to that required to improve shovel or haul truck or process plant eciencies Trends Blasting professionals are strongly oriented towards increasing blasting eciency. Metso's Imre
Details
-
File Typepdf
-
Upload Time-
-
Content LanguagesEnglish
-
Upload UserAnonymous/Not logged-in
-
File Pages7 Page
-
File Size-